As recently as 2020, the global market for rechargeable Lithium-Ion Batteries (LIBs) was valued at approximately USD 40.5 billion, anticipated to increase to around USD 92 billion by 2026 – driven in part by the increased adoption of electric vehicles and the central role of rechargeable batteries in renewable energy production.
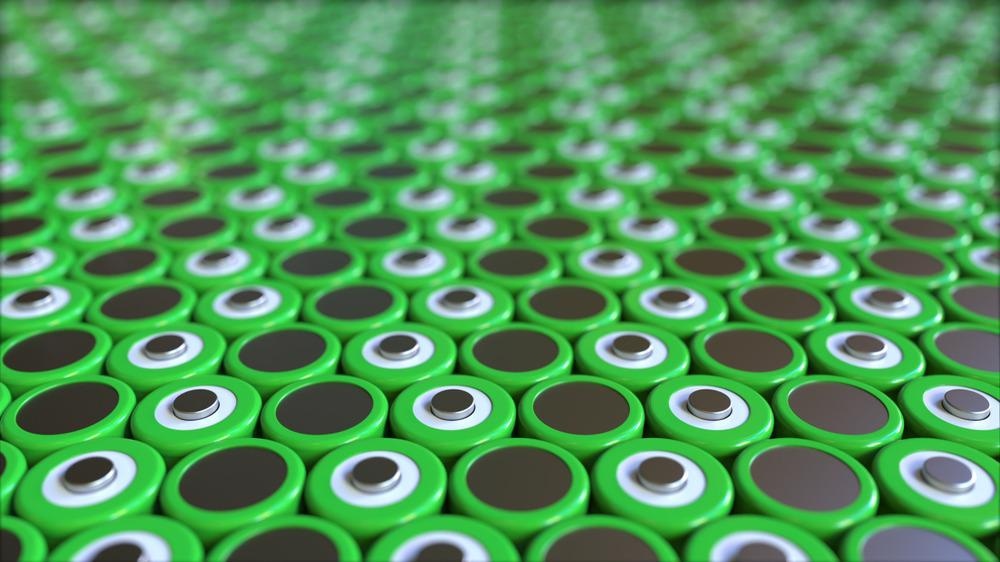
Study: Synthesis and Recyclability of Sheet-like Cobalt Carbonate Recovered from Spent Li-Ion Batteries Using a Simple Hydrometallurgy Process. Image Credit: Novikov Aleksey/Shutterstock.com
Most of these LIBs have a viable working life of between 1 and 3 years, resulting in vast amounts of end-of-life LIBs entering the waste stream annually.
To help alleviate this problem, a new paper presented in the journal Sustainability explores a simple hydrometallurgy process for recovering and recycling valuable cobalt from the spent lithium cobalt oxide (LiCoO2) found in lithium-ion batteries.
Recycled cobalt from spent LIBs’ cathode materials has the potential to be employed in the production of further batteries, or as a cobalt precursor in a range of other applications.
Flow-sheet of the black material (BM) extraction process. Image Credit: Aboulaich A et al., Sustainability
As well as the economic benefits of re-using this high-value material, there are significant environmental benefits due to the sheer number of risks presented by spent LIBs, such as organic solvents, harmful inorganic compounds, and toxic metals entering local ecosystems and harming plant and animal life.
The paper’s authors turned to hydrometallurgy as a potential option for the environmentally friendly, cost-effective, and scalable recycling of substantial quantities of spent LIBs, with a view to reducing the number of these entering the waste stream.
More from AZoM: A to Z of Lithium-Ion Battery Recycling
Hydrometallurgy is widely recognized as a cost-effective recycling process that has the advantage of comparatively low energy consumption versus other recycling processes, low gas emissions, good product purity, and improved metal recovery rates.
This conventionally involves an acid leaching process, a purification step, and a metal separation step, the latter performed by solvent extraction or selective precipitation.
Acid leaching is done by dissolving the battery’s cathode active materials, following a mechanical treatment step using inorganic acids – most typically HCI, H3PO4, and HNO3. H2O2 is also employed as a reducing agent, allowing the conversion of Co3+ to acid-soluble Co2+ ions.
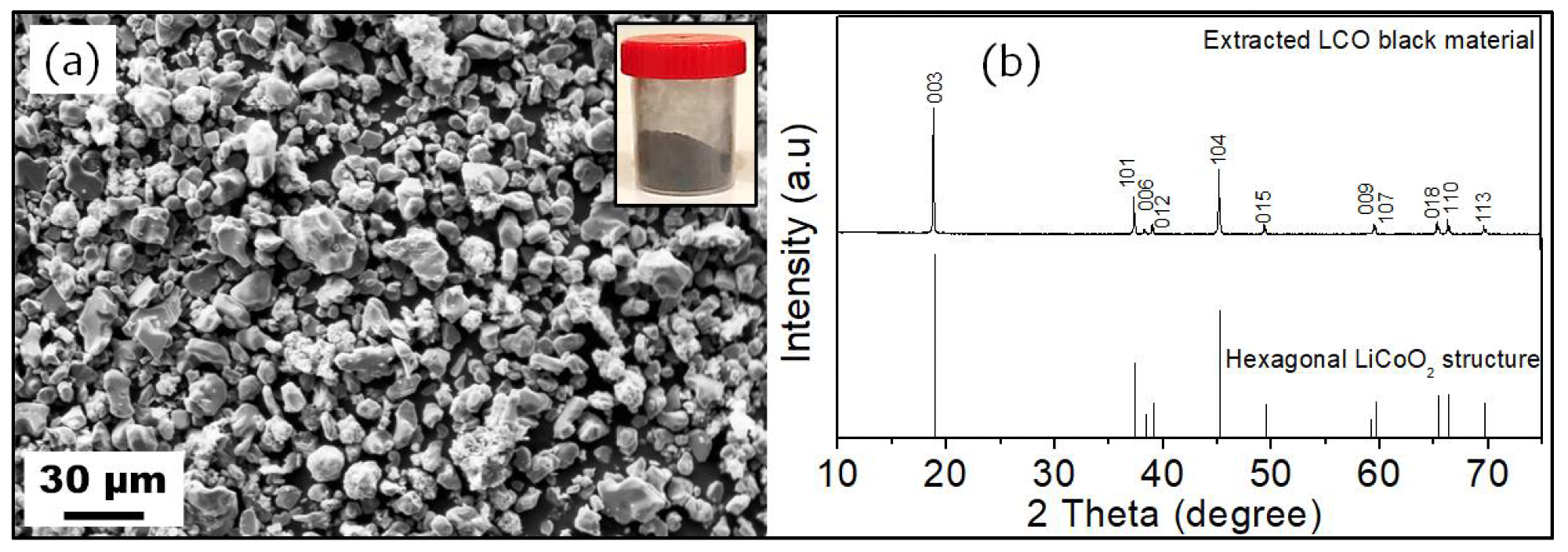
SEM image (a) and XRD pattern (b) of the extracted BM. The inset of figure (a) is a digital photograph of the extracted BM. Image Credit: Aboulaich A et al., Sustainability
The downside of this step, however, is that these inorganic acids are, themselves, environmentally damaging, negating any positive environmental impact of the recycling process.
Once the removal of metal impurities dissolved at the leaching step is complete, a solvent extraction method is used. This sees the purified leaching solution mixed with an organic extractant solution – a solution that is selected according to the metal of interest so only this is separated from the aqueous solution and transferred to the organic phase. The disadvantage of this step lies in the need to employ expensive and generally toxic organic chemicals as part of complex, time-consuming experimental procedures.
The paper’s authors cite chemical precipitation as a potential alternative to solvent extraction. This method involves the selective precipitation of a metal of interest via the use of a precipitating agent design to adjust the pH of the leaching solution. This method is considered to be more straightforward, scalable, and environmentally friendly than the solvent extraction method.
Recovery of cobalt to Co(OH)2 is generally acheived using NaOH as the precipitating agent, while Na2CO3 is used to precipitate Li+ as Li2CO3.
In order to demonstrate the viability of this method in the recovery of cobalt from LIBs, the paper’s authors used a precipitation process with sheet-like CoCO3 crystals from an acid-leaching solution containing Co2+ and Li+ ions. Their goal was to convert the sheet-like CoCO3 to a flower-like LiCoO2 active material that is appropriate for reuse in LIBs.
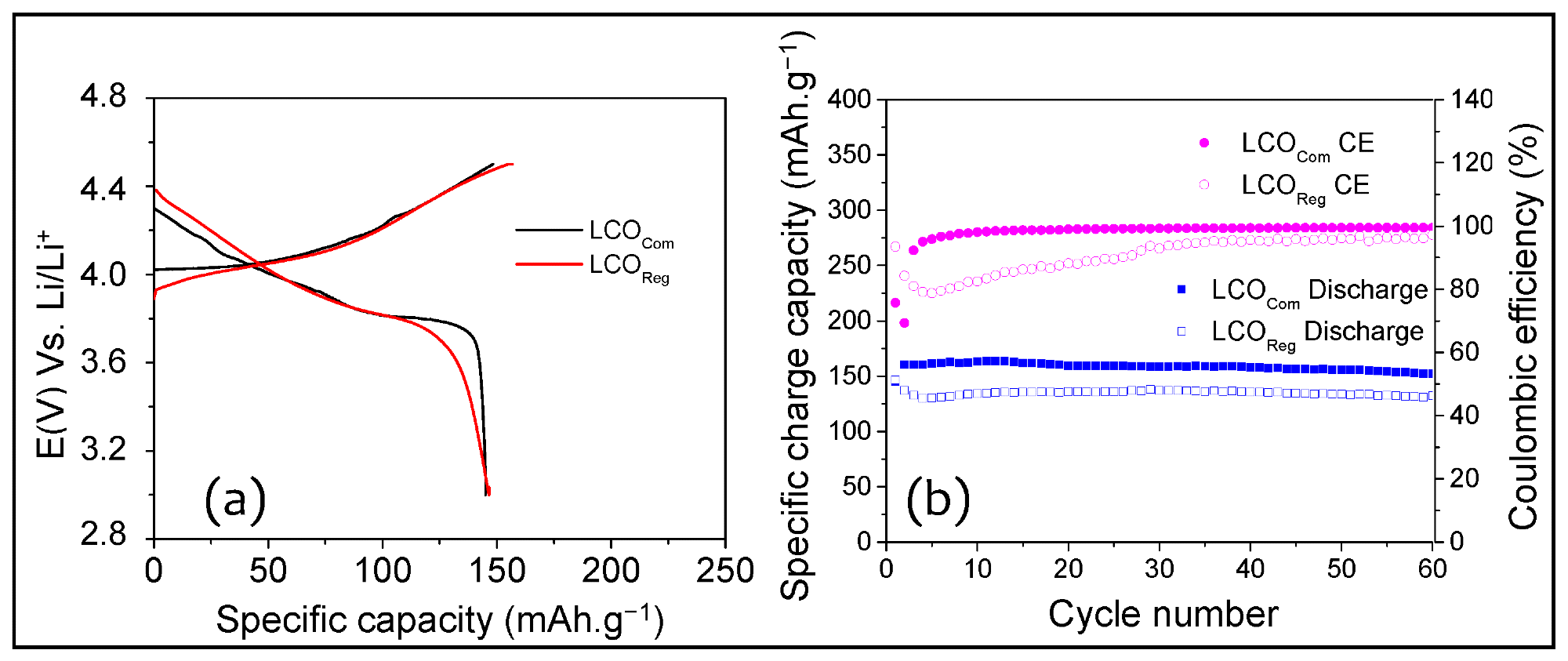
First charge/discharge curve (a), cycling performance and coulombic efficiency (CE) (b) of LCOReg and LCOCom cathodes in Li-ion half-cells. Image Credit: Aboulaich A et al., Sustainability
Having undertaken this conversion process, the paper’s authors then studied and compared the performance of the resulting lithium cobalt oxide against lithium cobalt oxide that had been created from commercially available cobalt/lithium precursors.
Most notably, their revised method was determined to yield a high-grade CoCO3 (48.2% Co, w/w) that contained just 0.18% Li, making this product ideal for reuse in the creation of new lithium cobalt oxide cathode material. This recovered CoCO3 was also determined to be able to regenerate lithium cobalt oxide powder with a flower-like morphology via a solid-state reaction using Li2CO3 as the Li precursor.
It was also observed that the regenerated lithium cobalt oxide cathode displayed an initial discharge capacity that was comparable to lithium cobalt oxide prepared from the commercially cobalt/lithium precursors, retaining 90% capacity at the 60th cycle.
These findings could lead to the development of optimized and highly scalable approaches to LIB recycling that are not only economically attractive – a key consideration, given rises in cobalt prices – but also highly beneficial from an environmental perspective.
References
Aboulaich A, Yaden A, Elhalya N, Tayoury M, Aqil M, Hdidou L, Dahbi M, Alami J. Synthesis and Recyclability of Sheet-like Cobalt Carbonate Recovered from Spent Li-Ion Batteries Using a Simple Hydrometallurgy Process. Sustainability. 2022; 14(5):2552. https://www.mdpi.com/2071-1050/14/5/2552
Disclaimer: The views expressed here are those of the author expressed in their private capacity and do not necessarily represent the views of AZoM.com Limited T/A AZoNetwork the owner and operator of this website. This disclaimer forms part of the Terms and conditions of use of this website.