A novel study in the journal Metals focuses on the importance of bond strength as a significant factor for plasma-sprayed NiCrBSi thin films; the researchers have proposed a unique method reliant on total areas of interlayer pores.
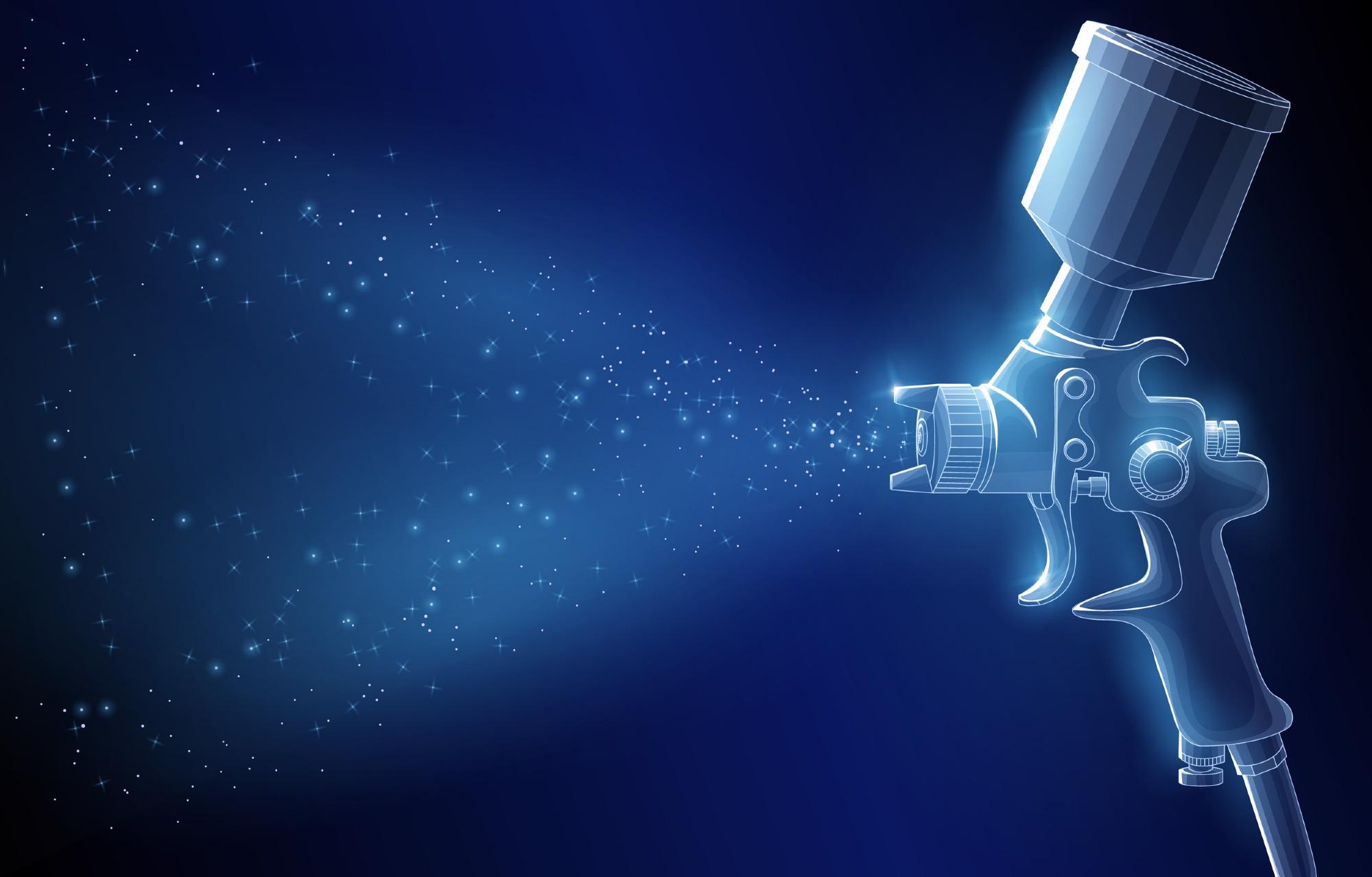
Study: A New Method for Evaluating the Bond Strength of Plasma-Sprayed NiCrBSi Coatings. Image Credit: Vitamin444/Shutterstock.com
Introduction to Surface Modification Techniques
Surface treatment makes it much easier to improve the surface characteristics of metals. Surface modification methods may be broadly categorized as those in which the exterior of a material can be employed as a constituent of a surface-modified coating, such as laser cladding, frictional stir refining, and micro-arc oxidizing. The second procedure is the one in which an external layer, such as thermal spraying, or chemical vapor deposition, is created or synthesized on the surface of the substrate.
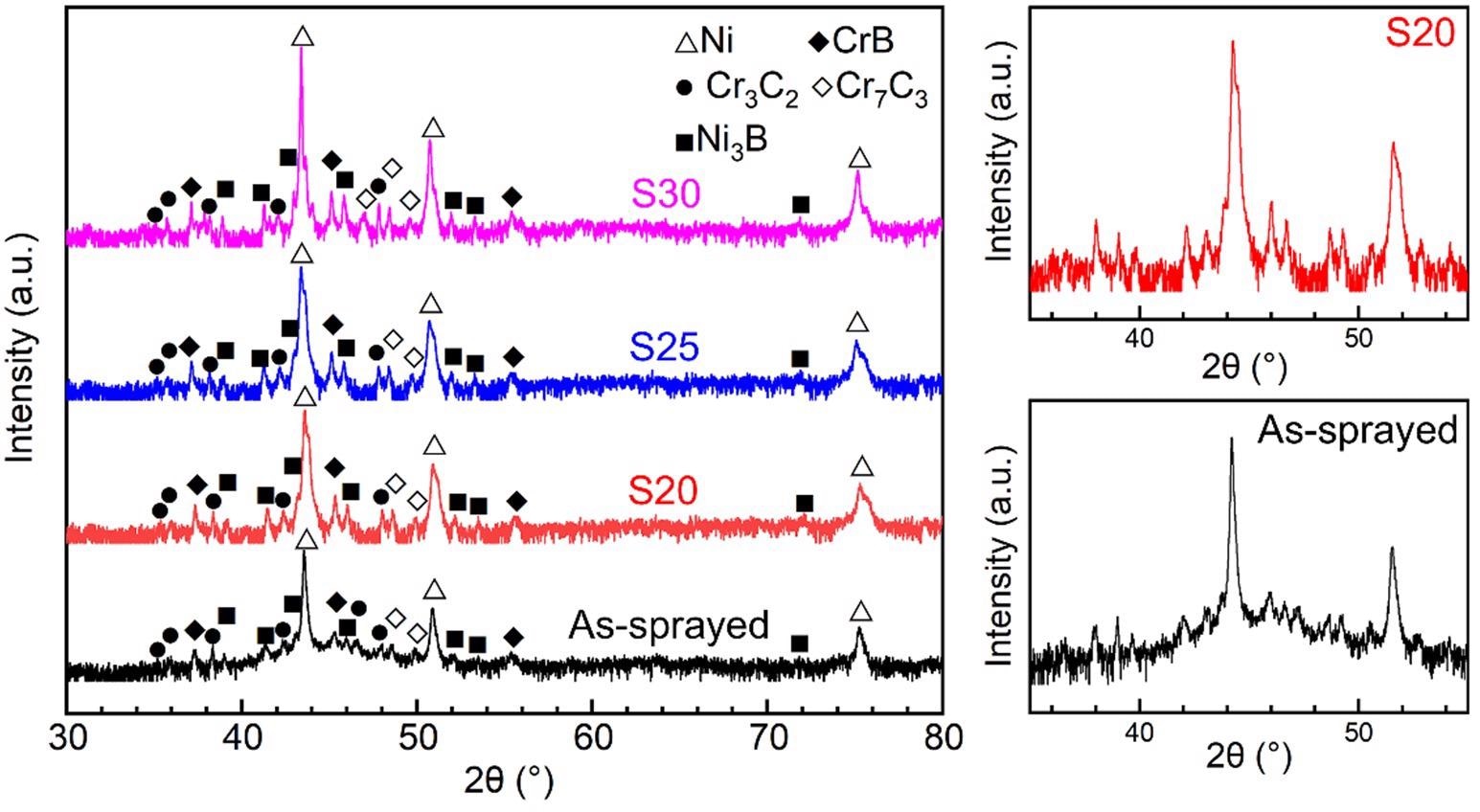
XRD patterns of all coating samples. The two figures on the right are the magnified view of the XRD patterns of the as-sprayed and S20 between 35° and 50°. S20, S25, and S30 indicate the as-sprayed NiCrBSi coatings remelted at 20 kW, 25 kW, and 30 kW. Image Credit: Chen, L.-Y. et al., Metals
Utilization of Thermal Spray Technology
Among the ways for creating the exterior layers, the thermal spray technique is extensively utilized. This approach employs metallic and/or ceramic particles as substrate and distributes the particles on a platform at high speeds and temperatures.
A high-speed conveying vapor ejects the material from the tip while concurrently heating it using heat supplies. The thermal spraying technique, which can quickly create coverings on the faces of weldments, has been used in numerous industrial industries. Thermal spraying technology is classified as plasma spraying technology, flame spraying technology, electric arc spraying technology, and high-velocity oxygen-fuel spraying technology based on the kind of heat resource.
Plasma Spraying Technique
The intensity of a plasma arc is greater than that of conventional heating systems. As a result, a broader variety of materials may be employed as fuel sources for plasma spraying technologies to prepare diverse coverings. Whatever biomasses are utilized, the bond strength between the manufactured layer and the substrate is a significant concern for the result in the plasma spraying technique.
Coatings with inadequate binding strength are susceptible to peeling away from the substrate, resulting in the product's nullification.
NiCrBSi Coatings and Bond Strength
The NiCrBSi metal covering is a common alloy covering used in compressors, cylinder shafts, and furnaces because the NiCrBSi alloy has great strength and wear resistance. There are primarily two techniques for assessing the bond strength of NiCrBSi films (including other plasma-sprayed films) published.
To make a tensile specimen, one cuts the covering with the foundation into a tube and glues it to some other metal cylinders with the same basal area. The tensile test is used to determine the binding capacity of a specimen after the glue has solidified.
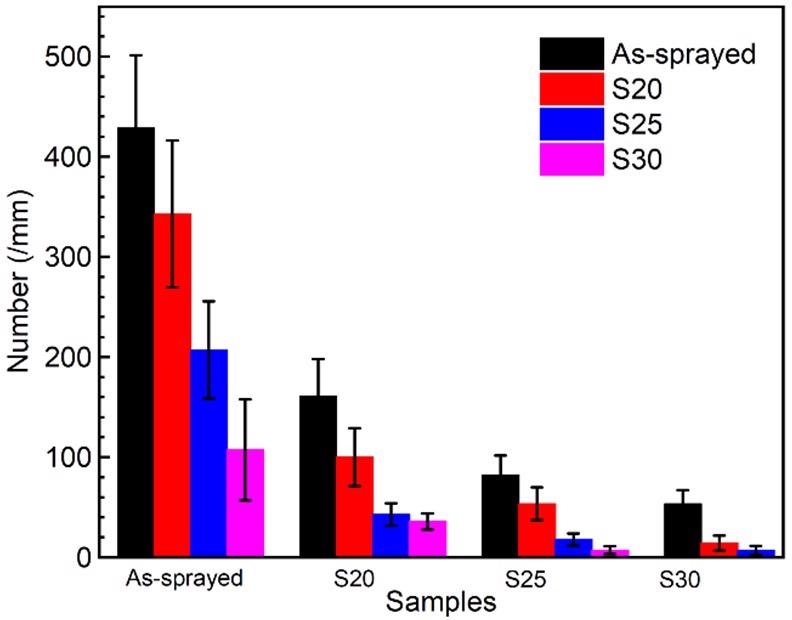
Size distribution of interfacial pores for the as-sprayed, S20, S25, and S30 samples. S20, S25, and S30 indicate the as-sprayed NiCrBSi coatings remelted at 20 kW, 25 kW, and 30 kW. Image Credit: Chen, L.-Y. et al., Metals
The binding toughness of the as-sprayed NiCrBSi layer is typically in the 1166 MPa region. The tensile modulus of the adhesive utilized is around 70 MPa. As a result, this procedure was commonly utilized in the past. However, as preparation processes (such as remelting and shell-core structural particle) have improved, the binding toughness of NiCrBSi coverings has surpassed 70 MPa.
In such a case, the binding strength of the NiCrBSi covering cannot be determined using the above-mentioned approach. As a result, for the tensile strength, a novel approach utilizing a particular dual tool has been devised.
Need for a New Method of Evaluating Bond Strength
In terms of NiCrBSi coating strength and durability generation, the gaps at the contact cannot generate any strength properties for the coating. The binding strength of the coating may be calculated using the microstructural properties of the coating contact described above.
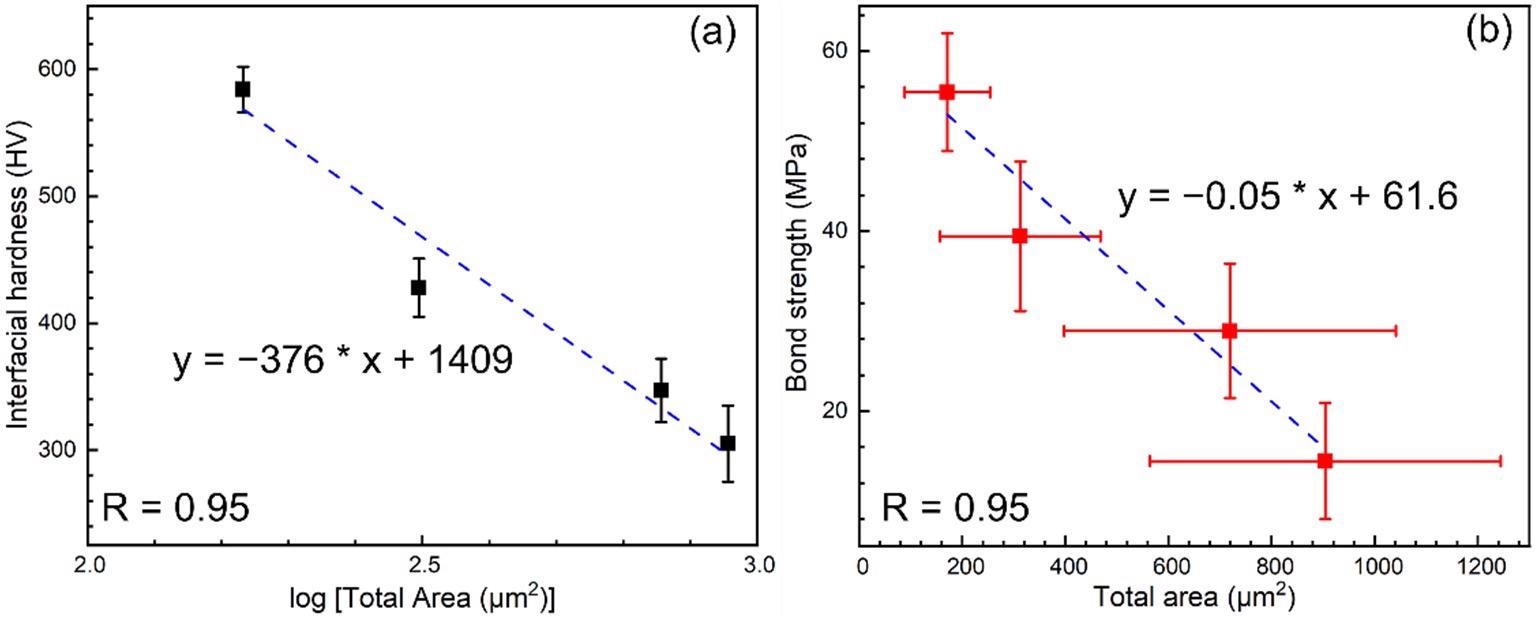
Relationship between the total areas of the coating samples and their mechanical properties: (a) interfacial hardness and (b) bond strength. Image Credit: Chen, L.-Y. et al., Metals
The coating is immediately synthesized on the dual instrument, and the tensile strength is then performed on the dual instruments with coverings. Although this technology can evaluate coatings with higher strength properties, the manufacture of a dual instrument is prohibitively expensive. Henceforth, a novel inexpensive method is needed immediately.
Research Findings
A substantial number of pores were observed upon microscopic examination of the specimen. Remelting is routinely used to enhance the characteristics of as-sprayed NiCrBSi coatings.
Without a doubt, the deposited NiCrBSi covering had the greatest total area of pores at the coating/substrate contact. After remelting, the overall area of perforations dropped considerably. The holes in coatings (as well as other materials) had a considerable impact on cohesiveness and hence toughness.
The pores, like the pores in polymeric media, limited their durability. The interface roughness of the material rose as the amount and total surface area of pores dropped. Meanwhile, the creation of the interfacial film aided in the improvement of hardness.
To summarize, the NiCrBSi coatings were produced on a 2Cr13 stainless steel substrate in this study. It was discovered that the surface capacity of contact porosity and contact hardness exhibited an essentially exponential distribution. The fitted findings may aid in predicting the bond strength of produced NiCrBSi coatings, and the approach described in this study may find wider use.
Further Reading
Chen, L.-Y.; Liu, Y.-T.; Xuan, H.-N.; Zhao, C.-H.; Bobrov, M.; Zang, Q.-H.; Peng, J.-H.; Lu, S.; Zhang, L.-C. A New Method for Evaluating the Bond Strength of Plasma-Sprayed NiCrBSi Coatings. Metals 2022. 12. 168. Available at: https://www.mdpi.com/2075-4701/12/2/168
Disclaimer: The views expressed here are those of the author expressed in their private capacity and do not necessarily represent the views of AZoM.com Limited T/A AZoNetwork the owner and operator of this website. This disclaimer forms part of the Terms and conditions of use of this website.