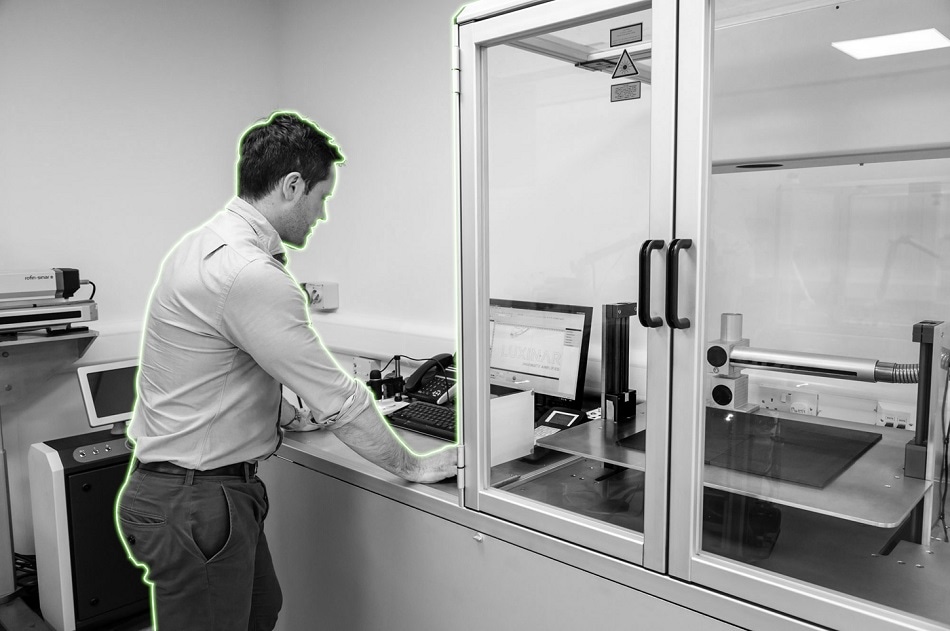
Technical support is key for buyers of CO2 laser sources in order to find the product that is best suited to their marking, cutting, drilling or scribing process. At Luxinar, a global leader in laser technology, this service is provided by our applications laboratories, a team of engineers with a wealth of applications knowledge, and a huge database containing details of all the application tests we have carried out over the years.
Application Testing at Luxinar
At Luxinar’s applications laboratories we carry out free-of-charge testing on product samples received from new and existing customers and OEMs. We can trial laser processes including cutting, marking, engraving, drilling and ablation, and we are able to work with an almost endless list of materials, including plastics, textiles, leather, wood, paper and card, metals, rubber, glass and ceramics. This service allows you to identify the best laser for your application before you commit to buying from us. In addition, our applications engineers can give general advice on all aspects of the laser process including laser parameters, beam delivery, fume extraction, and workpiece holding fixtures. Although we only provide the laser source and do not sell the full system, we can guide you towards a solution which meets your needs.
Our applications engineers will work with you to replicate the conditions of your application as closely as possible in the lab. Upon completion, you will receive a detailed report outlining our findings, along with some laser-processed samples for your evaluation. Most application tests can be completed within 10 working days, although complex projects may take slightly longer.
For a more in-depth proof of concept, you can hire the laboratory for a day or two, at a cost. Under normal circumstances you are welcome to attend our facility in order to witness your application trials; however, this may not be possible at the present time, due to coronavirus restrictions.
Luxinar in the UK has the largest facilities, with two applications labs, staffed by a team of experienced applications engineers. Our labs are equipped with lasers from the OEM, SCX and SR series of laser sources, with power levels ranging from 125W to 1kW, as well as the MULTISCAN laser marking systems. Other equipment includes a robotic cutting cell, on-the-fly label marking simulators, a flying optic setup for industrial cutting applications, and 2D and 3D scanning test stations. Different laser wavelengths are available, namely 9.3µm, 10.25µm and 10.6µm, in order to optimise processing performance for certain materials, particularly plastics. Inspection equipment includes an optical microscope, which allows us to provide you with detailed images of laser-cut edges and precise measurement of feature sizes. We always aim to simulate your process as closely as possible, providing you with meaningful results and constructive, practical advice.
At the Luxinar regional offices in China, Germany, Italy, South Korea and the USA we offer a smaller selection of lasers and equipment for application trials, including a MULTISCAN VS, various laser heads, scanners and motion stages. A team of colleagues is available to assist with your enquiries, wherever you are in the world.
Applications Database
Our applications database contains over 2000 entries. It holds details of every application test Luxinar has carried out since 2007, and typically includes information on the test objectives, what experiments were carried out, what laser system was used, details of the laser parameters used to optimise the process, along with a full description and photographs of the results.
Should you approach us with a new project, the information held in the database helps us to advise you, and to provide you with some general information based on our previous experience. For example, we may be able to estimate the likely cutting speed for a given material, thickness and laser power. This preliminary information will help you to decide whether to proceed with a proof of concept, by sending product samples to us for testing. We can then provide more specific information and detailed recommendations, backed up by test results on representative samples from you. Of course, we are sometimes asked about novel applications and materials of which we have no prior knowledge. In these cases, we will always ask you to provide samples for us to test; the results of these experiments are then added to our database for future reference. We operate across a wide range of markets, and we welcome the challenge of working with new and unusual applications and materials, for creative and innovative projects.
We understand that the details of your project may be confidential, and that you may need to share sensitive information with us in order to fully benefit from our application testing service. Access to our applications database is strictly controlled, and no proprietary information will ever be shared outside our organisation. We are happy to carry out application work under NDA if required, for your peace of mind.
Applications Laboratory Case Study: Seatbelt Cutting
The service provided by our applications engineers can speed up your product development and production line integration process and increase your chances of a successful outcome. A recent example is the following seatbelt cutting application from China.
Back in January 2020 one of our UK-based applications engineers received 3 rolls of seatbelt webbing from her counterpart at Luxinar China. A Chinese customer needed a laser to cut the material to the right length, rounding off the corners at the same time.
The applications engineer knew that we had tested similar applications before, so she could refer to the application database for details. This information provided a starting point for the trials, significantly speeding up the test process. A well-known advantage of laser cutting is that it melts synthetic textile fibres, “sealing” the cut edges so the fabric doesn’t fray. However, this melting effect often causes the edges to be slightly thickened and hardened, something which this particular customer was keen to avoid. The applications engineer used a 110W laser, the SR 10i, to carry out the cutting. She carried out a series of experiments to optimise the process, and a few days later she sent a selection of laser processed samples along with her report to China.
In April of this year, the managing director of the Luxinar China office emailed the applications engineer with the good news that the customer had ordered two SR 10i units with confidence, thanks to her successful sample testing. This was an impressive result, not least because most of the activity took place during the restrictions imposed upon us all by coronavirus.
In summary, the technical support team at Luxinar provides a valuable service to buyers of CO2 lasers across a wide range of industries and market sectors.We offer rapid sample turnaround times, detailed information and practical advice, and easy access to our applications team if required.Close liaison between our applications, sales and aftersales staff ensures a straightforward journey from your initial enquiry to the delivery and installation of your laser.
To find out more about Luxinar and the uses of lasers in manufacturing, visit www.luxinar.com.