Greene Tweed, a leading global manufacturer of high-performance seals, thermoplastics, composites, and engineered components, highlights WR®650, a next-generation PFA composite with superior dry run characteristics designed to replace metallic wear parts in centrifugal pumps and other pump applications.
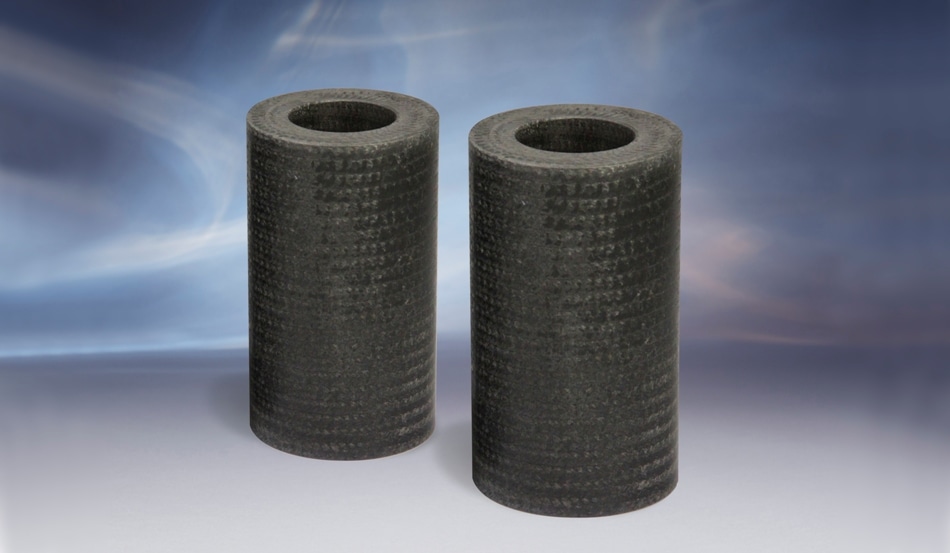
Metallic wear parts fail quickly in dry run conditions, giving pump operators limited time to restore lubrication or shut down a pump before costly damage occurs. High quality composite parts increase this effective response time and can extend the mean time between repair. Reinforced with a 3D carbon-fiber architecture, WR®650 can sustain 2.5-times higher dry wear conditions before showing signs of degradation when compared to the leading PFA-based material.
WR®650 delivers high chemical compatibility, excellent wear characteristics, and operability from subzero to 500 °F (260 °C). The advanced material also possesses a coefficient of thermal expansion comparable to steel over a wide range of temperatures, offering a constant running clearance, no interference, and no efficiency drop. Unlike metallic wear components, the malleable nature of PFA ensures metallic counter-parts are preserved, even those that are relatively soft. This helps to extend pump service life and improve reliability. Plus, WR®650’s non-galling/non-seizing characteristics and ability to dampen vibrations allow for tighter clearances and increased efficiency compared to traditional metallic components.
Ideal for stationary wear parts in vertical, horizontal, single, and multistage centrifugal pumps, WR®650 can improve the mean time between repair for pumps in refineries, chemical plants, power plants, pipelines, and water treatment plants. WR®650 is available in a broad range of stock shapes, ranging from ID1” to OD12” and finished parts are available upon request.
In addition to WR®650, Greene Tweed offers the broadest range in the industry or high-performance materials for wear ring bearings and bushings, including compression molded PEEK™ WR®300 and WR®525 for normal wear applications, and AR®1 and AR®HT for abrasion-resistant applications.