Researchers from RMIT University, Melbourne, Australia, have developed a sustainable 3D concrete printing process for building structures by replacing 50% of natural river sand with different grades of recycled glass. This study is available in the journal Construction and Building Materials.
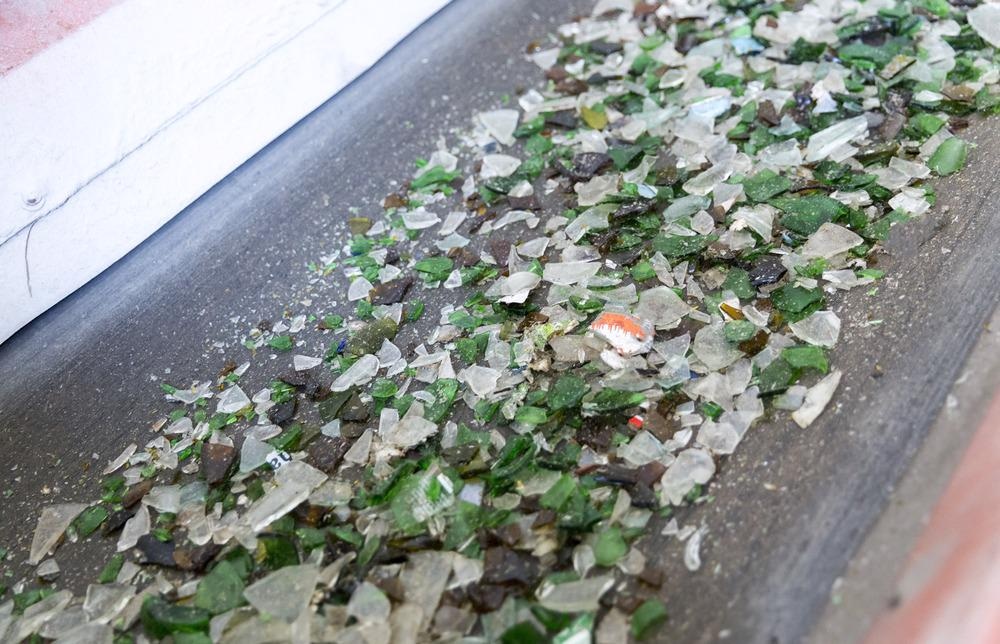
Study: 3D-printed concrete with recycled glass: Effect of glass gradation on flexural strength and microstructure. Image Credit: Belish/Shutterstock.com
The researchers analyzed the impact of the orientation of beam-shaped specimen with respect to the printing direction, the correlation between microstructures and mechanical properties, and the effect of glass particles on flexural strength and crack propagation.
With the advent of rapid prototyping technology, the traditional construction industry has leaped into a different dimension of ultrahigh-speed construction, intrinsic designing, and cost-effectiveness. 3D concrete printing (3DCP) technology enables the fabrication of concrete structures through an extrusion-based layer-to-layer deposition. However, it still inherits the drawbacks of traditional molding-based construction, especially the ones that are not environmentally friendly.
Portland cement and natural river sand are key components of traditional construction techniques. However, they also cause carbon dioxide emissions and exploitation of limited natural resources.
What is a More Sustainable Approach for 3DCP?
The answer to this is replacing natural river sand with recycled glass. There are hundreds of metric tonnes of waste glass generated worldwide. Also, the amount of recycled glass is significant in developed countries. Recycling these waste glasses leads to fewer landfills and more energy savings. Additionally, glass’s chemical compositions and physical properties resemble those of the raw materials in concrete, such as river sand and cement.
About the Study
The researchers investigated the relationship between the gradation of recycled glass and the performance of 3D-printed concrete structures from the perspectives of microstructures and flexural properties. They prepared five mixture samples with varying matrix to filaments ratios.
Also, graded the recycled glass into two different categories viz. coarse and fine. Then blended them at various mixing ratios with keeping the overall sand-to-glass ratio constant. The median grain sizes of coarse glass, fine glass, and river sand are 796 μm, 367 μm, and 204 μm, respectively.
Mechanical properties are investigated based on the three-point bending test. X-ray micro-computed tomography (μCT) is used for the microstructural evaluations, to analyze the pore size and spatial distribution within the prepared specimens and the fracture surface and crack propagation path in post-test specimens. Scanning electron microscopy (SEM) is used to probe into the microstructures of interlayer bonding regions and the interface between glass and cement matrices.
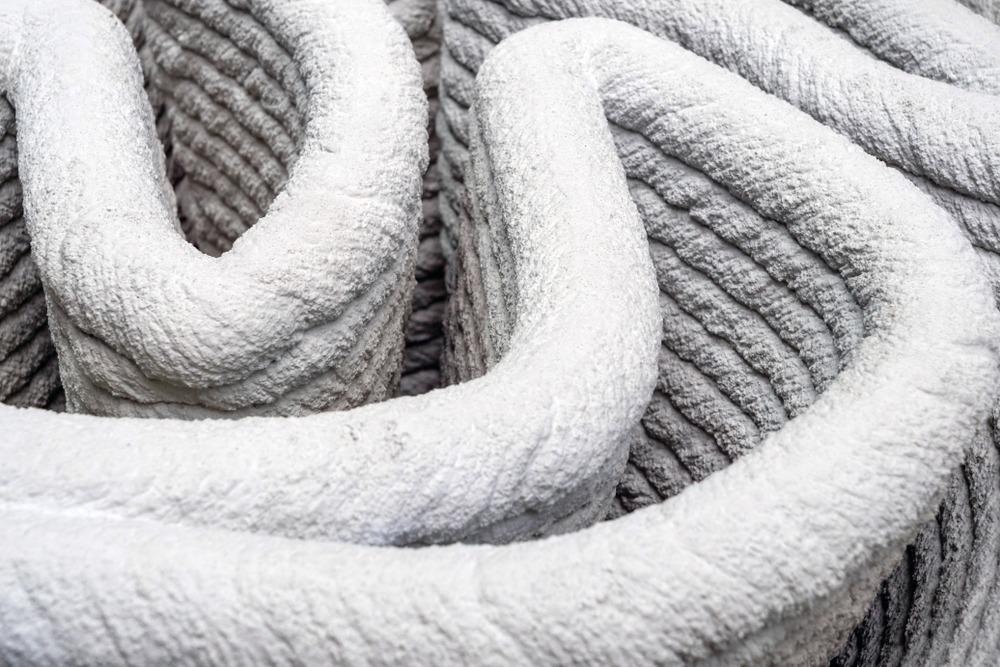
3D printed concrete. Image Credit: Zapp2Photo/Shutterstock.com
The binder materials used for this study included general-purpose cement (GPC), ground slag (GS), and silica fume (SF). Both river sand and recycled glass were obtained locally. A small amount of clay is added to the mixture to improve the buildability of printed structures. Two different directions of printing deposition are incorporated, one along the span of the beam specimen and the other one across it.
What does the Study Show?
The researchers partially replaced river sand with recycled glass and studied the effect of different grades of recycled glass on the bending performance of 3DCP structures and found the following results. The presence of glass particles increases the porosity of the samples.
Additionally, porosity in the samples with coarse glass particles is more significant than samples with fine glass; porosity is highest for a sand to glass ratio of 50:50. Also, the amount of medium-to-small pores are almost the same for all samples; the number of large pores increases with an increase in coarse glass content.
X-ray μCT images confirm that the primary factor of crack propagation is the presence of glass particles in voids. Samples containing glass particles show stress softening in the post-peak region of the stress-strain graph, whereas specimens with only sand filament show a brittle fracture. Moreover, the flexural strength of samples depends on the grade of glass grains and the type of loading. The addition of glass particles increased flexural strength by 25% to 33% when the beam span is perpendicular to the printing direction, contrary to that,
when specimen span was parallel to printing direction, it decreases flexural strength by 8% to 20%.
Therefore, a cross-loaded 3DCP with an optimal concentration of coarse glass particles is a suitable alternative for natural river sand and a sustainable approach in the construction of building structures.
Reference:
Liu, J., Li, S., Gunasekara, C., Fox, K., Tran, P., 3D-printed concrete with recycled glass: Effect of glass gradation on flexural strength and microstructure, Construction and Building Materials, 314, Part B, 2022, 125561, ISSN 0950-0618. https://www.sciencedirect.com/science/article/pii/S0950061821032992?via%3Dihub
Disclaimer: The views expressed here are those of the author expressed in their private capacity and do not necessarily represent the views of AZoM.com Limited T/A AZoNetwork the owner and operator of this website. This disclaimer forms part of the Terms and conditions of use of this website.