When mixing bulk solids, residues can pose the threat of cross contamination or introducing product impurities so what are the options for mixer cleaning if these threats are to be avoided.
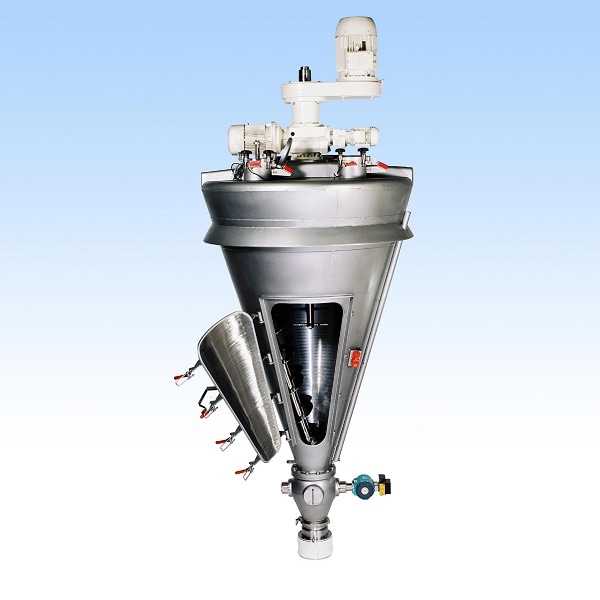
As rinsing mixer and screw with water and cleaning agents brings unwanted moisture into the system which can cause creation of lumps in the product, wet spots behind O-rings or gaskets and generate vast quantities of contaminated water or other cleaning fluids that have to be dealt with, here we consider the best dry cleaning approaches to minimise the propagation of bacteria.
Stewart Bryan, Hosokawa Micron Ltd, suggests, ‘Let us firstly look at the options to reduce the cleaning effort required by reviewing the process design, the vessel used, material transfer steps and any liquid additions. It is often the case that original processes are simply repeated even though the products involved have changed thus generating your own problem. Often it is difficult to review the process without bias and you may find speaking with a powder processing specialist such as Hosokawa can help.
Secondly look at the mixer design, what are the features that will aid dry cleaning regimes for minimising cross contamination’.
- Conical mixer designs, with inclined surfaces and gravity discharge leave little opportunity for powders to form residues. In the case of the Hosokawa Vrieco Nauta Conical Mixer there are no horizontal or vertical partitions or sharp corners and as few joints, flanges and seals as possible come into contact with the product eliminating the potential to harbour residue.
- For restriction free discharge a central bottom outlet offers best options for complete emptying.
- In a conical screw mixer opt for open screw flights.
- Powders simply slide off smooth surfaces without seams so a one part mixer is ideal for dry cleaning. With these and other sanitary design features only an extremely low amount of residue (<0.05%) remains when the Vrieco Nauta mixer is emptied, minimising the risk of subsequent batch contamination
Common deposit collection zones
Zone 1 is the surfaces above the product level of the filled mixer, mainly caused by dust, dispersed by filling. This can easily be blown away by compressed air.
Zone 2 is the surface of the vessel below the filling level, in contact with the movement of powders. Addition of liquids to the mixture will increase adhesion to the mixer wall. Cleaning with a cloth may remove such residue.
Zone 3 the mixing screw and in particular the underside of the blades can be difficult to clean without brushes and friction tools to break the residue from its bond with the blade.
Whilst CIP dry cleaning of residues is both difficult and time and labour intensive Hosokawa Micron Ltd suggests a number of solutions to enhance the cleaning of conical mixers that can be applied to both dry bulk powder mixing and moist mixtures containing a small percentage of liquid.
Enhanced Mixer Dry Cleaning
A large inspection door in the vessel wall creates an opening through which the operator can easily access all surfaces to be cleaned. Areas for special cleaning consideration include screw flights and the lower surface of the screw blade. The large opening also aids visibility of areas to be cleaned. The full and correct closure of this door is a significant safety factor when the mixer is in operation.
A semi domed cover, welded to the cone, offering a large radius and no crevices in which bacteria might settle offers enhanced cleanability.
Hosokawa’s Isem ball segment valve with its rounded interior surfaces reduces the possibility for material deposition to a minimum. An inspection port in the valve is available as standard. In case deposits have to be removed this can be done using special tools.
‘Of course there are many, mainly wet or sticky mixing applications where dry cleaning is not an option and wet cleaning is inevitable. In the case of the example, Vrieco Nauta mixer, there are enhanced wet CIP options that are more appropriate,’ explains Stewart Bryan.