By Susha Cheriyedath, M.Sc.Reviewed by Skyla BailyJan 10 2022
In an article published in the open-access journal Materials, researchers studied welded joints of Al- MG-LI alloy with zirconium additives.
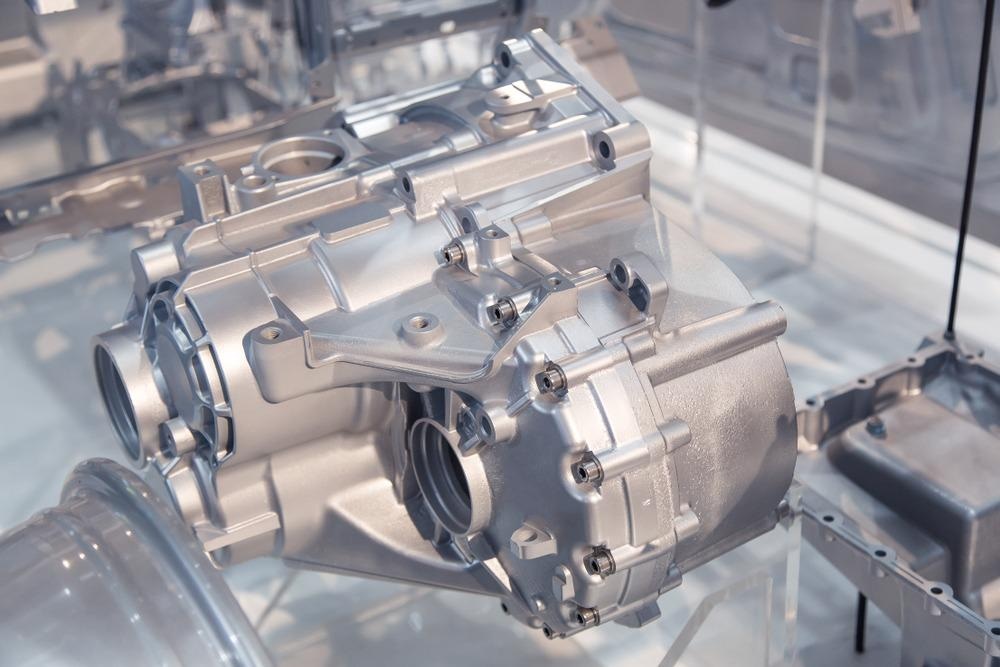
Study: Porosity Formation in Thin Welded Joints of Al–MG–LI Alloys. Image Credit: patruflo/Shutterstock.com
The character and regularity of pore formation were studied by the application of thermal vacuum treatment (TVT) and by using different welding technologies like electron-beam welding (EBW) and metal inert gas (MIG) welding. Metallographic analysis was carried out and the composition of the alloy and weld metal was investigated.
Why Study Pore Formation in Al– MG–LI Alloy?
For every 1% lithium, there is a decrease in the density of the Al–MG–LI alloy by 3% but an increase in Young’s modulus by 5%. The alloy possesses a high elastic modulus, low density, high corrosion resistance, high weldability property, and is used in the synthesis of lightweight structures, particularly in the aircraft industry.
The main difficulty in welding Al-MG-LI alloy is the formation of a strong oxidation layer and high adsorption of gases that assists pore formation. The pore formation in the alloy is mainly due to the formation of the surface layer during heating, and the compounds of the surface layer separate during heating with the release of gases like hydrogen.
The All-Russian Scientific Research Institute of Aviation Materials (VIAM) recommends the thermal vacuum treatment of materials to prevent pore formation in welds of the Al-MG-LI alloy. The application of TVT changes the composition of the weld and reduces the concentration of hydrogen released and in turn reduces pore formation.
Two welding techniques - MIG argon arc welding and electron beam welding – were employed in welding the Al-MG-LI alloy. The chemical composition of the alloy was analyzed, and the microstructure of the section was studied using an optical stereomicroscope and an inverted light microscope. The phase composition was analyzed using XRD analysis, and thermodynamic calculations during equilibrium crystallization of alloy were performed using JMatPro, the materials property simulation package software.
Thermodynamic calculation of the alloy the phase composition of: (a) stable phases; (b) metastable phases. Image Credit: Olshanskaya, T et al., Materials
Observation
The addition of Zirconium additives revealed the strengthening phase formation; the alloy without TVT revealed stable strengthening phases and a metastable phase. After the standard heat treatment T6, Al2LiMg and Al3Mg2 were the stable hardening phases and Al3Li was the metastable phase. The content of chemical elements released changed based on temperature changes.
TVT with subsequent heat treatment resulted in the alignment of chemical components on the surface grain body and the fixation of homogenous solid solution, which disperses the strengthening phases and these results were confirmed by metallographic studies. The metallography results revealed finely dispersed phase allocation and the nature of formation and distribution of pores with and without TVT.
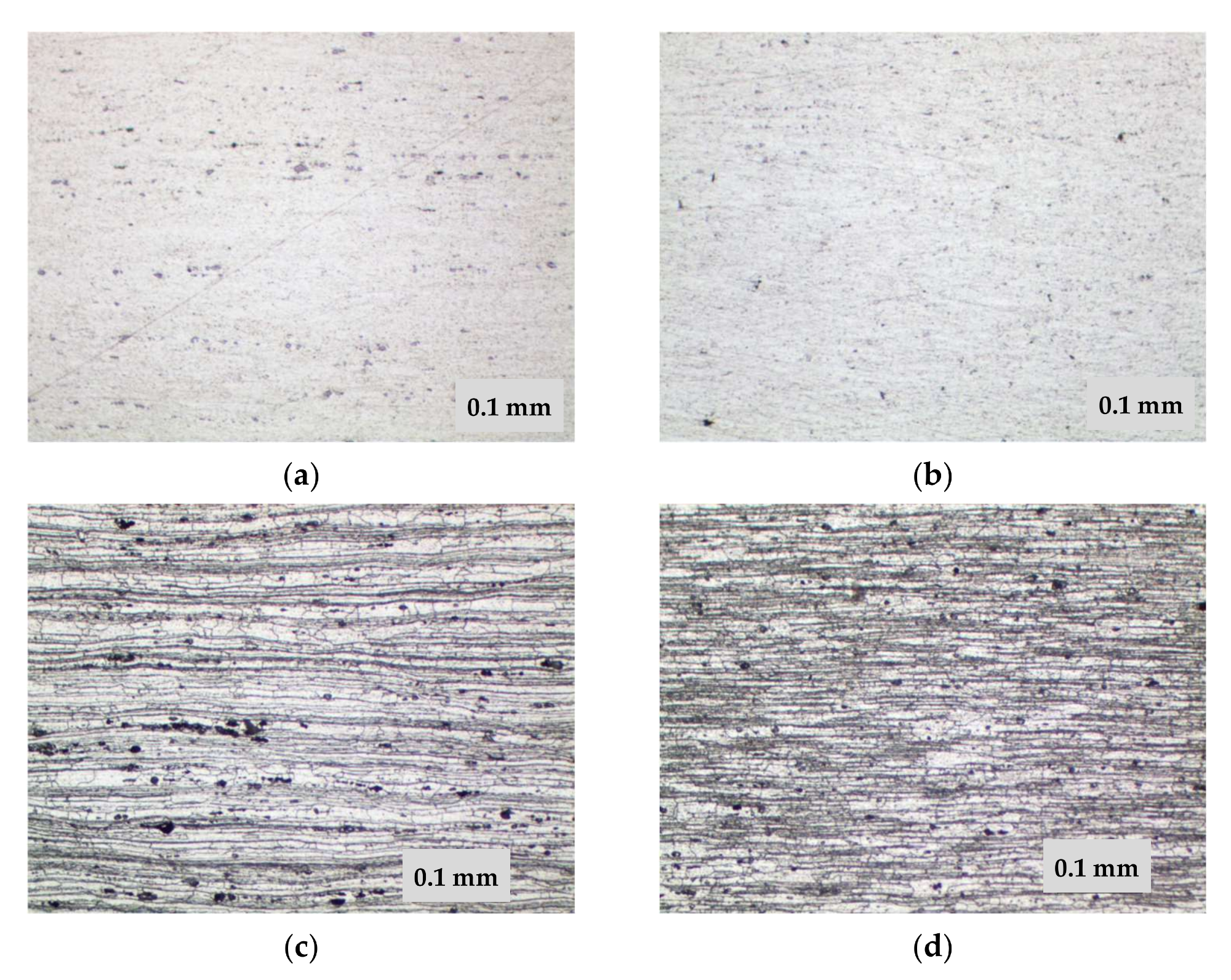
Microstructure of 1420 alloy after standard heat treatment (a,c) and after TVT (b,d), x200: (a,b) not etched surface; (c,d) after etching. Image Credit: Olshanskaya, T et al., Materials
The XRD data showed phase composition data and that TVT followed by aging and quenching has no effect on the phase composition of the alloy and this agrees with the thermodynamic results.
During MIG welding, the pores were formed irrespective of TVT and no pores were observed during EBW. The formation of certain phases like Al6Mn and Al3Mg2 was observed during the beginning and end of crystallization and this correlated with the literature data. The gas accumulates in a boundary layer of the metal when the crystallization front moves and this increase exceeds the standard solubility.
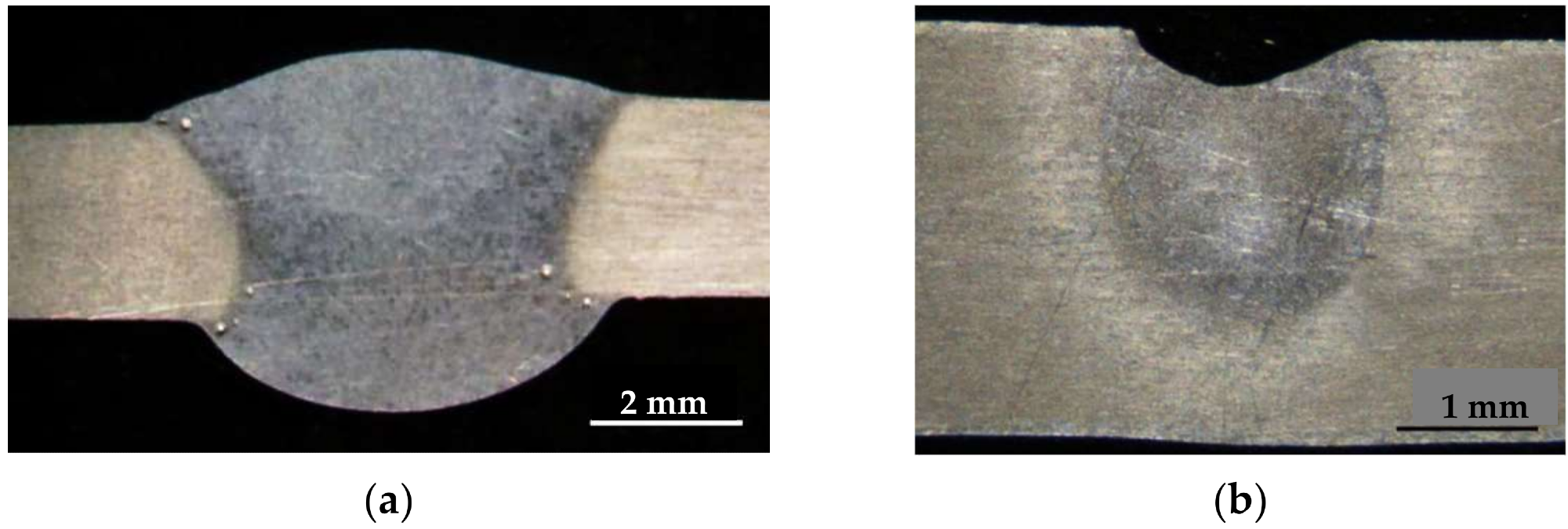
Macrostructure of welds made by different welding methods of 1420 alloy at different initial state: (a) argon arc welding (MIG) with AlMg-6 wire, base material after TVT; (b) electron beam welding (EBW), base material after TVT. Image Credit: Olshanskaya, T et al., Materials
During aluminum crystallization, the hydrogen atoms tend to decrease the solubility, and hydrogen is redistributed between the solid and liquid layers by laws of diffusion. This causes the impurities in the metal to recombine and form gas bubbles. The gas bubbles float onto the surface because of the ductile properties of the metal. The bubbles that do not resurface remain in the metal after crystallization and form pores. EBW was performed under vacuum conditions and the gases were removed before crystallization.
In EBW welded joints, a more uniform distribution of hardness was observed. This is because the process is carried out in a vacuum where all the gases are removed. When aluminum mixes with hydrogen, it forms an embedding solid solution and this changes the hardness of the weld. TVT helps achieve a uniform hardness of the alloy in both welding techniques.
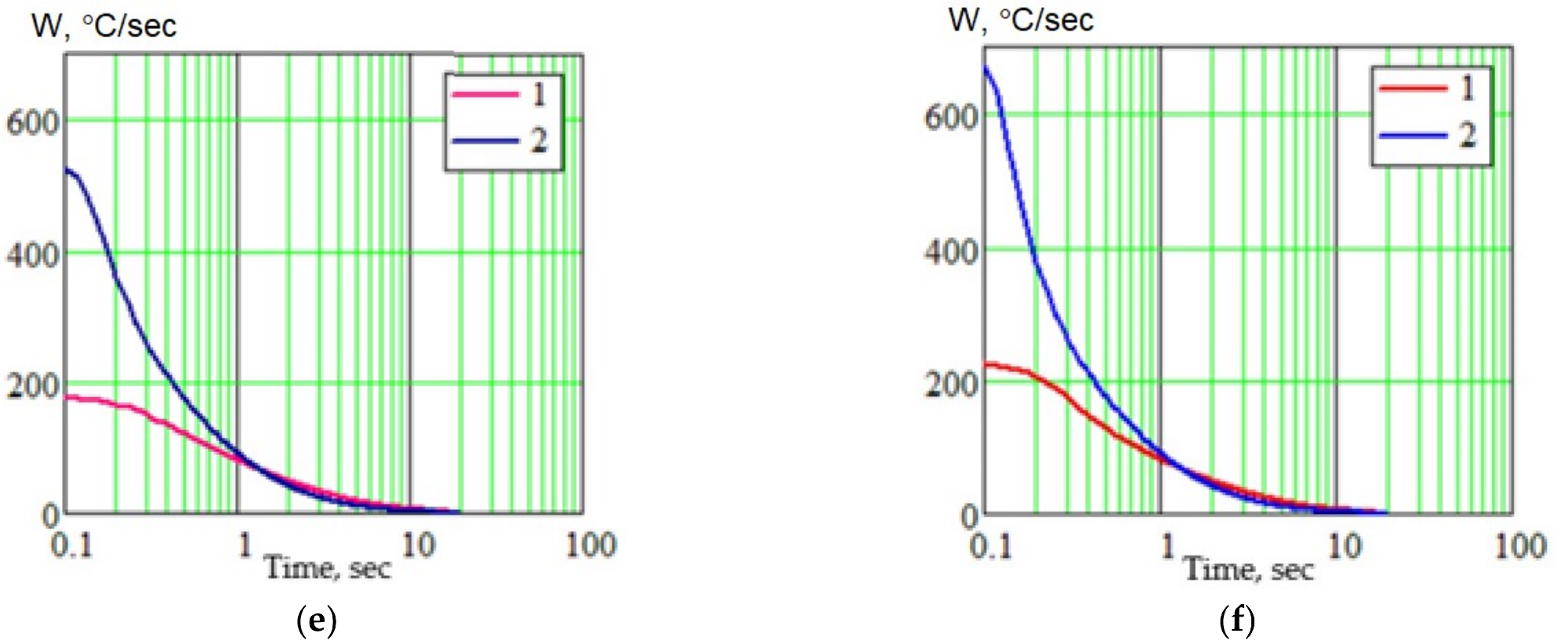
Calculation results of thermal cycle parameters for MIG (1) and EBW (2) welding for the fusion zone (a,c,e) and weld metal (b,d,f): (a,b) thermal cycle; (c,d) cooling curves; (e,f) instant cooling rates. Image Credit: Olshanskaya, T et al., Materials
Conclusion
To conclude, the influence of base material, thermal vacuum treatment, and welding technologies on pore formation have been analyzed in welded joints of the Al–MG–LI alloy. The addition of zirconium additives to the Al– MG–LI alloy revealed the strengthening phases. The thermodynamic data revealed the formation of the strengthening phases with and without TVT after standard heat treatment. No pore formation and a better distribution of hardness were observed in EBW welds compared to MIG welds.
Disclaimer: The views expressed here are those of the author expressed in their private capacity and do not necessarily represent the views of AZoM.com Limited T/A AZoNetwork the owner and operator of this website. This disclaimer forms part of the Terms and conditions of use of this website.
Source:
Olshanskaya, T.; Fedoseeva, E. Porosity Formation in Thin Welded Joints of Al–MG–LI Alloys. Materials 2022, 15, 348. https://www.mdpi.com/1996-1944/15/1/348