Intense and stable nanosecond laser pulses are increasingly being used in several research fields. Writing in the journal Optics Communications, a team of scientists has explored their use to propel stainless steel microspheres.
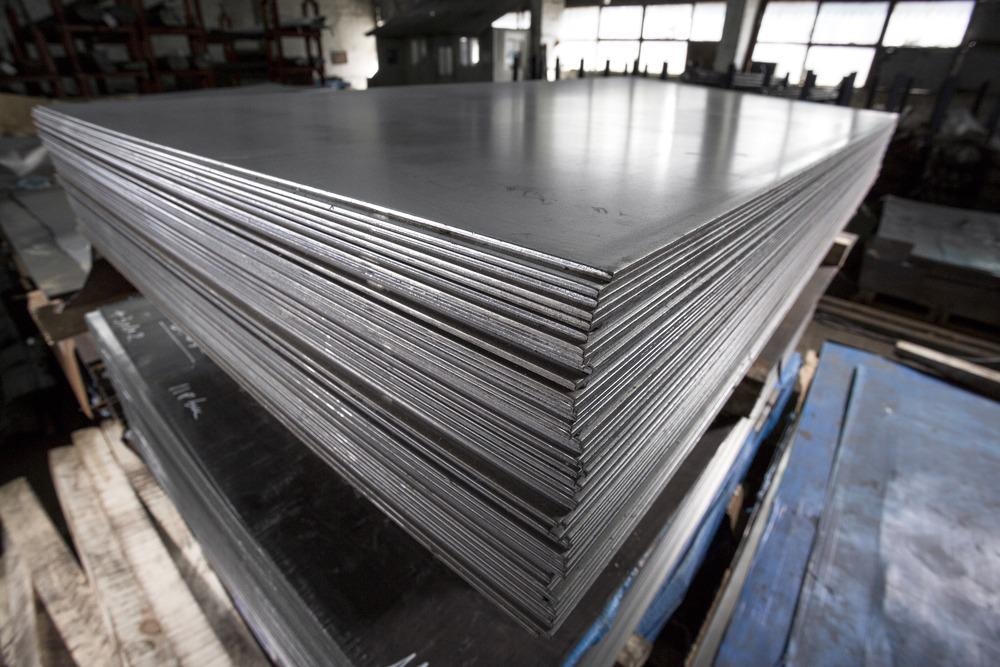
Study: Metal microspheres propelled by shock wave based on the fiber structure laser propulsion. Image Credit: Alexandru Rosu/Shutterstock.com
Nanosecond Laser Pulses and Propulsion
Nanosecond laser pulses have recently gained research focus for their use in several applications such as laser drilling, laser micromachining, and laser propulsion. Using nanosecond laser pulses for propulsion has been proposed as an alternative thrust method due to low launch cost, high payload, and laser propulsion being a non-contact technique. The technique has the potential for cleaning orbital debris, micro-adjustment of satellite attitude, and laser cleaning.
The potential of using nanosecond laser pulses for propulsion was demonstrated by L Felicetti et al. by using the method to propel a small satellite. The results of this research demonstrated that the propulsion efficiency is related to the energy of the laser. Thrust is generated by high-energy and high-temperature plasma, and a recoil effect facilitates the movement of the object. Laser propulsion can be generally divided into two modes: ablation and air-breathing.
Using nanosecond laser pulses to provide propulsion offers high controllability, non-contact, and directionality. Research has now started to focus on utilizing laser propulsion at the microscale for the control and manipulation of materials and machinery.
Recent Work in Microscale Laser Propulsion and Challenges
Recently, there have been studies in this field that have demonstrated the potential of nanosecond laser pulses to provide microscale propulsion for a variety of applications. Yu et al. investigated the effect of shockwave mechanisms on polystyrene and SiO2 microspheres using nanosecond laser pulses. The work clarified the influence of microsphere size and laser energy on laser propulsion. However, due to the lack of free electrons in these materials, propulsion efficiency and plasma intensity was reduced.
Metal materials have been explored to improve propulsion efficiency. In a recent research study, Demo et al. investigated laser cleaning to help understand the interaction between the laser and the metallic materials and further understand the laser-induced damage upon materials.
More on Lasers - Increasing Wear Resistance with Laser Heat Treatments
Challenges with using nanosecond laser pulses for microscale and nanoscale applications have been identified in recent bodies of work. There are issues with the high irradiation of the microsphere’s surface by laser energy, which can exceed the microsphere’s breakdown threshold and cause the proliferation of contaminant particles. Additionally, the laser spot can have a high diameter. Furthermore, the microsphere’s propulsion direction can be difficult to control.
Due to these challenges, research has focused on creating fiber-based systems that improve laser energy control and scalable spot size to improve the microscale propulsion of metal microspheres. These systems have the advantage of high power, specialized fiber structures, and controllable distance from the microspheres and can effectively improve the efficiency of propulsion.
Developing a Fiber-Based Nanosecond Laser Pulse Propulsion System for Controlling Metallic Microspheres
The study published in Optics Communications has proposed a fiber-based laser propulsion system for propelling stainless steel microspheres. The fiber face emits nanosecond laser pulses in a highly controllable manner. Using the system, the authors investigated the interaction between metal microspheres and laser pulses. The team observed that the novel laser propulsion system provided directional control of the stainless-steel microspheres.
Moreover, using the system, the microsphere's propulsion efficiency could be controlled by adjusting the laser pulse energy and gap distance. The results of the study also demonstrated that the stainless-steel microsphere’s propulsion efficiency was higher than non-metallic spheres. Furthermore, the team utilized the system to clean contaminants off the surface of the stainless-steel microspheres.
The team used a combination of simulations and experimental observations to draw conclusions on the propulsion efficiency of the stainless-steel microspheres using the novel fiber-based nanosecond laser pulse system. Experimental phenomena displayed a good level of agreement with the simulation results.
Based on their observations, the team proposed that their novel fiber-based nanosecond laser pulse propulsion system could be utilized for laser cleaning and the manipulation of microelectronics and microscale metallic machinery.
The Future
The authors behind the study in Optics Communications have demonstrated the development of a novel nanosecond laser pulse system that is constructed out of fibers. The system provides enhanced levels of control and propulsion efficiency with the advantage of non-contact for microscale applications.
Furthermore, by demonstrating that the system can be used for laser cleaning, the possibility of using it for applications like metal pollution control. Additionally, the team concluded that the novel laser system could be used for the manipulation of microscale metal machinery. The research helps to lay the groundwork for future laser propulsion studies.
Further Reading
Li, H et al. (2021) Metal microspheres propelled by shock wave based on the fiber structure laser propulsion [online] Optics Communications | sciencedirect.com. Available at: https://www.sciencedirect.com/science/article/abs/pii/S003040182100910X
Disclaimer: The views expressed here are those of the author expressed in their private capacity and do not necessarily represent the views of AZoM.com Limited T/A AZoNetwork the owner and operator of this website. This disclaimer forms part of the Terms and conditions of use of this website.