Mar 26 2013
A typical storage silo can hold several thousand tons of corn, seed, sawdust and other granular material. These particles funnel down through a hopper, or chute, into freight cars, which haul the material away for processing.
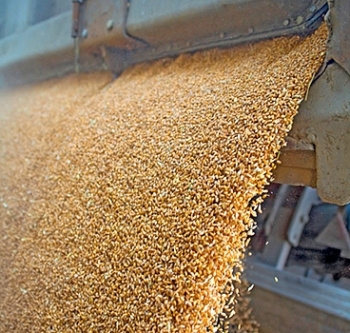
But it’s not uncommon for a chute to clog, and the only fix in many cases is for a worker to stand by the opening and break up the jam with a mallet. At other times, a worker may need to climb into the silo to loosen material from the walls — a dangerous task that can trigger a deadly avalanche.
Such accidents might be prevented if silos were designed to accommodate granular flow. The problem is, it’s extremely difficult to predict how grains behave collectively: While kernels of corn are solid, they behave more like a liquid when flowing through a silo. Simulating the flow of grains in silos, and in other geometries, has proven a tricky, centuries-old problem for scientists.
Now researchers at MIT have devised a model of granular flow in three dimensions. The team found the model accurately predicts the results of granular flow experiments, including a flow configuration that has long puzzled scientists. The results of the team’s research are published this week in the Proceedings of the National Academy of Sciences.
Ken Kamrin, the Class of 1956 Career Development Assistant Professor of Mechanical Engineering at MIT, says the model may also be useful for improving the flow of drug powders, tablets and capsules in pharmaceutical manufacturing.
“There are a lot of big questions in granular materials,” says Kamrin, who co-authored the paper with MIT postdoc David Henann. “One of the biggest is, ‘If I draw a silo and tell you about the grains I fill it with, can you predict how rapidly it will flow?’ Now we can try this with demonstrable accuracy … that’s much easier than trying to track every single grain of sand.”
A neighborly effect
The new three-dimensional granular flow model builds upon a two-dimensional prototype that Kamrin developed last year. In that model, he made a key adjustment to an existing set of equations that are normally used to describe the way liquids flow. To predict, for example, how water flows through a funnel, these equations essentially divide the volume of water into a fine grid, predicting how the whole volume will flow based on how water molecules behave in a single box of the grid.
Kamrin says such “local” equations do a good job of accurately predicting water flow because water molecules are so much smaller than most vessels they flow through. But the same is not true of granular materials. Kamrin realized that, in granular flow, size matters: Because grains are not vanishingly small compared to their environment — they are much larger than water molecules — their size affects how neighboring grains move, making it impossible to generalize the flow of one tiny box of grains to an entire silo. Recognizing this, Kamrin added a new “nonlocal” term to the equations to account for grain size, and found that the resulting predictions matched simple, two-dimensional, particle-by-particle simulations of granular flow.
A new dimension
In the current paper, Kamrin and Henann propose a general, three-dimensional model for granular flow. It adopts a similar nonlocal term, taking into account the size of individual grains and the effect of neighboring grains. The researchers then tested the model against experimental flows of glass beads in various geometries, including the split-bottom cell — a geometry that has long confounded scientists, as its flow of grains has been difficult to describe mathematically.
A split-bottom cell resembles the bowl of a food processor, with an inner and outer cylinder mounted on a cylindrical floor; the inner cylinder remains stationary as the outer ring rotates. In experiments, scientists have observed that grains in this geometry flow in a cooperative fashion: Those in the very bottom layer move with either the inner or outer ring, while the next layer up begins to flow more smoothly. With each higher layer, Kamrin says the movement of grains “smears,” since the speed of one layer affects layers further up in the cylinder. In this way, the sharp motion of the grains at the bottom of the cell induces a spread-out, wide flow in the grains at the top.
Kamrin and Henann applied their model to this geometry, and found that their equations accurately predicted the flow of grains throughout the rotating cylinder — a first in granular modeling. They then dug through the granular literature and tested the same model against other three-dimensional geometries examined in more than 150 published experiments, finding quantitative agreement between their predictions and actual observations.
This model may work well in predicting the flow of glass beads, sand and agricultural grains, says Martin van Hecke, a professor of condensed matter physics at Leiden University in the Netherlands.
“By tuning a few physical parameters [such as] friction [and] length-scale, a host of other materials can be described,” says van Hecke, who did not contribute to the study. “Granular media are the most abundant materials in industrial processes … a proper understanding of slow granular flows therefore has the potential for very wide impact.”
Going forward, Kamrin and Henann hope to test the model against experiments, and plan to build various structures to observe the way grains of different sizes flow. The goal, Henann says, is to provide manufacturers with a tool to design more efficient silos and other grain-handling equipment.