Manufacturing productivity and efficiency specialist, Leader Chuck International (Stand D23) will launch the new B-Safe machine tool monitoring system at this year’s Advanced Engineering show, held at the NEC, Birmingham from the 31 October to 1 November 2018.
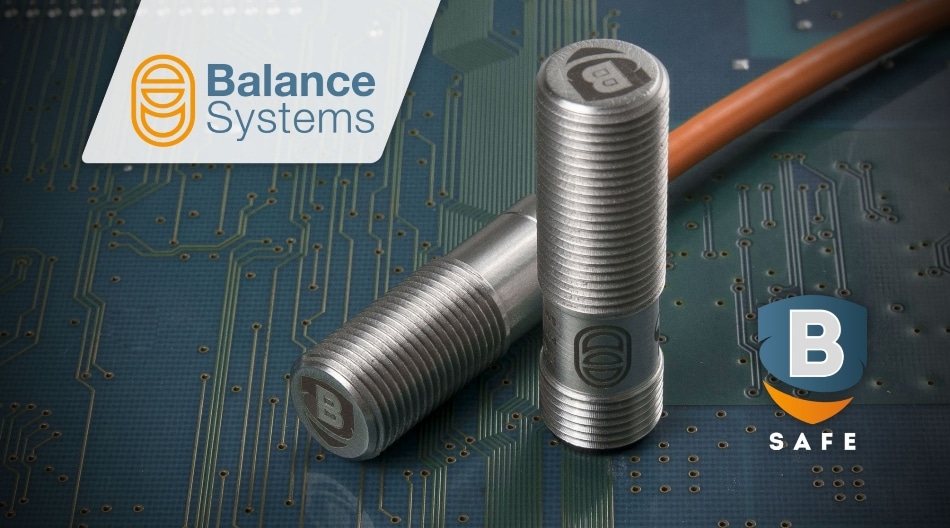
B-Safe is a new concept that supports the complete monitoring and diagnostics of spindles and machine tools using vibration and temperature analysis. The miniaturised system can be directly installed into any machine spindle guaranteeing a real-time monitoring of all anomalies, predicting malfunctions and safeguarding businesses by reducing the machine downtime.
Managing Director, Mark Jones, explains: “B-Safe provides collision protection and can stop either the spindle or the whole machine within milliseconds, monitoring is continuous even when the machine is switched off, a ‘black box’ embedded data logger stores events locally, and it is designed to support the growing move towards IoT and Industry 4.0.”
Comprising an advanced sensor, an interface switch and a user-friendly software platform, B-Safe can be easily retro-fitted to any machine tool. At just 12 mm diameter the sensor contains hybrid technology MEMS 3D and piezoelectric sensing to guarantee complete signals analysis on a wide band. The inclusion of a microprocessor with integrated memory allows local detection and on-board memory data logging of collisions, unbalances, overloads, anomalies of the working cycle, tool wear and bearing diagnostics. It provides evidence for predictive maintenance at a glance.
The software program provides a ‘dashboard’ where all the parameters and thresholds for the sensor can be set up, monitored and viewed over logged time, and any alarms can be investigated and fully analysed. The wide range of functions within the software allows users to manage the whole process with one single system.
For example, its Spindle Check-Up function includes a series of algorithms to check the efficiency level of the production process, with the aim of maximising the productivity of the machine’s spindle and the quality of the products. The statistical analysis provided by the system provides essential support for planning maintenance interventions, according to the real use of the equipment.
Events recorded by the sensor include collision alarm, temperature alarm, overloading alarm, with programmable thresholds to stop the spindle, and the 5-day battery back-up with memory integrated on the sensor means alarm events are recorded even when the machine tool is powered down. Real-time data for process-monitoring and digital data for post-processing of data logged events supports statistical analysis and historical trend awareness.
Key parameters shown on the dashboard can be customised so that only events or trends that are important to each user are shown, and authorisations levels can be set such that users are view only or have the ability to interrogate the data and adjust parameter setting or thresh-holds.
Sensors can be specified in two formats, hardwired to an integrated 5 m cable or with a 5-pin connector, to suit the installation application. In either format the rugged sensor can reliably operate between -40 and +85 oC and is robust enough to withstand a 10 kg shock load under collision conditions.
Mark Jones concludes: “B-Safe is a set of different evolved technologies, that has been developed to allow machine tool users to create a distributed and interconnected system of analysis and supervision for any production plant.”