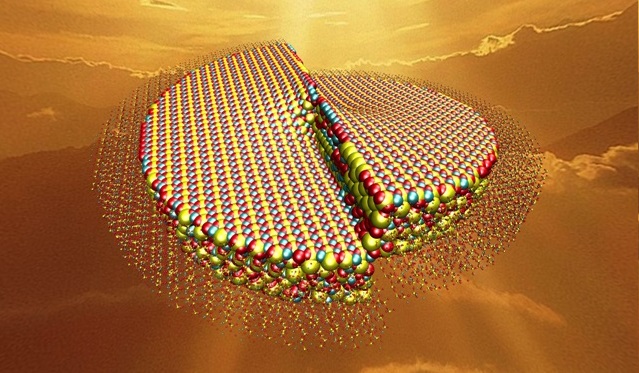
A cutaway illustration of a clinker, a pellet manufactured in a kiln and then ground to make cement, shows a defect called a screw dislocation.
Image credit: Shahsavari Group / Rice University
Researchers at Rice University conducted a study, which showed that significant amounts of energy can be saved by making changes to current cement manufacturing processes.
Lu Chen, former Rice graduate student, and Rouzbeh Shahsavari, materials scientist and a member of the Richard E. Smalley Institute for Nanoscale Science and Technology at Rice University, found that by modifying the process where lumps of calcium silicate, or clinkers, are converted into cement could help in saving large amounts of energy. The latest study has been described in the American Chemical Society journal Applied Materials and Interfaces.
Portland cement is the most widely used cement in the world. Clinkers are made by first heating the raw elements in a rotary kiln and then crushing them into a fine powder. When cement is combined with water, it acts almost like a glue and holds the concrete firmly together. According to previous research exploring the molecular structure of cement, global concrete manufacturing practices contribute to 5-10% of CO2 emissions.
The scientists studied both the atomic and crystal structures of the five phases of clinkers that represent stages of cooling once they exit the kiln. They specifically examined the internal stresses, which make certain clinkers more fragile and thus make them easier to crush than others.
They also inspected defects known as screw dislocations. Such effects in raw materials, even when ground, can affect the way powders mix with water. This reactivity is what determines the ultimate strength of cement.
In addition, the researchers also noticed that when clinkers are heated to a high temperature, they become extremely fragile and highly reactive. The team then ranked the qualities of five samples and proposed that the study could allow cement manufacturers to integrate processes to reduce grinding energy, which currently accounts to about 10-12% of the energy needed to manufacture cement. The researchers also found that for each ton of cement produced, the grinding energy releases approximately 50kg of CO2 emissions.
Defects form naturally, and you cannot do anything about them. But the more brittle the clinkers are, the better they are for grinding. We found that the initial phase out of the kiln is the most brittle and that defects carry through to the powder. These are places where water molecules want to react.
Rouzbeh Shahsavari - Assistant Professor of Civil/Environmental Engineering and Materials Science and Nanoengineering
The research was funded by the National Science Foundation.