Researchers from Portugal recently developed an effective thermistor-type temperature monitoring method for boron-doped diamond-coated carbide cutting tools. It overcomes the limitations of the traditional temperature measurement approach with thin-film thermocouples and infrared thermography in certain cutting scenarios. This study is available in the journal Materials.
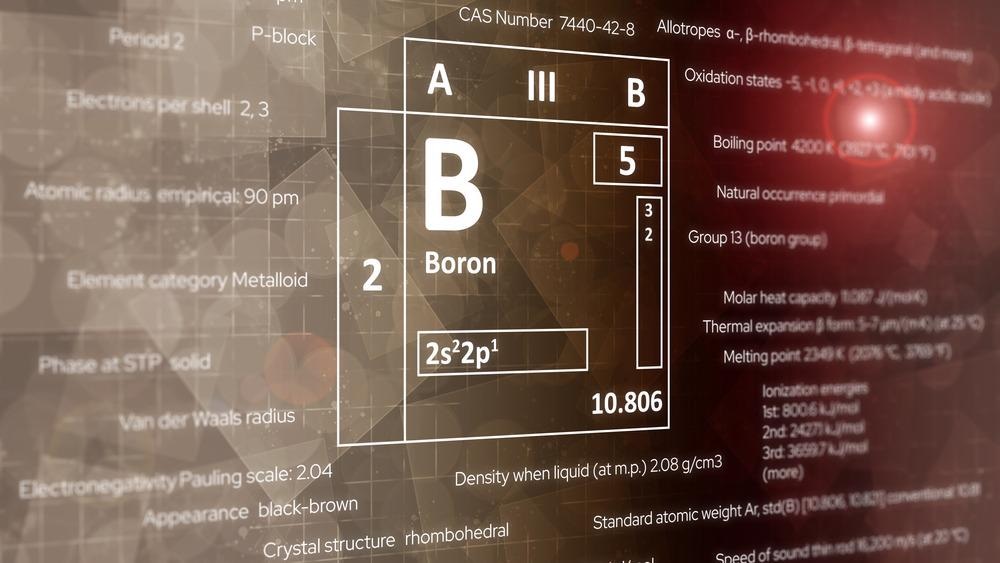
Study: Boron Doped Diamond for Real-Time Wireless Cutting Temperature Monitoring of Diamond Coated Carbide Tools. Image Credit: GRADIENT BACKGROUND/Shutterstock.com
Why Effective Temperature Monitoring is Essential for Higher Productivity?
In the metal and alloy machining industry, productivity is directly dependent upon process parameters such as cutting speed and feed rate. Hence, an increase in productivity can be achieved by optimization of the cutting cycle, increasing tool lifetime, and minimization of downtime. Two major factors, cutting force and cutting temperature, affect tool life. Thus, effective monitoring of cutting temperature can improve machining productivity.
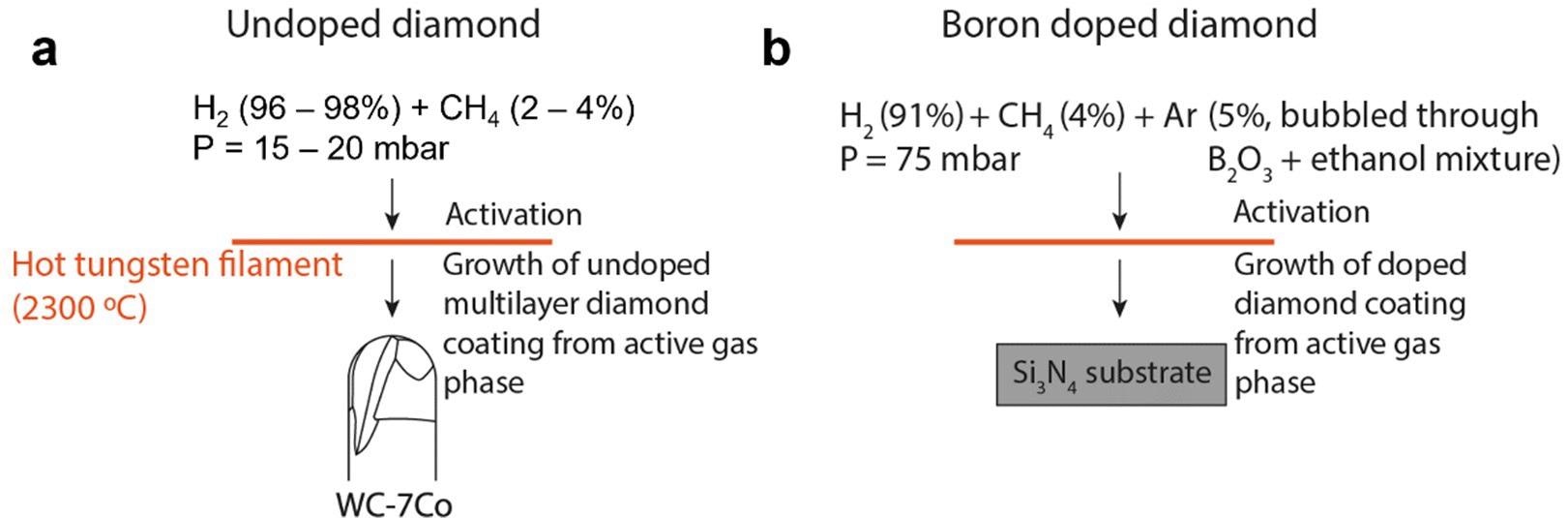
Experimental setup for Hot Filament Chemical Vapor Deposition of (a) undoped diamond on carbide end mills and (b) boron-doped diamond on a silicon nitride substrate for thermistor fabrication. Image Credit: Pratas, S et al., Materials
Heat generates at three primary zones during machining viz. the primary shear-zone (the plastic deformation at the interface of the machining tool and the workpiece), the secondary shear-zone (the friction at the interface of the tool and moving chips), and the tertiary deformation zone (the friction between flank face and the machined surface).
In situ temperature-monitoring methods such as infrared (IR) thermography and thermocouples provide good approximations of the metal surface temperature, but there are certain limitations for both.
Temperature monitoring with thermographic cameras is very sensitive to the emissivity of work material, which depends on factors like surface roughness, measurement angle, and the temperature of the surface being measured.
Hence, an accurate measurement can only be attained if the emissivity of the work object is well known throughout each specific range of varying machining conditions. Thermocouples suffer from the physical accommodation of wiring in tools and also provide inaccurate temperature readings since the hot junction of the thermocouple cannot be positioned directly at the machining interface, where maximum heat is generated.
Thermistors are temperature sensors calibrated by the dependency of resistance on temperature variation. Boron doped diamond (BDD) films developed by chemical vapor deposition (CVD) exhibit excellent temperature sensitivity.
When the temperature increases the electrical resistance of the BDD thermistor decreases. BBD also exhibits high chemical inertness, thermal conductivity, and mechanical robustness for applications under harsh working conditions.
About the Study
In this study, first, a diamond-coated carbide tool (DCC) is fabricated by depositing undoped diamonds on the tungsten carbide tool. The 7 wt.% cobalt cemented tungsten carbide (WC) grains are attacked with Murakami reagent for surface roughening followed by immersion in H2SO4 and H2O2 solution for cobalt etching.
These chemically treated specimens are coated with diamond powder to form multilayer diamond films in a hot filament-assisted CVD (HFCVD) reactor. The films are composed of nanocrystalline diamond (NCD) and sub-microcrystalline diamond (SMCD).
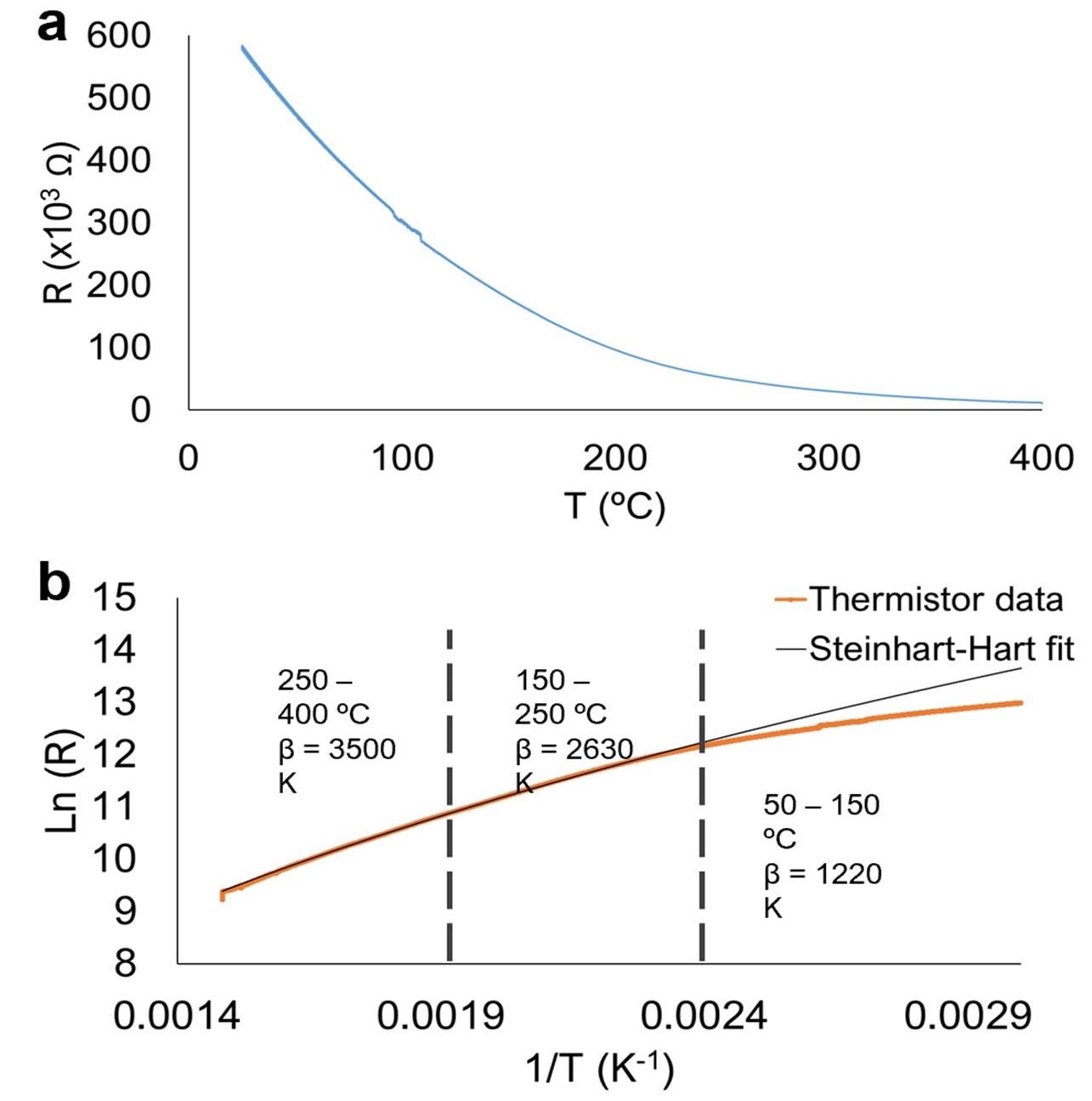
Resistance variation of the diamond NTC thermistor in the range 25–400 °C. (a) Measured curve. (b) Linear regression and fitting according to the “beta” and Steinhart-Hart models. Image Credit: Pratas, S et al., Materials
Subsequently, a thermistor is fabricated by the deposition of a BBD film on top of a silicon nitride (Si3N4) insulating substrate. Here, argon is used as the carrier gas for boron dopant in HFCVD. The carrier gas is bubbled through a B2O3/ethanol solution and deposits on the Si3N4 substrate.
Then, tungsten oxide (WO2) is vaporized from the tungsten hot filaments at 1800 ℃ followed by the reduction of WO2 in presence of hydrogen and methane to form ohmic tungsten carbide WC contacts.
Observations
The undoped CVD diamond films have a nine-layer architecture with two different morphologies viz. nanocrystalline diamond (NCD) and sub-microcrystalline diamond (SMCD). The increase in grain size increase the density of grain boundaries of the coating, which improves the cutting performance.
The prepared BDD thermistor demonstrates higher sensitivity in the higher temperature range. This behavior is attributed to a hopping conduction mechanism at low temperatures, which is due to the low doping level of the diamond film (~600 kW at 25 ℃).
This corresponds to a resistivity of approx. 900 W.cm. The response time of the diamond thermistor closely matches the response time of the thermographic camera with an average delay of ~1 s. The BDD thermistor shows an average voltage variation of 16.5 mV in the photodiode, due to the difference between the highest temperature at inflection positions of the cutting tool and the lowest temperature at the mid path.
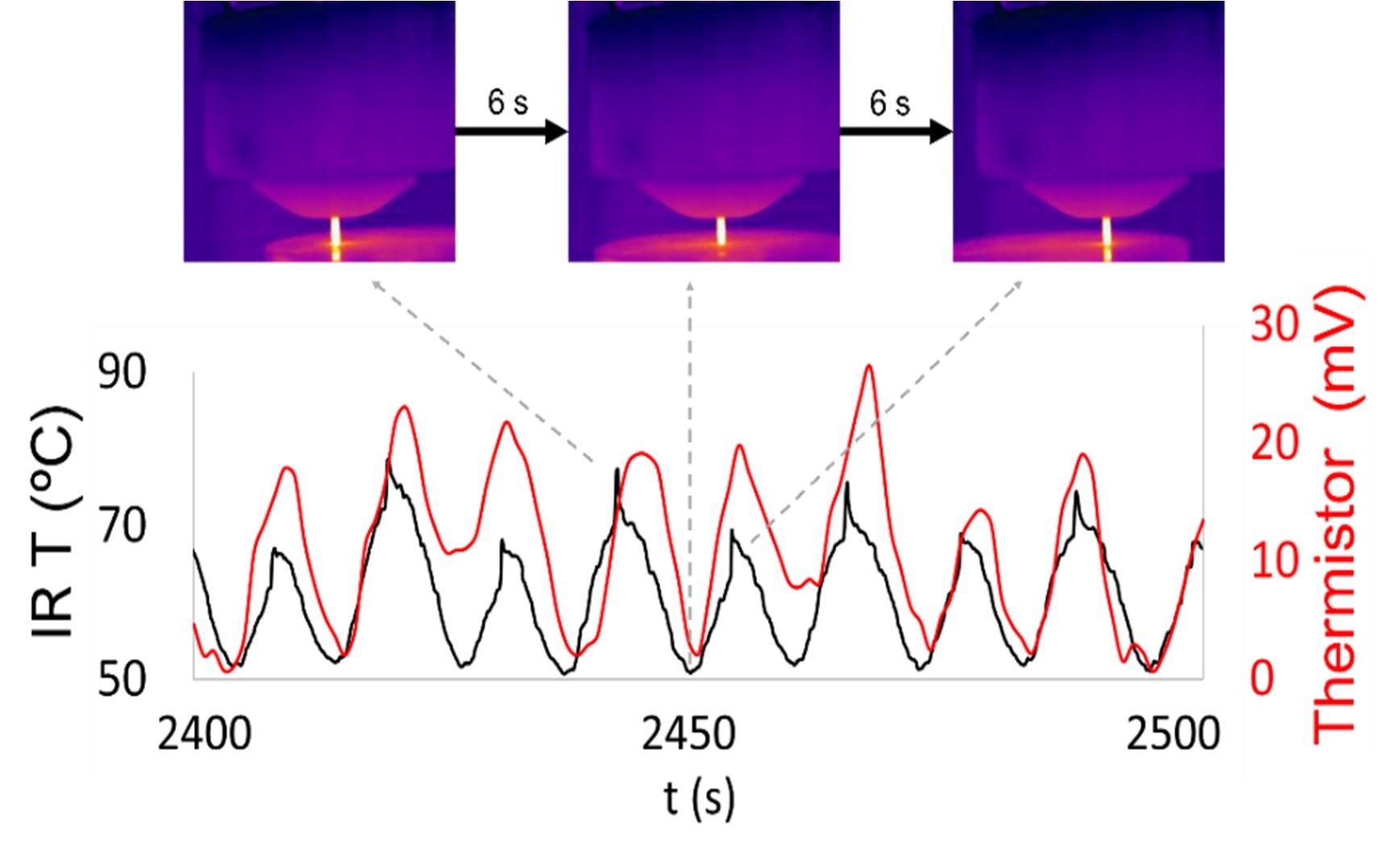
Temperature measurement recorded by the thermographic camera shows the occurrence of lower temperature at the tool tip when approximately at the middle of the cutting path and higher temperature at inflection positions. This curve was used for calibration of the diamond-based thermistor, for which the resistance variation induced a 0.84 mV/°C variation at the photodiode. Image Credit: Pratas, S et al., Materials
Conclusions
In this study, a BBD-based thermistor is fabricated by HFCVD to monitor the temperature variation during the milling of an Inconel workpiece using a DCC cutting tool. The linear regression of the characteristic resistance-temperature dependence of the BDD thermistor indicated higher temperature sensitivity in the temperature range of 250 to 400 ℃.
Moreover, the BBD thermistor exhibits a faster response and minor average variation of 0.84 mV/ ℃ than its counterpart IR thermography. To conclude, BBD thermistor is an effective, fast responsive, real-time, and in situ temperature monitoring solution for the heavy machining industry.
Reference
Pratas, S., Silva, E.L., Neto, M., Fernandes, C., Fernandes, A., Figueiredo, D., Silva, R., Boron Doped Diamond for Real-Time Wireless Cutting Temperature Monitoring of Diamond Coated Carbide Tools. Materials, 2021, 14, 7334. https://www.mdpi.com/1996-1944/14/23/7334
Disclaimer: The views expressed here are those of the author expressed in their private capacity and do not necessarily represent the views of AZoM.com Limited T/A AZoNetwork the owner and operator of this website. This disclaimer forms part of the Terms and conditions of use of this website.