A team of Spanish researchers has applied the 5S production methodology to provide a framework for metal welding processes, with the aim of improving process efficiency, weld quality, sustainability, and worker safety. They have published their findings in a new paper in the journal Sustainability.
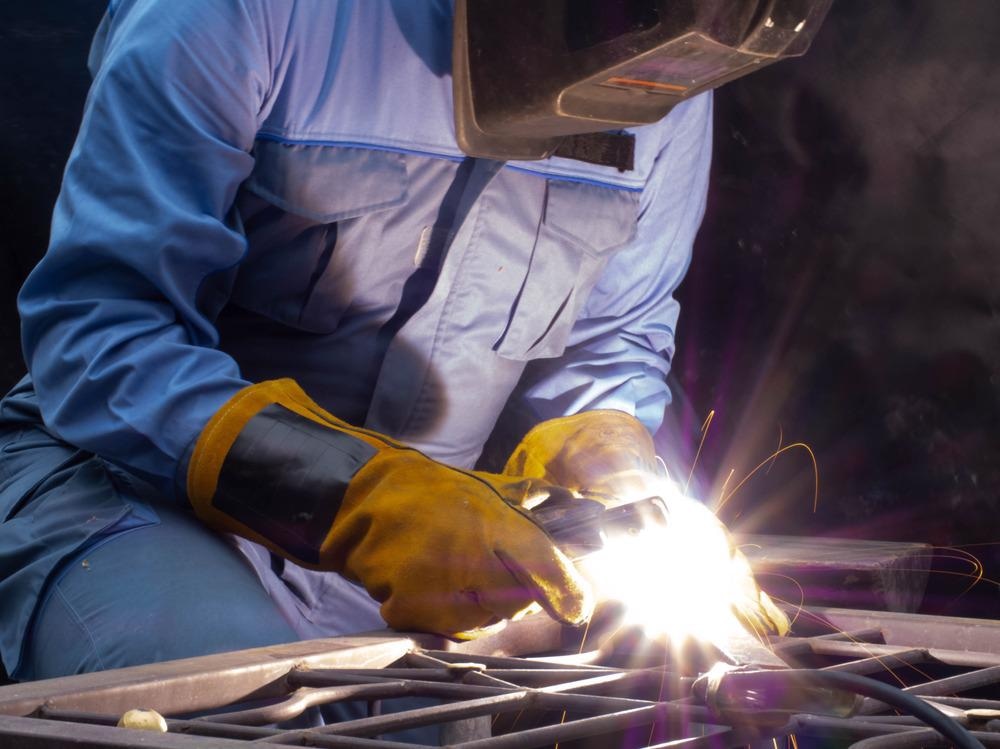
Study: A 5S Lean Strategy for a Sustainable Welding Process. Image Credit: StreetonCamara/Shutterstock.com
Background to the Research
Welding is used to manufacture almost every metal product used in sectors such as automobile manufacture, the aerospace industry, construction, shipbuilding, and railways. Producing products for these industries requires a collaborative approach between technicians, research and development scientists, engineers, and many other personnel.
Whilst electric arc welding has improved in recent decades, issues can still be encountered during the manufacture and use of welded parts, leading to reduced quality, part lifetime, economic loss, and potentially fatal outcomes for workers and end-users. Defective welds are a critical issue in the metal manufacturing industry.
Because of the issues which can arise from defective welds, several standards have been introduced in recent decades to improve the quality of parts and guarantee the safety of workers and individuals who use the final product. These standards govern the production of welded parts in factories, shipyards, and workshops. Examples include ISO 3834 and EN 1090.
(a) Storage of metal sheets, (b) Structure for the storage of metal profiles for railway products, (c) Example of identifying hand tools for the manufacture of stainless-steel products with the color yellow. Image Credit: Manzanares-Cañizares, C et al., Sustainability
By correctly applying these standards, risks are minimized. The 5S methodology is highly recommended to ensure that processes and parts meet the required standards. This methodology aims to improve workplace cleanliness, order, and organization, eliminating or mitigating risks and thereby improving workplace safety. The 5S methodology can serve the dual purpose of eliminating risk and ensuring part quality.
Several studies have been performed in recent years to investigate the suitability of 5S methodologies in various industries, demonstrating its benefits for multiple sectors. Empirical analysis has been employed on aspects such as quality, safety, and productivity.
Whilst the 5S methodology may seem simple to apply, studies have revealed this not to be the case in real-world conditions. It requires the integration of all processes and mechanisms in order to assess its degree of implementation.
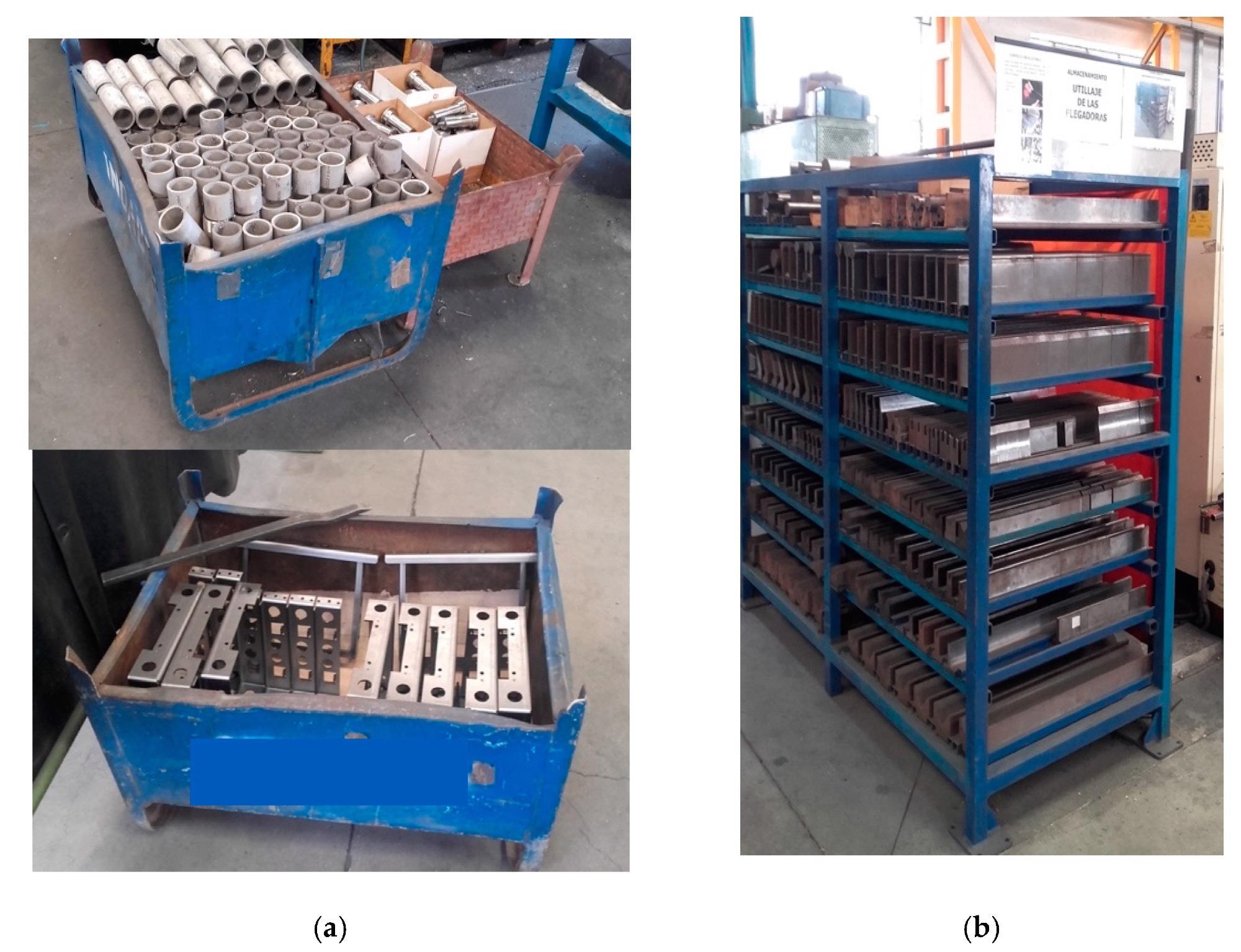
(a) Storage of products in containers, (b) Storage of press brake tools with 5S visual control signage. Image Credit: Manzanares-Cañizares, C et al., Sustainability
The Study
In the new paper, the authors have aimed to develop a comprehensive and systematic methodology to assess the degree of 5S implementation in metal welding. Using the proposed methodology, improvement actions can be suggested and these steps quantified. The authors selected sixteen indicators from the current literature to build their proposed methodology.
The proposed systematic method uses IPA methodology to determine improvement actions and fuzzy logic to treat evaluation uncertainty. Additionally, the authors have proposed an index to measure the process’s degree of 5S methodology implementation. The research aims to provide a framework for applying this methodology to improve metal welding processes.
To demonstrate the practical application of the proposed methodology, the authors have applied it to real company processes. The methodology was employed in a small company working in the metal products sector for building metal structures. Stainless steels, carbon steels, and aluminum alloys are used by the company to manufacture products.
The company employs eleven workers, with three employees dedicated to the arc welding process. A quality department engineer measured the indicators, and two engineers made 5S implementation and improvement proposals. All members of the work team evaluated the indicators using the proposed methodology. A geometric mean was employed to synthesize each indicator’s individual scores.
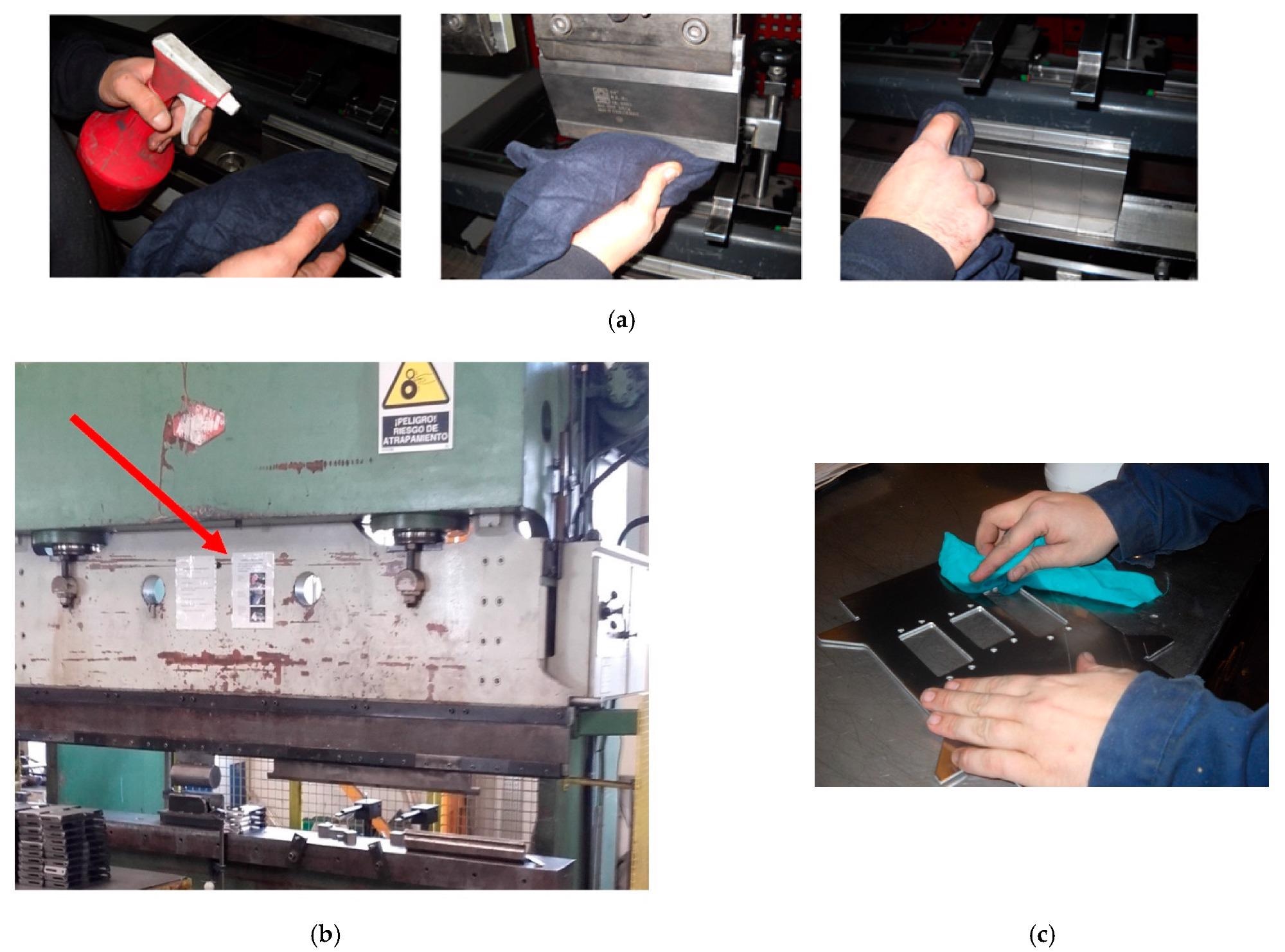
(a) Bending tool cleaning sequence, (b) Instructions for cleaning the bending tools placed on the press brake, (c) Cleaning the workpiece with acetone. Image Credit: Manzanares-Cañizares, C et al., Sustainability
Study Results
Results of the practical evaluation demonstrated that the 5S methodology improves manufacturing, handling, and storage practices for the manufacturing of welded metal parts. Using the author’s proposed systematic method, the company prevented possible safety issues and welded part defects, reducing the instance of critical issues such as cracks that lead to seam failure.
Eighteen non-conformities were detected using the proposed methodology across all production orders, with only three corresponding to welding orders. It was concluded that this was within acceptable limits. Due to this, it was not necessary to measure non-conformality cost, which was instead entrusted to management.
IPA matrix interpretation prompted the company to start measuring quality costs, and this has been extended to all the company’s workstations. A future indicator for the company will be the cost of implementing improvements. As a result of implementing the 5S methodology, the company has increased their welding workstations from three to five, with the number of work orders being increased whilst maintaining required levels of ergonomics, safety, and quality.
The methodological framework presented in the paper provides a useful strategy for implementing 5S improvements, helping companies to meet the required standards, and can be adapted for other processes. Whilst the authors have identified some limitations, the methodology can help to improve safety, productivity, sustainability, and product quality.
Further Reading
Manzanares-Cañizares, C et al. (2022) A 5S Lean Strategy for a Sustainable Welding Process Sustainability 14(11) 6499 [online] mdpi.com. Available at: https://www.mdpi.com/2071-1050/14/11/6499
Disclaimer: The views expressed here are those of the author expressed in their private capacity and do not necessarily represent the views of AZoM.com Limited T/A AZoNetwork the owner and operator of this website. This disclaimer forms part of the Terms and conditions of use of this website.