The Talyrond 500 series is unsurpassed in speed and position control making it the ideal system for high volume precision components
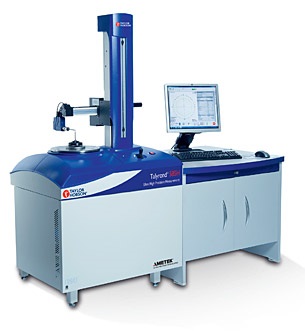
High precision emulation of your manufacturing process
The all-new Talyrond 500 roundness instruments use rotary, vertical and horizontal measuring datums to duplicate your machine tool’s movement and exactly reproduce the workpiece shape. This ultra high precision simulation of the cutting tool path enables precise control of your manufacturing process.
Reproducible measurement results
Decades of experience, ultra precision machining expertise and FEA optimized design combine to provide low noise and near flawless mechanical execution of the measuring axes. Further enhancement via the use of traceable standards and exclusive algorithms effectively eliminates instrument influence from the
measurement results.
Unparalleled measurement capability
Five measurements in one
Emulating the manufacturing process with a higher degree of
precision allows all features to be measured on one instrument
Roughness
High resolution gauge and low axis noise enables linear or circumferential
surface roughness measurement.
Roundness
Frictionless air bearing spindle and precision column for roundness,
cylindricity and straightness measurements.
Contour
Our patented calibration technique enables measurement of radius, angle,
height, length, distance and more.
Cylindrical mapping
Precision control and low noise in all axes allows in depth analysis of
cylindrical components including wear scars and material volume.
Cams and pistons
A precision encoder and linear scales in all axes enables measurement
of non round parts such as cams and pistons.
Powerful software tools help improve your process
Harmonics
Ordinary inspection might detect bad components but Talyrond 500 can
help you fix the production issues that are causing them. Deviation in
form on a workpiece can be broken down into irregularities that have
both frequency and amplitude. Harmonic analysis identifies these
imperfections allowing you to pinpoint and correct their cause, reducing
the need for ever tighter tolerances on size.