2020 was an extremely challenging year for companies in the automotive sector. Fortunately, the industry is slowly recovering. After a large decline in car manufacturing as a consequence of disrupted global supply chains, it is now time for a rebound.
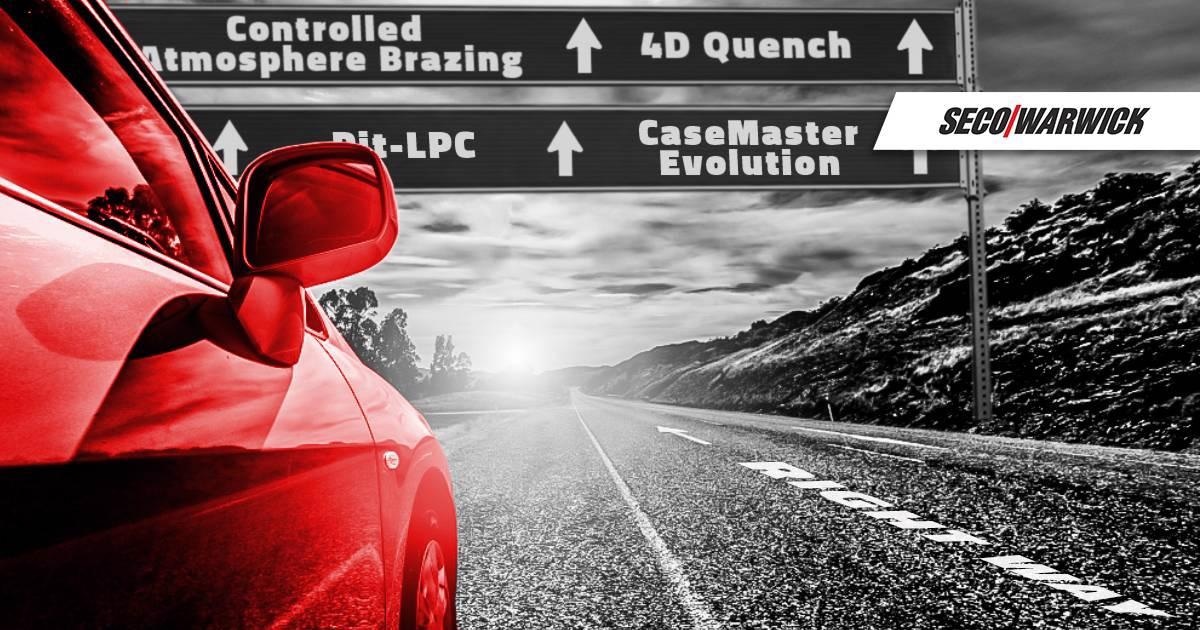
Image Credit: SECO/WARWICK
The automotive industry is actively looking for solutions that will lead to real reductions in production costs without sacrificing quality. This is reflected in the increase in orders from the automotive industry for metal processing solutions provided by SECO/WARWICK.
Heat treatment is used by the automotive industry to manufacture gears, bearings, shafts, rings, sleeves, and batteries for electric cars. What is most important to this sector is the reliability of solutions, their efficiency, and process repeatability. This is why the solutions addressed for this market sector must take into consideration the need to reduce distortion, lower the process costs, shorten the processing time, use efficient and effective carburizing technologies, and lower CO2 emissions.
After a difficult first and second quarter of 2020, the automotive industry is slowly beginning to rebuild its production capacity. This can also be seen in increased interest in new metal treatment technologies.
The automotive sector invests in R&D
“The ACEA report shows that as much as 29% of all EU R&D spending in the year preceding the pandemic was made by automotive players. This is an industry that is open to novelties, which is why we are actively looking for solutions that will effectively support production in the automotive area,” says Sławomir Woźniak, CEO, SECO/WARWICK Group.
“The flagship solutions for this sector include our vacuum furnaces, in particular the CMe® line of furnaces, the Pit-LPC® pit furnace, and the 4D® Quench®, our ground-breaking vacuum heat treatment system designed for individual nitrogen quenching of single elements. The segment of electric cars and the enormous contribution of the SECO/WARWICK Group to the manufacturing of such vehicles cannot be overlooked either,” adds S. Woźniak.
SECO/WARWICK solutions for the automotive industry
The traditional automotive industry has already chosen to use several SECO/WARWICK solutions, such as the CMe and CMe-T vacuum furnaces, the Pit-LPC pit vacuum furnace, and the 4D Quench vacuum system for nitrogen quenching of individual mechanical gear parts.
The family of CaseMaster Evolution vacuum furnaces is designed for semi-continuous case hardening by means of low-pressure carburizing and quenching in oil or gas, as well as for through hardening. The CaseMaster Evolution – T (CMe-T), our product of 2020, deserves some special attention here. This three-chamber vacuum furnace hardens surfaces using low-pressure carburizing and high-pressure nitrogen quenching technologies.
The CMe-T furnace can replace the existing lines and generators used for mass heat-treatment in a controlled atmosphere and oil quenching while ensuring higher precision and process repeatability. The distinguishing feature of this solution is improved process quality improvement and cost reduction. Thanks to doubling the performance and higher production flexibility, it has become a desirable solution for the automotive industry. Last year, this was a top solution in India, chosen by an Indian manufacturer of heat exchangers, among many others.
The Pit- LPC technology is popular among those manufacturers who need to carburize massive or longitudinal elements, such as gears, bearings, and other pieces requiring thick carburizing layers. This equipment guarantees three main advantages: cost reduction, production increases, and finally, safety and protection of the environment. All this is possible solely by running the process in a vacuum at higher temperatures. This state-of-the-art solution meets the most stringent environmental standards while increasing work safety by eliminating the use of flammable and explosive atmospheres. An Important consideration from the point of view of the automotive sector is that we also get high process uniformity, ensuring a better quality of work being processed.
The 4D Quench is a vacuum heat treatment system designed for individual nitrogen quenching of single elements of mechanical gearboxes, such as gears, shafts, rings, sleeves, etc., made of standard and custom case- and through-hardened steels. It significantly improves the precision and repeatability of the heat treatment results while reducing production costs. It provides vacuum heating followed by powerful and uniform nitrogen quenching, resulting in distortion control and reduction with high repeatability of the final result.
The electric car industry is not slowing down
SECO/WARWICK is the undisputed leader of CAB technology, which has been consistently popular among electric car manufacturers. For several decades, this has been the automotive industry’s technology of choice for manufacturing aluminum heat exchangers.
The projected growth of electric car use and the associated surge in demand for battery coolers bodes very well for the aluminum brazing and heat treatment segment. Numerous installations worldwide, technical experience, and an innovative approach make the CAB solutions by SECO/WARWICK the technology of choice for soldering radiator plates for hybrid (HEV) and electric vehicle (EV) batteries. In the first quarter of 2021 alone, SECO/WARWICK received several large orders to supply CAB lines for this application.
Real savings for hard times
Given the current market situation and declines in production, the automotive industry must seek to introduce systems that produce significant savings without sacrificing quality. With SECO/WARWICK vacuum solutions, the entire automotive sector could save billions of euros yearly.
According to an analysis carried out on this subject by the Bremen Institut für Werkstofftechnik starting in 1995, the cost of adjustments amounted to ca. 850 million euros per year in the German automotive and gearbox industry alone, and one billion euros yearly in the bearing sector. That is why it is so important to use equipment that shortens process time, eliminates material deformation, and ensures high quality of the final product at optimum cost.