Tungsten is one of the materials with the most potential for fusion reactor plasma-facing materials (PFC). The thermomechanical response of materials in fusion devices to PFC is discussed in the Materials and Design Journal.
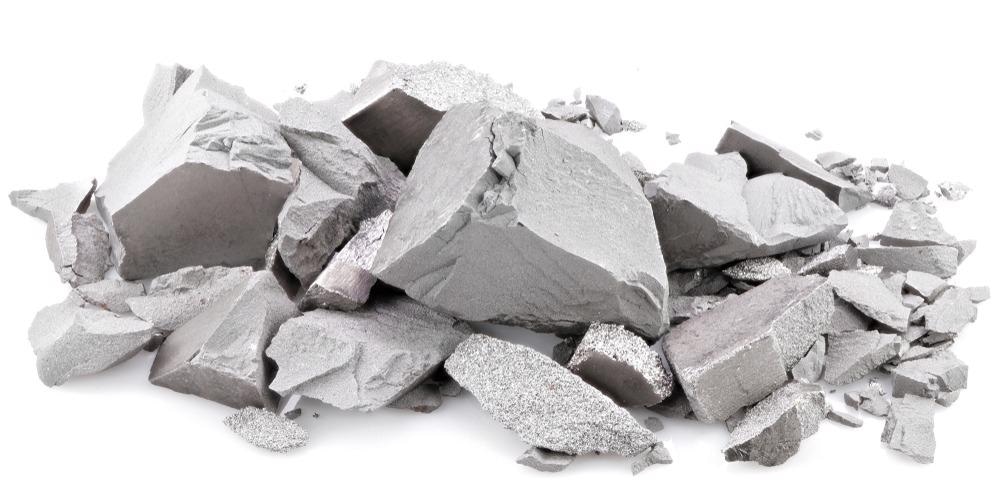
Study: Joining and cycling performance of ultra-thick tungsten coatings on patterned steel substrates for fusion armour applications. Image Credit: Bjoern Wylezich/Shutterstock.com
Tungsten as A Promising Material
Neutron irradiation responses of tungsten and tungsten alloys by nuclear fission reactors were good. The connection between displacement damage and transmutation components under neutron irradiation is presented based on these investigations. Plasma surface contact is demonstrated using He ion irradiation and tungsten.

(a) Schematic of the field-assisted sintering technique (FAST). Sketch of (b) the patterned surface of the steel substrate, (c) the cross-section along the A-A line highlighted in (b), and (d) a magnified view of the region B circled in (c). Dimensions in mm. Image Credit: Cui, W., et al, Materials and Design Journal
Due to its strong heat conductivity, very higher melting and boiling point and low vapor pressure, minimal physical erosion rate, and low tritium retention, tungsten is a promising material for plasma-facing applications in fusion reactors. Tungsten coatings might potentially be used to safeguard components that are exposed to the most extreme temperature and other reactor characteristics present at the diverter.
The use of ultra-thick millimeter-scale tungsten coating as expendable armor against plasma hits in the diverter and elsewhere is usually thought to be necessary to safeguard the underlying structural components.
Tungsten Unfavorable Traits
However, tungsten's appealing features are regrettably accompanied by unfavorable traits such as high fabrication temperatures, low machinability, and oxidation susceptibility, all of which affect manufacturing. Because tungsten has a substantially lower coefficient of thermal expansion than ferritic/martensitic steels like EUROFER97 or copper, attaching tungsten to underlying structural elements, such as ferritic/martensitic steels like EUROFER97 or copper, is a considerable issue.
Temperature excursions encountered during manufacturing and service necessarily result in the generation of large thermal expansion mismatch stresses at the tungsten/steel contact in this combination.
These strains, as well as the latent strain energy associated with them, can cause tungsten coatings debonding and the emergence of catastrophic fractures adjacent to the interface plane, resulting in coating delamination. As a result, although only a few hundred microns thick, typical tungsten coatings on iron have inadequate thermal cycling ability.
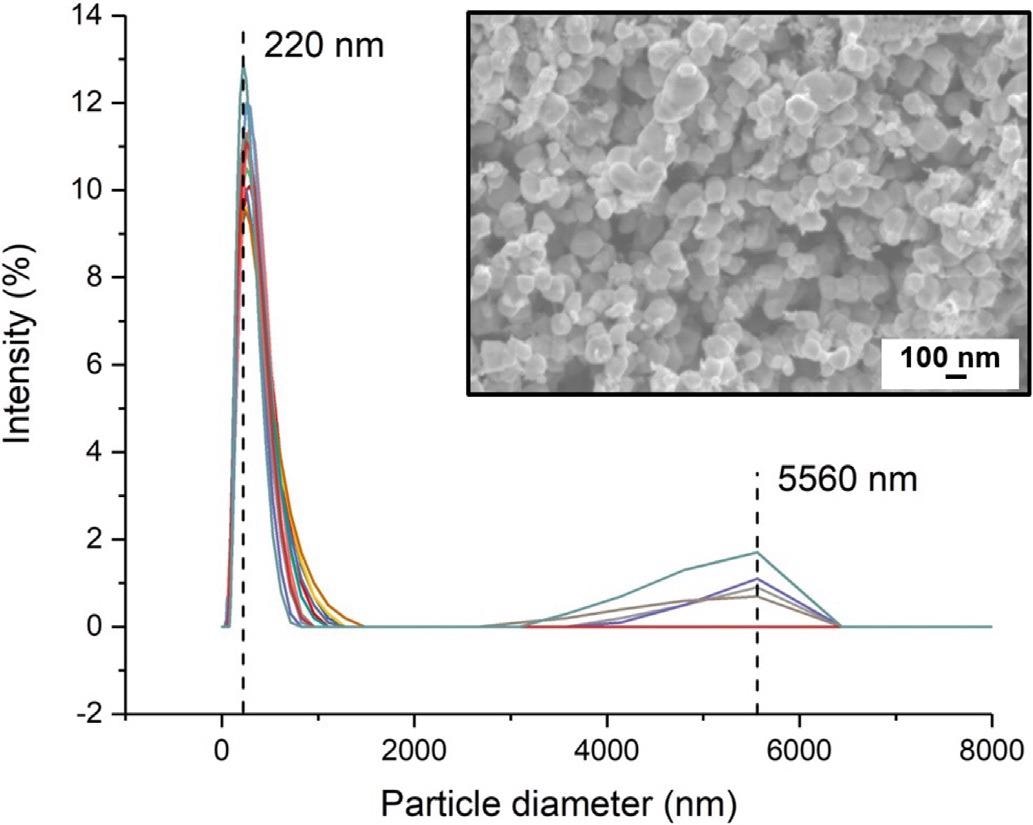
Repeat measurements of the particle size distribution and (inset) a SE micrograph showing the morphology of the as-received tungsten powders. Image Credit: Cui, W., et al, Materials and Design Journal
Tungsten Coating Methods
Because of the large difference in melting points, tungsten/steel joining is frequently done independently from tungsten manufacture. Alternatively, a tungsten outer coating can be deposited directly onto iron or other material via a deposition method.
The deposition of thin inter-leaved layers of tungsten and steel to produce a graded interface has been researched using techniques for thermal transfer mismatch strain control, such as air or vacuum plasma spraying (APS, VPS) of tungsten in the liquid form or droplets. The goal of the graded interface technique is to spread thermally induced stresses over a larger area of material and lower the potential for failure for delamination of a discrete interface.
The field-aided sintering process was used to create button-like tungsten on steel samples in cylindrical high-density graphite die (FAST). A cold-pressed powder compact is heated in FAST by putting an electric current between the die and powder material, causing fast Joule heating. To facilitate sintering, a uniaxial pressure of up to 50 MPa is often applied at the same time.
To avoid heat loss throughout FAST, the die was each covered in carbon felt. To prevent direct contact between the die/punch set and the sintered materials, a top and bottom layer of graphite foil were utilized inside the die. At the base of the die, a steel disc substrate was placed.

(a) SE micrograph showing a dark grey interlayer at the tungsten/steel interface, and (b-f) EDS spectra showing the distribution of Fe, W, Cr, O and Mn. Image Credit: Cui, W., et al, Materials and Design Journal
The tungsten nanopowder was placed into the die and pressed to encourage a uniform dispersion and infiltration across and through the pre-sculptured metal surfaces after any EDM-induced surface oxide layer was removed by glass bead blasting and cleaning. Coatings of various thicknesses were created using tungsten weights at 4, 6, and 8 g.
Result of Experiment
The substrate is substantially thicker than the coating, resulting in no appreciable substrate deflection, and a significantly larger thermal expansion mismatch caused larger strain energy per unit volume in the coating than in the substrate.
The strain energy per unit volume of the coating and the substrate become more similar as the coating becomes thicker and reaches the thickness of the substrate, based on the differences in their Young's modulus; in the extreme, the coating is so thick that it effectively functions as the substrate.
To limit the otherwise disastrous effect of thermal expansion mismatch stresses on coatings delamination, the field aided sintering approach was examined to produce thick, dense tungsten coating immediately onto pre-patterned AISI 416 steel substrates.
The method was effective in producing tungsten coatings with intentionally generated segmentation fissures and equiaxed, randomly distributed grains of 200 nm. In the as-fabricated state and following heat cycling between 300 and 800 in a specialized furnace designed to imitate the temperature conditions essential to fusion plasma-facing applications, the coated segments remained firmly adhered to the substrate.
References
Cui, W., et al. (2021). Joining and cycling performance of ultra-thick tungsten coatings on patterned steel substrates for fusion armour applications. Materials and Design Journal. https://doi.org/10.1016/j.matdes.2021.110250
Disclaimer: The views expressed here are those of the author expressed in their private capacity and do not necessarily represent the views of AZoM.com Limited T/A AZoNetwork the owner and operator of this website. This disclaimer forms part of the Terms and conditions of use of this website.