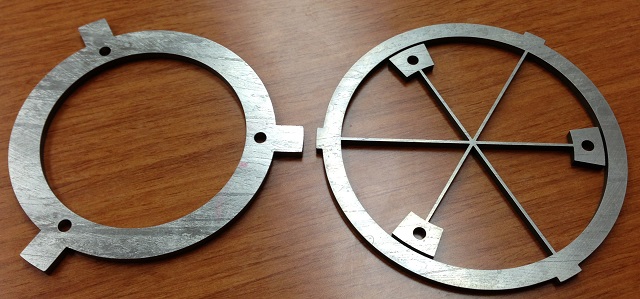
Components of a mirror structure that can be rotated very precisely by flexing parts made of "bulk metallic glass."
Image Credit: NASA/JPL-Caltech
Researchers at NASA's Jet Propulsion Laboratory (JPL), the California Institute of Technology, and Brigham Young University have developed a new technique for producing complex compliant mechanisms, by combining innovative manufacturing methods and materials.
Compliant mechanisms are found in surgical instruments, springs, paperclips, and micro-devices. Such devices can move easily because they are flexible, but when strained they do not deform permanently (plastic deformation). This kind of mechanical motion is important for creating different types of movable structures, such as antennas and mirrors for spacecraft.
The scientists showed that bulk metallic glasses have the preferred characteristics required for these mechanisms.
The metals can be easily molded like plastics in a cost-effective way, and can be used in applications where both durability and flexibility are important, explained Douglas Hofmann, principal investigator of the study at JPL.
According to Larry Howell, co-author of the study, titanium alloys are generally utilized in compliant mechanisms, but working with such alloys is often difficult. In contrast, bulk metallic glasses have increased strength, low melting temperatures, and excellent flexibility. This means complex shapes, such as artificial limbs and robot bearings, can be easily developed without affecting their performance.
The researchers demonstrated the supremacy of bulk metallic glasses in these applications by modeling the performance of a variety of compliant mechanisms. In order to validate the model, the researchers used a bistable spring, which is capable of locking in two different positions. Metallic glass, as well as titanium, was used to make this spring, which was later mechanically tested.
Using the latest injection-molding technology, the scientists developed over 30 similar models of the new mechanism to demonstrate the benefits of the metallic glass components.
The applications of these mechanisms in space will not only help in improving the accuracy of instruments, but will reduce their weight. Such mechanisms could even be used for storing elastic energy to deploy components in space without using motors. Other potential applications include medical implants, sporting goods, consumer devices and cars.
The study has been published in the journal Advanced Engineering Materials.