Hardide Coatings, provider of advanced surface coating technology, has identified previously unquantified properties within its Hardide-T coating thanks to masters students from the University of Southampton Advanced Tribology program.
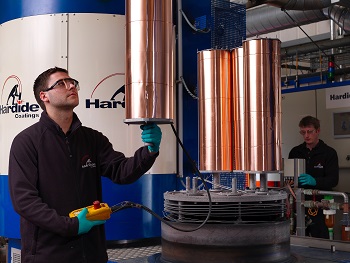
Christian Micallef and Chen Wang, both studying MSc Engineering Materials (Advanced Mechanical Engineering Science), undertook research with Hardide Coatings as part of their masters degree. Under separate tests, the pair measured the fracture toughness and anti-galling properties of the coating.
In the fracture toughness tests, four samples were coated within the range of Hardide-T hardness values and tested using a nano-indenter. After 100 nano-impact tests, the samples showed no signs of fracture. Tests were then carried out on the samples by making deep indentations with a sharp diamond cube corner indenter. Although indents were made, these tests also failed to induce fractures to the coating.
Fracture toughness and galling resistance of the coating were two areas where we wanted further test results to get quantitative measurements and to demonstrate the effectiveness of the coating. From the experience of using our coatings in extreme conditions we were confident that the Hardide coated samples would perform well but we were very pleased at the strength of the results. The fact that the samples couldn’t be fractured shows just how tough the Hardide-T coating is. To measure the anti-galling resistance, tests were carried out using the TE77 standard galling test.
In the control test, two stainless steel samples were used and a Coefficient of Friction of 1 was established under a load of just 65 N (7kg) with galling occurring at 500 N (51kg). In the same test using two Hardide coated samples, Coefficient of Friction stabilised at 0.2 and under the maximum load of 800 N (82kg) no galling occurred.
The galling test in particular is very valuable for tooling operating in extreme conditions. As these tools are often in exposed environments, the traditional lubrication between metal components can be abraded, squeezed under high loads or washed away by the elements.
The tests show that Hardide on Hardide parts do not gall even under maximum load and are ideal for these tough conditions. Cutting friction by a factor of five will also offer a huge reduction in damage to parts which are moving against each other.
We have a long-standing relationship with Southampton University and we always enjoy working alongside the students to support their research projects and increase the knowledge-base on our technology at the same time.
Dr Yuri Zhuk - Technical Director, Hardide Coatings
Following the research project, Christian impressed the senior management so much that he was offered a job and joined the company full time in October as a Research and Development Engineer.
Hardide-T is one of the range of Hardide coatings which are highly abrasion, erosion, corrosion and chemical resistant while also being tough, ductile and impact resistant. Applied by chemical vapour deposition (CVD), the process can coat external and internal surfaces and complex shapes. The coatings technology is proven to offer dramatic improvements in component life, delivering cost savings to customers through reduced downtime and increased operational efficiency.
Combined with the other properties, the anti-galling will be beneficial for valves, bearings, heavy rotating equipment, oil tools assembled by threads and other applications where components experience metal to metal contact under high contact stress.
In heavy duty applications which put components under regular impacts, pressure or shock loads, such as downhole drilling or fracking where the tools hit rock formations, the fracture toughness is beneficial as brittle coatings wouldn’t be able to survive the impact or deformations.