The latest research in the Journal of Materials Research and Technology is focused on the evaluation of microstructural properties and toughness of industrial electric resistance welding (ERW) equipment.
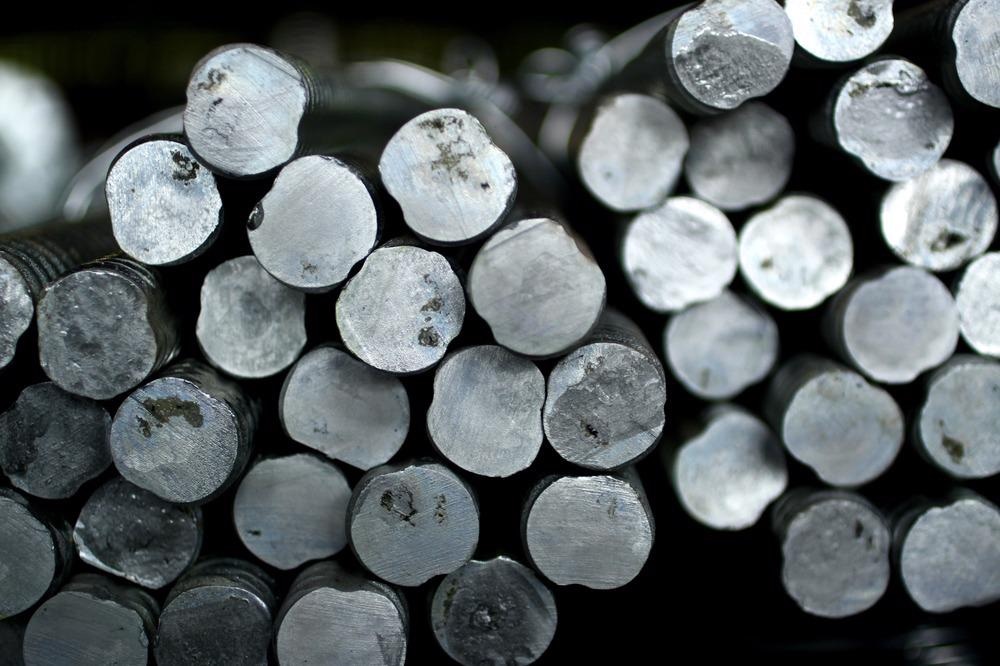
Study: A Significant Toughness Enhancement, And Microstructural Evolution Of An Electric Resistance Welded (ERW) Microalloyed Steel. Image Credit: SARIN KUNTHONG/Shutterstock.com
The research has successfully demonstrated that the implementation of an enhancement treatment would be beneficial for significant improvement in mechanical properties, particularly the toughness of steel.
Industrial Utilization of Steel Alloys
High-strength steel alloys usually contain elements such as Molybdenum, Titanium, etc., and are readily used in the oil and gas industry particularly in the transportation engineering department. Apart from this, the automotive industry, manufacturing industry, industries related to cranes, coasters, and rollers, etc. along with other structures that are specifically designed to operate under the high value of stresses requiring superior mechanical properties utilize them readily.
Inferior material qualities, inappropriate design, faulty engineering or fabrication procedures, unequal or excessive loads, and pre-existing defects can contribute to catastrophic failures. Understanding the strength and toughness properties of a certain material is frequently the best way to overcome these issues.
Difference between Toughness, Strength, and Hardness
Toughness is the ability of the material to absorb energy before undergoing fracture. In other words, it could be the material’s ability to withstand the shock up to fracture. Toughness is different from hardness and strength.
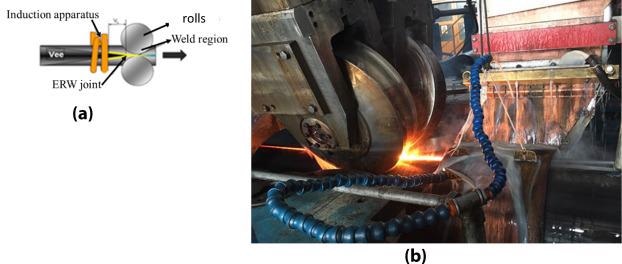
a) pipeline jointing by ERW process. b) a snapshot of ERW process used for the welding of X52 plate. Image Credit: Anijdan, S. M et al., Journal of Materials Research and Technology
Hardness could easily be termed as the material’s ability to withstand friction or prevent scratching. Strength could be termed as the force required to deform the material and toughness as mentioned above is its ability to resist any sort of fracture.
Importance of Microstructural Engineering in Steel
Microstructural engineering is achieved to reach adequate standards of mechanical characteristics by maintaining the balance of displacement and temperature during the annealing process, also known as thermomechanical control processing. Stopping recrystallization by generating titanium carbonitrides is the single most important phenomenon to achieve this procedure.
Importance of Electric Resistance Welding (ERW)
In the industrial sector, the electric resistance welding (ERW) technique is used to manufacture large-scale pipes since it has a reasonably high efficiency while maintaining an acceptable total production cost. Cold forming is used in this procedure to bend different plate thicknesses before the application of ERW equipment and without the use of welding materials. Brittle phases are formed as a result of the quick cooling used in the ERW process.
Enhancing toughness values has a significant design impact since ERW pipe with appropriate toughness qualities might be utilized for seamless purposes.
Research Findings
The latest study showed that the rapid cooling rate following the ERW operation resulted in a greater number of these second phases, albeit with smaller sizes and a more scattered arrangement. Typically, the comparatively greater hardness aspects of steel were obtained during the quick cooling phase following the welding operation.
Scanning Electron Microscopy revealed a finer microstructural characteristic, which might suggest improved mechanical qualities, notably toughness. There was a difference observed in the hardness value of the base metal and welded zone.
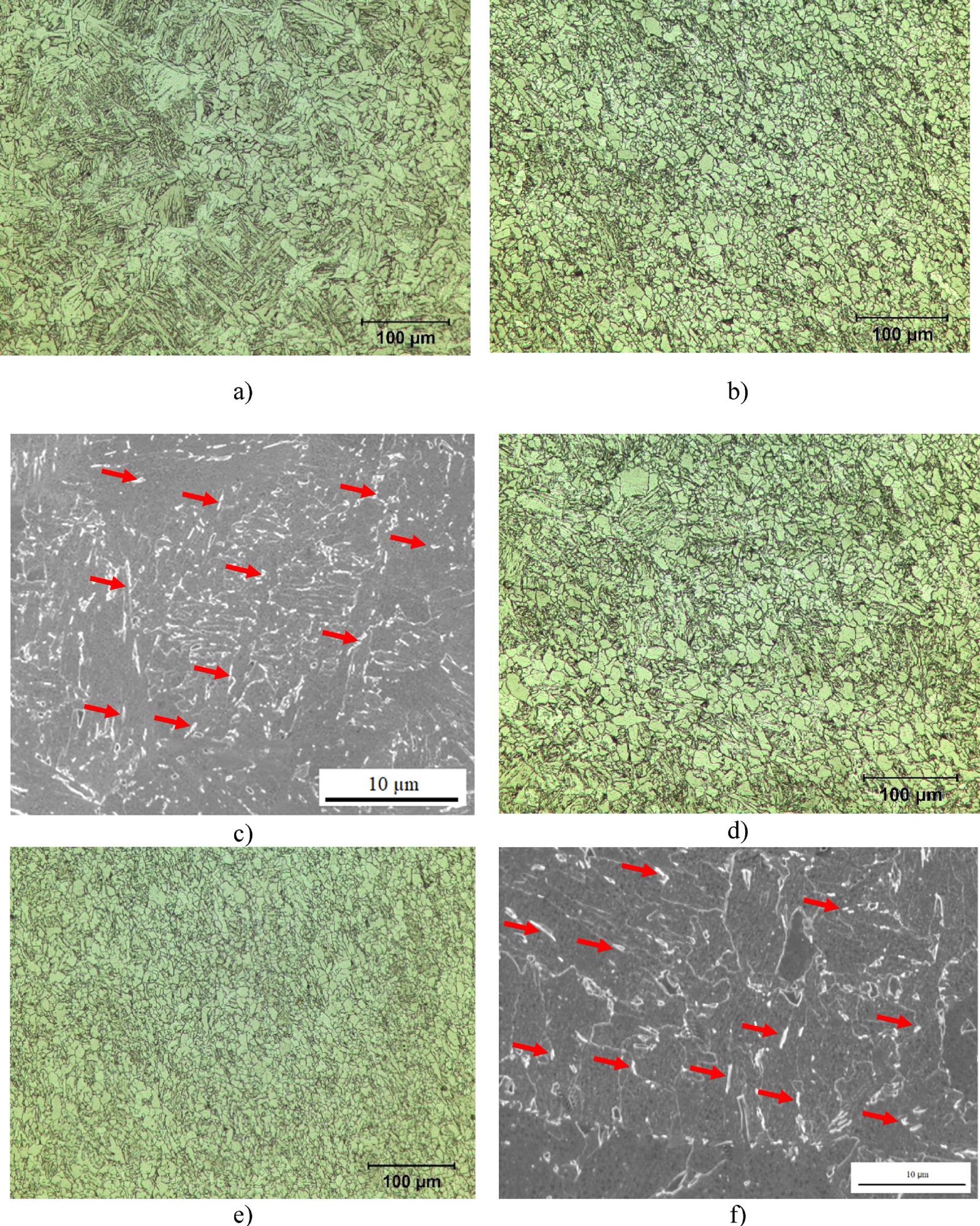
OM images of X52 steel, a) OM of weld zone of normalization stage, b) HAZ area of normalization, c) SEM image of the WZ of the normalization stage, d) OM of the weld zone of second stage treatment, d) HAZ area of second stage, f) SEM image of the WZ of the second stage (arrows show M/A constituents). Image Credit: Anijdan, S. M et al., Journal of Materials Research and Technology
Along with this, a difference observed in the grain size resulted in a major difference in mechanical properties. The results were an indication that an even higher cooling rate would result in the formation of harder phases resulting in an improvement of mechanical properties.
Heat Treatment and Mechanical Properties
A significant point raised is that there is also variance in the values within each thermal treatment process, which might be attributed to variations in the microstructural characteristics caused by each heat treatment method (i.e. size and configuration).
The variation in heat treatment temperatures and the cooling rate used alters the precipitates' properties, particle size distribution, and phase features. These modifications may result in increased toughness during the second step of heat treatment. The results showed that impurities did not affect the fracture toughness of steel.
Limitations of Resistance Welding
Resistance welding is advantageous, yet its equipment is costly and it has its limitations for high conductive materials. The requirement of high electric power is also a major problem.
Limitations of Microalloyed Steel
Microalloyed steel is implemented for various purposes in different industries, yet a few disadvantages still exist. The drawbacks are that the ductility and hardness are not as good as in quenched and tempered (Q&T) steels. They must also be heated to a temperature high enough to dissolve all of the alloys; after forming, the material must be swiftly cooled to 540 to 600 °C.
In short, the research has thoroughly assessed the microstructure and toughness of ERW micro-alloyed steel; these steel alloys are used readily in various industries such as the aerospace, metallurgical, and oil and gas transportation industries.
References
Anijdan, S. M., Khafri, M. A., Khoshakhlagh, A. R., Eivani, A. R., Park, N., & Jafarian, H. R. (2021). A Significant Toughness Enhancement, And Microstructural Evolution Of An Electric Resistance Welded (ERW) Microalloyed Steel. Journal of Materials Research and Technology. https://www.sciencedirect.com/science/article/pii/S2238785421012928
Disclaimer: The views expressed here are those of the author expressed in their private capacity and do not necessarily represent the views of AZoM.com Limited T/A AZoNetwork the owner and operator of this website. This disclaimer forms part of the Terms and conditions of use of this website.