In a recent paper published in the journal Energies, researchers from Mexico simulated the aerodynamic behavior of a Savonius-type vertical wind turbine with a semi-elliptical profile using a 3D computational model based on computational fluid dynamics (CFD).
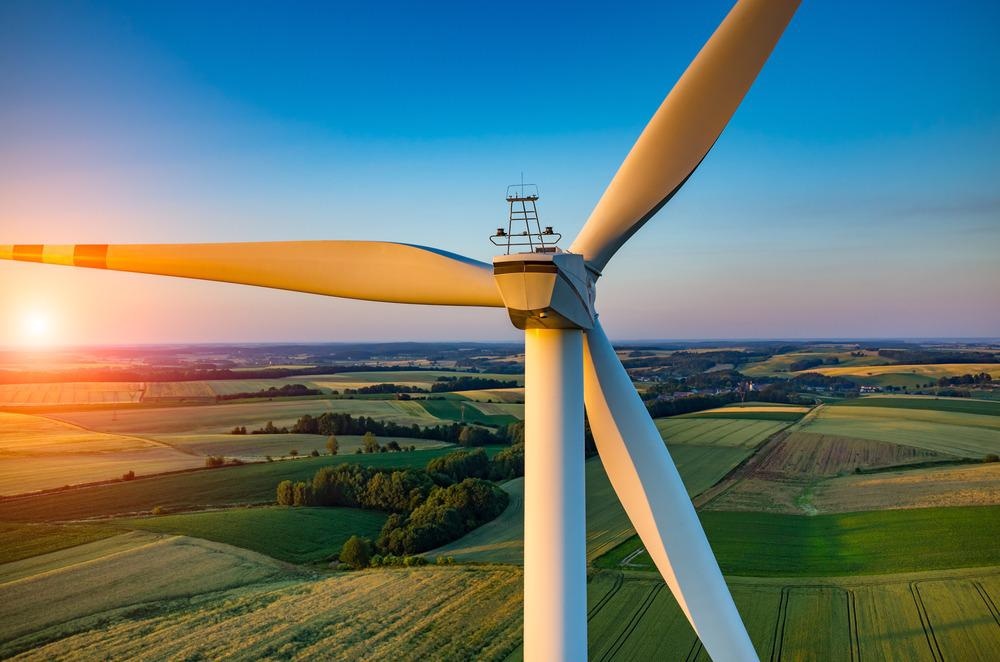
Study: Integrated Surrogate Optimization of a Vertical Axis Wind Turbine. Image Credit: Stockr/Shutterstock.com
The researchers evaluated its power coefficient (Cp), defined a full factorial design of experiments (DOE) to achieve a sample search space on the geometry of the wind turbine, and used machine learning to optimize its Cp.
Vertical Axis Wind Turbines
Wind turbines are one of the primary devices used to harness wind-based renewable energy. They are classified into two types based on their orientation of the axis of rotation to the direction of the wind flow, namely, vertical axis wind turbine (VAWT) and horizontal axis wind turbine (HAWT).
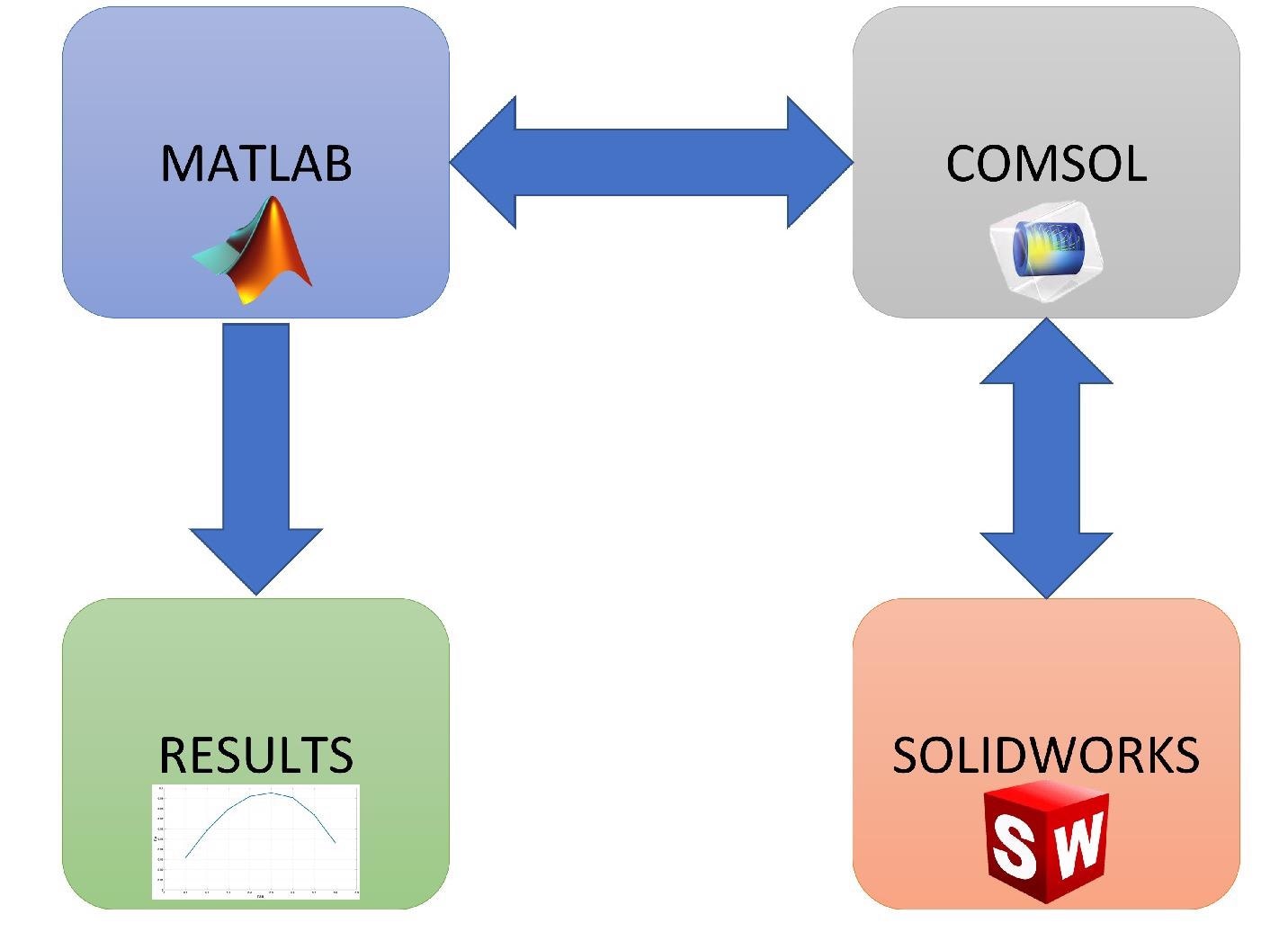
Integration of computing platforms. Image Credit: Moreno-Armendáriz, M.A et al., Energies
In particular, the Savonius VAWT has several advantages such as simple small-scale design, low installation, and maintenance cost, high self-starting capacity, and independence to wind direction and wind speed, which allows it for small-scale applications for self-consumption purposes. However, the major issue with this type of wind turbine is its low theoretical efficiency, which needs to be optimized using suitable analysis tools.
The previous studies have found several factors that are known to affect the Cp of VAWT, which are the number of blades, the shape of blades, the helix angle, tip speed ratio (TSR), the overlap region between each blade, incorporation of endplates and wind deflectors, and the shape and number of wind deflectors.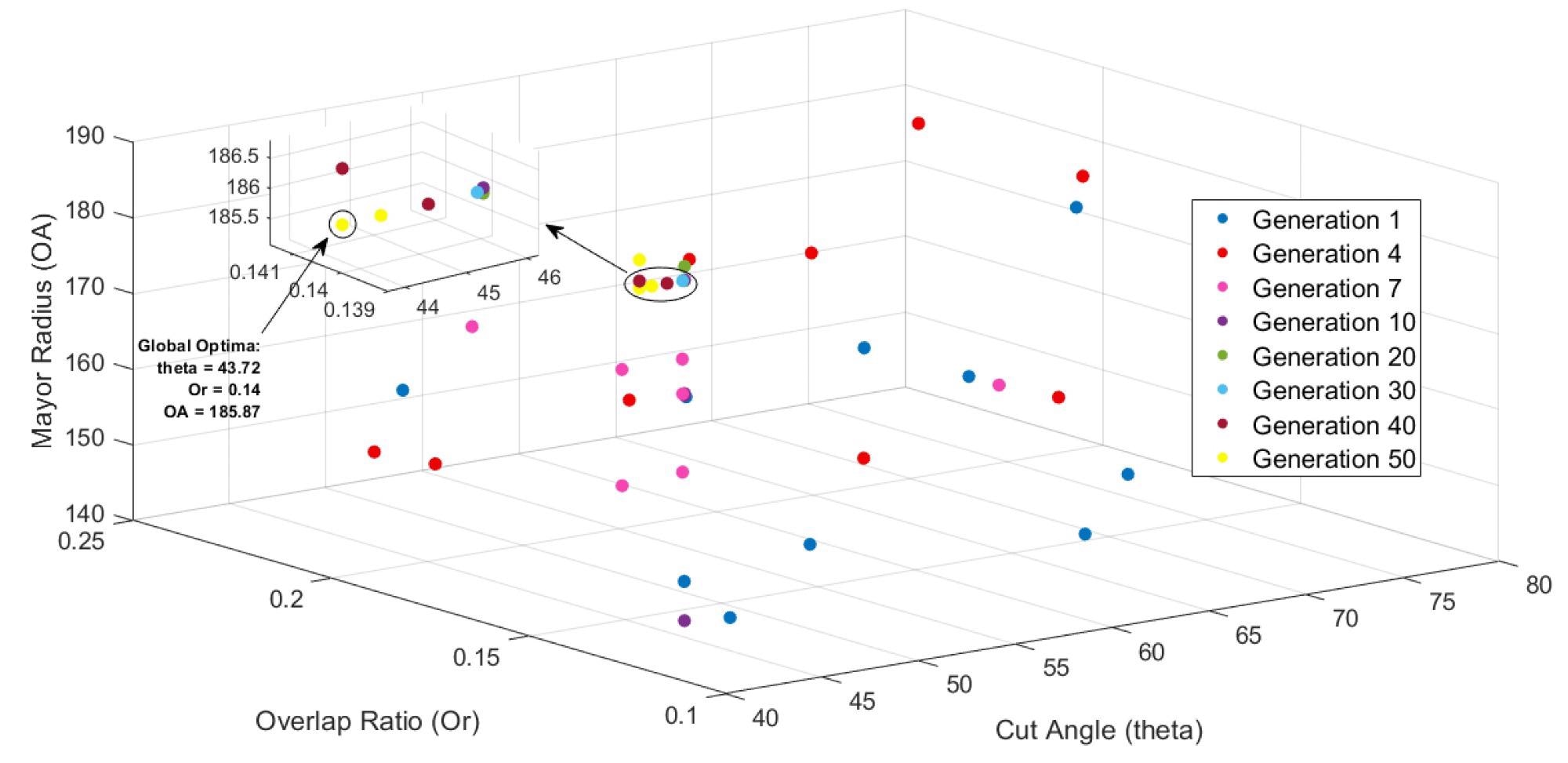
Evolution of population in genetic algorithm. Image Credit: Moreno-Armendáriz, M.A et al., Energies
About the Study
In this study, researchers optimized the design of a Savonius VAWT to maximize its energy conversion efficiency using a surrogate model and metaheuristic optimization algorithm for machine learning. Also, they compared three methods of design and optimization based on experimental tests, computational models, and surrogate models for better accuracy.
Initially, a 3D geometric model of the wind turbine was built using computer-aided design (CAD) software, followed by a computational model was built using computer-aided engineering (CAE) software to simulate the rotor’s interaction with the wind flow. After that, a DOE was defined to search for the optimized solution in a sample space. Finally, the surrogate model designed through machine learning was subjected to metaheuristic optimization algorithms.
Furthermore, the algorithms used for building the surrogate model were support vector machine (SVM), random forest (RFR), Bayesian ridge regression (BR), and multilayer perceptron (MLP). Moreover, the metaheuristic algorithms were artificial bee colony (ABC), genetic algorithm (GA), and particle swarm optimization (PSO). Finally, all the computing models viz. Matlab, Cosmol Multiphysics, and Solidworks were integrated using a client-server type link.
Observations
Due to the presence of turbulence in the flow of wind, the CAE model underestimated the value of Cp with an average error of 0.0548. However, the Cp-TSR curve indicated good convergence in terms of the mesh at a suitable operating range of the wind turbine. Additionally, the RFR algorithm showed the best performance for the surrogate models with a coefficient of determination of 0.98 and 0.97 in the testing and training stages, respectively.
The RFR surrogate models were designed using all three metaheuristic optimization algorithms viz. ABC, GA, and PSO indicated identical performances. Also, the difference or absolute error between the maximum Cp values estimated by the RFR model and those calculated by the CAE model did not exceed 0.008, which was equivalent to a marginal error of less than 1%. The designs calculated with the CAE model and at a TSR of 0.6 demonstrated a maximum Cp for the GA algorithm of 0.1296, followed by a maximum Cp of 0.127 and 0.1264 for the PSO algorithm and ABC algorithm, respectively.
Furthermore, it is important to diminish the negative effect of the return blade through the redirection of flow from the forward blade to the return blade, which is evident from the outcome that wind flown through the overlap between the blades with a speed of up to 4 m/s runs through the entire concave surface of the return blade, which provided it with an additional thrust.
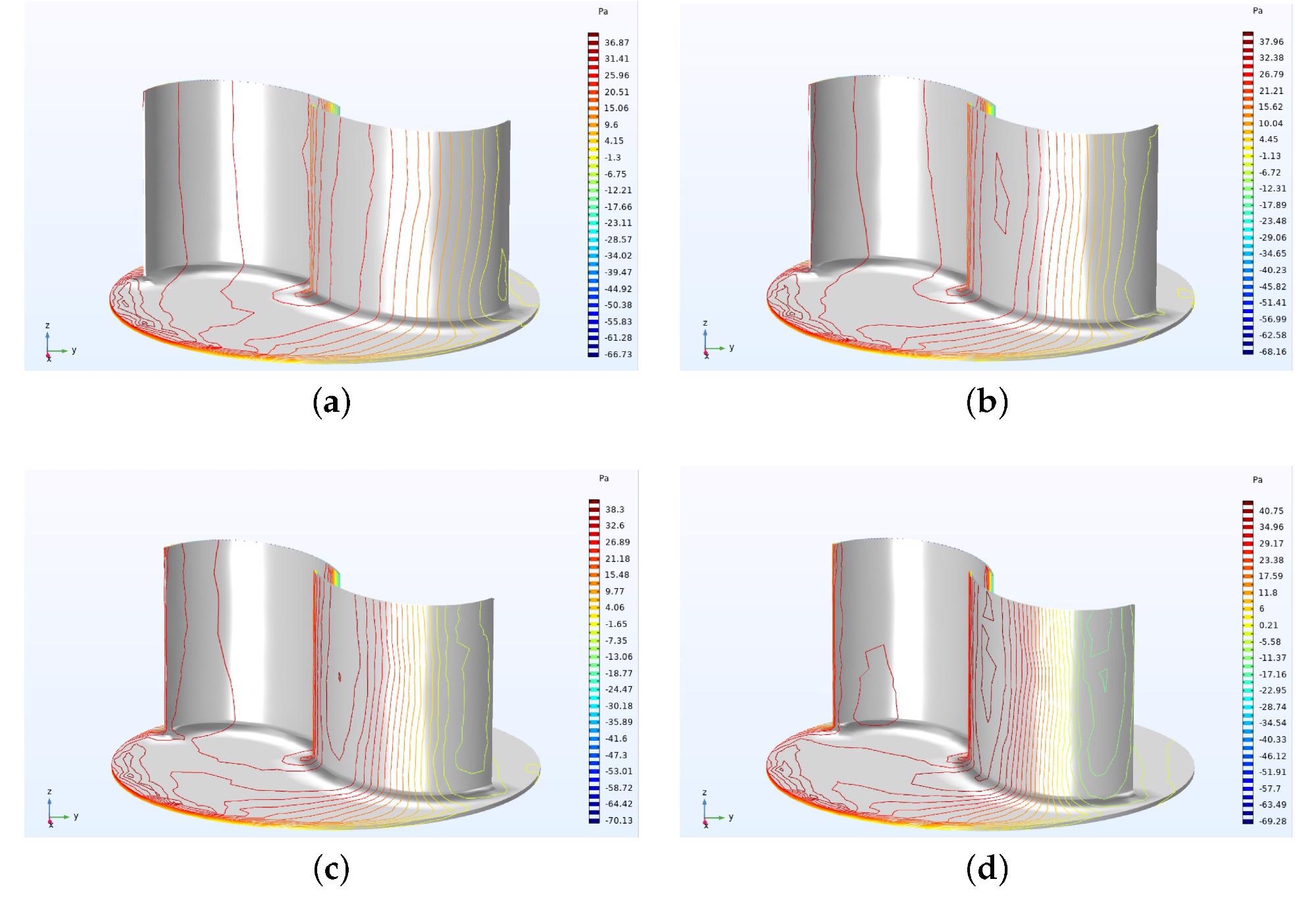
Pressure lines (Pa) on the lower half of the geometry of the GA-optimized Savonius wind turbine, (a) Instant pressure at t=1.2217, (b) Instant pressure at t=1.2305, (c) Instant pressure at t=1.239, (d) Instant pressure at t=1.248. Image Credit: Moreno-Armendáriz, M.A et al., Energies
Conclusions
In this study, the researchers simulated the aerodynamic behavior of a Savonius VAWT using a surrogated model with several metaheuristic optimization algorithms to obtain an optimized design with maximum Cp. The RFR model with GA algorithm demonstrated better performance overall compared to any other combinations. Moreover, the Savonius type VAWT with a semi-elliptical blade profile has the most potential for self-consumption applications in rural and urban areas, where the wind flow speed is lower, and the power demand is less than 1 kilowatt.
Reference
Moreno-Armendáriz, M.A.; Ibarra-Ontiveros, E.; Calvo, H.; Duchanoy, C.A. Integrated Surrogate Optimization of a Vertical Axis Wind Turbine. Energies 2022, 15, 233. https://www.mdpi.com/1996-1073/15/1/233
Disclaimer: The views expressed here are those of the author expressed in their private capacity and do not necessarily represent the views of AZoM.com Limited T/A AZoNetwork the owner and operator of this website. This disclaimer forms part of the Terms and conditions of use of this website.