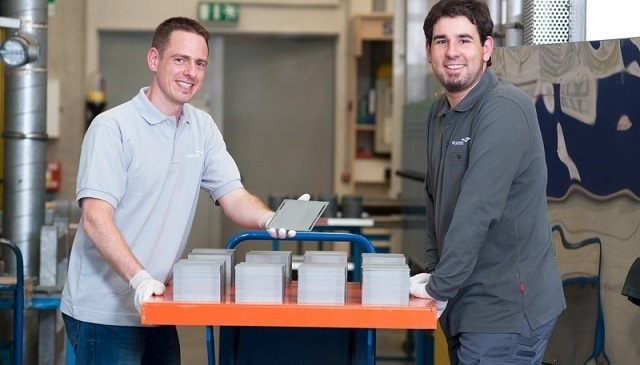
This year, Plansee will once again be showcasing its innovative interconnects for fuel cells at the Hanover trade fair.
With interconnects Plansee produces vital components in SOFC fuel cells and thus makes a decisive contribution to the further development of this technology in both mobile and stationary applications.
Plansee is one of the few suppliers that is able to manufacture high-quality interconnects for the SOFC sector in large-scale quantities using powder metallurgical techniques. In parallel to our role as supplier to a range of companies, we are involved in many development projects.
Dr. Werner Schulmeyer - Fuel Cell Division, Plansee
The production of interconnects demands a detailed and wide-ranging knowledge of various material alloys and specialist expertise throughout the entire manufacturing chain. Plansee manufactures all its products, including the interconnects, using powder metallurgical processes. Using this production method, it is possible, for example, to create different structures on the top and bottom side independently on the same interconnect.
The required profiles are imprinted at the time the powder is compacted. There is therefore no need for any subsequent machining, time-consuming welding operations to bond multipart, formed sheet metal components, or forging processes.
Powder metallurgy is vitally important in order to be able to manufacture large-scale quantities economically and at a consistent quality.
Dr. Werner Schulmeyer - Fuel Cell Division, Plansee
Plansee offers suitable alloy materials for different SOFC cell types since it is vital that the interconnects and the cell itself are optimally harmonized. One critical parameter here is the coefficient of thermal expansion of the components. Only if compatible values are chosen for the cell and the interconnects is it possible to avoid the generation of critical mechanical stresses during the thermal cycles to which the components are exposed.
Plansee has already gained over 20 years' experience in the development and manufacture of components of SOFC fuel cell applications and has repeatedly demonstrated the long-term durability of the finished interconnects.
The most recent example is the long-term testing of a solid oxide fuel cell by the Jülich research center which started in 2007. Today, the high-temperature fuel cell stack is still running and currently holds the world record with nearly 80,000 hours of operation so far. Plansee originally supplied the interconnects for this stack.
This result is an important and encouraging signal showing that the desired stack lifetimes can also be transferred into commercial applications. This is an important prerequisite for the economic operation of SOFC fuel cell systems and one of the Plansee Group's many contributions to the ecologically responsible power generation solutions of the future.
Meet the Plansee Team at the Hanover trade fair: April 19-23, Hall 27 Stand C71.