By Surbhi JainReviewed by Susha Cheriyedath, M.Sc.Mar 2 2022
In an article recently published in the open-access journal Materials, the researchers presented a detailed discussion regarding the shock imprinting technique using polymer molds through a combination of numerical analysis and experimental research.
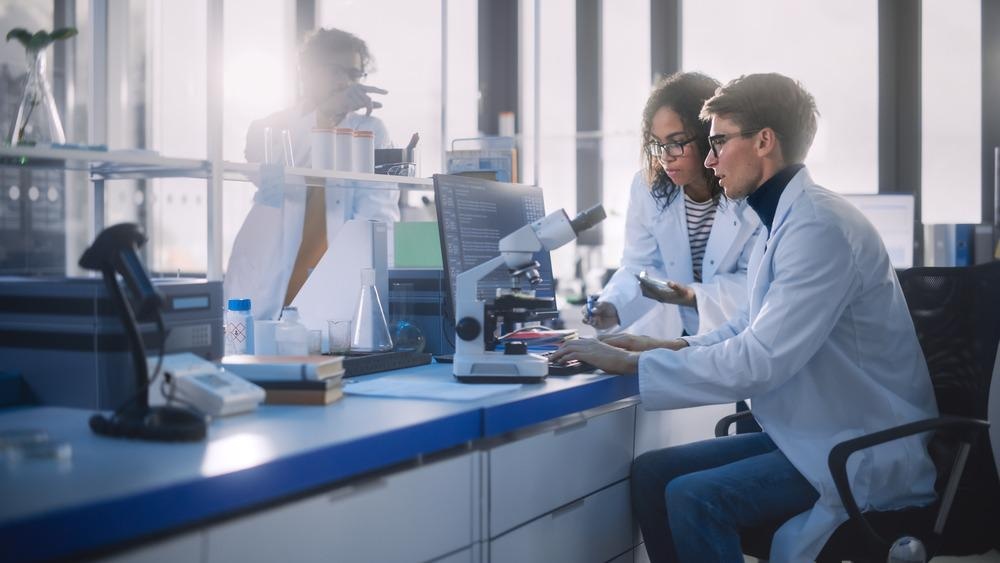
Study: Toward a Better Understanding of Shock Imprinting with Polymer Molds Using a Combination of Numerical Analysis and Experimental Research. Image Credit: Gorodenkoff/Shutterstock.com
Background
Nanostructures on metal surfaces have different electrical properties depending on their size and form. Surface plasmons, for example, produce high local electric fields in gold, silver, and copper nanostructures with nanogaps, which are beneficial for ultra-trace investigation in Raman spectroscopy due to signal augmentation.
Metal nanostructures, in addition to semiconductors, could be a new choice for solar cells. However, the inability of such structures to be mass-produced is a fundamental barrier to their practical deployment.
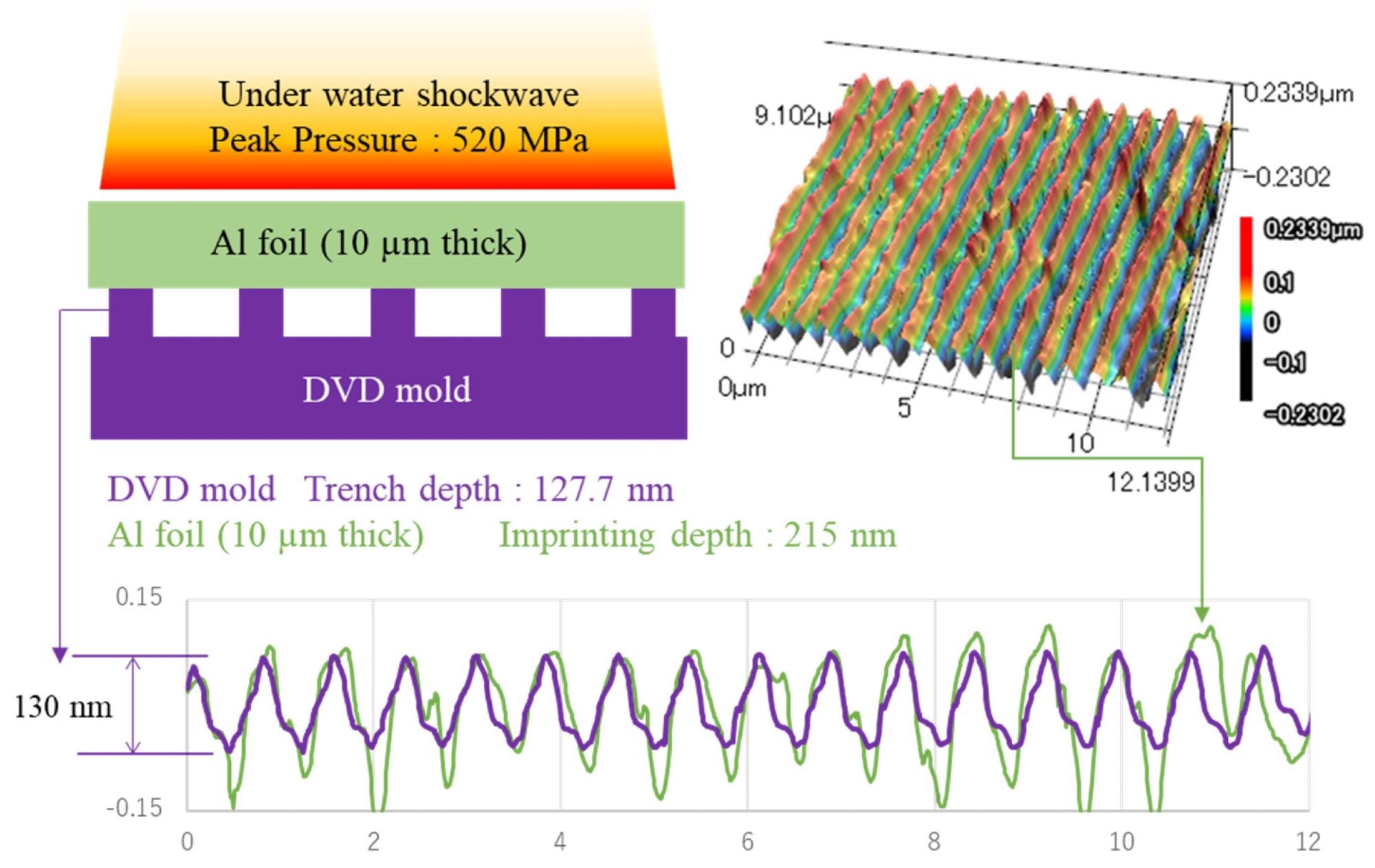
Imprint experiment: an Al foil was compressed into a DVD mold by an underwater shock wave derived from an explosive, yielding a deeper imprinting shape than the DVD mold. Image Credit: Hasegawa, K et al., Materials
With the invention of soft lithography, research on the use of low-cost polymer molds in the laser shock-imprinting (LSI) process was introduced, resulting in enhanced mass production by sacrificing imprinting accuracy for reduced costs.
Underwater shock waves created from explosives have evolved as an innovative method to shock-imprinting technology. Furthermore, shock waves generated by explosives allow deeper imprinting than molds, substantially facilitating the use of this technology in mass production.
About the Study
In the present study, the authors discussed the explosive-induced shock waves and their lasting duration in comparison to laser-induced shock waves. To determine the reason for the deep impression, numerical analysis and a series of simplified molding experiments were performed. The pressure history and deformation behavior of the workpiece and mold were approximated by the numerical analysis.
The factors that contribute to the appearance of deep imprinting were investigated in this study. To generate specimens for comparison with numerical analysis and minimize difficulties owing to the variability of the starting material, sub-millimeter-order molding tests were performed on aluminum (Al) workpieces utilizing explosive-derived underwater shock waves and polycarbonate (PC) molds.
Using existing equations of state and constitutive laws, the explosive, pressure transmitting medium (water), Al workpiece, and PC mold were numerically modeled. During the shock compression process, the dynamic behavior of the metal workpiece and the mold were also investigated.
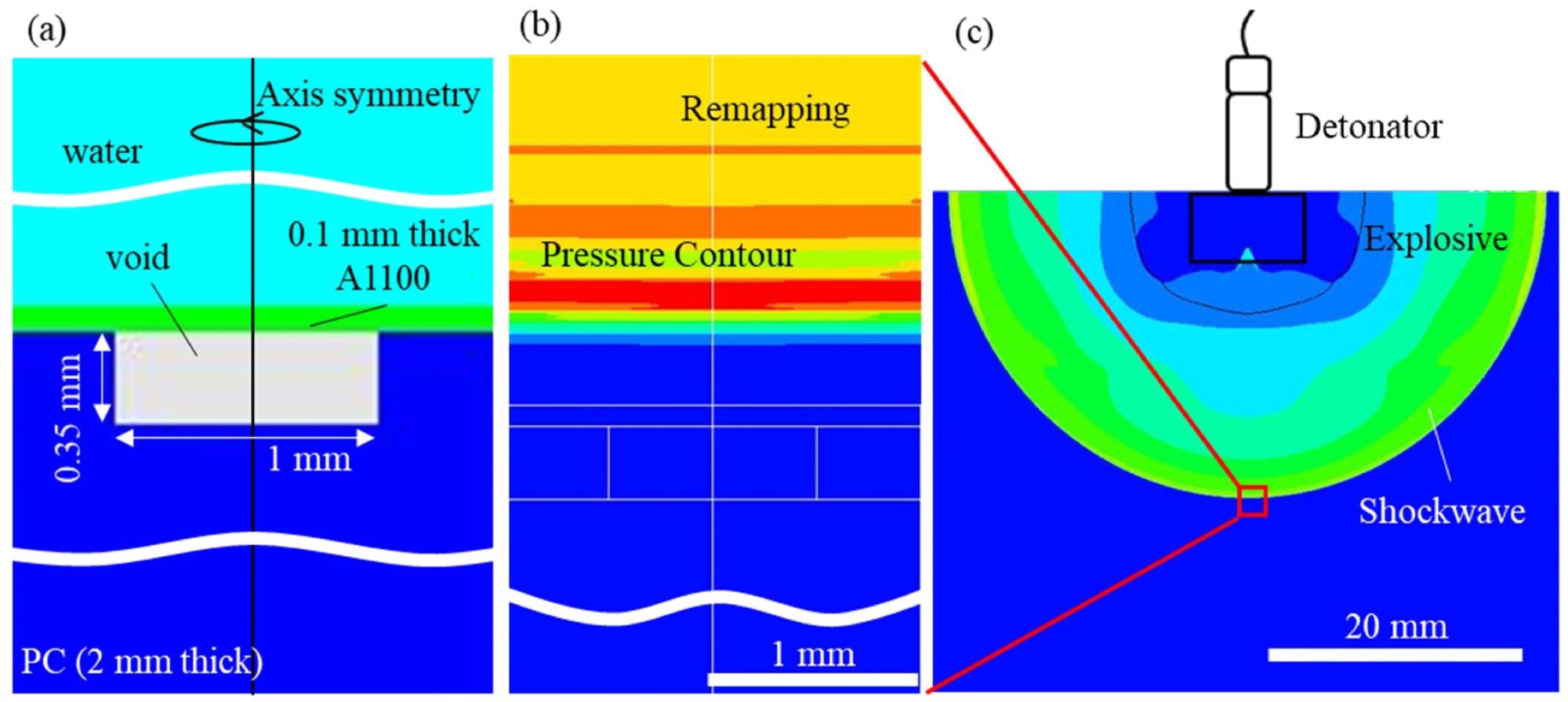
Numerical-simulation model using 2D Lagrangian and Eulerian solvers. (a) Dimensions and shapes of the PC mold, Al workpiece, and water. (b) Setting of the initial conditions. (c) Underwater shock-wave model consisting of the explosive and water. Image Credit: Hasegawa, K et al., Materials
The experimental results were compared with the numerical simulation results in this study, which included molding trials with Al workpieces with relatively large diameters and pressure-measuring experiments employing explosive-derived underwater shock waves. To simulate the deformation process of the Al workpiece and PC mold, a numerical model containing explosives and water was added into the deformation analysis model.
Observations
In this study, the researchers observed that the punched hole diameter for H = 40 mm was 0.85 mm, and for H = 60 mm was 0.92 mm. The punching diameters for H = 80 mm and H = 100 mm were 0.91 mm and 0.93 mm, respectively. Furthermore, it was observed that in the experiments and numerical simulation, the pressure rise times were 130 ns and 180 ns, respectively.
A drop was observed in the thickness of the Al workpiece along the border of the mold which was reproduced in the H = 40- and 60-mm examples, but no such local decrease was observed in the H = 20 mm case. It was also shown that the workpiece deformation was limited to the mold edges at strain rates >105/s in the LSI tests utilizing Si nano-molds, leading to a high dislocation density and dislocation avalanches.
It was also determined that the duration of pressure was one of the requirements for controlling the shock-imprinting phenomena. The proposed pressure-measuring experiment yielded a pressure profile that represented the substrate's compressive deformation. The pressure profile generated by numerical analysis closely matched the experimental pressure, having two pressure peaks, confirming the experimental findings.
The effect of the shock pressure on the mold shape was found to be the most important factor in assessing the effect of pressure parameters on the punching. The strain rate had no effect on increasing the PC strength when pressures were in the gigapascal range; however, explosive-derived shock waves that lasted for microseconds, together with the polymer mold’s flexibility, enhanced the molding depth. During numerical analysis, constitutive laws, the equation of state, and parameters used to the material model accurately mimicked the dynamic deformation processes.
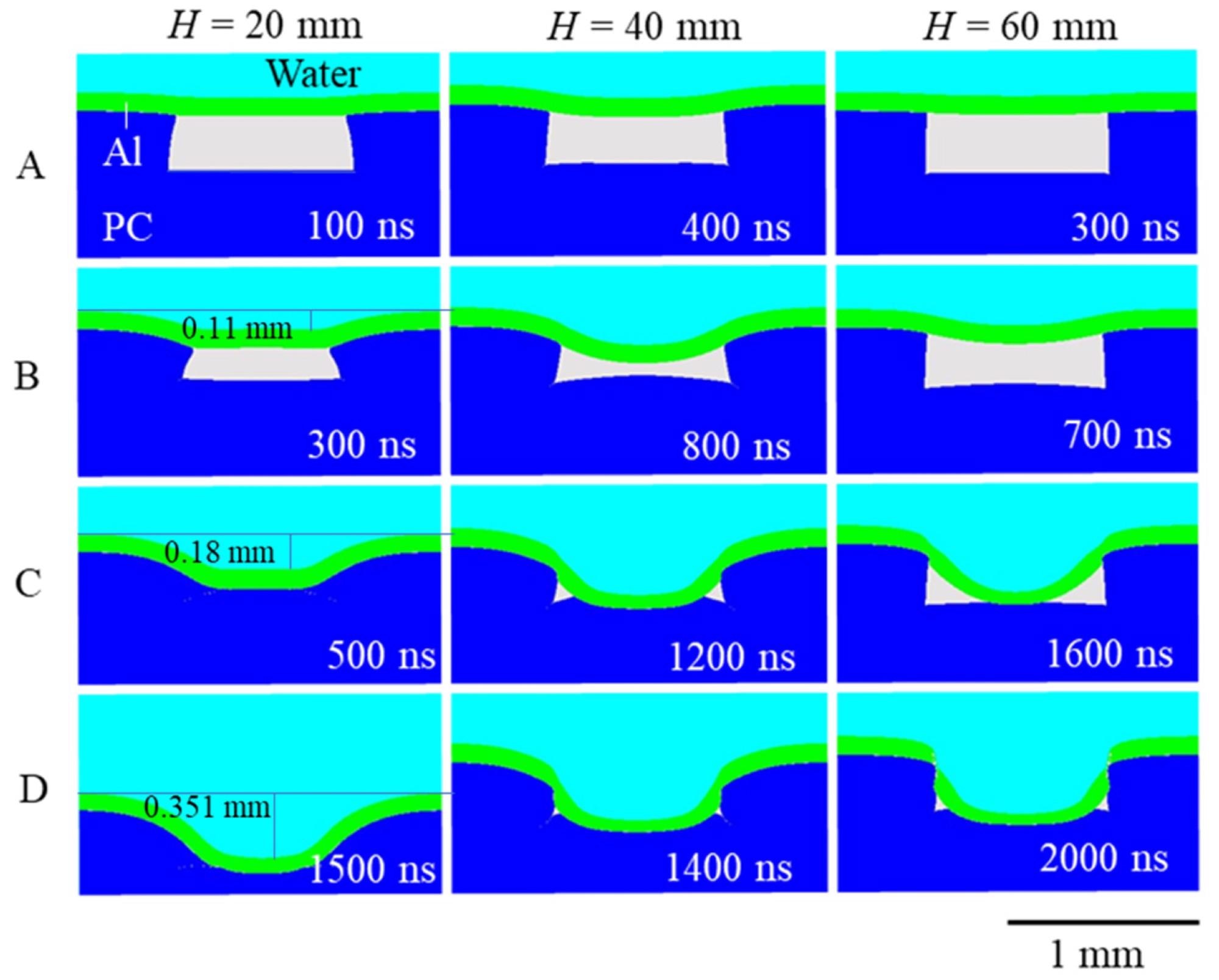
Deformation of the workpiece and mold due to the underwater shock wave. Image Credit: Hasegawa, K et al., Materials
Conclusions
In conclusion, this study elucidated the utility of polymer molds for shock-imprinting research on the basis of molding precision and cost savings. The authors observed that controlling the pressure and time of the imprinting process can help to relax the workpiece thickness restriction while also improving the imprinting accuracy. They emphasized that sustained pressure progressively raises the molding depth of the workpiece, whereas a strong pressure rapidly deforms the polymer mold. As a result, one of the requirements for controlling the impact imprint phenomena could be the length of the pressure.
The researchers believe that the findings of this study will add a new factor to shock-imprinting research and its corresponding pressure duration.
Disclaimer: The views expressed here are those of the author expressed in their private capacity and do not necessarily represent the views of AZoM.com Limited T/A AZoNetwork the owner and operator of this website. This disclaimer forms part of the Terms and conditions of use of this website.
Source:
Hasegawa, K., Tanaka, S., Bataev, I., et al. Toward a Better Understanding of Shock Imprinting with Polymer Molds Using a Combination of Numerical Analysis and Experimental Research. Materials 15(5), 1727 (2022). https://www.mdpi.com/1996-1944/15/5/1727