Lithium-ion batteries (LiBs) are among the most widely used energy storage technologies available in the market. In a variety of fields, such as electronics products, machine tools, hospital equipment, and electric vehicles, their ability to offer high power and energy density in conjunction with a long life cycle, little memory effect, and acceptable cost provides an unrivaled advantage (EVs). LiBs usage in 3D printing is studied within the Applied Materials Today journal.
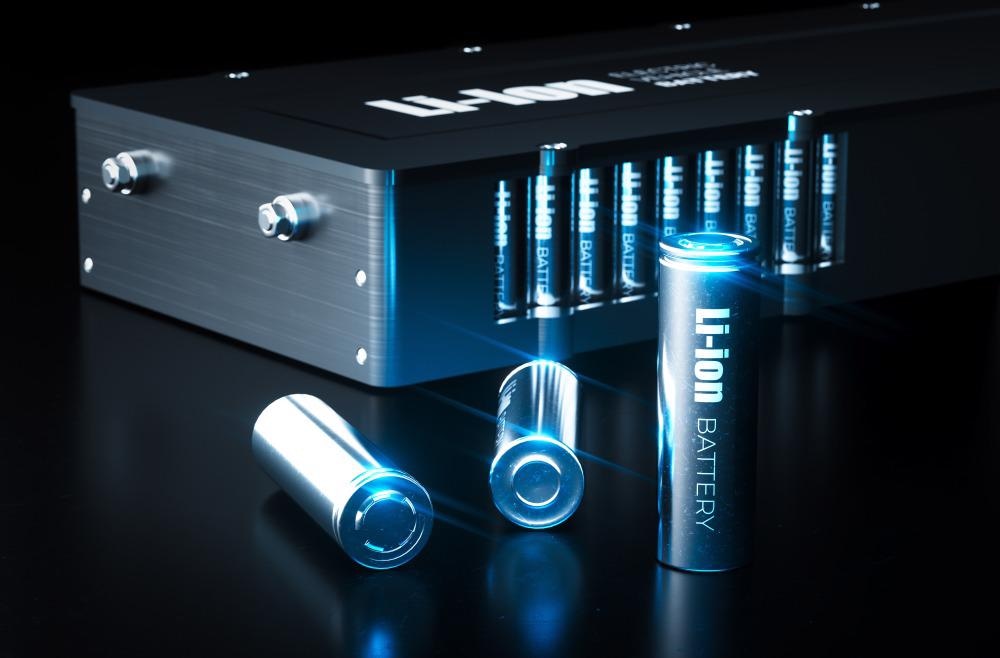
Image Credit: Development of full ceramic electrodes for lithium-ion batteries via desktop-fused filament fabrication and further sintering. Image Credit: petrmalinak/Shutterstock.com
Furthermore, the need for large-capacity battery systems, such as those used in electric automobiles, is now satisfied by cramming hundreds or thousands of ordinary cells into battery modules.
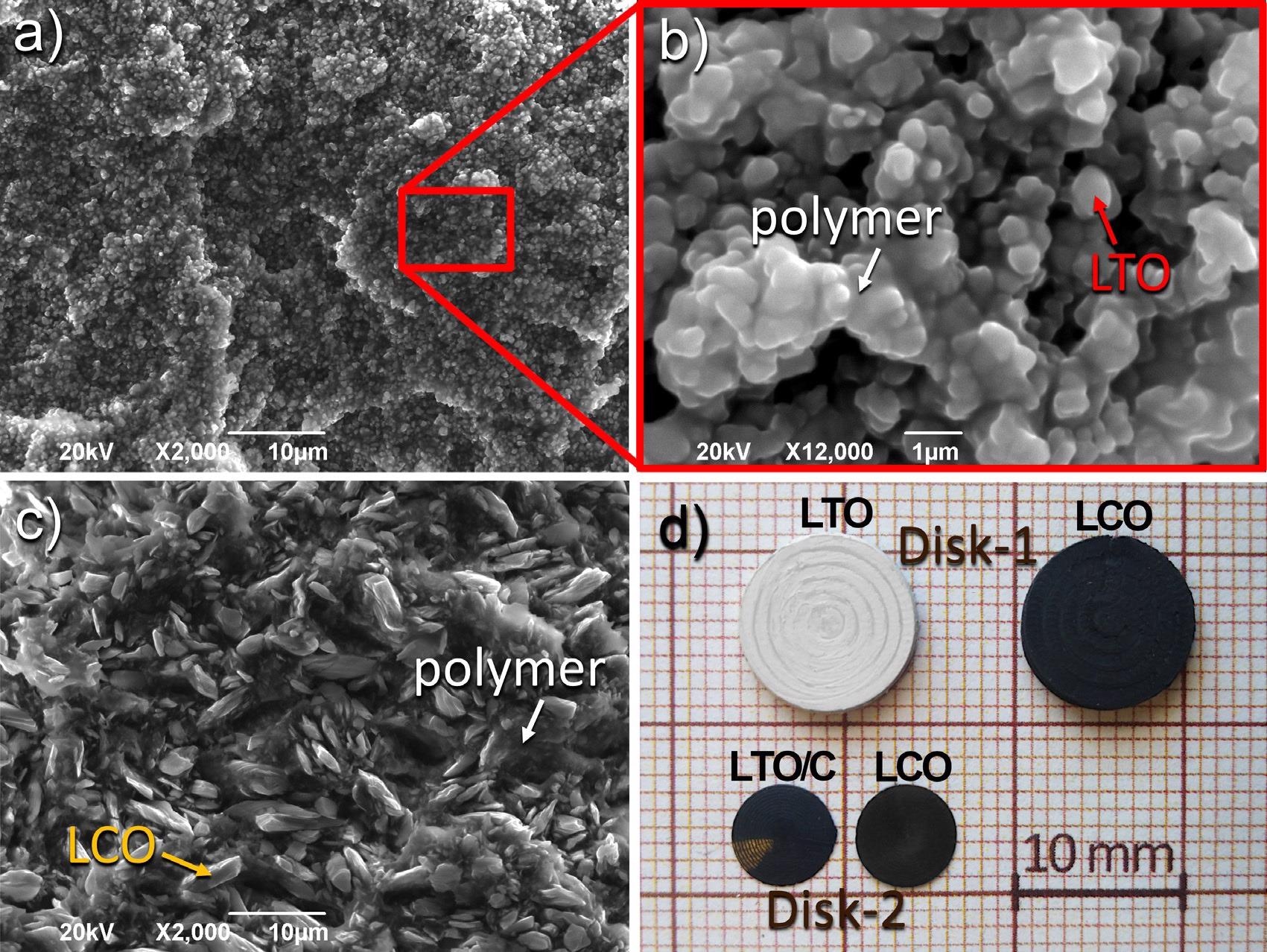
SEM images showing: (a, b) the distribution of the LTO particles in the polymeric matrix of the LTO filament; (c) the distribution of the LCO particles in the polymeric matrix of the LCO filament; (d) Disk-1 and Disk-2 green bodies of LTO and LCO-based materials. Image Credit: Valera, J., et al., Applied Materials Today Journal
The Problem of Lithium-Ion Batteries
Under these conditions, space utilization is problematic, and managing such battery storage implies challenges connected to precise control of cell energy and battery states.
To overcome these issues, two approaches might be considered: improving the electrochemical characteristics of the materials involved or, alternatively, optimizing the structure of both the batteries and the device. In terms of the latter, the use of multifunctional batteries, which have a structural purpose in addition to their electrical use, is an attempt to lower the overall system's volume and weight.
In fact, using batteries with certain shapes that fit specific positions within the hosting electronics might be a useful way to optimize the quantity of active material and so boost the entire system's energy density.
Furthermore, in the recent decade, a variety of solutions have been developed to improve both the power density and energy of devices by developing electrodes with larger surface areas, such as LiBs with interdigitated electrodes. However, the range of geometries accessible in most available commercial cell types is quite restricted, limiting the adaptability gained by altering battery storage.
Fused Filament Fabrication for Lithium-Ion Batteries
In comparison to conventional production processes including physician blading or die pressing, 3D printing of power devices and their elements offers indisputable advantages in this field, allowing for the development of electrodes with high surface area or the manufacturing of devices with geometries that fit product-specific designs and optimize the number of active materials within the processes.
Fused filament fabrication (FFF) is a viable and low-cost approach for fabricating lithium-ion batteries with customizable geometries among various technologies.
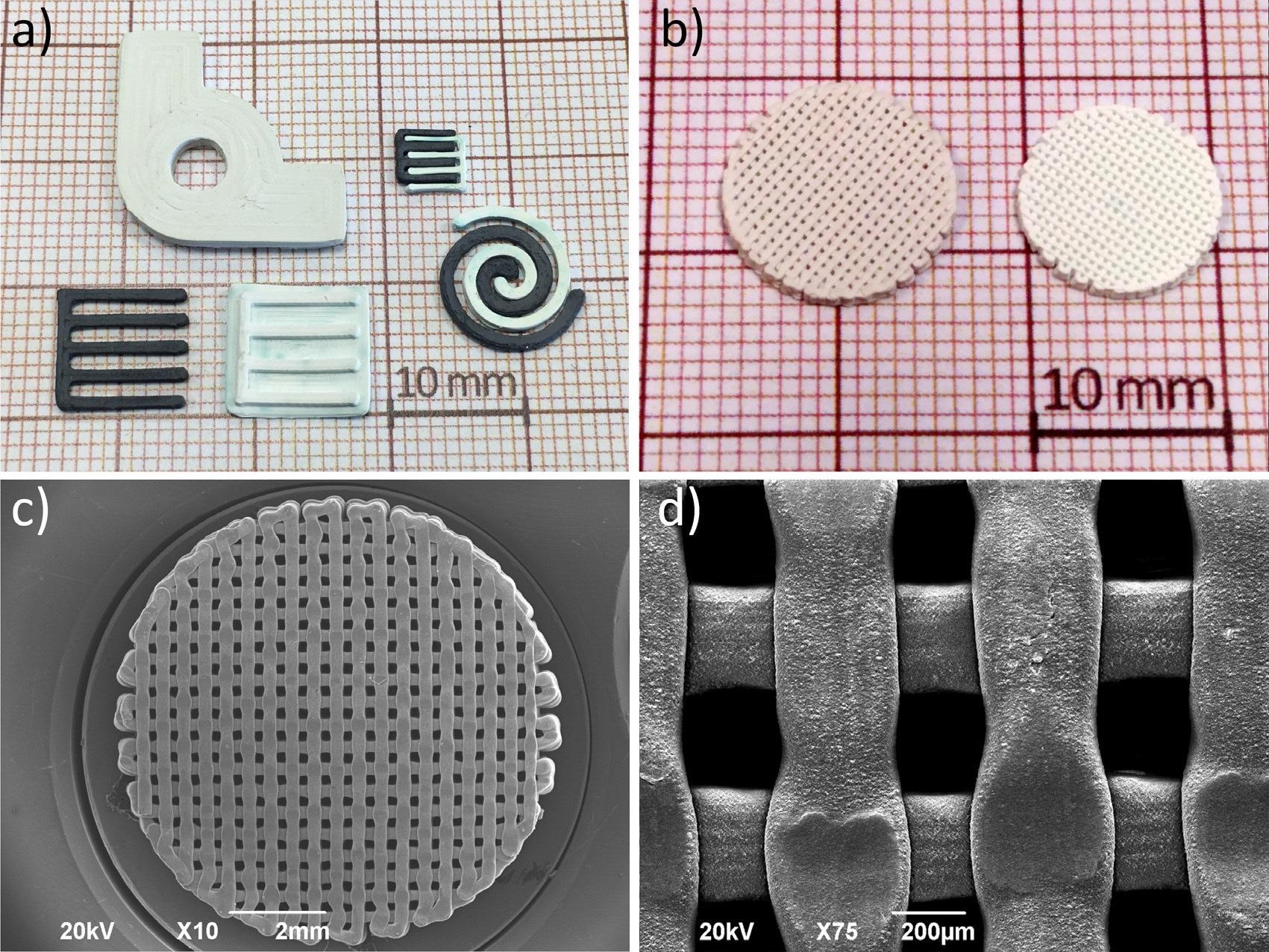
(a) Full ceramic LTO (white) and LCO (black) components manufactured via FFF and sintering; (b) LTO porous electrodes in green (left) and sintered (right) state; (c) SEM image showing LTO grid-shaped electrode; (d) SEM image showing the pore size of the grid-shaped electrodes. Image Credit: Valera, J., et al., Applied Materials Today Journal
The use of FF of ceramic to make piezoelectric and thermal materials, photonic bandgap frameworks, catalytical structural components, and bioceramic scaffolds has been suggested, indicating the technology's promise for advanced technologies.
Similarly, whole ceramic electrodes offer better energy density than standard composite electrodes that need the use of organic binders; therefore, FFF of ceramics implemented to the area of electrodes might be a worthwhile technique.
The report details the manufacturing of full ceramic LTO anode and LCO electrodes using FFF 3D printing of composite filaments and subsequent sintering, as well as a detailed examination of the printed electrodes' microstructure and macrostructure analysis, electrical conductivity, phase stability, and electrochemical properties.
With this method, 3D printed LTO and LCO electrodes with identical electrical conductivity to uniaxially pressed ceramic pellets were created, displaying 168 and 129 mAh g-1, respectively, 96 percent and 94 percent of their theoretical capacities.
Fused filament fabrication (FFF), on either hand, is the most widely used AM innovation both at the individual/domestic and industrial level, due to a combination of ease of use, large-scale fabrication abilities, a broad variety of commercial materials available, and low costs of both components and 3D printing devices.
While some other common methods, such as DIW or vat polymerization processes, may result in better resolutions, the storage and management of the inks and resins needed as raw ingredients are more difficult. Degradation and stabilization concerns may arise, particularly in the case of slurries, since the solid load wants to agglomerate/precipitate, implying, in the optimistic outcome, intermediate reconstitution procedures.
Method of FFF Application
FFF, on the other hand, employs solid thermoplastic-based filament that may be held under vacuum until needed. Furthermore, unlike DIW or vat polymerization methods, including solid fillers/pore precursors on these filaments is extremely straightforward and does not create any substantial modifications in the 3D printing process. FFF techniques are also among the most sophisticated systems in the field of multi-material printers, which is a crucial link in the innovative notion of "print-it-all" production strategies.
![HRTEM images and the corresponding electron diffraction patterns showing the [110] zone axis of 3D printed LTO sintered at 900 °C for 6 h in (a) N2 and (b) air.](https://d12oja0ew7x0i8.cloudfront.net/images/news/ImageForNews_57374_16372312733734679.jpg)
HRTEM images and the corresponding electron diffraction patterns showing the zone axis of 3D printed LTO sintered at 900 °C for 6 h in (a) N2 and (b) air. Image Credit: Valera, J., et al., Applied Materials Today Journal
Nonetheless, commercial FFF feedstock filament for electrochemical devices are limited, despite the recent introduction of graphene/PLA composite filament, among many others, in the commerce, with a series of studies employing them to make graphene-based LiB anodes.
DIW, or direct ink writing, has significant problems in 3D printing, like the usage of inks as raw resources, which have long-term storage concerns and are more difficult to manage than filaments used in FFF. This study advances the creation of FFF 3D printable LiBs with micro-features commonly associated with DIW throughout this context.
Reference
Valera, J., et al. (2021). Development of full ceramic electrodes for lithium-ion batteries via desktop-fused filament fabrication and further sintering. Applied Materials Today Journal. https://www.sciencedirect.com/science/article/pii/S2352940721003061?via%3Dihub
Disclaimer: The views expressed here are those of the author expressed in their private capacity and do not necessarily represent the views of AZoM.com Limited T/A AZoNetwork the owner and operator of this website. This disclaimer forms part of the Terms and conditions of use of this website.