Researchers from Switzerland and China recently developed a process to reuse the extracted carbon dioxide back into a biogas upgrader using an ionic polymer catalysis method and thus obtained epoxides as a by-product. This research has been published in the journal Industrial & Engineering Chemistry Research.
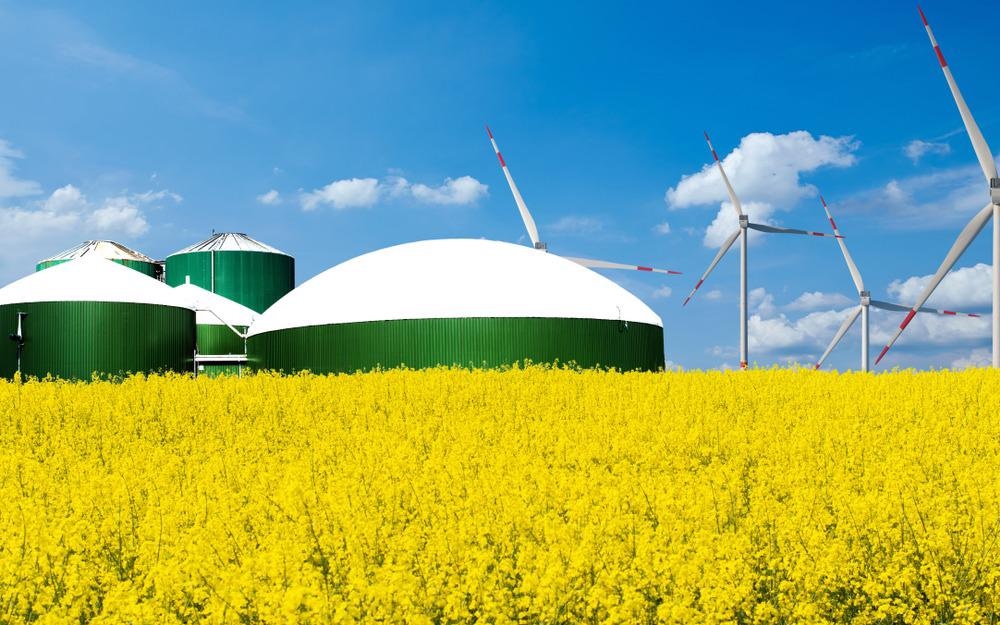
Study: Cycloaddition of Biogas-Contained CO2 into Epoxides via Ionic Polymer Catalysis: An Experimental and Process Simulation Study. Image Credit: Natascha Kaukorat/Shutterstock.com
What is a Biogas Upgrader?
A biogas upgrader is a facility used to obtain high purity methane (CH4) from biogas after removal of unwanted carbon dioxide (CO2), hydrogen sulfide (HS), siloxanes, water (H2O), and other contaminations. The obtained methane from biogas is called biomethane.
Cycloaddition of Carbon Dioxide into Biogas Upgrader
Typically, biogas contains methane (50-75 vol %), carbon dioxide (25-50 vol %), and other minor components. Pure methane is used in many industrial applications as fuel, which makes biogas an eco-friendly alternative to fossil fuels.
However, the presence of a substantial amount of CO2, water, and corroding HS makes biogas unsuitable for direct use in the industry. In industry, biogas is periodically cooled to condense the water, and sulfur compounds are neutralized by passing the gas through activated charcoal.
Traditionally, CO2 is removed from biogas by amine scrubbing, water scrubbing, pressure swing adsorption (PSA), and membrane transfer. However, all these methods simply release the extracted CO2 into the atmosphere.
Through cycloaddition, the extracted CO2 is reutilized to achieve an energy-efficient and cost-effective biogas upgrading method that simultaneously converts the CO2 into a value-added product.
Currently, the pilot in situ methanation plants are incorporating hydrogen (H2) to reduce CO2 in sorbents such as ash at the bottom; this is called direct air capture (DAC). However, the high cost of industrial-scale H2 production using a water electrolyzer can be eliminated by reacting CO2 with suitable base or epoxide compounds. The by-products of CO2 and epoxides are organic cyclic carbonates (PC) which are of industrial importance.
What Does the Research Say?
The researchers used propylene oxide (PO) for epoxide, polymeric ionic liquid (IL) as a catalyst, and pressurized the CH4-CO2 gas mixture at different proportions. The gas mixture was passed through the PO-IL mixture, and the purity of yield PC was analyzed.
The activity of the IL polymer catalyst improved significantly as the reaction temperature was increased, which reduced the time required to achieve reaction equilibrium. However, the equilibrium yield of PC decreased with an increase in temperature due to the exothermic reaction. The reaction rate was found to be dependent upon both Henry’s constant and the concentration of CO2.
The team simulated three cases with different CO2 concentrations and respective PO conversions and found that the product purity enhanced with an increase in CO2 concentration in the feed gas mixture and resulted in a high flow rate of PC in the product outlet.
Prediction of the Biochemical Methane Potential for More Efficient Biogas Production
The researchers made a comparison of PC purity achieved using Peng−Robinson and other methods. They observed a small difference in PC purity and product temperature when the flash tank was set to work at 35 °C and 1 atm. The same order of PC purity was followed in case studies - case 1 < case 2 < case 3. This validates the optimization of the newly developed process.
Moreover, the process significantly intensified after incorporating scrubbing-flashing of biogas before the reaction rather than directly using the crude biogas as feed. Overall, the team achieved a PC yield of 88.9% in the reactor and 93.9% in the product outlet.
The researchers concluded that the design process of an industrial scale cycle adding carbon dioxide biogas upgrader requires matching the kinetic behavior of the reaction with the production of biogas and the prior integration of biogas scrubbing to achieve high PC yield with fast kinetics.
Economic Evaluation
The researchers also performed an economic evaluation for the new process for the valorization of CO2 contained in biogas. They carried out general sensitivity analysis and identified two critical parameters: 1) the unit size and 2) the price difference between the product and feed.
Their evaluation model indicated that the process can be profitable depending on the size of the plant. Even when the price of PC is lower than that of PO, the overall process can still be lucrative due to the higher molecular weight of PC compared to PO in terms of price per ton. Based on the results of this modeling, the biogas upgrading plant can produce over 80 000 tons PC per year (330 working days).
Reference:
X. Hu, F. Bobbink, A. Muyden, M. Amiri, A. Bonnin, F. Marechal, M. Nazeeruddin, Z. Qi, and P. Dyson, Cycloaddition of Biogas-Contained CO2 into Epoxides via Ionic Polymer Catalysis: An Experimental and Process Simulation Study, Ind. Eng. Chem. Res., 2021. https://pubs.acs.org/doi/10.1021/acs.iecr.1c03895
Disclaimer: The views expressed here are those of the author expressed in their private capacity and do not necessarily represent the views of AZoM.com Limited T/A AZoNetwork the owner and operator of this website. This disclaimer forms part of the Terms and conditions of use of this website.