A team of researchers recently published a paper in the journal Materials that demonstrated the effects of heat treatment on the microstructure, mechanical properties, and residual stress of Invar alloys.
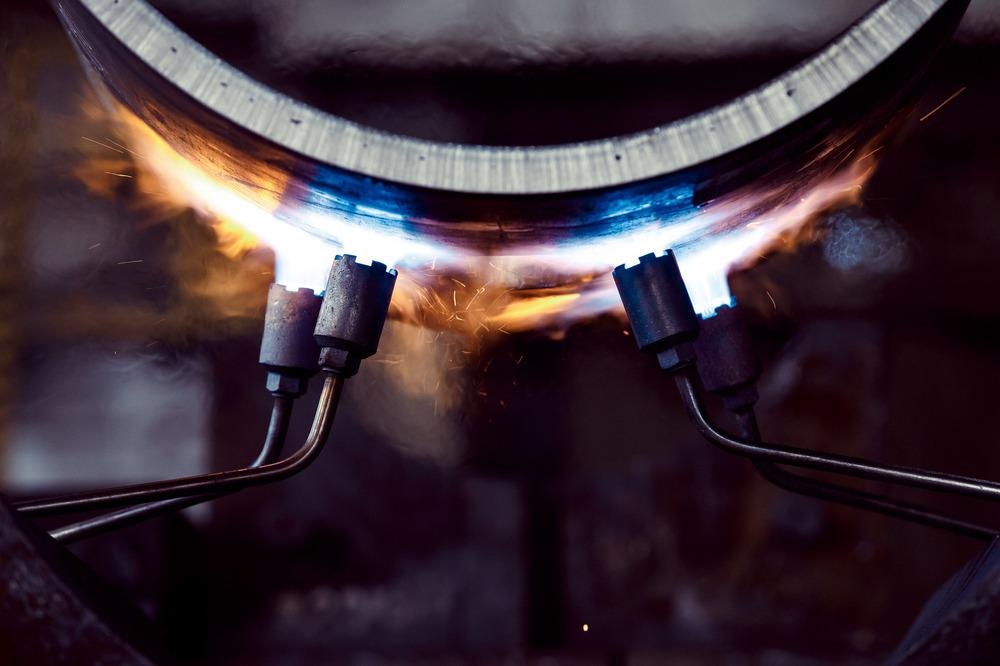
Study: Evolution of Microstructure, Mechanical Properties and Residual Stress of a Cold Rolled Invar Sheet Due to Heat Treatment. Image Credit: Picture Industry/Shutterstock.com
Invar alloy is mostly used in fine metal masks (FMMs) for its exceptionally low coefficient of thermal expansion. During the production of fine metal masks, residual stress develops in the Invar alloys during the cold-rolling of alloys. In order to effectively control the residual stress, heat treatment is typically applied to the Invar alloys after cold rolling.
Significance of Invar Alloys
The development of high-resolution displays is becoming increasingly important for computer monitors, smart device displays, and larger television screens. RGB pixels determine the resolution of the display units. In the OLEDs, the pixels are arranged using an evaporation process where the FMMs ensure that every pixel is positioned appropriately. In order to execute the task, FMMs require materials such as Invar alloys that are thermally stable and well patterned. These alloys are also required to match the thickness (in the range of microns) of the FMMs.
Normal direction inverse pole figure (IPF) map of the (a) cold-rolled, (b) 400 °C, (c) 500 °C, (d) 700 °C, (e) 800 °C, and (f) 900 °C heat treated specimens. Image Credit: Park, S.J. et al., Metals
The target thickness of the alloys for the FMMs is achieved by either cold rolling or electroplating. Between the two methods, cold rolling is used more extensively, as the method allows the mass production of metal sheets with homogenous chemical compositions and high strength. However, cold rolling leads to the development of residual stress in the Invar sheets, which must be eliminated in order to produce distortion-free high-quality FMMs.
Study Background
Heat treatment based on metallurgical processes such as recovery and recrystallization can remove the residual stress after cold rolling. However, some heat treatment can lead to unintended changes in the mechanical properties and microstructure of the alloy sheets, which is not desirable for high-strength sheets.
Thus, researchers in this study investigated the way by which the residual stress, the mechanical properties, and the microstructure of cold-rolled Invar alloys evolve after heat treatment in order to develop Invar sheets with high mechanical properties and low residual stress.
The Study
In the study, annealing was performed by placing the cold-rolled Invar alloys in a tube-type furnace with a thermocouple at 900 oC, 800 oC, 700 oC, 500 oC, and 400 oC temperatures for 35 s. However, the alloys were not heated for 35 s to the exact temperatures due to the need for short annealing. Subsequently, the annealed alloys were cooled to room temperature for analyzing and observing the changes in the mechanical properties, microstructure, and residual stress.
A servo-hydraulic universal testing machine was used for evaluating the mechanical properties of the Invar sheets. The strain rate of the tensile tests was 0.001/s, while the tensile specimens used in the tests conformed to the ASTM E8 standard specimen type.
Micro-/colloidal-polishing and grinding methods were used to prepare the specimens for microstructure characterization. The field emission scanning electron microscope (FE-SEM) with a step size of 0.66 microns and the electron backscattering diffraction (EBSD) technique were jointly used for the microstructure analysis.
Texture analysis was used for scanning multiple EBSD data, while the TSL OIM 7 software was used for post-processing the EBSD analysis results. X-ray diffraction (XRD) was used for performing residual stress measurements on the surfaces of the annealed and cold-rolled specimens. The Xtronic software was used for obtaining the residual stress values.
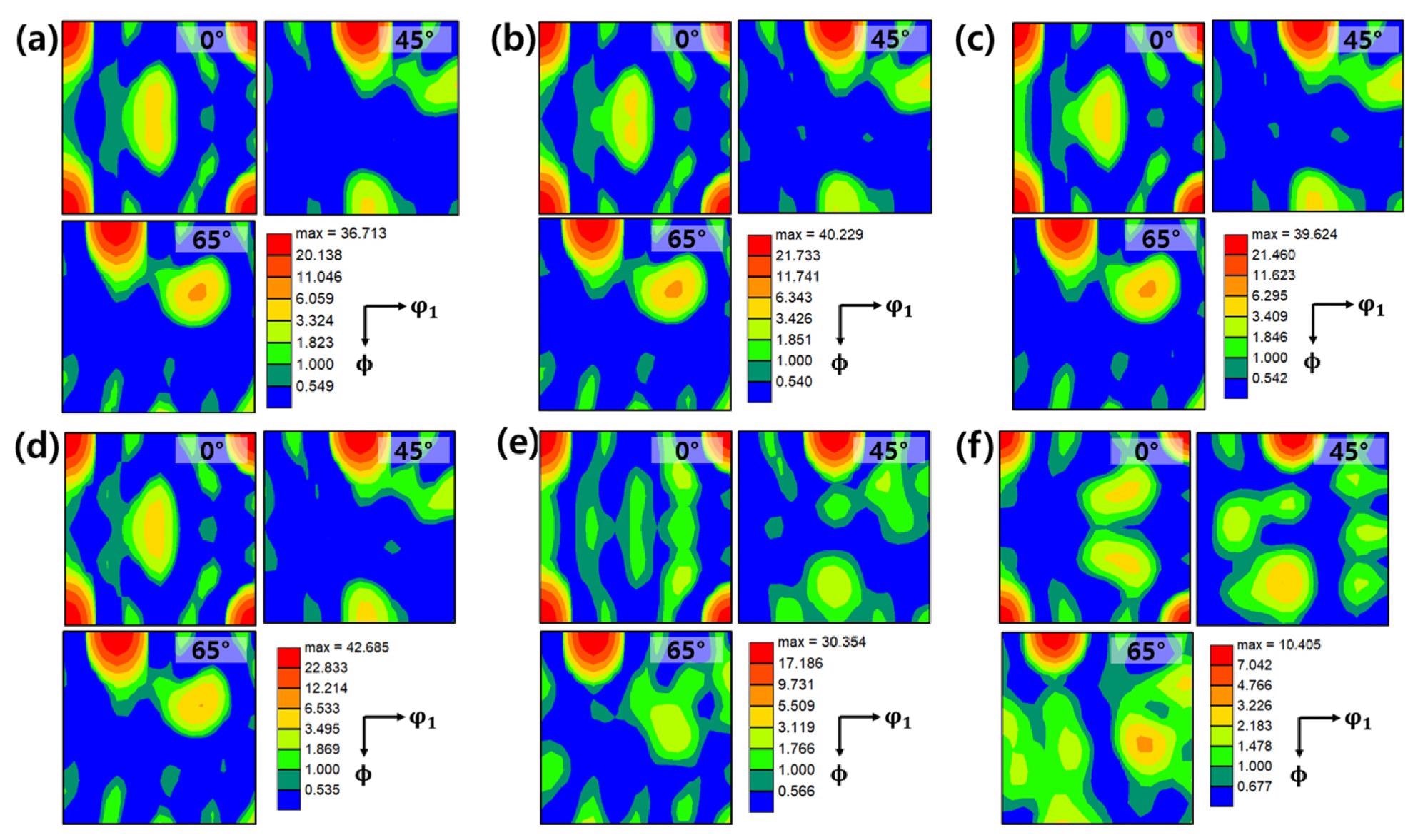
Orientation distribution function plot of the (a) cold-rolled, (b) 400 °C, (c) 500 °C, (d) 700 °C, (e) 800 °C, and (f) 900 °C heat-treated specimens. Image Credit: Park, S.J. et al., Metals
Observations
The initial thickness of the Invar alloy used in the study was 0.82 mm; it was reduced to 0.381 mm after the cold-rolling process. The observations from the microstructure analysis indicated that recrystallization started between 700 oC and 800 oC and was fully completed at 900 oC. After annealing the alloy at 700 oC, the strength of the alloy was reduced slightly, while the ductility was increased moderately.
The residual stress of the alloy showed no reduction at 400 oC and 500 oC owing to no recrystallization. The release of residual stress started at 700 oC and the stress was completely released after the full recrystallization and recovery of the alloys at 900 oC. Additionally, heterogeneously distributed low angle boundaries were observed in the microstructure, implying lower values of the residual stress.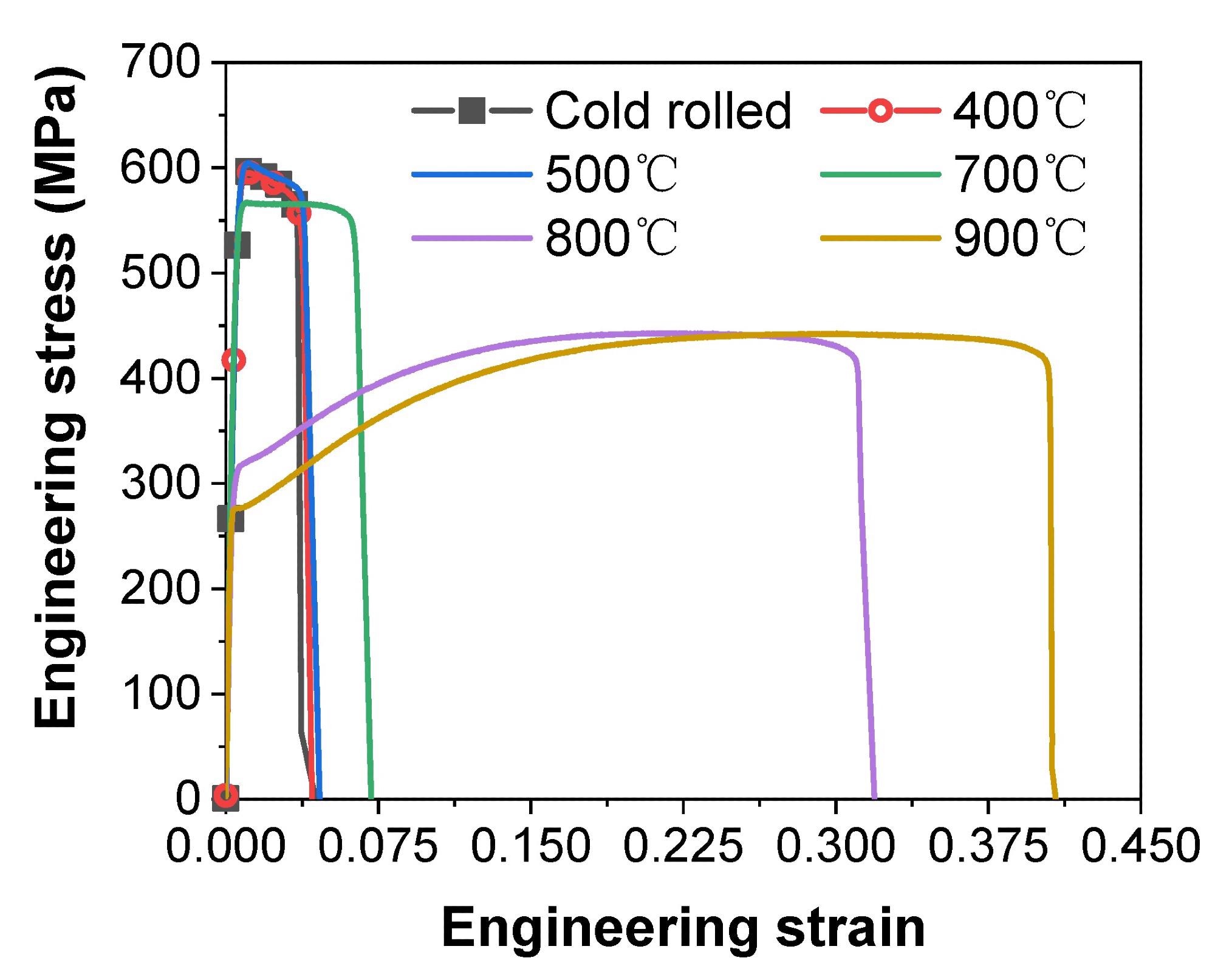
Stress strain curves of the specimens. Image Credit: Park, S.J. et al., Metals
Significance of the Study
The study demonstrated that recrystallization and recovery can effectively decrease the residual stress and substantially change the microstructure. Thus, if lowering the residual stress of the alloy sheets is more important than the strength, then recrystallization is sufficient for lowering the residual stress. The findings prove that recovery and recrystallization can help lower the residual stress of Invar sheets without degrading their mechanical properties.
Disclaimer: The views expressed here are those of the author expressed in their private capacity and do not necessarily represent the views of AZoM.com Limited T/A AZoNetwork the owner and operator of this website. This disclaimer forms part of the Terms and conditions of use of this website.
Source:
Park, S.J., Jo, S.-H., Kim, J.G. et al. Evolution of Microstructure, Mechanical Properties and Residual Stress of a Cold Rolled Invar Sheet Due to Heat Treatment. Metals 2022, 12, 110. https://www.mdpi.com/2075-4701/12/1/110