Monitoring grippers during handling and assembly tasks is much easier now, due to the MMS 22-PI1 magnetic switch from SCHUNK, which uses two programmable switching points, making it an all-purpose sensor.
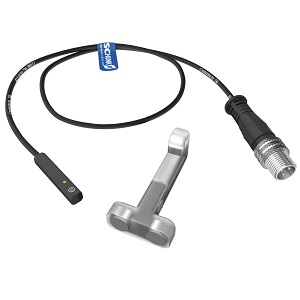
Spare parts re-stocking is reduced and monitoring is carried out by a magnet inside of the actuator. Since the switching point can be individually adjusted, and the actuator can be completely inserted into the C-slot, no additional interfering contours occur at the actuator.
Instead of adjusting the switching points mechanically, the MMS 22-PI1 can be programmed quickly. The required teach tool can be used as a wired or contact-free magnetic version. For programming purposes, the teach tool is held up to the sensor until the control LED illuminates. Then the teach tool is removed and the gripper is directed into its target position. The teach tool is again held up to the sensor and the sequence is finished. Compared with conventional magnetic sensors, the operator saves up to 90% set-up time.
In order to increase process reliability, the release sensor point of the MMS 22-PI1 can be programmed on demand, too. The teach tool is put on for five seconds, the gripper is placed into the position you want the signal to drop out at, and the position is confirmed with the tool. The adjustable hysteresis allows reliable position monitoring at very short strokes, and the gripper can differentiate workpieces of different sizes. Overall, the complete gripping process can be better evaluated and controlled.