A team of researchers recently published a paper in the journal Cleaner Materials that demonstrated the feasibility of using supplementary cementitious materials (SCMs) obtained from the calcination of low-grade clay deposits to produce low-carbon cement.
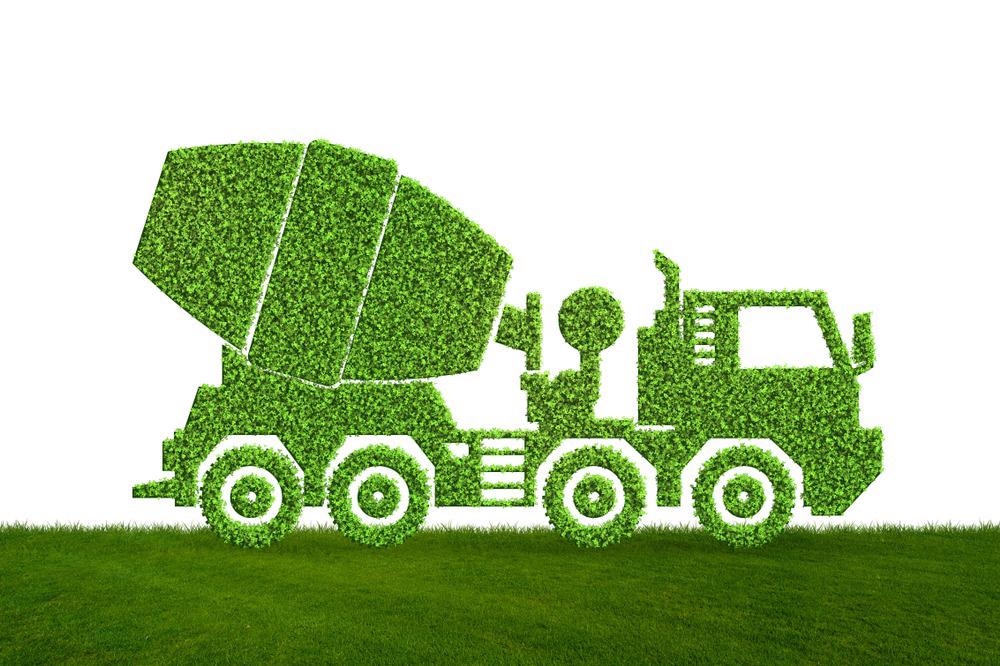
Study: Low-carbon cements: potential for low-grade calcined clays to form supplementary cementitious materials.Image Credit: Elnur/Shutterstock.com
Background
The production of Portland cement (PC) has notably contributed to anthropogenic carbon dioxide emissions across the world. Thus, carbon dioxide emissions from PC production must be reduced significantly to achieve a substantial reduction in global carbon dioxide emissions.
Several strategies based on clinker substitution, carbon capture and storage (CCS), the use of alternative fuels in cement kilns, and increasing the energy efficiency of the PC production process were investigated to reduce the carbon dioxide emissions from PC production.
Although strategies based on CCS, alternative fuels, and enhanced energy efficiency were effective in the reduction of carbon dioxide emissions, they also have a few drawbacks, such as a high cost of implementation, which made them economically unviable. The substitution of cement clinker with SCMs is typically considered the most viable strategy to reduce carbon dioxide emissions from PC production.
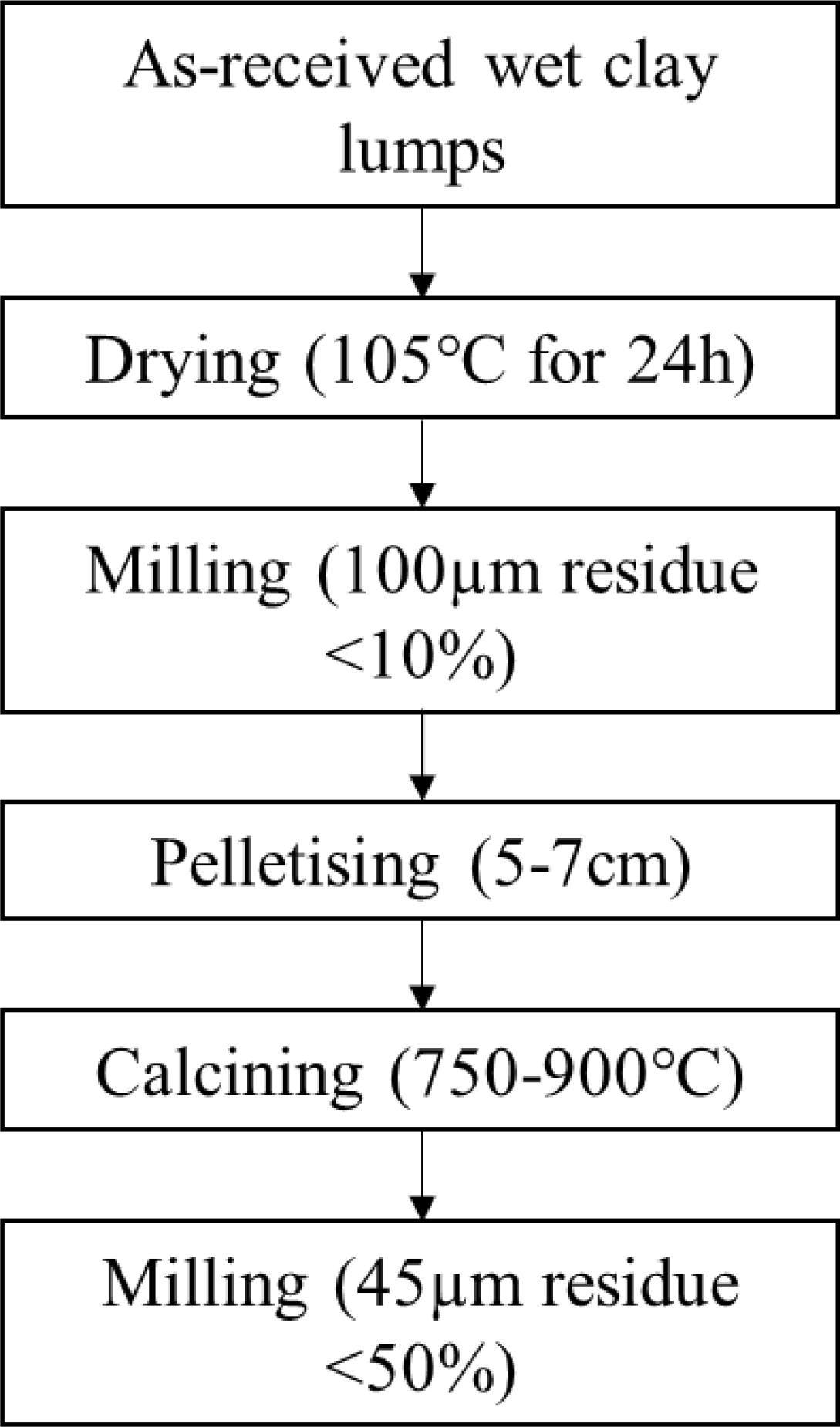
Process flowchart showing the stages prior to calcination and the follow-up milling regime. Image Credit: Wong, H et al., Cleaner Materials
Ground granulated blast furnace slag (GGBFS) and pulverized fuel ash (PFA) are the most commonly used SCMs for clinker substitution. However, potential difficulties related to the supply of these SCMs in the future have necessitated the identification of alternative materials for clinker substitution and reducing the carbon content in concrete.
Calcined clays have gained considerable attention as a potential SCM as clays are geologically abundant and their calcination is a simple, low-carbon, and low-cost process. Clays are typically stockpiled in quarries and are also available as clay excavation wastes or basal deposits. Moreover, big civil engineering infrastructure projects, such as road construction and tunneling, can act as other major sources of clay.
Clays generally contain minerals such as illite, smectite, and kaolinite, which can become pozzolanic when calcined at temperatures between 700 and 900 oC due to dehydroxylation reactions and amorphous aluminosilicate formation.
Amorphous aluminosilicates react in presence of hydrating PC to yield calcium silicate hydrate (C-S-H). Previous studies have confirmed that no significant difference exists in the performance between 30% calcined kaolinitic clay/ 70% PC samples and 100% PC samples.
Limestone calcined clay cement (LC3) systems utilize synergies between limestone and calcined clay to allow up to 50% substitution of clinker with calcined clay. However, the clays utilized in the LC3 system typically contain 40% kaolinite.
Several studies have demonstrated the effectiveness of using low-grade calcined clay in LC3 systems for clinker substitution. For instance, calcined mica-rich clays were used to successfully substitute 15% of PC mass without decreasing the cement strength.
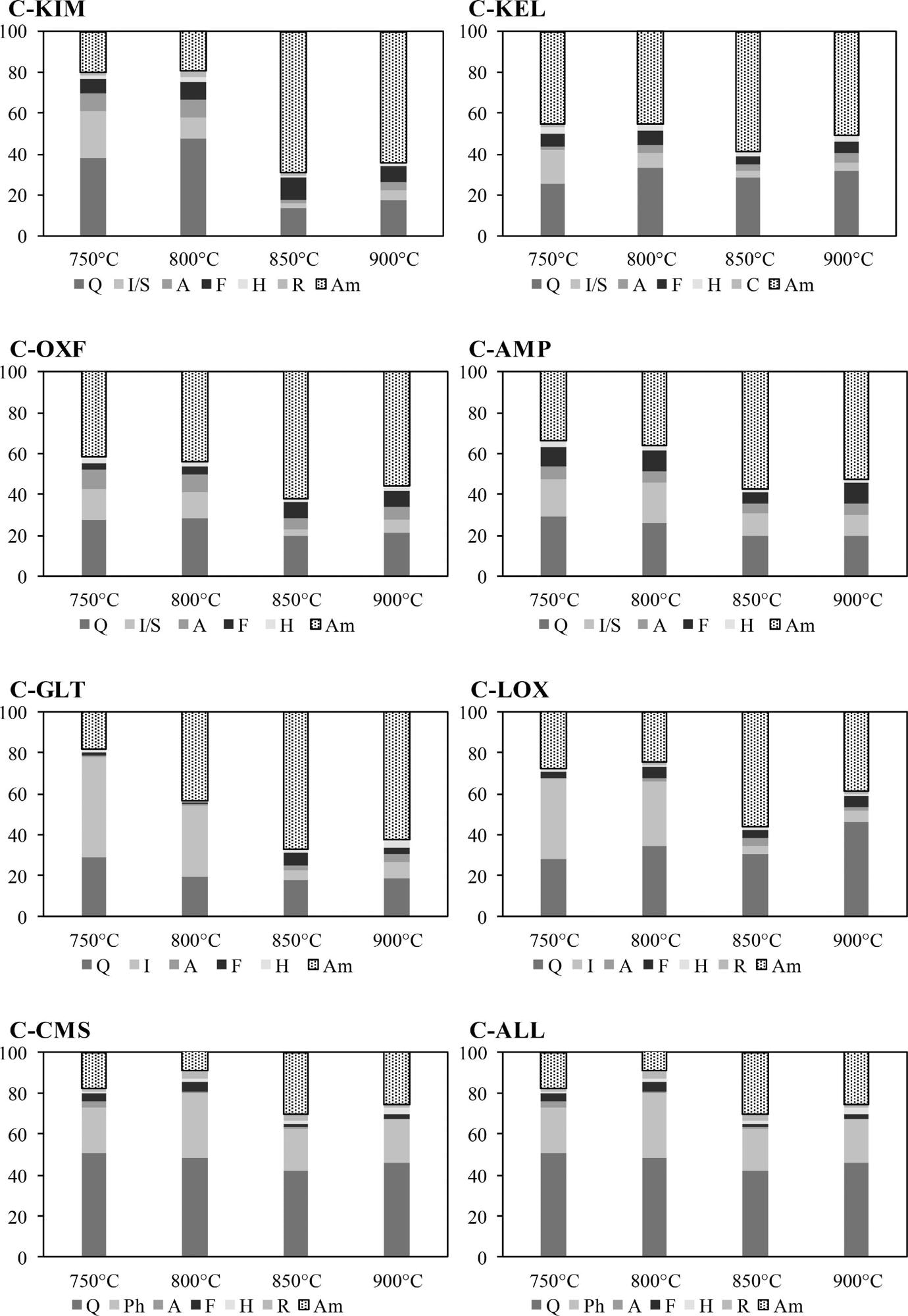
Mineral phase composition and the amorphous content (Am) of calcined clays at different temperatures measured using XRD/Rietveld analysis. Phases quantified included quartz (Q), illite (I), smectite (S), chlorite (C), phlogopite (Ph), anhydrite (A), feldspar (F), rutile (R) and hematite (H). Image Credit: Wong, H et al., Cleaner Materials
The Study
In this study, researchers calcined eight low-grade clay samples obtained from various geological formations across the United Kingdom (UK) with less than 20% kaolinite to synthesize SCMs.
Researchers characterized the clays after and before calcination and determined the pozzolanic activity and amorphous phase contents of calcined clays to evaluate the potential of these low-grade clays to produce viable SCMs.
The geological formations of the clay samples were alluvial clay (ALL), coal measure shale (CMS), lower-Oxford clay (LOX), Gault clay (GLT), Ampthill clay (AMP), Oxford clay (OXF), Kellaways clay (KEL), and Kimmeridge clay (KIM). The X-ray diffraction (XRD) method and the internal standard method were used to determine the mineralogical phase and amorphous content of the clay samples, respectively.
The clay samples were then dried for 24 hours at 105 °C and milled in a disc mill to obtain a 100 µm residue. Pellets of five to seven cm in diameter were prepared by adding water to the as-obtained residue and hand rolling the resultant mixture before the calcination process.
Subsequently, the pellets of different lay samples were calcined at 900, 850, 800, and 750 °C for 60 min in an electric chamber furnace at a 5 °C/min heating rate. The XRD data was used to determine the optimal calcining temperature to evaluate the non-reactive phase recrystallization, dehydroxylation, and amorphous phase generation.
All calcined clay samples were ground before the pozzolanic activity tests. The laser diffraction method was utilized to determine the specific surface area (SSA) and particle size distribution (PSD) of both PFA and calcined samples. Researchers also performed a pozzolanic activity test to determine the pozzolanic activity of the calcined samples and measured the strength activity index (SAI) of the samples.
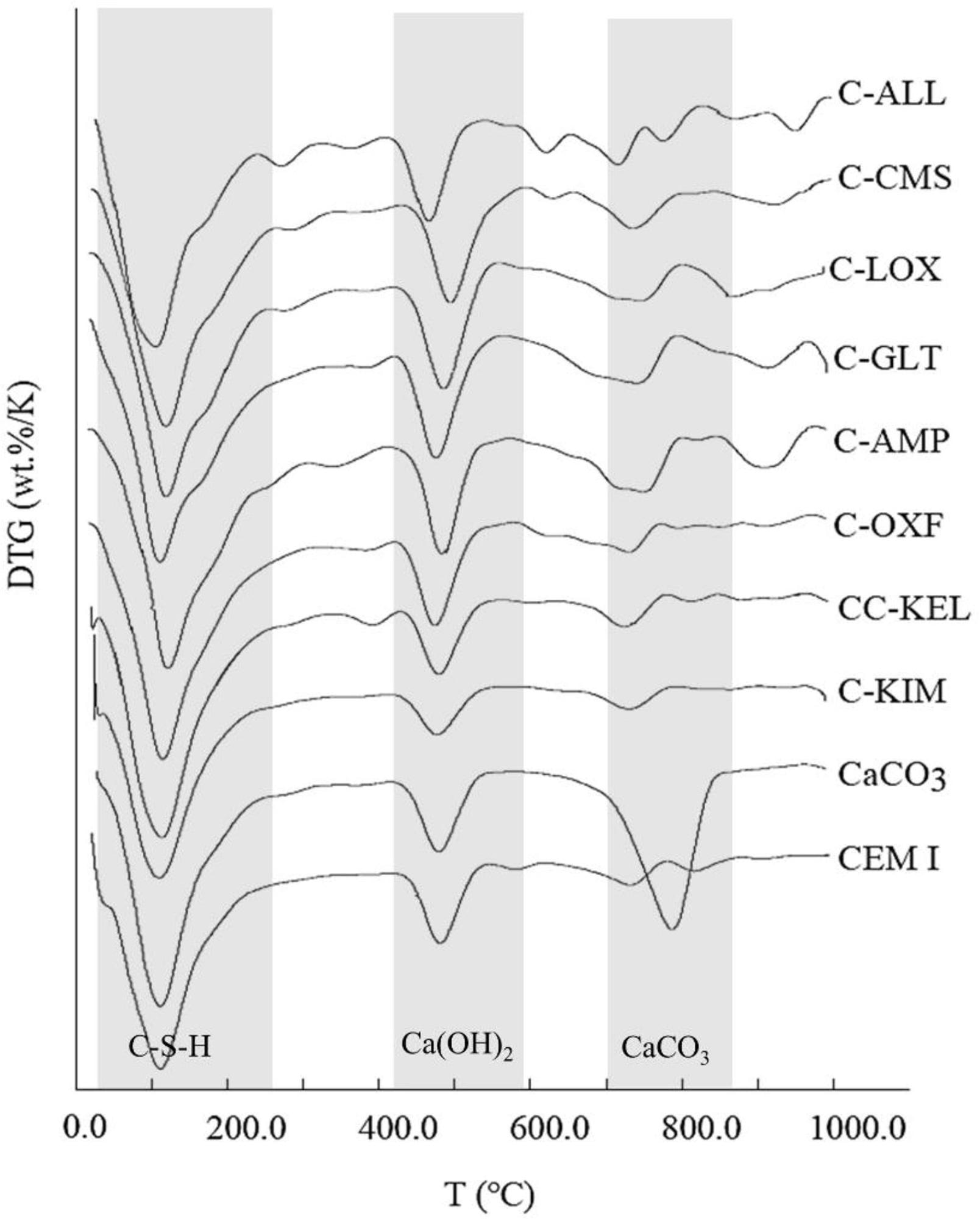
Derivative thermogravimetry (DTG) curves of 75% PC: 25% calcined clay (850 °C) paste mixes after 28 days of curing showing weight loss peaks in C-S-H, Ca(OH)2 and CaCO3 decomposition temperature ranges. Plain PC (CEM I) and 75% PC: 25% CaCO3 mixes were used as controls. Image Credit: Wong, H et al., Cleaner Materials
Observations
Researchers successfully characterized the eight clay samples obtained from different geological formations. Pelletization created a reducing environment in the pellets upon heating and cooling, leading to the formation of a ferrous ion matrix phase that produced calcined clays with a grey-black color, which was comparable to the color of PC.
The optimal calcining temperature was 850 °C for maximum reactivity. The AMP and OXF clays calcined at 850 °C demonstrated a high SAI and pozzolanic activity when reacted with calcium hydroxide compared to traditional SCMs such as PFA.
These samples were rich in smectite/ illite mixed layered clays and produced 60% reactive amorphous phases after calcination. However, non-clay impurities such as pyrite, quartz, and calcite were present in the calcined clays.
Mortars containing calcined OXF and AMP clays displayed higher compressive strengths compared to mortars produced using PFA. Additionally, calcined clay mortars attained 90% of the compressive strength of 100% PC mortars at 28 days.
To summarize, the findings of this study demonstrated that SCMs produced by the calcination of readily available low-grade clay resources could be used effectively to form cementitious materials with reduced carbon dioxide emissions.
Disclaimer: The views expressed here are those of the author expressed in their private capacity and do not necessarily represent the views of AZoM.com Limited T/A AZoNetwork the owner and operator of this website. This disclaimer forms part of the Terms and conditions of use of this website.
Source:
Wong, H., Newport, D., Ayati, B. et al. Low-carbon cements: potential for low-grade calcined clays to form supplementary cementitious materials. Cleaner Materials 2022. https://www.sciencedirect.com/science/article/pii/S2772397622000594?via%3Dihub