Juki Automation Systems (JAS), Inc., a world-leading provider of automated assembly products and systems and part of Juki Automation Systems Corporation, will exhibit at SMTA International, scheduled to take place Sept. 24-25, 2019 at the Stephens Convention Center in Rosemont, IL. Juki’s team will showcase the RS-1, G-Titan, ISM UltraFlex 3600 and the Incoming Material Station (IMS) in Booth #1026.
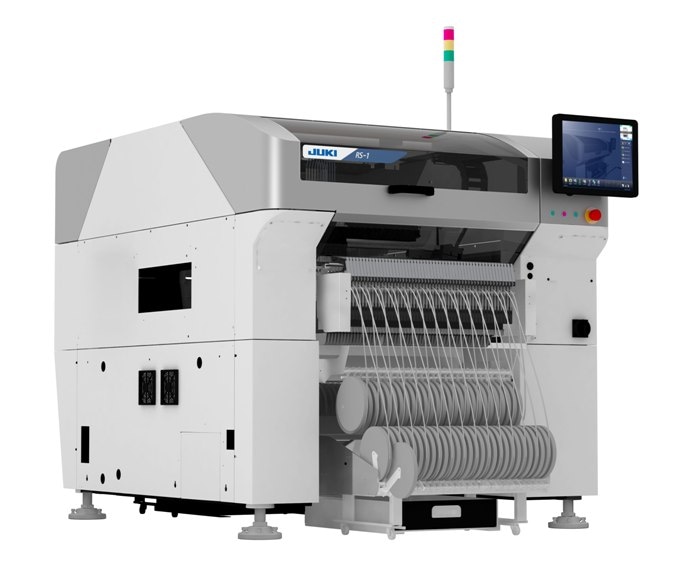
In the past, the placement head had to be mounted high enough for the tallest component on the PCBA, resulting in excess movement for short components. Now, the RS-1 features the Takumi head, a dynamic height, 8 nozzle placement head that automatically adjusts pick-and-placement height on-the-fly to optimize speed, resulting in the highest possible CPH. With the new offline teach camera and JaNets/NPI Plus software, the RS-1 provides easy data entry for faster programming for both standard SMT and odd-form parts.
The new G-Titan screen printer from Juki with industry-leading “standard” features empowers customers with the highest quality printing solution, a path to Industry 4.0, and “Lights-Out-Manufacturing” with its award-winning specifications. The printer features a new interface with a modern look and many standard features, including touchscreen LCD, stencil inspection, solder paste rolling measurement, stencil lock, support block crash prevention and automatic solder paste dispense (500g jar).
Intelligent and efficient storage management is turning into the key success factor regarding SMT manufacturing. Intelligent storage systems provide complete inventory control and increases the efficiency of production lines.
Juki’s ISM storage management system provides you with this intelligent and flexible storage solution and helps you refocus on your value-adding activities. Using the ISM UltraFlex 3600 you will be able to flexibly store up to 3,644 reels, monitor them intelligently, as well as oversee the fully automatic import and export of the components.
With the Incoming Material Station, operators can speed up material registration activities, avoid mistakes, and increase the traceability of each individual reel or component package. With its Auto-Incoming features, it is possible to automatically import information from the supplier and/or customers’ label into the ERP and print a new Unique ID that can be used for many other functions within the factory. In fact, after setting the rules for each supplier’s label, the operator can simply position the material on the Station and the high-resolution camera will read all the needed codes and information, take a picture for traceability purposes and print the new label.