The use of hydrogels is widespread in the development of electronics and biomedical devices. A new breakthrough could increase the range of materials that can be used in the creation of hydrogel hybrids, opening up a wide range of properties and uses.
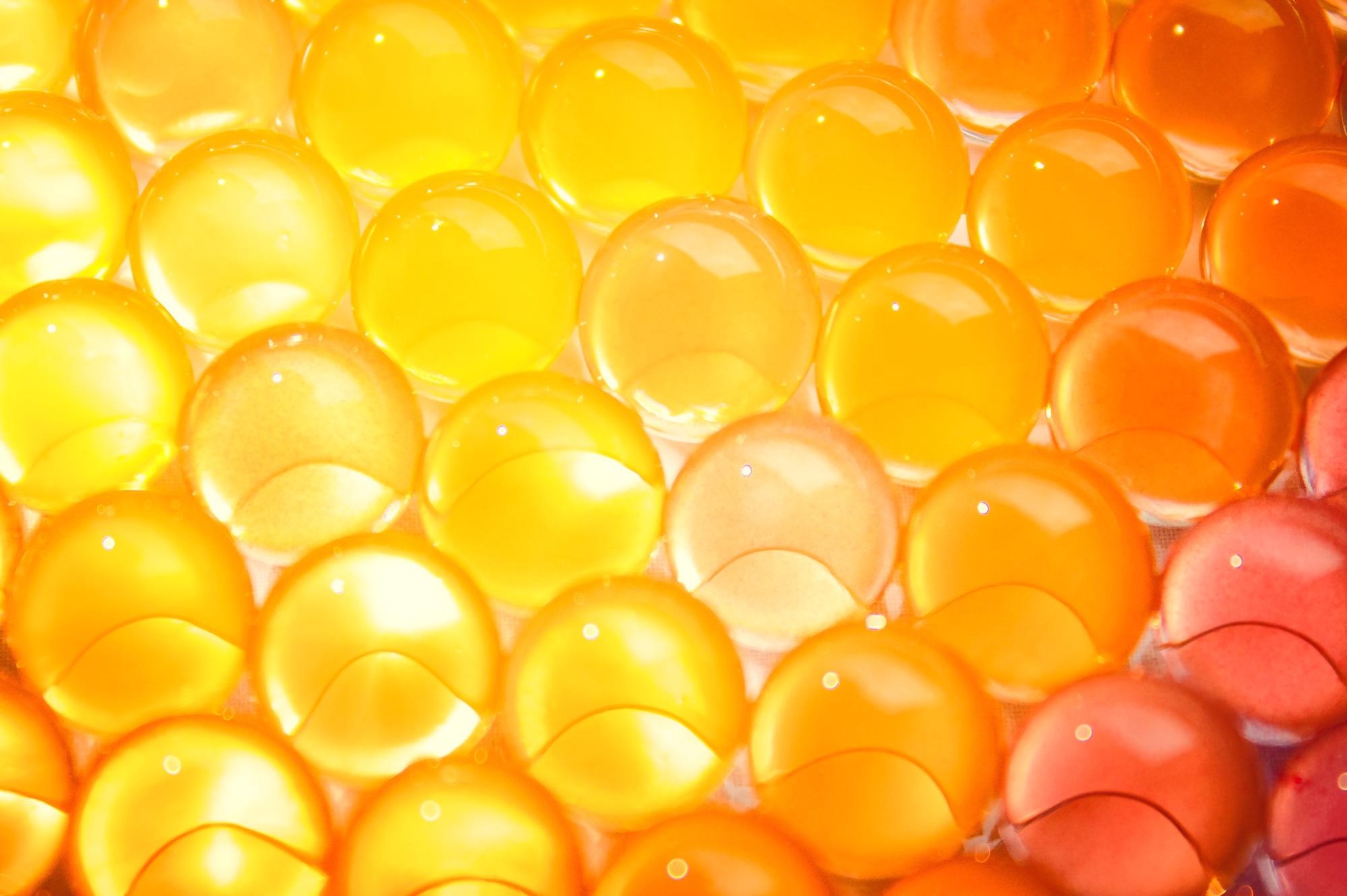
Image Credit: Alexa_Space/shutterstock
Hydrogels are hydrophilic 3D networks of polymer chains that are capable of retaining large amounts of water and provide impressive ionic conduction.
Despite being used in a wide range of varied applications, such as in flexible electronic devices and in biomedical devices, a significant drawback has hindered the efficiency of hydrogels.
Current technologies can only practically and efficiently fuse hydrogel polymers with laminates that also consist of silicone rubbers, which are used to provide protection and reinforcement.
This limitation has led to a desire to develop an approach to hydrogel-polymer–based hybrid fabrication that is both effective and delivers an increased choice of materials to deliver the same benefits as silicon rubber. Whilst simultaneously providing the same benefits as silicon rubber, these materials could equip hydrogels with a range of other properties.
A team of materials scientists, including researchers from the Department of Mechanical and Energy Engineering, Southern University of Science and Technology, Shenzhen, China, could have hit on such an approach.
Where the Rubber Meets the Road: Finding Alternatives to Silicon Rubber in Hydrogel Hybrids
In a paper published in the journal Science Advances, the team discusses the development of a versatile multi-material 3D printing approach that enables the fabrication of highly complex hybrid 3D structures consisting of highly stretchable and high–water content hydrogels that are covalently bonded with diverse water-insoluble UV curable polymers including an elastomer — a polymer with both viscosity and elasticity — and a rigid polymer.
The team printed their hydrogel polymer on a high-efficiency Digital Light Processing (DLP) based multi-material 3D printer — a 3D printer that uses UV light from a stationary projector that cures resin layer by layer. This allowed the team to build a ‘bottom-up’ approach and precisely control the thickness of each layer, resulting in the easy development of complex structures.
The team was able to utilize a range of commercially available polymer precursor solutions that were methacrylate-based monomers, cross-linkers and oligomers with non–water-soluble photoinitiators — molecules that create reactive species like free radicals, cations, or anions when exposed to UV light.
At the interface where the hydrogel met the elastomer, the team found that strong covalent bonds formed. Compression of the resulting material revealed that it could withstand 50% deformation before any debonding between these layers began to occur.
Adding a rigid polymer to the mix didn’t weaken the covalent bonding, with the hydrogel strongly bonding with both materials. The result was a foam that could withstand a high degree of stretching without debonding occurring between the three materials.
Peeling tests — generally used to test a material’s adhesive properties — conducted by the materials scientists showed that the energy needed to break their hydrogel-polymer interface is greater than the energy needed to break the hydrogel itself. This means an exceptionally tough, flexible material.
Further to this, the team says that the mechanical behavior and properties of the material they created can be adjusted by changing the PEGDA/acrylamide mixing ratio — the molecular weight of PEGDA — and the water content.
As the ability to tailor the material’s properties suggests, there is a wide range of applications for the new hydrogel-hybrids.
Flexible Applications Take Shape
The ability of the material to withstand large degrees of deformation without its layers debonding means that it can adapt to a variety of microstructures.
The team points out that amongst these is a horseshoe microstructure that could lend itself to biomedical applications in which the difference in flexibility between hydrogels and human tissues have traditionally presented difficulties.
The researchers demonstrated this by printing a meniscus consisting of AP hydrogel reinforced by Vero rigid polymer. Using the ability to vary the rigid microstructures to tune the local mechanical properties of the team's hydrogel-hybrid allows for adaptation to a wide variety of tissues.
Another medical use discussed by the team is the possibility of developing a cardiovascular stent that can widen and shrink by varying temperature. This allows the stent to not only widen blood vessels but also simultaneously administer drugs into a patient’s system.
The process created by the researchers could also improve on the ionic conductivity that makes such hydrogels so attractive in the development of flexible electronics. By 3D printing the hydrogel/elastomer with a lattice-shaped micro-structure, an elastomer protective skin can be created that protects the structure from water evaporation.
Improvements can also be made in this area by the inclusion of a strain sensor without reducing the bonding strength between the hydrogel and the elastomer.
The team’s breakthrough could result in a number of applications that take advantage of its multi-material 3D printing approach, paving the way to a new efficient way to build soft devices and machines.
References
Qi Ge., Zhe Chen., Jianxiang Cheng., et al., [2021], ‘3D printing of highly stretchable hydrogel with diverse UV curable polymers,’ Science Advances, [DOI: 10.1126/sciadv.aba4261]
Disclaimer: The views expressed here are those of the author expressed in their private capacity and do not necessarily represent the views of AZoM.com Limited T/A AZoNetwork the owner and operator of this website. This disclaimer forms part of the Terms and conditions of use of this website.