The latest article published in the journal Materials focuses on the hydrogen sorption properties of casted Ag-Mg alloys.
Study: Hydrogen Sorption Behavior of Cast Ag-Mg Alloys. Image Credit: D. Alimkin/ Shutterstock.com
The research was conducted on four alloys from the two-phase area (Mg) + γ `(AgMg4 )with nominal concentrations of 5 wt. percent, 10 wt. percent, 15 wt. percent, and 20 wt. percent Ag, as well as four alloys with nominal compositions comparable to intermetallic phases: AgMg4, AgMg3, AgMg, and Ag3Mg.
Introduction to Hydrogen Sorption
Hydrogen sorption (adsorption/absorption) in metals, whether as thin films or nanoparticles, is a significant procedure in power storage and chemical processing. Molecular hydrogen absorbed in a metal's substructure influences its interface molecular and electrical frameworks, as well as its surface chemistry and catalysis characteristics. Furthermore, alloy effects influence both catalysis and gas sorption events. For storing hydrogen, hydrocarbons absorption on activated carbons (ACs) is a potential option for compressing and decompression.
Importance of Hydrogen, Its Storage and Green Technologies
Intensive research has been conducted in recent years to enable the growth of renewable initiatives, such as hydrogen energy, in the context of vehicle industries and renewable sources. Hydrogen is a volatile and combustible fuel that necessitates particular measures for proper storage.
Hydrogen can be held in compacted or liquefied form, as well as attached to the surface of objects or chemically bonded as hydrides. Although it appears to be irrational, society considers condensed hydrogen to be unsafe and economically unviable due to significant compression costs and a comparatively low volume capacity of around 40 kg/m3.
Liquid Hydrogen Systems
Solvent hydrogen storage is even less cost-effective than compressed hydrogen storage and necessitates the use of specialized refrigeration systems at a temperature of 20 K. Metal halides or interfacial materials, which may hold 80–150 kg of hydrogen per 1 m3, are the last way of energy storage. As a result, this approach is the most beneficial type of hydrogen storage in terms of both safeties (when utilized appropriately) and volumetric capacity.
Magnesium Based Materials for Hydrogen Storage
Many metals and intermetallic phases absorb and desorb hydrogen efficiently, however because of their poor specific gravity capability, they are not being evaluated for potential mobile applications. Because of the high gravimetric capacity of hydrogen (up to 7.6 wt. percent for MgH2) and low price, magnesium-based halides are among the most potential candidates for hydrogen storage.
However, due to the requirement for extreme temps and the sluggish dynamics of the hydrogen sorption cycle, the use of Mg for hydrogen storage is impractical. As a result, much research is presently being performed throughout the world to optimize the kinematics of hydrogen sorption in magnesium alloys by the use of alloying additives or catalysts.
Research Findings
The major diameters of the particles following the filling procedure were shown by SEM images to be between tens and hundreds of Microns. This size is adequate to facilitate hydrogenation. The overall finding is that filings obtained from two-phase alloys are bigger than those derived from intermetallic phases.
This most likely suggests that two-phase alloys have slightly increased plasticity. Brittle cleavages were detected for the "e" and "f" samples, which is relatively counterintuitive given that strong brittleness is expected for AgMg and Ag3Mg materials.
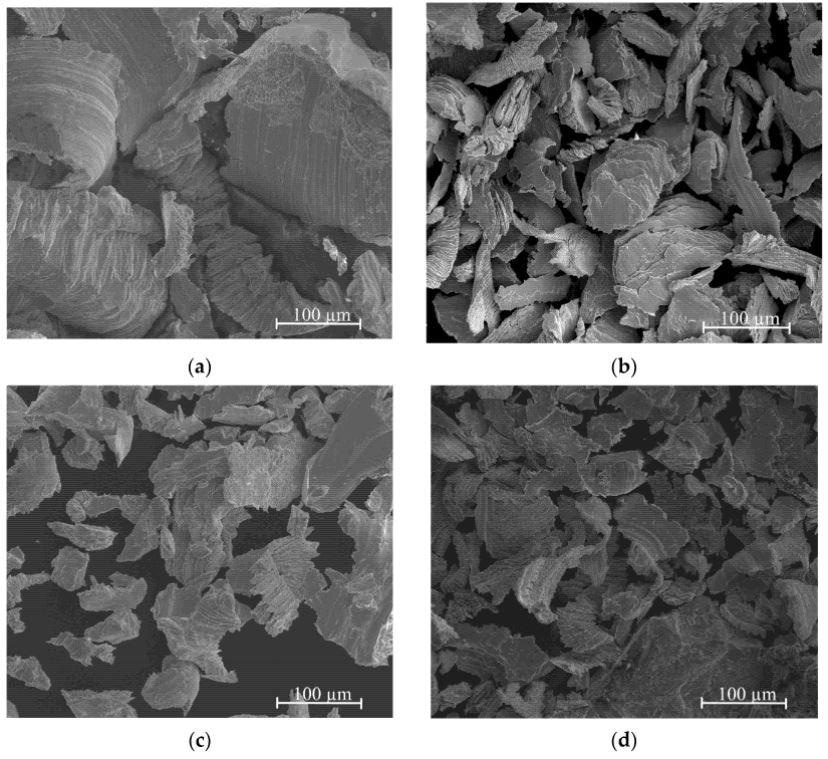
SEM microstructures of various Ag-Mg alloys: (a) Alloy 10, (b) Alloy 9 (e) Alloy 6, (f) Alloy 5. Image Credit: Dębski et. al, Materials
The existence of the predicted inter-metallic phases was verified by XRD analyses in the majority of the acquired samples. The most notable change is the occurrence of an ε’ phase rather than the ε predicted phase (Alloy 6). This phase has previously been discovered in cast alloys.
Hydrogen sorption experiments were carried out. It was discovered that the alloy includes 10% wt. Ag, allowing for maximal hydrogen absorption at 350 C in a proportion remarkably comparable to that of pure Mg. Because the sample did not achieve the optimum level at the specified (acceptable) single point saturation timings for 300 C, it became clear that the measurement points were kinetically impacted (90 min).
The addition of silver to magnesium lowered sorption capacity and had no influence on hydrogen sorption kinetics; however, samples from the hypoeutectic zone (up to 20% Ag) showed a relatively unfavorable correlation. The evident discrepancies in kinetics might be attributed to variances in particle size employed in the tests, among other things.
The very first 3 specimens with the greatest Ag content did not show surface alterations, but the next four samples with Ag concentrations less than 50% showed surface changes.
In short, a study examining the impact of Ag in Ag-Mg alloys prepared by metallurgy methods on Hydrogen sorption was performed, which revealed that the higher the Mg concentration, the more hydrogen assimilated, and as the reaction of alloys with hydrogen continued, the AgMg part is established, which continues to remain in the commodity.
Reference
Dębski et. al. (2022) Hydrogen Sorption Behavior of Cast Ag-Mg Alloys. Materials. 15(1). 270. Available at: https://www.mdpi.com/1996-1944/15/1/270
Disclaimer: The views expressed here are those of the author expressed in their private capacity and do not necessarily represent the views of AZoM.com Limited T/A AZoNetwork the owner and operator of this website. This disclaimer forms part of the Terms and conditions of use of this website.