Researchers published their study in the journal Sustainability, which investigated the use of CHP systems in the textile industry.
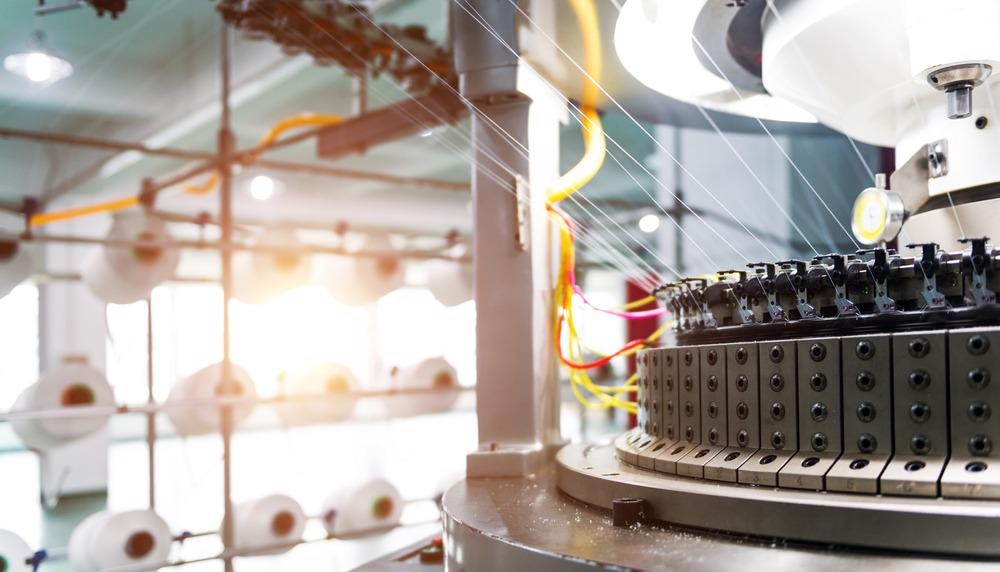
Study: Investigation and Optimization of the Performance of Energy Systems in the Textile Industry by Using CHP Systems. Image Credit: hxdbzxy/Shutterstock.com
Across all industries, energy-saving issues are taking center stage as there is a focus on reducing energy consumption to mitigate the impact the industrial sector has on energy consumption and subsequent emission of harmful greenhouse gasses including carbon dioxide (CO2).
According to a group of global researchers, led by Dr. Reza Alayi and Professor Mohsen Sharifpur Islamic Azad University, Iran and the University of Pretoria, South Africa, respectively, combined heat and power (CHP) would offer an efficient way to reduce energy consumption in various sectors.
“The combination of heat and electricity recovers heat energy lost during power generation, unlike conventional systems where heat is simply transferred to the environment,” explains Alayi. Thus, finding a system that suitably offers a way to reduce energy waste in the industry could also help reduce costs and overall fuel consumption.
The textile industry retains a record as the lowest efficiency in energy utilization and is one of the main energy-consuming industries.
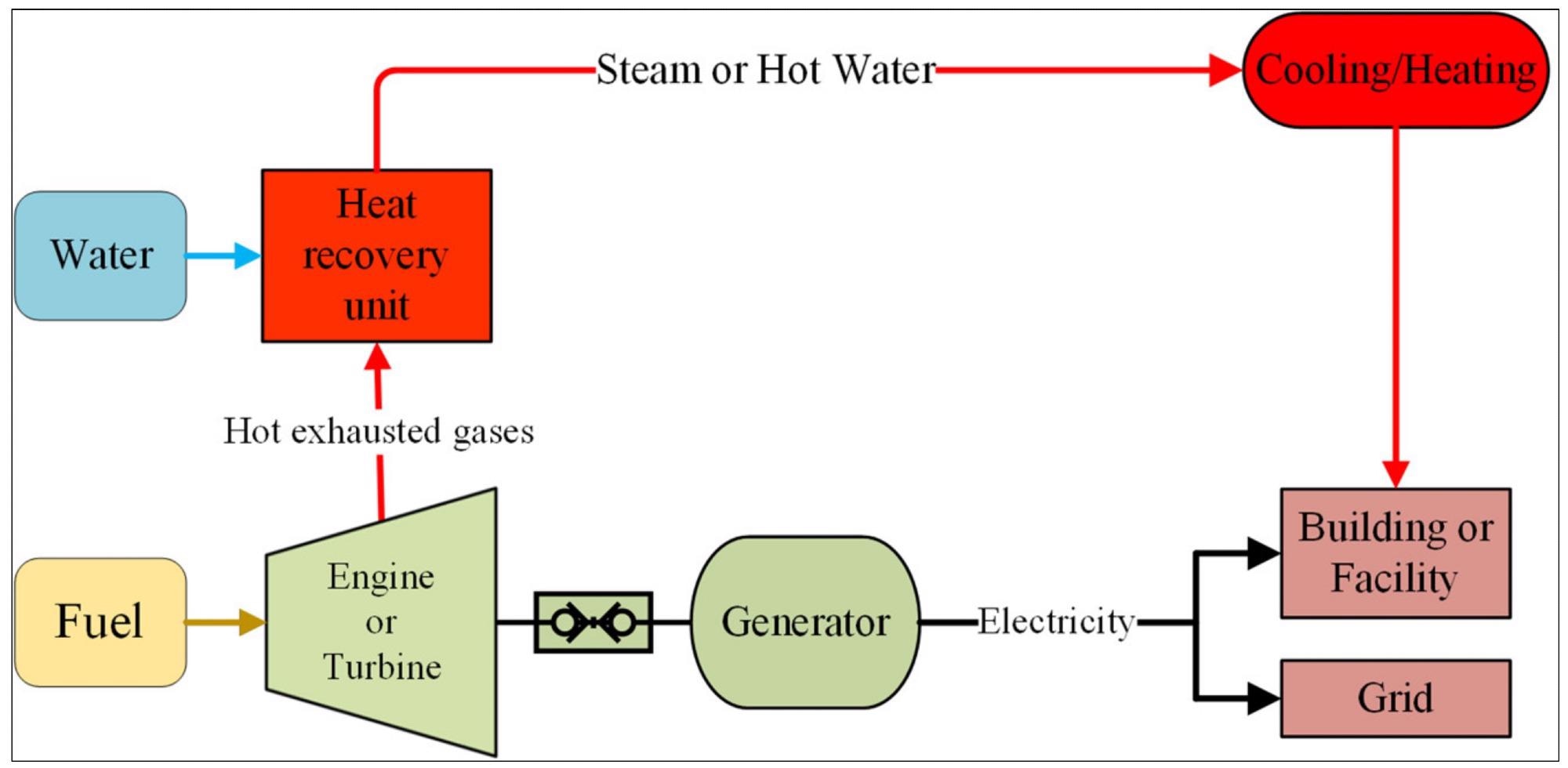
The proposed combined heat and power (CHP) system. Image Credit: Victorovna M et al., Sustainability
Optimization of CHP systems in the textile industry is therefore considered to be an important issue as one of the main energy consumers of the industrial sector. “CHP systems have an efficiency rating of 50–90%, and, due to the proximity of the generator and the consumer, have fewer losses in the process of transmission and distribution of electricity and heat,” says Alayi.
Across the entire textile industry, energy is consumed in a variety of ways at all stages of the production process. Steam is used in each of the various stages, particularly in the areas of dyeing, printing, and finishing (wet processes).
It is, therefore, vitally important that researchers develop new technologies to optimize traditional industrial processes in order to conserve energy by incorporating innovative systems with good efficiency ratings.
CHP
Combined heat and power (CHP) systems are characterized by the simultaneous reduction of useful heat and electricity from the same energy source. Due to the fact that the heat is delivered as a product, these systems are deemed energy efficient and can be used to deliver electricity and heat to commercial and residential buildings and complexes.
![Energy balance in the combustion chamber [4].](https://d12oja0ew7x0i8.cloudfront.net/images/news/ImageForNews_58086_16437193972321575.jpg)
Energy balance in the combustion chamber. Image Credit: Victorovna M et al., Sustainability
However, when the energy and heat are transferred, a large amount of this can be wasted. Therefore it is crucial that CHP power plants are located close to the target users for efficient energy consumption. Industrial power plants are seen to be ideal for such facilities as they require a constant source of electricity and heat and minimize any loss in energy transfer.
“The goal [of the study] is to establish the optimal location of the turbine by considering various economic and energy factors. In this regard, the effect of different turbine locations on fuel consumption and system efficiency has been evaluated,” explains Sharifpur.
The researchers propose a gas turbine model which utilizes natural gases as a fuel that can be used to produce both electricity and heat, with the inclusion of a heat recovery system that recaptures exhausted gases.
The team then set about modeling a number of desired scenarios with regard to fuel, turbine, and boiler locations. They found the most effective turbine location to be in the path of steam boilers to generate electricity: “after generating electricity, it will provide the amount of energy required by these boilers, explained Sharifpur.
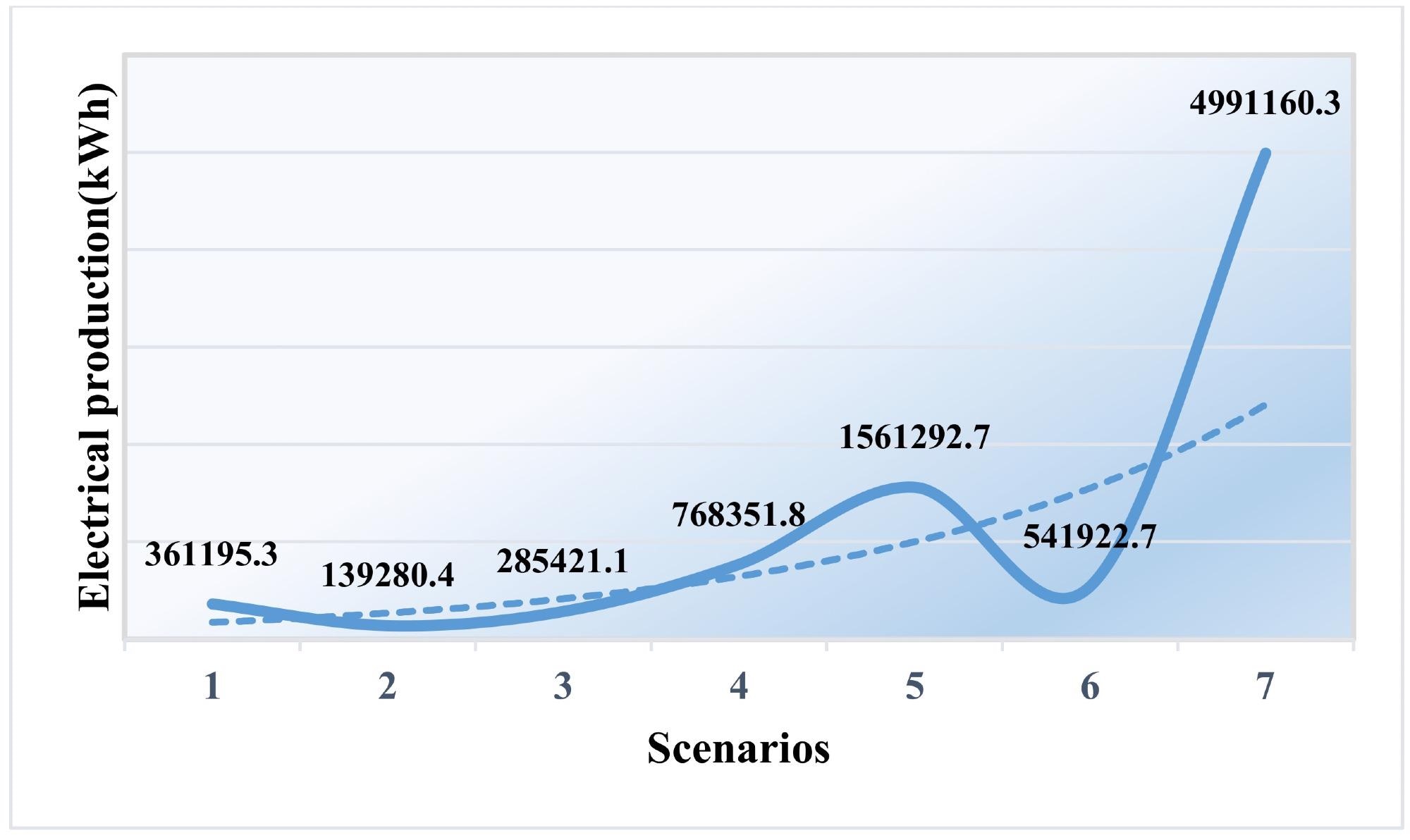
The amount of electricity generated by the scenarios. Image Credit: Victorovna M et al., Sustainability
While the optimal scenario did generate the requisite amount of electricity and heat, it did consume the most energy (gas); however, due to the exceptional reliability of the desired assembly, it would also be the most profitable. Overall, this scenario would optimize the CHP system and potentially offer the best energy efficiency in the long term due to the amount of power generated.
While more work is required to identify other factors such as thermal waste and further environmental analysis, the study identifies energy-efficient CHP systems that could optimize energy consumption in the textile industry. This is particularly important where fossil fuels are still used as an energy source as limiting pollution problems will offer considerable advantages including energy management, cost, and investment reduction, and most importantly improving the environmental impact.
References
Victorovna Morozova, Tatiana, Reza Alayi, John W. Grimaldo Guerrero, Mohsen Sharifpur, and Yaser Ebazadeh. 2022. "Investigation and Optimization of the Performance of Energy Systems in the Textile Industry by Using CHP Systems" Sustainability 14, no. 3: 1551. https://www.mdpi.com/2071-1050/14/3/1551
Disclaimer: The views expressed here are those of the author expressed in their private capacity and do not necessarily represent the views of AZoM.com Limited T/A AZoNetwork the owner and operator of this website. This disclaimer forms part of the Terms and conditions of use of this website.