MakerBot has launched METHOD X that amplifies accessible 3D printing with real ABS, a 100 °C build chamber, and SR-30 supports designed for end-use parts and manufacturing tools. It is engineered to challenge traditional manufacturing and deliver complex parts with precision and accuracy.
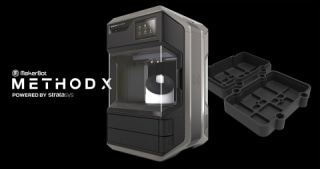
“With METHOD X, we are taking a step further to revolutionize manufacturing. METHOD X was created for engineers who need true ABS for production-ready parts that are dimensionally accurate with no geometric restrictions. METHOD X delivers industrial-level 3D printing without compromising on ABS material properties and automation in a new price category,” said Nadav Goshen, CEO, MakerBot.
Challenging Traditional Manufacturing with Real ABS
METHOD X, a manufacturing workstation is engineered to challenge traditional manufacturing with real ABS (acrylonitrile butadiene styrene) material, and Stratasys SR-30 soluble supports to deliver exceptional dimensional accuracy and precision for complex, durable parts.
METHOD X is capable of printing real ABS that can withstand up to 15 °C higher temperatures, is up to 26% more rigid, and up to 12% stronger than modified ABS formulations used on desktop 3D printer competitors. Real ABS parts printed on METHOD X have no warping or cracking that typically occurs when printing modified ABS on desktop platforms without heated chambers.
MakerBot METHOD X - Meeting the Manufacturing Needs
MakerBot ABS for METHOD has excellent thermal and mechanical properties like ABS materials used for injection molding applications—making it ideal for a wide range of applications, including end-use parts, manufacturing tools, and functional prototypes. A 100°C Circulating Heated Chamber provides a stable print environment for superior Z-layer bonding—resulting in high-strength parts with superior surface finish. With the MakerBot METHOD X, engineers can design, test, and produce models and custom end-use parts with durable, production-grade ABS for their manufacturing needs.
METHOD X is the only 3D printer in its price class that uses SR-30—enabling unlimited design freedom and the ability to print unrestricted geometries, such as large overhangs, cavities, and shelled parts. The combination of SR-30 and MakerBot ABS is designed to provide outstanding surface finish and print precision.
Industrial Features of METHOD X
Engineered as an automated, tinker-free industrial 3D printing system, METHOD X includes industrial features such as Dry-Sealed Material Bays, Dual Performance Extruders, Soluble Supports, and an Ultra-Rigid Metal Frame. METHOD X’s automation and industrial technologies create a controlled printing environment so professionals can design, test, and iterate faster. The lengthened thermal core in the performance extruders are up to 50% longer than a standard hot end to enable faster extrusion, resulting in up to 2X faster print speeds than desktop 3D printers.
These key technologies—combined with MakerBot ABS for METHOD—are designed to help engineers achieve dimensionally-accurate, production-grade parts at a significantly lower cost than traditional manufacturing processes. Engineers can print repeatable and consistent parts, such as jigs, fixtures, and end-effectors, with a measurable dimensional accuracy of ± 0.2mm (± 0.007in).
MakerBot METHOD X’s automated and advanced features provide users with a seamless workflow to help them optimize their design and production processes. The MakerBot METHOD X is considered to be one of the most intelligent 3D printers on the market, with 21 onboard sensors that help users monitor, enhance, and print their projects, including RFID chips, temperature sensing, humidity control, material detection, and more. The METHOD platform provides a seamless CAD to part workflow, with Solidworks, Autodesk Fusion 360 and Inventor plug-ins and support for over 30 types of CAD files, helping users turn their CAD files to parts quicker.