As governments and international organizations face increasing pressure to enact more robust and stringent climate policy, the steel sector has in turn been required to implement lower-emission technology on a wide scale.
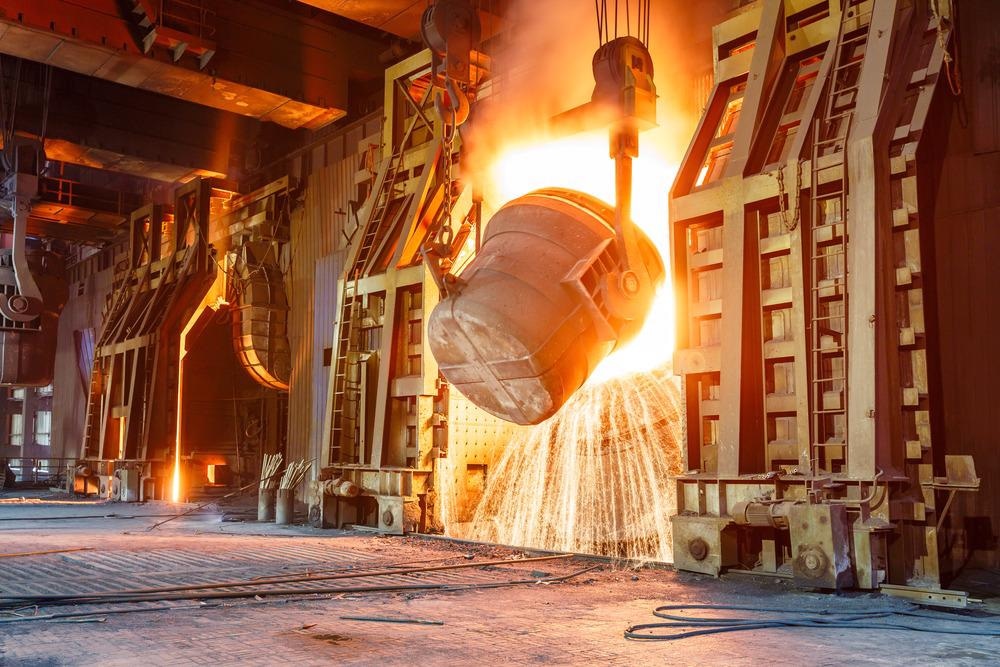
Study: Phasing out the blast furnace to meet global climate targets. Image Credit: ABCDstock/Shutterstock.com
Research recently presented in the journal Joule aimed to demonstrate that while replacing the largely coal-based global blast furnace fleet remains the most environmentally friendly and best long-term option, it may be possible to introduce comprehensive equipment-level analysis to help reduce the furnaces’ environmental impact in the short to medium term.
One of the most notable factors that are hindering this sector-wide decarbonization stems from the industry’s use of large-scale industrial assets which have extensive economic lifetimes and are not due for replacement for many years.
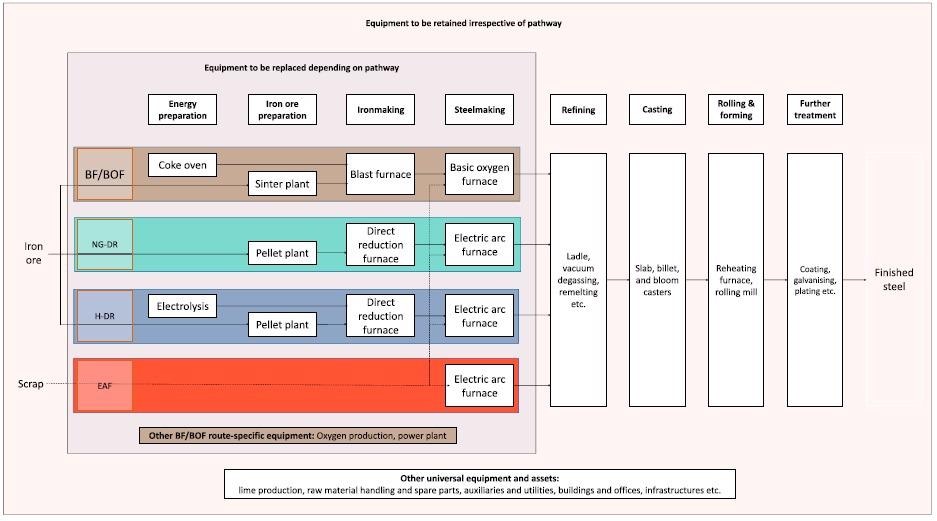
Schematic illustration of typical configurations of selected steel production pathways and the associated differences in necessary equipment. BF/BOF, blast furnace/basic oxygen furnace; NG-DR, natural gas direct reduction; H-DR, hydrogen direct reduction; EAF, electric arc furnace. Image Credit: Valentin Vogl et al., Joule
There is also political and socio-economic pressure to maintain local jobs and maintain value creation, factors which are discouraging policy makers from retiring polluting production methods and industries entirely.
The Paris Agreement introduced necessarily ambitious targets requiring anthropogenic greenhouse gas emissions (GHG) to peak at the earliest opportunity, reaching net-zero by 2050 and then to become negative.
Negative emissions technologies remain largely unproven, meaning that the steel sector has been required to keep its decarbonization progress in line with economy-wide targets.
Steel production accounted for 7% of global GHG emissions and 10% of total anthropogenic CO2 emissions in 2018. Despite its adverse impact on the climate, the demand for steel continues to rise, driven by emerging economies and consumer demand.
Primary steel production (including steel made from iron ore) generates significantly more emissions than secondary steel production, due to its dependency on metallurgical coal, so any effective decarbonization of the steel sector must centralize substantial changes in this process.
A number of solutions have been explored as a means of decarbonizing this process; for example, equipping blast furnaces with carbon capture and storage (CCS) technology and replacing coke and coal with biomass where possible, or replacing the blast furnace altogether and using the hydrogen direct reduction process in its place.
Despite these advances, steel has widely been regarded as one of the most challenging industries to decarbonize. As well as the longevity of many steelmaking assets and facilities, these challenges stem from a number of technical factors; for example, most steel industry emissions originate from the ironmaking process rather than basic fossil fuel combustion, whereby fossil coke is employed in the reduction of iron ore in the blast furnace.
Blast furnace technology is a mature production system with a thousand-year history, and fossil coke has unique desirable mechanical properties which make it difficult to replace with less emitting alternatives.
One common means of quantitatively analyzing the impact of long-serving capital on global warming is the committed emissions accounting method which looks at the cumulative GHG emissions of utilizing current fossil infrastructure until the end of its anticipated economic lifetime.
The researchers took it upon themselves to estimate emissions commitment from worldwide primary steel production equipment. To achieve this, they collated data on the historic operating patterns of steelmaking equipment and used this as part of a modified approach to committed emissions accounting for industrial assets.
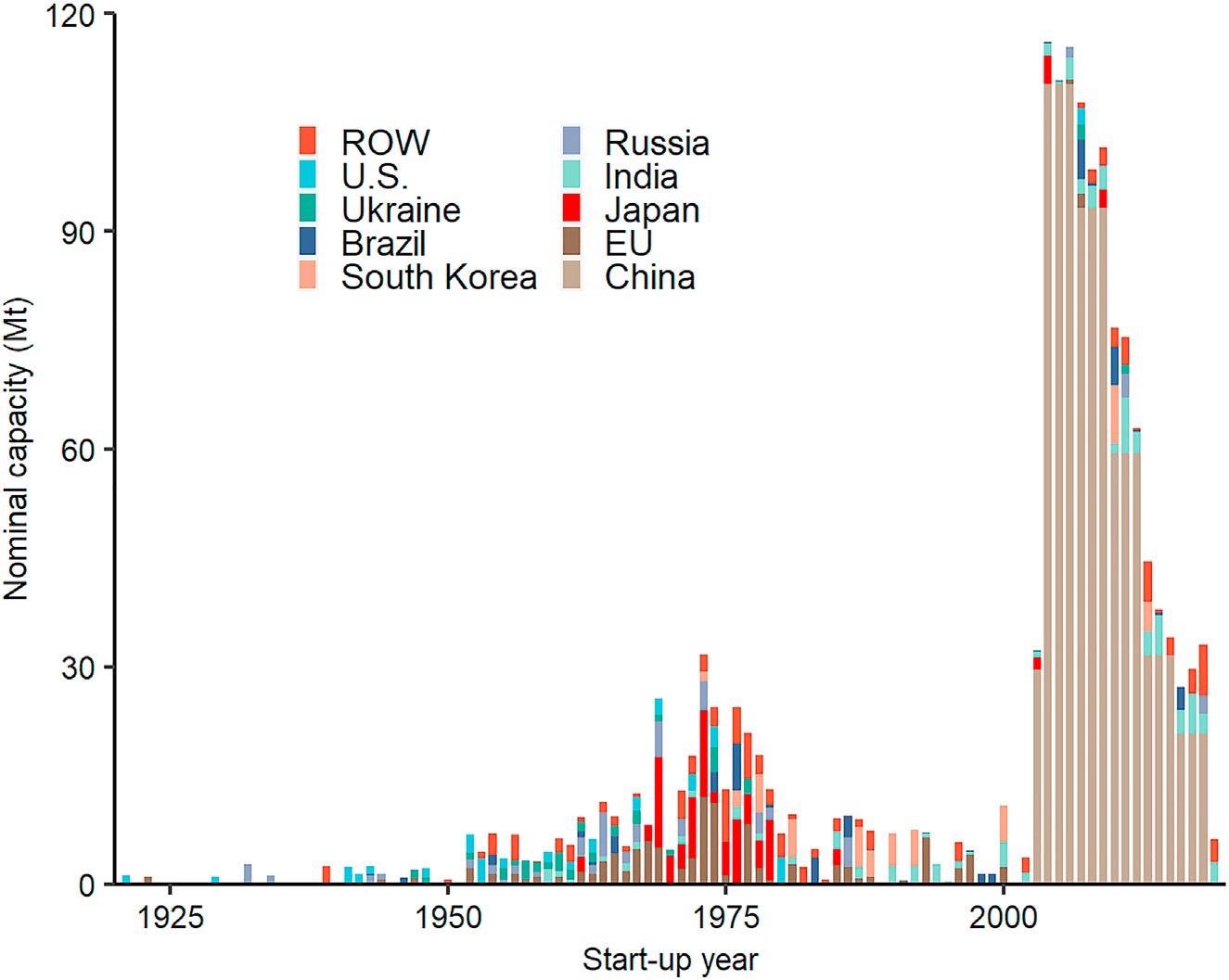
The age structure of currently (2019) operating global blast furnace equipment per country (ROW, rest of the world) Columns show the yearly capacity additions for furnaces that are still in operation. Two waves of capacity addition are apparent: a global expansion period in the 1970s and the great Chinese acceleration after 2000 (see also Tables S1 and S8). Data for China between 2004 and 2018 is presented as a three-year average due to data confidentiality. Image Credit: Valentin Vogl et al., Joule
One of the most notable and important findings of this process was that that the socio-economic inertia of steel assets would appear to be less of an obstacle to decarbonization than had been previously assumed, and that the investment in relining a blast furnace at the end of a campaign represents an ideal opportunity to phase out blast furnaces in favor of more sustainable technologies and processes.
These findings were based on the determination that the emissions commitment of currently utilized primary steel equipment is considerably smaller than had been previously estimated, meaning that it could theoretically be easier to negate these emissions than had been implied.
Despite these revised estimates, current steel production equipment could still consume large amounts of remaining global carbon budgets. It will be necessary to carefully monitor the ageing and use of emission-intensive assets and regulate their operation accordingly with a view to phasing these out as soon as possible.
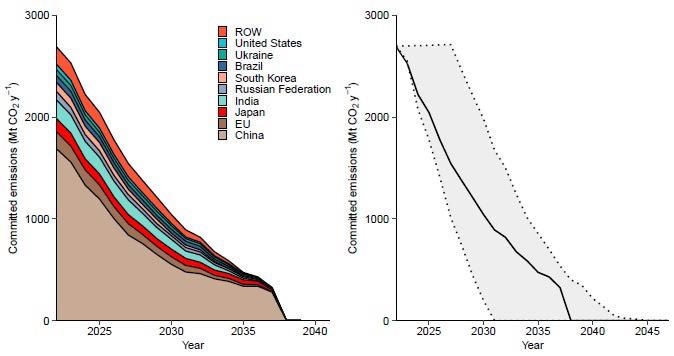
Committed emissions from existing global blast furnace equipment. (A) Committed emissions in main steel producing countries. Areas represent cumulative committed emissions. (B) Committed emissions based on median historic blast furnace campaign life (17 years, black line, 21 Gt CO2eq) and range of plus/minus one standard deviation (10–24 years, dotted lines, 13 and 32 Gt CO2eq, respectively; see also Tables S2–S4). Image Credit: Valentin Vogl et al., Joule
Policy remains the key tool in expediting and managing this phasing out of polluting assets such as blast furnaces. These policy approaches must be holistic and sector-wide, with any policy plan for blast furnace phase-out implemented as part of wider decarbonization of the steel industry that also prioritizes subsidies, market creation, material efficiency improvements, increased use of recycled steel, and a just transition for the industry’s employees and stakeholders.
A number of the key measures to addressing climate change are inherently steel-intensive; for example, renewable energy, railways, flood protection, and improved infrastructure. The researchers state that by integrating the right combination of strategies and policy, steel can support rather than hinder the move to a fossil-free society.
Disclaimer: The views expressed here are those of the author expressed in their private capacity and do not necessarily represent the views of AZoM.com Limited T/A AZoNetwork the owner and operator of this website. This disclaimer forms part of the Terms and conditions of use of this website.
Source:
Valentin Vogl, Olle Olsson, Björn Nykvist, Phasing out the blast furnace to meet global climate targets, Joule, Volume 5, Issue 10, 2021,Pages 2646-2662, ISSN 2542-4351, https://www.cell.com/joule/fulltext/S2542-4351(21)00435-9?_returnURL