RTP Company has designed and introduced thermoplastic compounds specifically for oil and gas service backup rings that perform well in both conventional and extreme high pressure and/or temperature conditions.
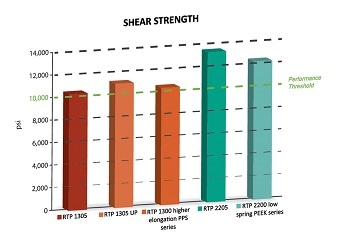
Sealing systems that incorporate backup rings are a significant contributor to the longevity of downhole oil and gas equipment, especially within high temperature and high pressure environments. Developing cost effective components to meet sealing system requirements is an ongoing industry challenge, one that RTP Company has met by offering a range of product solutions.
When selecting materials for backup rings, it is important to take shear strength into consideration. High shear strength in backup ring compounds is desired because it is an indicator of better overall performance and longer service life. As shown in Figure 1, a shear strength performance greater than 10,000 psi is an important performance threshold.
Ultra Performance (UP) Structural Compounds allow backup rings to perform beyond conventional high-pressure, high-temperature downhole conditions. For performance at a better value, RTP Company also offers cost-optimized RTP 2200 series PEEK compounds and RTP 1300 PPS compounds with mechanical properties suitable for conventional well conditions. RTP Company also offers compounds formulated to reduce “spring” associated with backup rings machined from injection molded stock shapes.
Controlled Geometry Pellet (CGP) products from RTP Company provide yet another option for oil and gas customers who use compression molded shapes to produce backup rings. Compression molded stock shapes manufactured from CGP have improved mechanical properties compared to shapes molded from dry blended compounds, which increases backup ring pressure and temperature performance.
Oil service companies benefit from our ability to provide multiple material solutions for injection and compression molding and from our R&D group, who have more than 30 years of industry experience. This allows customers to design backup rings from materials that meet the end-use requirements that ultimately provide longer life and greater reliability.
Duncan Hogg, Global Energy Market Manager
To learn more, download RTP Company’s innovation bulletins regarding backup (anti-extrusion) ring compounds, and Controlled Geometry Pellets. Product data sheets for RTP Company compounds are available at http://web.rtpcompany.com/info/data/index.htm. For more information call (507) 454-6900, or visit www.rtpcompany.com.