Due to the challenges presented by human activities and climate change, innovative solutions are needed for the future of construction. Writing in Sustainability, a team of researchers from France and the US has investigated using dredged sediment for manufacturing compressed earth blocks for sustainable building materials.
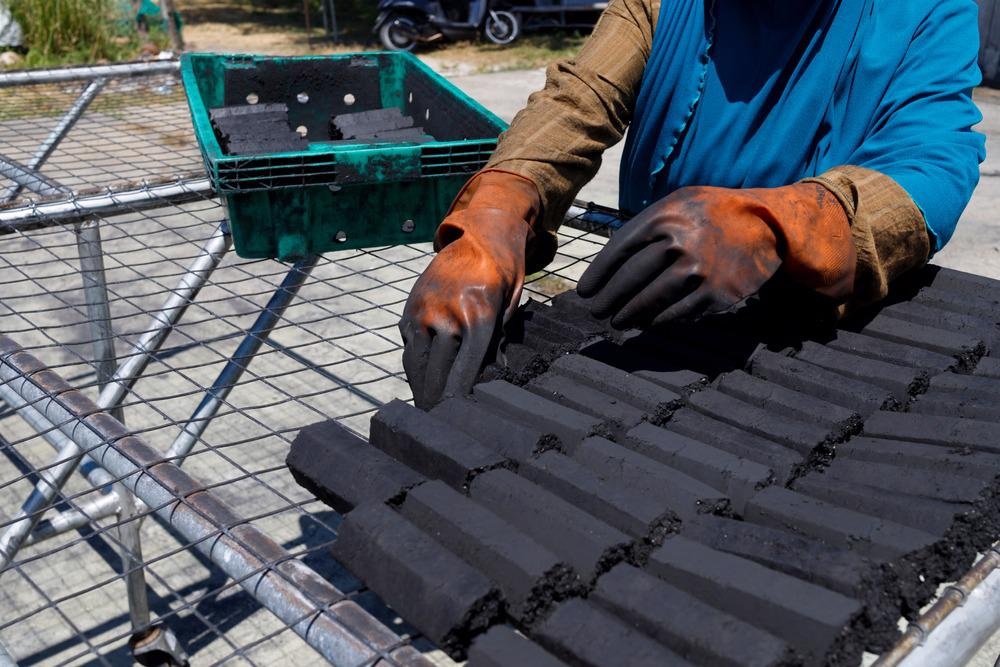
Study: Compressed Earth Blocks Using Sediments and Alkali-Activated Byproducts. Image Credit: phongwit phojurai/Shutterstock.com
Meeting the Challenges of Climate Change
The world is warming, presenting an existential danger for future generations. Whilst the world has relied on fossil fuels to drive rapid progress since the industrial revolution, using these non-renewable resources emits greenhouse gases which drive environmental damage on a scale previously unseen in human history. In order to combat environmental damage and limit carbon emissions, fossil fuel use needs to be reduced to zero as quickly as possible.
Amongst human activities driving climate change, construction is a key industry that emits greenhouse gases from areas such as concrete and steel production, building projects, and vehicle and plant use. Due to the exploitation of vast amounts of raw materials and the emissions, the production of valuable building materials from these resources entails, there exist huge opportunities for innovative solutions utilizing waste resources. Waste resources can reduce emissions and impart building materials with enhanced properties.
Compressed Block Materials. (a) Fly Ash class F. (b) Sediment 0/5 mm. (c) Ground Blast Furnace Slag. (d) Sodium Hydroxide pellet. Image Credit: Belayali, F et al., Sustaianbility
Sediments as Construction Material Resources
Dredging is an important activity that prevents waterways and harbors from silting up and becoming unusable, severely reducing the navigation depth necessary for ships and interrupting the flow of commerce. Worldwide, millions of tons of dredged materials are removed every year, with nearly 300 million m3 removed in both the US and Europe, and 50 million m3 removed in France alone.
These materials are stored, treated, and transported overseas. However, countries have limited storage capacities for dredged sediments, facilitating innovative reuse strategies for them. The past few decades have seen the development of technologies for beneficial reuse.
Due to the need to remove dredged materials and sediments and the requirement for reducing the construction industry’s reliance on conventional building material resources and reduce its carbon emissions, the valorization of dredged sediments as construction materials has become a topic of research in recent years. Utilization of alternative resources such as sediments improves the sustainability of building construction.
A key area of research has been the use of dredged sediments as building material aggregates for concretes, bricks, and so forth to reduce the amount of conventional raw materials and provide enhanced material properties. Additionally, studies have been performed on using sedimentary materials in compressed earth blocks. A main advantage of this type of block is the reduction in energy use compared to traditional clay blocks.
Traditional binders such as lime and Portland cement yield modest physical and mechanical properties when used in compressed earth blocks. Economic, mechanical, and physical drawbacks with traditional block production have facilitated the need for alternative construction materials. Amongst alternative materials, geopolymers have been proposed as binders for stabilizing the earth used in compressed earth blocks.
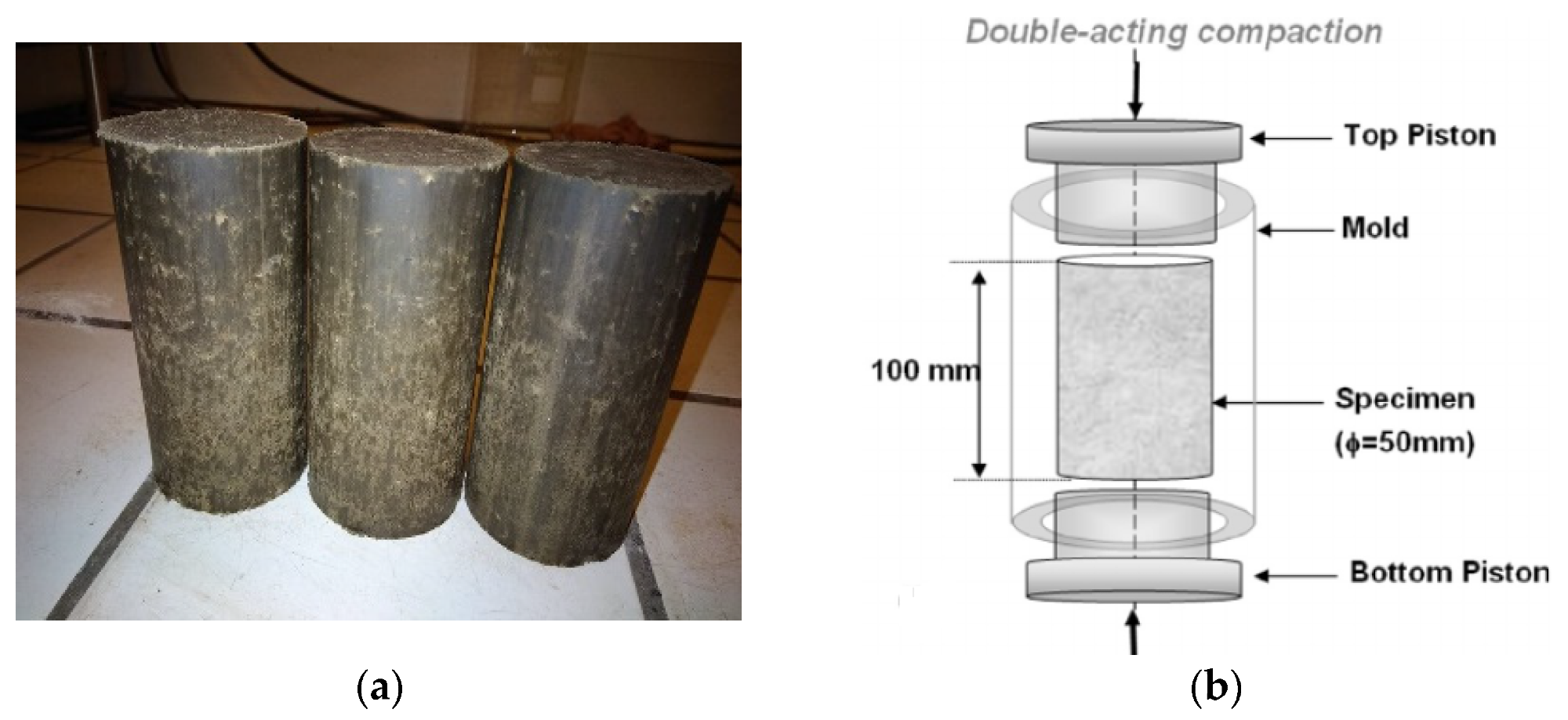
(a) Sample preparation; (b) device and specimens. Image Credit: Belayali, F et al., Sustaianbility
The Study
The study in the journal Sustainability has investigated using dredged sediments to produce compressed earth blocks. Alongside its benefits for the construction industry, this reduces the need for onshore storage or dumping of sediments further out to sea.
In the study, the authors conducted several experimental tests on two types of geopolymer. These geopolymers were produced by mixing sediments recovered from the north of France, and the geopolymers were mixed with fly ash and blast furnace slag, a byproduct of the steel and iron industry. The geopolymers were activated using a solution of concentrated sodium hydroxide at an 8M concentration and then cured at 50 °C.
Fly ash and ground blast furnace slag were both sourced from French companies and used as precursors to produce the geopolymerization reactions. Sediments were sieved to produce a granular size of 0-5 mm. The mixture of sediment and byproducts was homogenized to ensure even distribution using a Controlab mixer. Moistened mixtures were compacted using 40 bars of pressure. The final prepared specimens were removed from the molds using a piston.
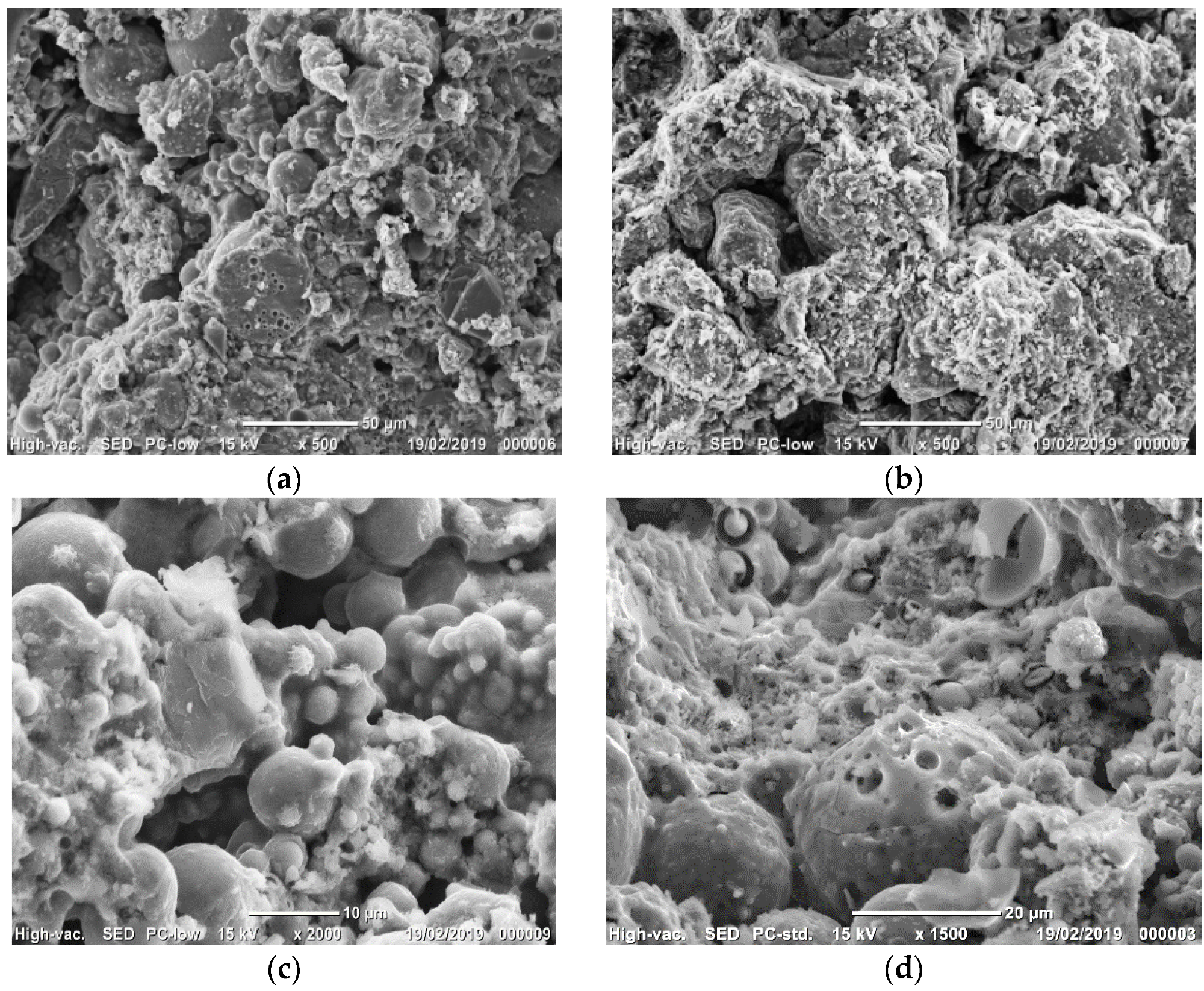
Scanning Electron Microscopy observations of CEB ((a,c,e) for F4 and (b,d,f) for F4′). Image Credit: Belayali, F et al., Sustaianbility
Specimens were covered with plastic film to prevent water loss and maintain humidity, and the curing time in the oven was seven days. Once cured, the specimens were removed and placed in a climatic chamber at room temperature for a further 14 and 28 days, and after this, the samples were characterized. Analysis was performed using X-ray diffraction and SEM.
Results of material categorization and analysis demonstrated that samples with a geopolymer content with 36% fly ash and 10% ground blast furnace slag demonstrated significantly improved mechanical and physical properties compared to using Portland concrete as a stabilizer. Addition of ground blast furnace slag enhanced the compressive strength and microstructure of the geopolymer paste.
Moreover, the use of dredged sediments and industrial byproducts significantly improves the sustainability of manufacturing compressed earth blocks. This will improve the circularity of the construction industry and reduce its carbon footprint as well as solve the problem of sediment disposal due to inadequate storage facilities.
Further Reading
Belayali, F et al. (2022) Compressed Earth Blocks Using Sediments and Alkali-Activated Byproducts [online] Sustainability 14(6) 3158 | mdpi.com. Available at: https://www.mdpi.com/2071-1050/14/6/3158
Disclaimer: The views expressed here are those of the author expressed in their private capacity and do not necessarily represent the views of AZoM.com Limited T/A AZoNetwork the owner and operator of this website. This disclaimer forms part of the Terms and conditions of use of this website.