Today, an estimated one-third of food produced for human consumption is lost or wasted, equivalent to 1.3 billion tons of food every year, according to the Save Food report by the Food & Agriculture Organization of the United Nations. Even in the most developed supply chain systems such as those in Europe, 4% of transported goods are damaged in some shape or form due to low pallet stability. A growing consumer focus on convenience and sustainability will also drive continuous changes and innovation in packaging.
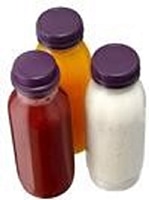
With tomorrow’s resource challenges, packaging has a crucial role to play, particularly in helping to reduce waste in the global food supply and in protecting goods for consumers while complying with ever more stringent regulations that are put in place to increase food safety and to secure safe packaging. Today’s fast-paced lifestyles also are driving demand for pre-packed food, and for hot filling and microwave use. At the same time, consumer expectations are spurring brands to create packaging that is distinctively shaped, highly transparent, hygienic, easy to open, and with excellent graphics. These challenges need to be met while lowering weight and cost by reducing cycle times, down gauging and increasing the share of reusable packages to minimize waste and lower the environmental impact of everything we produce.
On its stand at the K 2016 plastics trade fair in Düsseldorf, Germany, this October 19-26, SABIC will be showcasing several new products and technologies that help to address these specific market needs. With a strong focus on sustainability and an underlying theme of “Chemistry that Matters™,” SABIC will highlight a number of packaging solutions that address the challenges of the packaging industry, including:
REDUCING LOSS AND INCREASING EFFICIENCY
SABIC’s multilayer and polymer blend technologies may help manufacturers to reduce transport losses, optimize protection of goods, and maximize pallet stability by increasing the holding force of collation shrink and stretch films used to protect food packaging, while also making those films stronger.
The unique combination of SABIC polyolefin building blocks also continuously may enable improvements in efficiency during production. They may offer higher tensile strength and higher toughness to optimize the wrapping process, by reducing film breakage and improving stretch film consistency of quality.
SABIC technology may also reduce the environmental impact of packaging by enabling down gauging that can reduce thicknesses by up to 20% compared to current film concepts. Thinner products reduce plastic consumption and allow for higher processing speeds.
REDUCING FOOD WASTE
SABIC’s flexible packaging solutions already significantly contribute to minimizing food waste. The dedicated SABIC® PE/PP resins are essential in building advanced, multilayer barrier film concepts that provide longer shelf life of fresh and chilled food, cheese and meat. The corresponding reduction in food waste has a significant positive impact on the total life-cycle analysis of a flexible packaging system.
LIGHTERWEIGHT PACKAGING
Reducing packaging weight remains key and is facilitated by using SABIC’s solutions in flexible pouches for both food and non-food applications. Leveraging the extended SABIC® PE/PP portfolio in pouches may enable further improvements in stiffness, sealing performance and retortability.
The new SABIC® PP FLOWPACT Product Family, especially the very high MFI grades, are formulated to help our customers for thin-wall food packaging applications where a good balance of high stiffness and high flow is required:
- Enabling down gauging, thereby reducing packaging waste
- High flow and fast crystallization generates shorter cycle times, thus lowering production costs
NEW SABIC® LDPE film grade, is a new product from SABIC for manufacturing very thin-gauge packaging.
- Offers excellent draw-down ability, running stable at a film thickness as low as 12 μm, using less raw material and enabling higher production line speed
- Typically used in both mono and coex films and is available as a certified renewable grade
- Provides full compliance with stringent food-contact regulations for a broad range of applications with both fatty and non-fatty foods
SAFER PACKAGING
SABIC continues to take a pro-active role in the industry by improving the purity, organoleptic properties and cleanliness of resins used in PET and food packaging:
- Introduction of new product stabilizers in advanced LLDPE resins
- Introduction of phthalate-free PP solutions, co-developed with international companies in the UAE and Europe
- Unique additive-free LDPE product family (with no migration into food)
Advanced 5-layer barrier film structures are another new product from SABIC for applications in meat packaging by using blown film technology. The use of high-purity SABIC® LLDPE 218BE and LDPE resins was crucial to achieve improved draw ability and cleaner operations, with fewer deposits.
Maintaining water purity with SABIC® HDPE CC860V grade for Caps & Closures for still water
- Rated highly amongst available grades, it is now being used by leading OEM brand owners
- Provides excellent organoleptic properties that are important in preserving taste and odor
- Complies with new food-contact directives regarding product safety and purity
SABIC’s new range of PP copolymer cast films may offer extra protection with high puncture and tear resistance, excellent sealability, eye-catching optics, and compliance with food regulations.
SUSTAINABILITY
SABIC is proud to be the first chemicals company to offer both renewable polyethylene (PE) and polypropylene (PP) resins that are based on renewable feedstock sources. SABIC’s ISCC Plus-accredited renewable polyolefins help our customers meet increased regulatory demands. Unlike other products on the market, these new materials from SABIC are created using waste fats and oils and they use feedstock that is not in direct competition with the food chain. From sourcing to final production, SABIC’s renewable PE and PP require 84% less fossil fuel to manufacture than fossil-based polyolefins, and are fully recyclable. This enables SABIC, and our stakeholders, to reduce our collective carbon footprint and to save fossil feedstocks for future generations.
SUPERIOR PERFORMANCE – POLYETHYLENE WITH THE NEXLENE™ PROCESS TECHNOLOGY
SABIC produces its new C8 mPE, POP and POE products using NEXLENE™ technology – a cutting-edge technology that combines a solution process and a proprietary metallocene catalyst. The packaging industry will benefit from this new SABIC product family with state-of-the-art molecular design – Bimodal Solution Process with Octene co-monomer – for the manufacture of flexible (food) packaging and wrapping materials that deliver high performance properties such as:
- Outstanding processability: may enhance bubble stability, lower motor load and extrusion pressure
- Superior mechanical performance: may improve tear resistance, excellent puncture and dart impact resistance and tensile strength
- Outstanding sealing property: may lower sealing initiation temperature (SIT) that enables faster packaging speed
- Excellent optics with high clarity and very low haze
- Superb hygienic properties with low extractables and outstanding organoleptics
SABIC will be participating in K 2016 in Düsseldorf, from 19 to 26 October 2016, at Stand D42 in Hall 6. For more information, please go to www.sabic.com/Kshow.