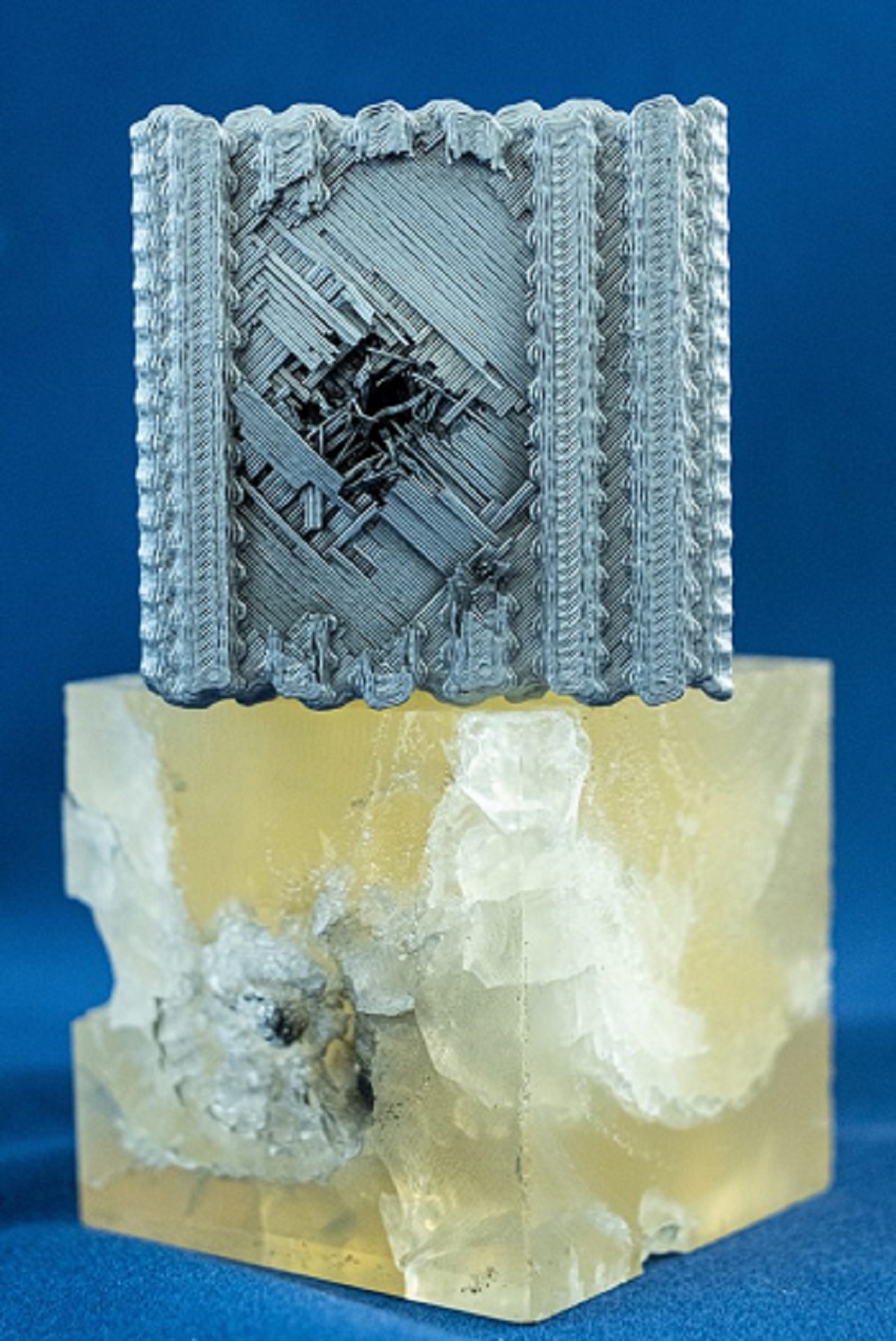
Image Credit: Jeff Fitlow/ Rice University
3D printing is an ever-evolving technology and one that continually reveals new applications, from concrete bridges to clean meat in space most things produced by the technology serve only as useful protypes for research and development.
Now, while investigating the complex architecture of a theoretical structure (known as tubluanes) a team of researchers at Rice University have 3D printed a solid object capable of stopping bullets in their path.
Initial theory surrounding tubulanes goes back to 1993 when chemist Ray Baughman and physicist Douglas Galvão predicted these theoretical microscopic structures that would be comprised of crosslinked carbon nanotubes would have incredible properties. Now, the Rice University team has demonstrated this by producing a lightweight structure that is almost as hard as diamond as well as being bullet-proof. Their research was recently published in the journal Small and describes the structure as, “a holy grail in materials design.”
The designs were based on the theory of tubulanes and simulated in a computer software system before being 3D printed from polymers to test a working version of the latticed design. “There are plenty of theoretical systems people cannot synthesize,” says lead author and Rice graduate student Seyed Mohammad Sajadi. “They’ve remained impractical and elusive. But with 3D printing, we can still take advantage of the predicted mechanical properties because they’re the result of the topology, not the size.”
To assess the strength of their scaled-up design the researchers conducted a comparison test using a solid block that was 3D printed using the same polymer material. They then fired ‘bullets’ traveling at 5.8 kilometers per second (almost 13,000 miles per hour) at both the tubulane-based latticed design and solid polymer cube. While both structures were able to remain somewhat intact, the solid polymer block was compromised by a huge dent and cracks that went all the way through, however, the bullet was stopped by the second layer of the latticed design, the rest of the structure was left undamaged.
Further to their ability of deflecting bullets, the latticed cubes were also highly compressible without crumbling or shattering, as demonstrated in the video below:
Theoretical tubulanes inspire ultra hard polymers
The unique properties of such structures comes from their complex topology, which is scale-independent. Topology-controlled strengthening or improving load-bearing capability can be useful for other structural designs as well.
Chandra Sekhar Tiwary, Rice Alumnus, Co-lead Author of the Paper and Assistant Professor at the Indian Institute of Technology, Kharagpur
When subjected to immense pressure the tubulane-based lattice structure collapsed in upon itself which absorbs the stress and tension and keeps the structure intact. A similar phenomenon was also observed when the lattice cube was hit with the fast-moving projectiles. Previous assumptions thought that a porous structure reduced an object’s ability to withstand such conditions, yet, the properties of the polymer latticed cubes allowed them to absorb the energy of impact, curb damage, and prevent the object being structurally compromised.
Furthermore, Sajadi states that object design based on the theory of tubulanes can be produced using a wide range of materials including metal, ceramic and polymer and would only be, “limited by the size of the printer.” This could usher in a new age of exciting design applications in the fields of construction, automotive industries, aerospace, biomedicine, sports equipment, and lightweight, ultra-strong packaging for commercial goods. Oil and gas industries could also benefit from tubulane-like structures for well construction as materials must be able to resist consistent impact.
So, while everything from architecture to sports equipment could be revolutionized by the pioneering research of the Rice University team, their findings could potentially also give 3D printing a boost in manufacturing.
Parts or components that had to be fabricated from metal or ceramics could potentially be printed from cheaper polymers. This would move 3D printing from the confines of being used for creating prototypes that won’t be subjected to tremendous stresses and arduous tasks to producing workable components and structures that can handle the wear and tear of everyday use.
Disclaimer: The views expressed here are those of the author expressed in their private capacity and do not necessarily represent the views of AZoM.com Limited T/A AZoNetwork the owner and operator of this website. This disclaimer forms part of the Terms and conditions of use of this website.