LANXESS is expanding the new polyamide 6 Durethan P product range with the addition of two highly reinforced material variants that can be used, among other things, as an economical alternative to polyamide 66 materials. Durethan BKV50PH2.0 and Durethan BKV60PH2.0EF have short glass fiber content levels of 50 and 60 percent by weight respectively. The “P” in the product name stands for “Performance” and indicates the high fatigue resistance of these materials against pulsating loads. This means that these grades are many times more resistant to cyclical mechanical loads than standard products with the same glass fiber content.
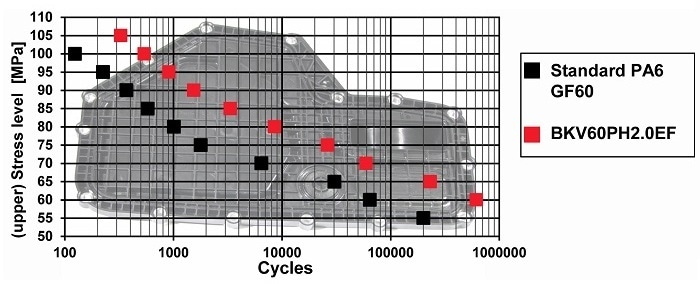
Potential applications include supporting structures for electrical and electronics modules in batteries for electric vehicles, engine oil pans, oil filter modules and end caps, engine and chassis mounts, damper pistons, and seat shells for passenger cars. In mechanical engineering, the new materials are suitable for dynamically highly stressed components such as gear wheels.
Substituting Polyamide 66 While Maintaining Component Weight
The mechanical properties of both high-modulus thermoplastics are at a high level similar to those of comparable polyamide 66 materials. “As a result, we also see both product innovations as cost-effective alternatives to polyamide 66 compounds, which have become significantly more expensive recently due to their limited availability,” explains Dr. Thomas Linder, an expert in the development of Durethan. Tests at LANXESS revealed that it is possible to use product variants with the same glass fiber content and therefore the same material density as substitutes. As a result the component weight does not increase.
At Fakuma, the international trade fair for plastics processing, in October 2018, LANXESS had presented the first representatives of the new product range with Durethan BKV30PH2.0, BKV35PH2.0, BKV40PH2.0, and Durethan BKV130P. Their glass fiber content levels are between 30 and 40 percent. Conceivable applications include air intake and oil filter modules for cars as well as load-bearing housings of power tools. The elastomer-modified Durethan BKV130P is particularly impact-resistant and is suitable for furniture locking system components, for example. All four compounds are also suitable substitutes for polyamide 66.
Better Tensile Strength at Higher Temperatures
Like their “siblings”, the two new highly reinforced compounds are characterized by improved mechanical and structural properties. “For example, their tensile strength at high temperatures is higher than standard polyamide 6 variants with the same glass fiber content,” says Linder. To assess this behavior under a pulsating load, LANXESS has developed a HiAnt fatigue screening test that is based on a conventional Wöhler test. This revealed that under a transverse load of 65 megapascals, the lifespan of Durethan BKV50PH2.0 is around eight times longer than that of a standard polyamide 6 with the same glass fiber content. In a corresponding comparison, Durethan BKV60PH2.0EF demonstrates a fatigue behavior that is around ten times better.
At the same time, Durethan BKV60PH2.0EF is characterized by its good flow properties (easy flowing, EF). The thermoplastic is therefore easy to process despite its high degree of glass fiber reinforcement. Its flowability is of a similarly high level to that of a polyamide 6 with glass fiber content of 30 to 35 percent.
HiAnt – Customer Service Right Through to the Start of Production
The services with which LANXESS supports project partners during the development of components for use under pulsating loads include a wide range of component tests. “The equipment at our shaker technical center covers all current vibration tests for the fatigue behavior of components in vehicle applications,” explains Linder. Its customer service also includes pressure threshold tests on components from the vehicle cooling circuit as well as pressure change and backfire tests.
All these services are part of HiAnt. Under this brand, LANXESS has bundled its engineering expertise in the development of thermoplastic components for customers.