The latest article in the journal Frontiers in Energy Research proposes a revolutionary immersion cooling method that uses water as a coolant fluid and employs a particular seal construction intended to avoid the interface between water and the battery's electrodes.
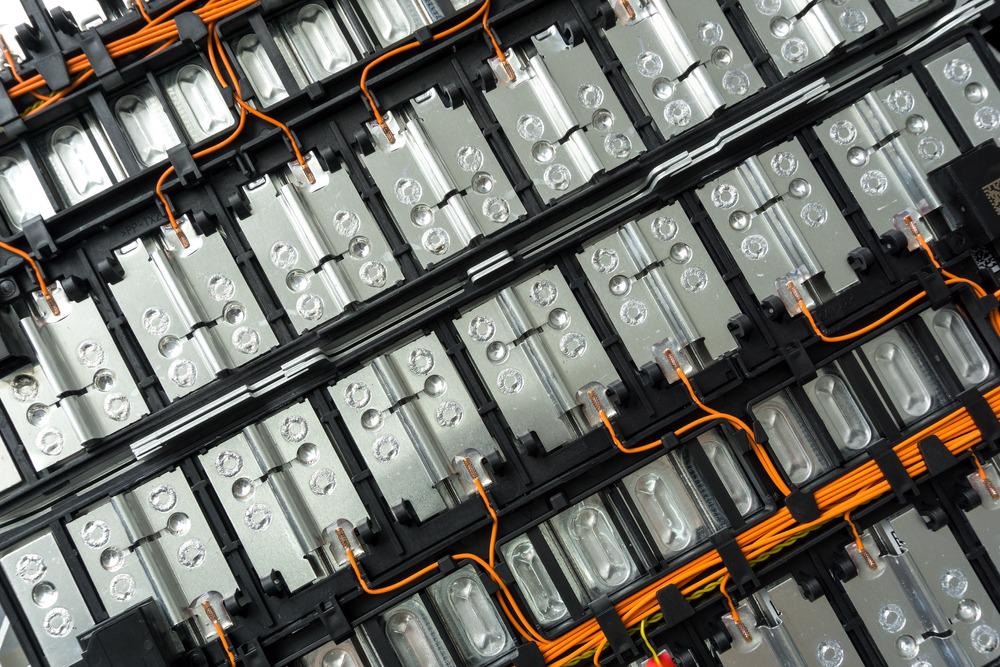
Study: Experimental and Simulative Investigations on a Water Immersion Cooling System for Cylindrical Battery Cells. Image Credit: Smile Fight/Shutterstock.com
Need for Thermal Management Systems for Batteries
The adoption and advancement of electric cars is a critical component in achieving global carbon neutrality. The lithium-ion battery is one of the significant power sources of electric cars and one of the major components of electric vehicles, hence its development is critical. Temperature, on the other hand, has a significant impact on power efficiency. Utilizing lithium batteries at high or low temperatures reduces their efficiency and longevity.
Excessive heat or a lack of temperature consistency may cause the rechargeable battery to thermally run away, culminating in burning or exploding. As a result, an efficient thermal management system is required to keep the batteries within a suitable working temperature range.
Battery test system (A) and the structure of the single-battery pack (B). Image Credit: Luo, M. et al., Frontiers in Energy Research
Types of Thermal Management Systems
Rechargeable batteries temperature control systems are classified into active thermal management and passive thermal management systems based on their cooling method. Both of these methods differ in their functionalities and cooling mechanisms along with possessing inherent advantages and disadvantages.
Advantages and Limitations of Active Thermal System
Active thermal management cools the batteries by eliminating the heat from them via a medium like air or liquid. These frameworks can efficiently and constantly cool the batteries, which have high dependability and are extensively utilized in many electric cars (EVs). Although, they have complicated architecture and necessitate the use of mechanical equipment such as pumps or fans.
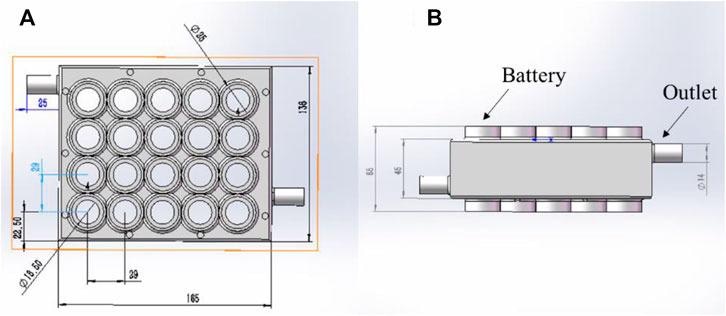
The structure of the 5s4p battery pack: (A) planform; (B) side view. Image Credit: Luo, M. et al., Frontiers in Energy Research
Are Passive Thermal Systems the Best Choice?
Passive cooling systems depend on energy storage devices such as phase change materials (PCMs) to capture and reduce the heat produced by the battery. These passive cooling systems use no energy and do not require any mechanical devices.
They also have the benefits of being small, inexpensive in cost, and noiseless. On the flipside, passively cooling solutions will be rendered ineffective if the heat reserved in PCM cannot be dissipated promptly. When coupled with active cooling, the energy absorbed by the PCM may be swiftly dissipated, considerably improving cooling system operational dependability. As a result, the thermal management approach with liquid cooling and PCM cooling offers the benefits of superior cooling and temperature uniformity.
However, when the battery is discharged/charged at a high pace, these indirectly operated cooling systems may not be able to provide the cooling requirements.
Introduction to Immersive Cooling (Direct Cooling)
For conditioning, direct liquid cooling (immersion cooling) employs a liquid such as mineral oil or silicone oil in close interaction with the lithium batteries. The battery cells are submerged or partly submerged in the cooling liquid, which considerably minimizes the interface thermal performance and improves system cooling.
When contrasted to the indirect cooling system, the immersed cooling system may decrease the heat of the battery pack by 9.3 percent. Furthermore, immersion cooling mechanisms are more compact since they do not require elaborate cooling ducts or cold panels. In the future, it may have a high application value in the case of a high discharge rate or fast-charge battery.
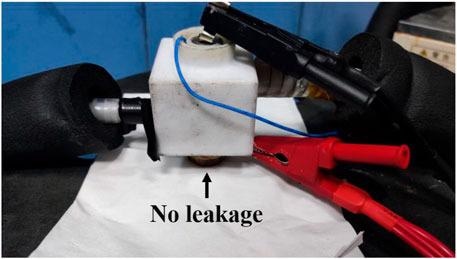
Schematic diagram of water immersion cooling system and leakage test. Image Credit: Luo, M. et al., Frontiers in Energy Research
Limitations of Immersive Technology
To minimize battery sparking, conventional immersion systems frequently employ a liquid coolant. However, dielectric fluids like mineral oil or silicone oil are very viscous, increasing system energy consumption. Furthermore, the dielectric fluids' low heat capacity reduces the cooling efficacy of the systems. Water is a great cooling medium because of its high thermal conductivity and low viscosity. The most recent study proposes an immersion system with water as a cooling agent.
Research Findings
The experimental findings demonstrate that even with a modest flow rate, this water immersion refrigeration system can provide an outstanding cooling effect. Furthermore, testing results reveal that the immersion cooling system construction efficiently prevents water leakage and may be utilized for submerged cooling of cylinder batteries. When the depletion rate increased, the battery generated greater heat. As the battery temperature rose, the cooling water absorbed more heat, causing the water's exit temperature to rise.
Even if the battery pack is depleted at a 3 C rate, a small water flow rate (200 ml/min) can keep the maximum temperature of the battery pack below 50 °C. Furthermore, by including a buffer structure at the inlet/outlet, the detrimental impacts of turbulent flow can be mitigated.
In short, the system proved to be quite efficient and could pave the way for future applications.
Further Reading
Luo, M. et al., 2022. Experimental and Simulative Investigations on a Water Immersion Cooling System for Cylindrical Battery Cells. Frontiers in Energy Research. Available at: https://www.frontiersin.org/articles/10.3389/fenrg.2022.803882/full
Disclaimer: The views expressed here are those of the author expressed in their private capacity and do not necessarily represent the views of AZoM.com Limited T/A AZoNetwork the owner and operator of this website. This disclaimer forms part of the Terms and conditions of use of this website.