A paper recently published in the journal ACS Engineering Au demonstrated the characterization of ashes produced from the co-firing of mallee bark/biochar and coal.
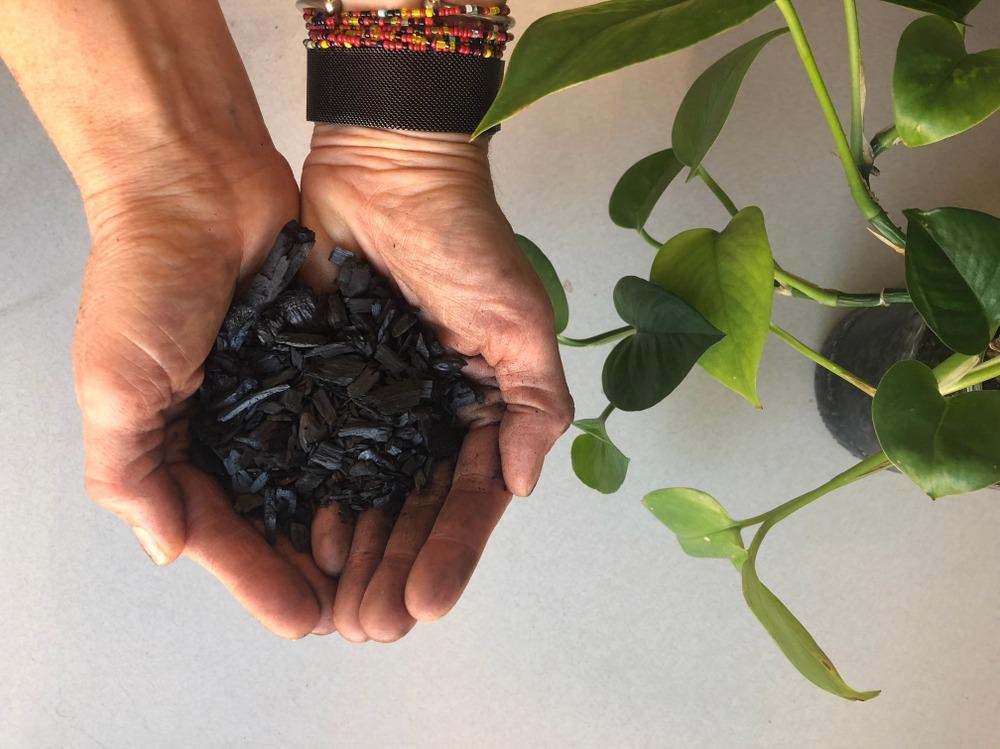
Study: Characterization of Ashes from Co-Firing Biochar with Coal under Pulverized-Fuel Conditions. Image Credit: Sydney Schaaf/Shutterstock.com
Background
Biomass can be used as a sustainable feedstock for power generation to ensure energy security. Direct biomass combustion is one of the established technologies for power generation. Nutrient-rich ashes obtained from the combustion of biomass must be recycled into the soil to promote the sustainable development of the biomass-based industry.
Biomass and coal are often co-fired under pulverized-fuel conditions to generate power. However, recycling the ash generated by this biomass energy technology can increase the risk of toxic elements leaching into the soil as coal ash contains several toxic trace elements. Thus, characterizing the ash produced from co-firing biomass with coal is necessary to identify the optimized ash management strategies.
The use of biomass as a co-firing feedstock is extremely challenging due to its high moisture content, bulky nature, mismatched properties with coal, and poor grindability. These issues can be addressed by co-firing biochar with coal in traditional pulverized-fuel boilers. The pre-treatment of biomass using distributed fast pyrolysis at low temperatures produces biochar and bio-oil.
The bio-oil can be converted into high-value green chemicals/liquid transport fuels, while the biochar with high energy density and excellent grindability can be co-fired with coal for electricity generation. Biochar contains higher contents of ash, carbon, and inorganic ash-forming elements and less volatile matter compared to biomass. Thus, biochar can produce ashes with different properties when co-fired with coal.
Although ashes obtained from the combustion of coal and biomass were investigated in previous studies, the ashes produced from co-firing coal with biochar have not been characterized until now.
Conceptual diagram of the proposed biochar-based co-firing technology. Image Credit: Wu, H et al., ACS Engineering Au
The Study
In this study, researchers characterized ashes produced from co-firing coal with biochar in terms of leaching characteristics, thermal behavior, mineralogy, chemical composition, particle size distribution (PSD), and morphology to evaluate the potential of this biochar-based co-firing technology for different applications.
Three fuel samples, a Collie coal, a mallee bark, and biochar produced from the fast pyrolysis of the mallee bark, were utilized to prepare the fuel blends for the co-firing experiments.
The bark was separated from Eucalyptus polybractea/mallee tree, dried in an oven at 40 oC, size-reduced using a cutting mill, and sieved into 75−90 μm size fractions. Subsequently, the bark was subjected to fast pyrolysis using fast pyrolysis reactor at 500 oC to produce the biochar.
The Collie coal was crushed and dried at 105 oC overnight and sieved to a 75−90 μm size fraction. Subsequently, the biochar or the bark was thoroughly mixed with the coal at 40, 20, and 5% concentrations based on the lower heating value (LHV) to synthesize blended fuels for combustion experiments.
A drop-tube furnace (DTF) system was used to perform the combustion experiments. The furnace temperature was maintained at 1400 oC, and the heating rate of feedstock particles was 10,000 °C/s. The feedstock particles were fed into the system at a 0.05 g/min feeding rate, and their residence time in the DTF isothermal zone was 1.7 s.
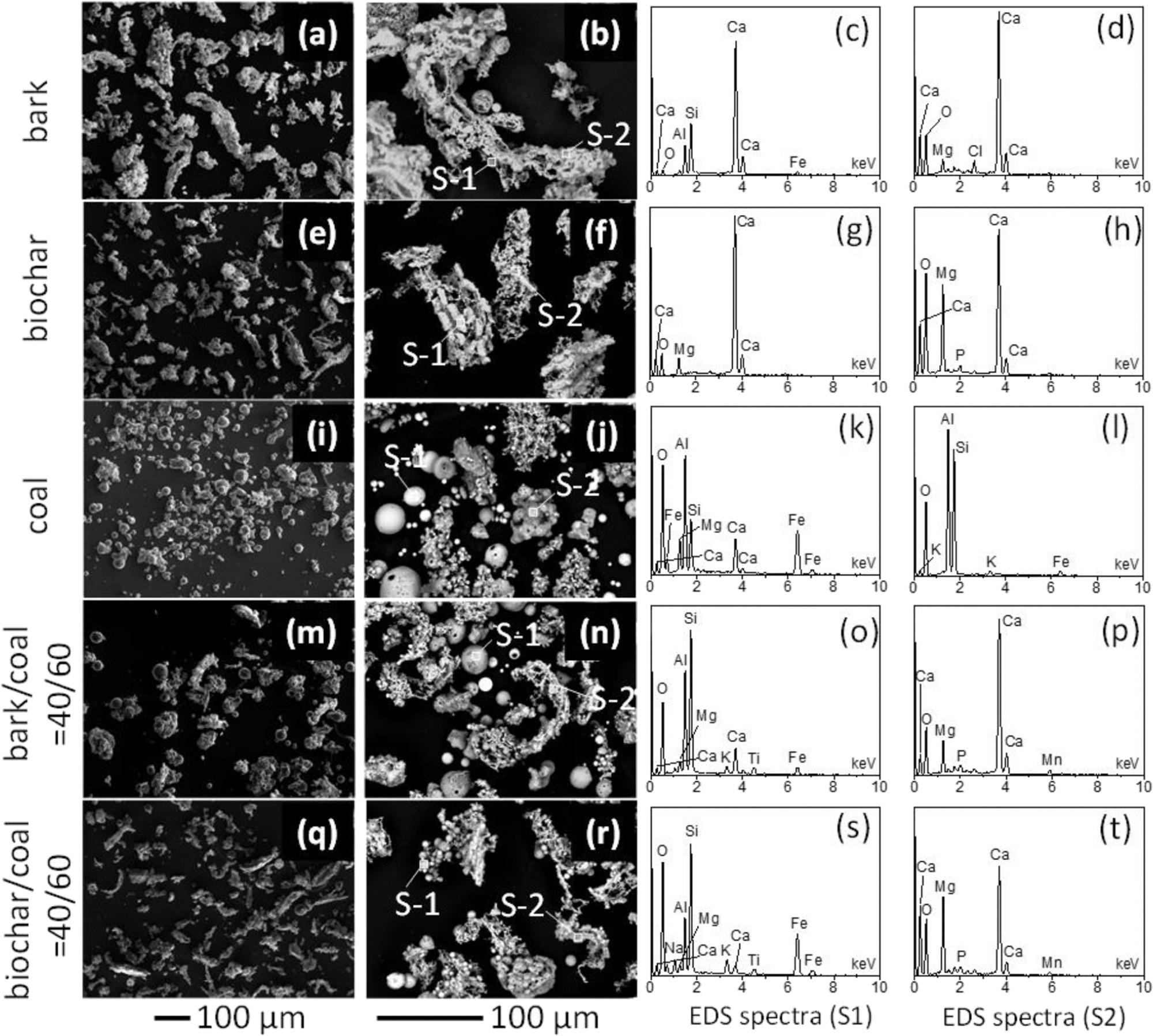
SEM images of the ashes produced from the combustion of bark (a,b), biochar (e,f), coal (i,j), bark/coal = 40/60 (m,n), and biochar/coal = 40/60 (q,r), along with their EDS spectra (c,d,g,h,k,l,o,p,s,t). It is noted that the EDS analyses are only qualitative because the ash particles were not polished. Image Credit: Wu, H et al., ACS Engineering Au
After complete combustion of feedstock particles, two streams of helium were used to quench the flue gas in a water-cooled sampling probe. The flue gas was then diluted with 3.4 L/min of air and transferred into a Dekati cyclone, where particles with more than 10 μm aerodynamic diameter were collected for further characterization.
Proximate analysis of the coal, biochar, and bark was performed under American Society Standard Test Method (ASTM) E870-82. An elemental analyzer was used to determine nitrogen, hydrogen, carbon, and sulfur contents, while chlorine was quantified using an improved Eschka method.
Dionex ICS-3000 ion chromatography was utilized to quantify the alkali and alkaline-earth metallic (AAEM) species in the fuels, while inductively coupled plasma-atomic emission spectroscopy (ICP−AES) was employed to quantify titanium, phosphorous, manganese, strontium, iron, silicon, and aluminum in the fuels.
A Zeiss EVO 40XVP scanning electron microscopy instrument equipped with an energy-dispersive X-ray spectrometer (SEM-EDS) and a Bruker-AXS D8 advance type X-ray diffractometer (XRD) was used for the characterization of ashes. Thermogravimetric analysis (TGA) was performed to investigate the thermal behavior of the ashes.
Observations
Researchers systematically characterized the ashes generated by the co-combustion of coal and biochar/bark. The biochar properties were closely matched with the properties of coal in terms of fixed carbon, volatility, and LHVs compared to bark. The high bio-oil yield was obtained during the pyrolysis, which improved the overall economic viability of the process.
The dry biochar yield after pyrolysis was 24.3 wt % of the original bark. However, almost 89% of potassium and 100% of the calcium, magnesium, and sodium in the bark were retained in the biochar after the pyrolysis process. Thus, the concentration of these elements was significantly higher in biochar compared to biomass.
Only 28% chlorine was retained in biochar as the majority of chlorine was released in the form of chloromethane and/or hydrochloric acid during pyrolysis, which showed another advantage of biochar as a co-firing fuel as chlorine-related problems were largely mitigated.
The morphology of biochar and bark ash particles was of irregular shape, while the coal ash particles were round. All ash particles followed a unimodal distribution, with 5−12 μm area-equivalent mode diameter, except the ash particles of bark that showed two bigger peaks at 95 μm and 65 μm.
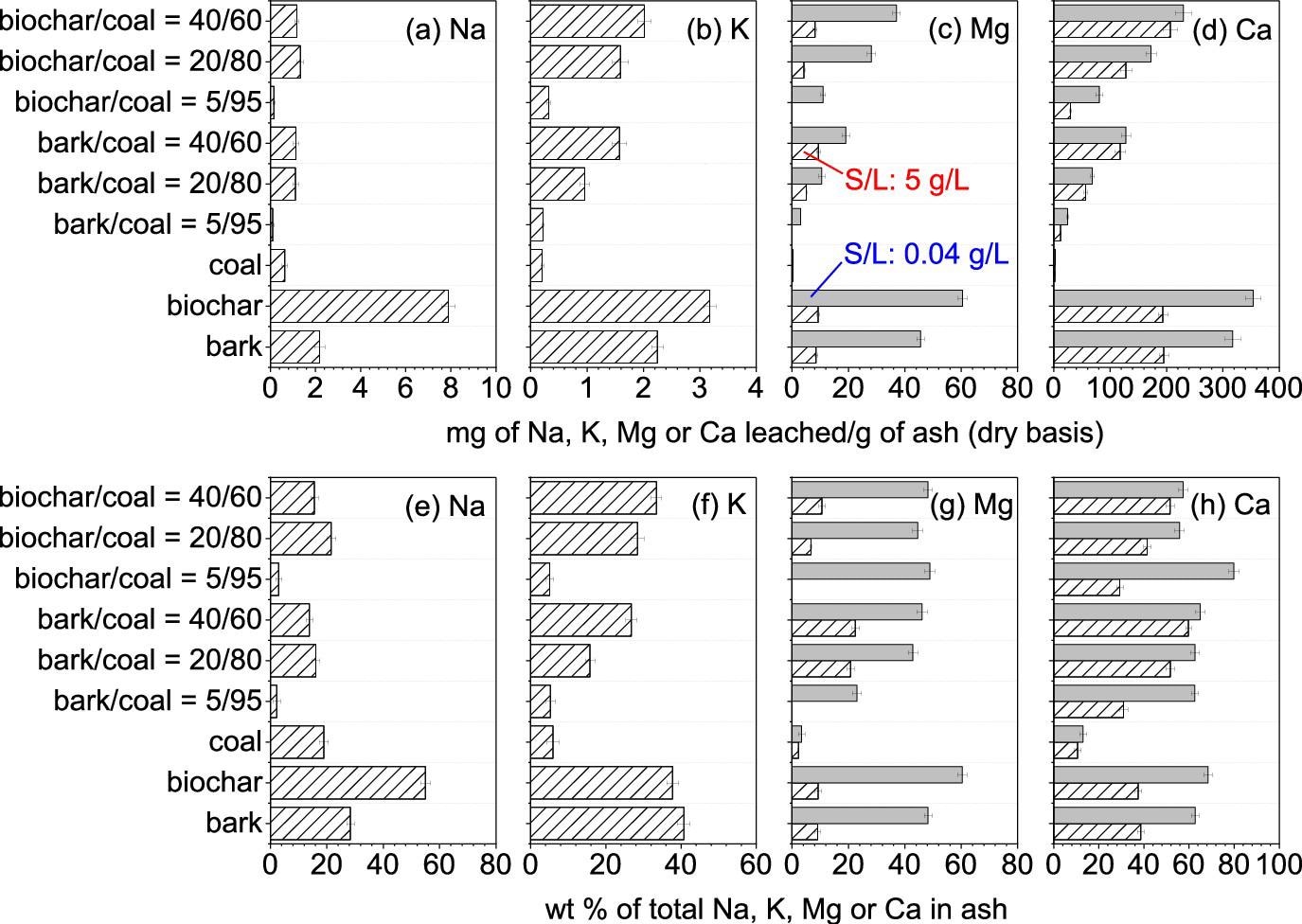
Quantity of water-leachable nutrient elements in the ashes produced from the combustion of the bark, the biochar, the coal, and their mixtures. S/L = Solid/liquid ratio during water leaching. Image Credit: Wu, H et al., ACS Engineering Au
AAEM species such as calcium, magnesium, potassium, and sodium were the major inorganic materials present in the biochar and bark ashes. These inorganic elements contributed 92−94 wt % of overall inorganic species in biochar/bark. In coal ash, silicon, aluminum, and iron accounted for 84 wt % of the overall inorganic materials.
The calcium and magnesium content was higher in the biochar/coal ashes compared to bark/coal ashes under similar co-firing ratios due to the high concentration of these elements in biochar.
Hematite, quartz, and mullite were the major minerals detected in the coal ash, while lime, calcite, magnesite, and portlandite were the dominant minerals in the biochar and bark ash. Unburned carbon content was negligible in these ashes. 69% of calcium, 56% of magnesium, 41% of potassium, and 56% of sodium in the ashes can be recycled through water leaching.
A large number of trace elements, such as arsenic, zinc, selenium, lead, nickel, manganese, mercury, cadmium, and copper, were not detected in the leachates from water washing. However, the chromium amount detected in the ash of 40%biochar/coal exceeded inert threshold values.
Taken together, the findings of this study demonstrated that nutrient-rich ashes obtained from the co-firing of bark/biochar-coal can be effectively and safely recycled into the soil, except for the ashes produced from 40%biochar/coal mixtures due to the presence of high levels of chromium.
Disclaimer: The views expressed here are those of the author expressed in their private capacity and do not necessarily represent the views of AZoM.com Limited T/A AZoNetwork the owner and operator of this website. This disclaimer forms part of the Terms and conditions of use of this website.
Source:
Wu, H., Gao, X., Chen, X. et al. Characterization of Ashes from Co-Firing Biochar with Coal under Pulverized-Fuel Conditions. ACS Engineering Au 2022. https://doi.org/10.1021/acsengineeringau.2c00012