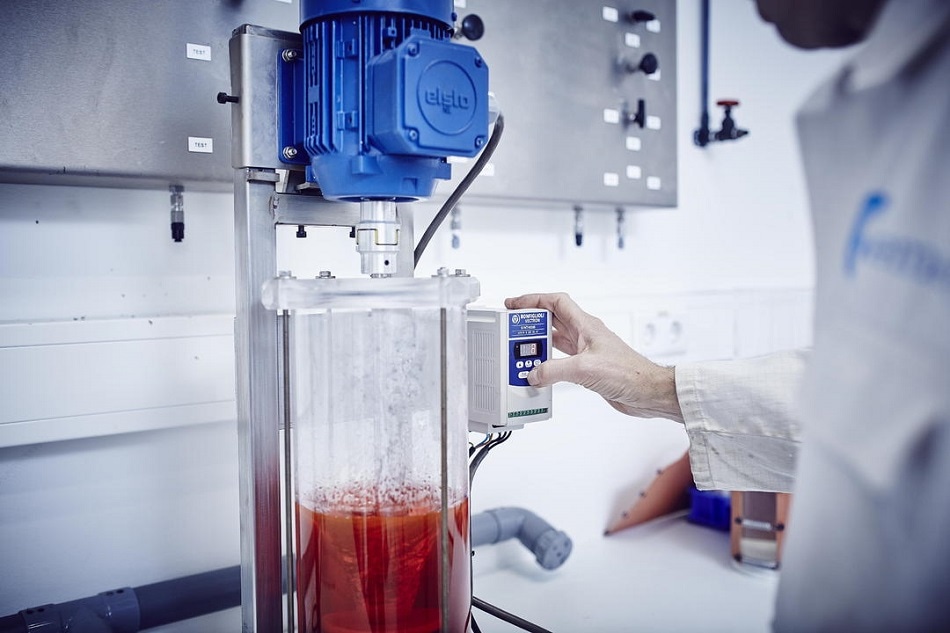
Element Materials Technology (Element) has further expanded its energy testing capabilities at its Amsterdam, Netherlands laboratory by adding additional corrosion inhibitor testing equipment.
The facility, which performs coatings and corrosion testing as well as failure analysis, has added another sweet corrosion inhibitor setup and a flow loop, significantly increasing the scope of Element’s inhibitor corrosion testing capabilities in order to simulate a wider range of service environments. In addition, a 3D optical profilometer has been added which allows experts to scan surface metrology and produce high-resolution imaging, post-corrosion inhibitor testing. The profilometer also allows the team to offer additional visual analyses in respect to failure projects and high-resolution surface product inspections.
The electrochemical test methods provide fast and accurate results in corrosion inhibitor investigations in order to determine and maximize the lifespan of metals used in a range of industries. Coupled with Element’s specialist knowledge of CO2 corrosion, H2S corrosion and galvanic corrosion, the service increases the scope of specialized corrosion services available to local and global customers across all sectors.
Michiel Graswinckel, VP Energy & Environmental Europe at Element, said: “This expansion of services in our Amsterdam laboratory will improve and speed up our ability to serve customers in these important markets. We remain committed to staying at the forefront of testing technologies globally, while working in partnership with our customers to develop highly technical test programs that best deliver for them.”
Element Amsterdam’s NEN-EN-ISO/IEC 17025 accredited laboratory provides a wide range of materials, corrosion and weld testing, as well as failure analysis services to the global energy sector. Its full suite of materials testing capabilities include mechanical testing, fatigue testing, failure analysis, chemical analysis and corrosion testing, including sour service corrosion testing (SSC, HIC and SOHIC). The facility offers unrivaled testing capabilities that simulate the environments in which metals are required to work, including: HPHT stirred autoclaves; acid gasses (sour and sweet); and the application of electrochemical monitoring systems in line with Shell’s Corrosion Inhibition Guidelines and International Standards.