Hardide Coatings, the provider of advanced surface coating technology, has announced today that its Hardide-A tungsten carbide coating has met the technical performance requirements as a potential alternative to hard chrome plating on some specific Airbus aircraft components.
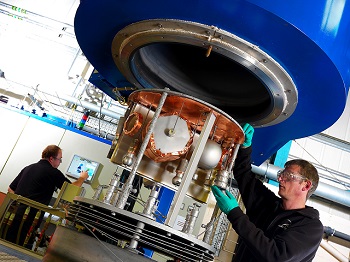
Following an eight year programme of development and testing, Hardide-A is now available for consideration by design engineers and sub-contractors on selected Airbus aircraft components. It met the Airbus requirements for thick CVD (Chemical Vapour Deposition) Tungsten Carbide coatings and is a suitable alternative for hard chrome plating, which is used extensively on airframe and landing gear components.
Hard chrome plating has been widely used in the aerospace industry for many years but its use is being banned in September 2017 under EU REACh environmental and health and safety regulations, unless otherwise authorised by the EU Commission, as it uses carcinogenic hexavalent chromium salts in its production. Increasingly tight restrictions are also being imposed in the USA by OSHA.
After many years of hard work and collaboration between Airbus and Hardide Coatings, it is a huge step forward to be technically qualified for potential use on component parts for Airbus aircraft. This is a significant achievement and we are absolutely delighted that the coating is now available to Airbus designers and engineers as an alternative to hard chrome plating on selected parts.
The selection of the coating by the designers will be based on further technical and commercial considerations as well as part-specific testing.
This success with Airbus is a key enabler for our further growth in the European, North American and wider aerospace markets which have enormous potential for the Hardide coating technology. Hardide has also recently commissioned its new US coating facility in Martinsville, Virginia to serve North American customers.
Philip Kirkham - CEO, Hardide plc
Hardide-A is one of the range of Hardide coatings which are highly abrasion, erosion, corrosion and chemical resistant while also being tough, ductile and impact resistant. Applied by low-temperature chemical vapour deposition (CVD), the process can coat external and internal surfaces as well as complex shapes and is a suitable alternative to many traditional coatings including HCP, HVOF, D-Gun and plasma thermal spray coatings in erosion, abrasion and corrosion environments.
The coatings technology is proven to offer dramatic improvements in component life, delivering cost savings to customers through reduced downtime and increased operational efficiency.