Koplas is South Korea's most important trade fair for the country's plastics industry, taking place every two years. More than 450 exhibitors from 26 countries will convene in the Kintex exhibition centre in Goyang in the Seoul metropolitan area from 7 to 11 March 2017. This year, Arburg is represented with its own exhibition stand for the first time at the Koplas. In Hall 5, stand P530, two exhibits will demonstrate how high-quality series injection moulded parts can be produced cost-effectively with electric and hybrid machine technology from Arburg.
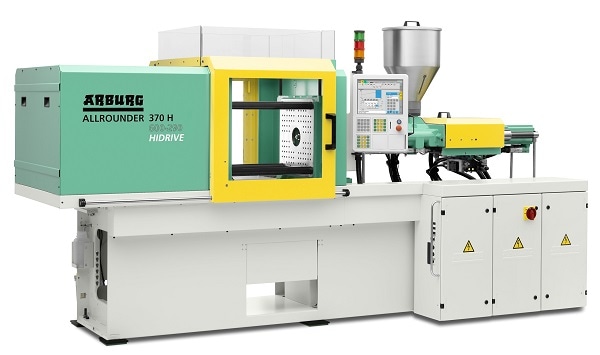
- Highlight: Leading trade fair for the South Korean plastics industry
- Premiere: Arburg with its own exhibition stand for the first time
- Efficient: Hybrid and electric Allrounder produce high-end, high-volume parts
With the production of stacking boxes, an Allrounder 470 E Golden Electric with 1,000 kN clamping force and size 290 injection unit demonstrates the potential of the new electric entry-level machine series which Arburg launched onto the market in 2016. The Allrounder 370 H is presented by Arburg as the smallest machine of the hybrid high-performance Hidrive series. The exhibit with 600 kN clamping force and size 170 injection unit manufactures the coveted toy buggy from Arburg with a 1+1+2-cavity family mould; an Integralpicker V removes the sprue.
Allrounder Golden Electric: Entry into the electric machine world
The high-performance electric Allrounder Golden Electric machines are designed for the precise and energy-efficient production of complex moulded parts. With this equipment, the new machine series meets the demands of the international market for electric machine technology in a practical size range, combining important features for modern injection moulding production, such as precision, energy saving and reproducibility, at an excellent price.
The series developed for standard thermoplastic processing applications combines consistently standardised component assemblies. This applies, for example, to the fixed combination of distance between tie-bars, clamping force and injection unit size. An excellent price-performance ratio can be achieved in this way. The new machines are available in four sizes with clamping forces of 600 to 2,000 kN.
High-performance technology
High performance and the associated fast cycle times are ensured by the double five-point toggle system and the high-precision, play-free spindle drives. The position-regulated screw enables cavities to be filled with a high degree of repeat accuracy, which is reflected in high moulded part quality. Liquid-cooled motors and servo inverters bring benefits in terms of energy efficiency, short dry cycle times and a high level of reproducibility. The high efficiency of the servo motors, continuous power adaptation and energy recovery during braking result in energy savings of up to 55 percent compared to standard hydraulic machines. Ease of maintenance thanks to swivelling injection units, plug-in cylinder modules and further improved lubrication and cooling are additional important features of the new Allrounders.
Hidrive: Combination of hydraulic and electric machine components
The hybrid Allrounders of the Hidrive series are designed for high production performance in thermoplastics processing. The combination of servo-electric toggle, electric dosing and hydraulic accumulator technology ensures precise, dynamic injection and high performance. Simultaneous machine movements reduce the cycle times, bringing significantly greater cost effectiveness to production. Interesting technical detailed solutions minimise set-up times, keep the dry cycle times of the toggle-type clamping unit extremely short and ensure that moulded parts fall in a particularly precise, reproducible way thanks to synchronous ejection. Energy savings of up to 40 percent can be achieved compared to hydraulic machines.
The hydraulic accumulator technology of the machines is the central element with regard to injection volume flow dynamics. High-speed sequences in conjunction with the automated components of production systems are achieved though the extensive programming options of the Selogica control system for simultaneous production processes.