From CSEMReviewed by Mychealla RiceMar 4 2022
Fuselages of next-gen aircraft increasingly feature composite materials. While these materials provide excellent strength-to-weight ratios and help reduce fuel consumption, they are typically poor electrical conductors. So, despite their obvious advantages, why is this design change problematic?
Image Credit: CSEM
Traditionally, aircraft fuselages are made with high-strength metal alloys, which provide enough electrical conductivity to ensure that electrical currents flow back into the aircraft. In next-gen aircraft, the use of composite materials with low conductivity limits or even prevents the return of electrical current to the ground. Finding a solution to this problem was the challenge laid out by the EU Clean Sky 2 initiative to the AMPWISE consortium.
The AMPWISE consortium responded by developing a low-cost, wireless, energy-autonomous current sensor to monitor the current feedback network, which uses the fuselage support beams and rails. The components of this beam-rail network are metallic and have good conductive properties. These structures, however, were not designed to support such a high electrical intensity, and the long-term effects of which are still unknown, especially in terms of corrosion resistance at the junction points.
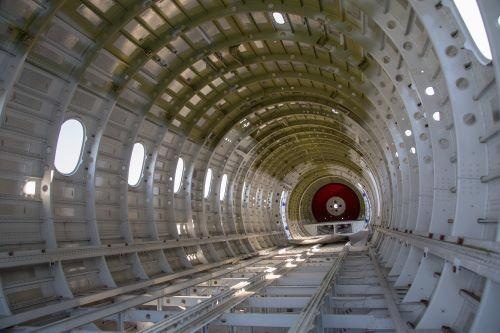
Fuselage structure. Image Credit: CSEM
The device developed in the AMPWISE project measures the amount of current at different points across the beam-rail network and monitors the long-term effects or failures caused by reverse current.
CSEM was instrumental in developing the wireless communication transmission protocols and the ultra-low-power hardware/software to ensure the new AMPWISE system consumed as little energy as possible,” notes Damien Piguet, Project Manager of Integrated and Wireless Systems at CSEM. “The communication system supports thousands of wireless sensors scattered throughout the aircraft in star topologies. Intelligent hubs then manage up to 300 wireless sensors each and control their operating cycle to minimize power consumption,” he adds.
The electronics developed by CSEM offer ultra-low-power wireless communication functions; they can measure the physical quantities required for the application and manage the system's activity and recovered energy to ensure continuous operation. CSEM also integrated robust communication elements at all levels: custom antennas optimized for metallic environments, secure and efficient communication protocols, node management, and self-healing.
The project was finalized in July 2021, and applications for the new sensing system could go well beyond its intended scope. Its potential extends to other transport vehicles, including trains and electric vehicles.
Consortium
The consortium includes one industrial partner, SENIS (CH), a sensor manufacturer, and SERMA INGENIERIE (FR), an OEM for aeronautical equipment. It also includes Imperial College London (U.K.), a university with a significant track record in Energy Harvesting, including prototypes for aircraft, and CSEM, who coordinated the project thanks to its long experience in IOT, space and aeronautical projects.
Funding: AMPWISE is an EU-funded Clean Sky H2020 project under the Grant agreement n° 785495. (https://cordis.europa.eu/project/id/785495)