Printing 2D functional materials is one of the current focuses of materials science. However, this has thus far proven to be problematic. A paper published in the journal Advanced Materials has demonstrated a novel and universal method for achieving room-temperature printing and coating of these industrially important materials.
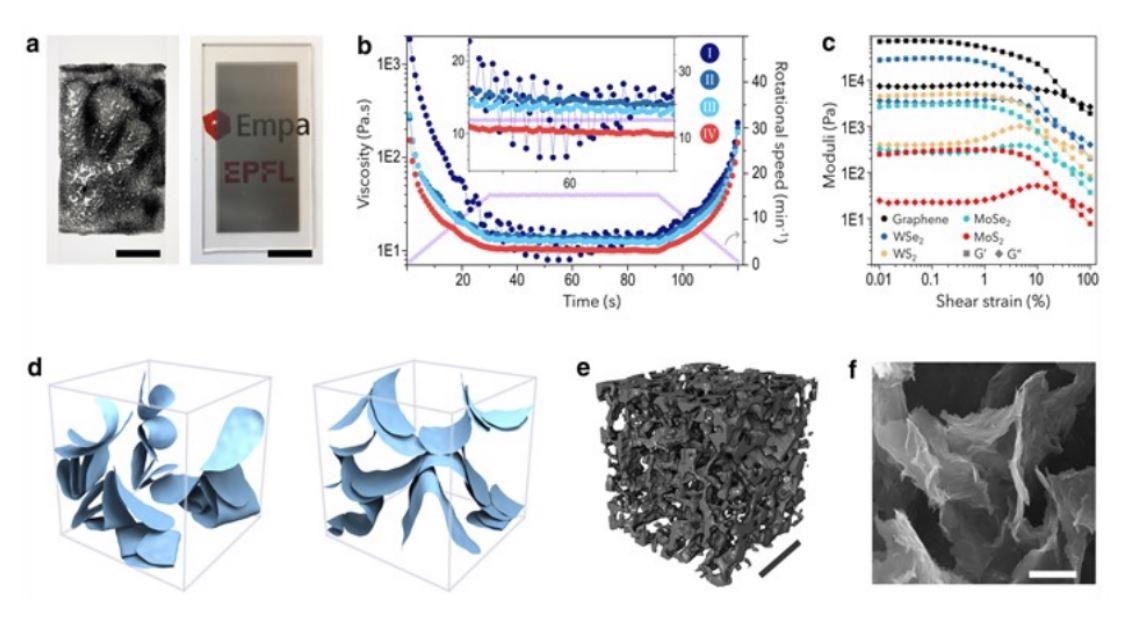
Structure and film-formation of aggregated 2D materials. (a) Left: An aggregated graphene dispersion in NMP (1 vol.%), capable of forming a gel. Right: A transparent film obtained from the same dispersion after homogenization (low-shear treatment). Scale bars: 1 cm. (b) Low-shear treatment of an aggregated dispersion in a dynamic shear rheometer by low-speed rotation of parallel plates. Curve (I): as-obtained aggregated dispersion. The huge irrecoverable drop in the viscosity during the ramp-up stage suggests a structural ordering. Curves (II) and (III): the repetitions of the same test on the same ink with 30 min rest in between. Curve (IV): the same ink after a three-roll-mill treatment. (c) Amplitude sweep test of vdW inks made of different 2D materials with different solid contents, confirming their gel structure. (d) Schematic illustration of the internal structure of (left) an aggregated dispersion and (right) the gel obtained after shear-treating the aggregated dispersion. (e) Binary X-ray tomogram (scale bar: 40 µm) and (f) SEM image (scale bar: 2 µm) of a freeze-dried graphene vdW ink. Image Credit: Abdolhosseinzadeh, S et al., Advanced Materials
Addressing Processing Challenges in Printing 2D Functional Materials
Traditionally, additives are used to address inherent processing challenges in fabricating materials. However, this causes problems. Additives significantly degrade the material’s electronic properties. High-temperature post-deposition treatments are used to remove the additives, but this complicates the fabrication process and limits available materials, removing the possibility of using heat-sensitive materials.
To address these challenges, it is necessary to fabricate additive-free inks that do not require post-treatment. Now, research has been presented that has developed a universal strategy for achieving this by exploiting the unique properties of 2D materials.
Synthesizing Functional 2D Materials
The family of 2D materials is vast, with hundreds discovered and many more predicted. They display a huge range of chemical and physical properties. 2D materials can be synthesized by either solution-based methods or gathered from layered crystals suspended in a liquid. Both synthesis methods create a suspension of 2D nanosheets which can then be further processed into printable inks.
The concentration of nanosheets within a suspension has an upper limit, beyond which they become unstable. High-concentration inks are necessary for the formation of percolated particle networks, however. Suspensions are also thermodynamically unstable, regardless of their concentration.
Particles reduce their surface energy via aggregation. Minimizing surface energy differences between solvent and material lowers this rate of sedimentation. Additionally, solvents may not be suitable for subsequent processing.
In conventional inks, additives such as binders and surfactants are used to address problems and fabricate functional inks. One commercial example is graphene: large concentrations of polymeric binders are necessary to process the material for screen printing.
Post-treatment helps but causes problems such as cracking and delamination. Similar problems exist with selective heating treatments including laser or microwave-based printing methods.
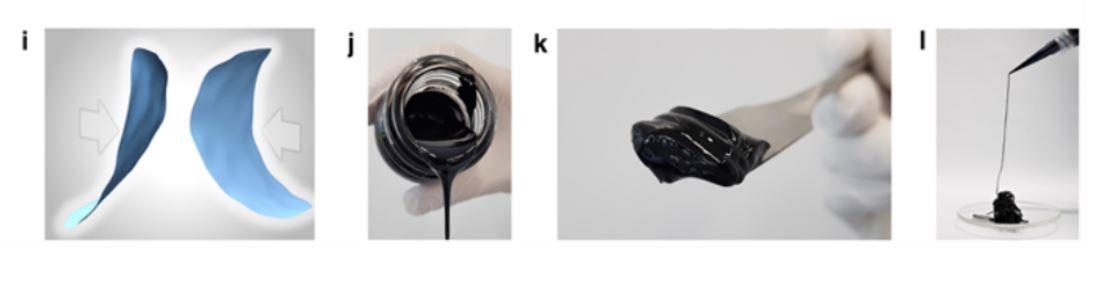
(i) Schematic illustration of two nanosheets moving towards each other to reaggregate. (j-l) Digital photographs of a terpineol-graphene vdW ink at three concentrations for (j) Flexographic printing (0.7 vol.%), (k) Screenprinting (2 vol.%), and (l) Extrusion printing (4 vol.%). Image Credit: Abdolhosseinzadeh, S et al., Advanced Materials
Moving Beyond Additive-based Inks
The team removed the need for additives and post-treatment. The additive-free process takes advantage of interparticle van der Waals interactions in the material, creating a class of inks termed vdW inks. By manipulating this property, it is possible to disperse solvents within the interconnected network of two-dimensional materials.
This improves the range of solvent selection, which is currently limited by dispersibility-related factors.
Furthermore, inter-flake vdW attractions control the flow behavior of the inks and the mechanical properties of the resultant films. The study discussed in large detail the structure of the inks, their film-formation behavior, and rheological properties.
Potential for large-scale production and formulation of the inks for commercially viable high-throughput methods and their room-temperature applications were also demonstrated.
How the Process Works
This process overcomes current challenges and can prevent undesirable outcomes in printing 2D materials. Able to facilitate room-temperature printing methods, these inks present a unique approach.
To create a space-filled gel, the nanosheets must be brought into close enough contact with each other to take advantage of the van der Waal interactions and aggregate. The particles are strongly bound to each other, and the film is bound to the substrate.
To create an ink with steady flow rate behavior that can be printed or coated on a substrate material, short gentle shearing is necessary by processes including three-roll-milling.
The flattening and aligning of the nanosheets is indicated by a substantial and irrecoverable drop in viscosity levels, resulting in the formation of a gel that can be synthesized at room temperature and printed without the need for any extra additives or post-treatment chemicals. Drying the ink after deposition creates a uniform and continuous film.
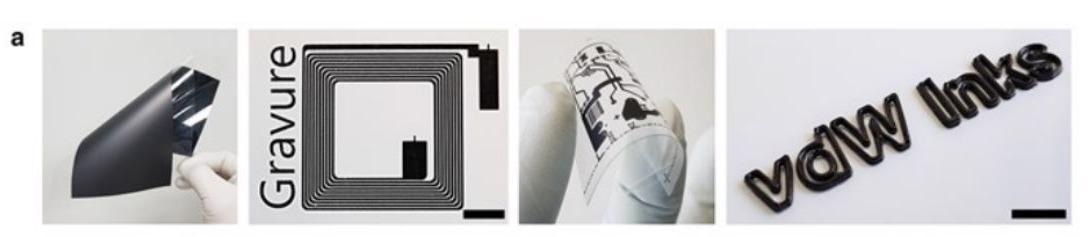
Applications of the vdW inks. (a) Left to right: 1. Slot-die coated propylene glycol-graphene vdW ink on a PET substrate (size of the substrate: DIN-A5). 2, 3. Gravure and flexographic printing of a 0.7 vol.% terpineol-IPA-graphene vdW ink (Terpineol:IPA 80:20) on glossy photo paper and PET substrates (respectively). 4. Extrusion printed 8 vol.% NMP-WSe2 vdW ink on a PET substrate (scale bar: 1 cm). Image Credit: Abdolhosseinzadeh, S et al., Advanced Materials
Challenges
The project addressed several challenges. For example, depending on the coating or printing method, films may experience issues such as increased surface roughness, variations in thickness, and discontinuity. In screen printing, the mesh of the cell walls can cause less or no ink to be deposited in certain places.
With long-enough recovery time, these issues lessen, but too long and the ink spreads uncontrollably and loses fidelity. The flow rate of vdW inks can be adjusted to fulfill the requirements of conventional printing methods. Other challenges were discussed and explored.
Potential of the Technology
The potential for vdW inks is huge. One commercially important potential demonstrated in the research was the room-temperature screen printing completely two-dimensional material-based field-effect transistors. Whilst challenges still exist, these inks may present a solution to common problems in the field of printable 2D functional materials.
Further Reading
Abdolhosseinzadeh, S et al. (2021) A Universal Approach for Room-Temperature Printing and Coating of Two-Dimensional Materials [online] Advanced Materials | onlinelibrary.wiley.com. Available at:
Disclaimer: The views expressed here are those of the author expressed in their private capacity and do not necessarily represent the views of AZoM.com Limited T/A AZoNetwork the owner and operator of this website. This disclaimer forms part of the Terms and conditions of use of this website.