Owing to increased power consumption all over the globe, the use of sustainable and pollution-free means of energy like wind power has gained considerable attention. However, accurate modeling of the losses occurring when a large number of turbines work together in a grid is essential. The latest article in the journal Energies focuses on the development of a mathematical model to maximize the power coefficient (CP).
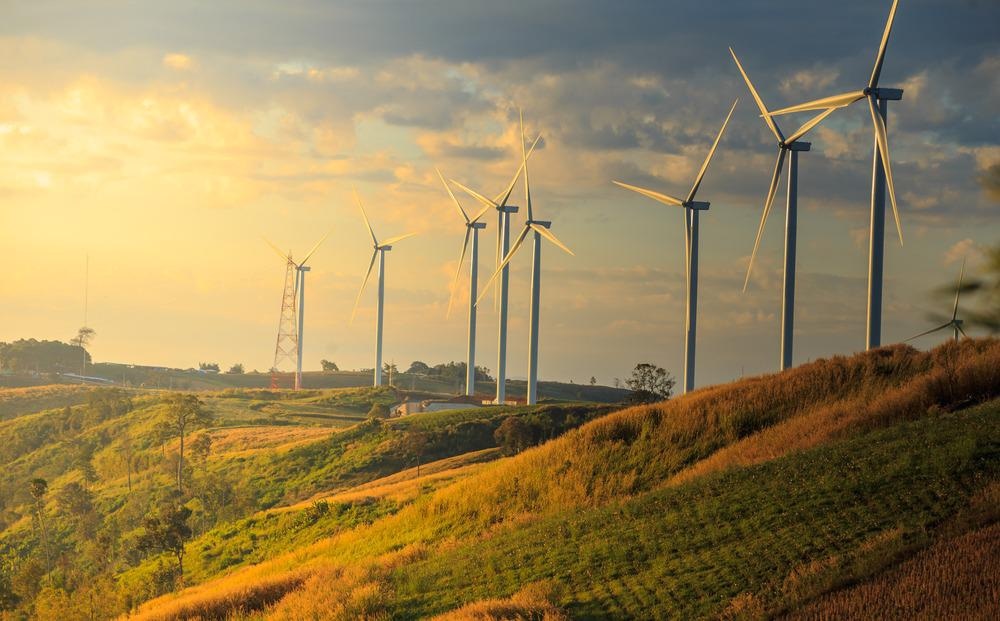
Study: Model for Optimal Power Coefficient Tracking and Loss Reduction of the Wind Turbine Systems.Image Credit: chaiviewfinder/Shutterstock.com
What are Wind Turbines?
A wind turbine is a mechanical assembly that converts the energy stored in the air to electrical energy. The wind turbine has a rotor upfront which is rotated by air. Turbines are labeled as horizontal axis and vertical axis based on their axis of rotation. Turbines operating on land are called on-shore wind turbines and those situated in water bodies are termed off-shore wind turbines.

Wind turbine power train and types of distributed losses. Image Credit: Sohail K et al., Energies
Advantages of Wind Energy
The production of electrical power via wind energy has several advantages. Firstly, it does not require any fuel to operate. It not only significantly reduces the operating costs but is also advantageous in terms of being ecologically friendly and sustainable. Additionally, the most recent technological advancements have converted basic wind turbine ideas into amazingly efficient power sources.
Disadvantages of Wind Energy
Wind turbines are recognized to be hazardous to animals. Flying birds and bats may be maimed or killed if they collide with the rotors. In this sense, it poses a serious threat to birds. Wind turbines may be rather loud, which is why they are generally located in remote places with few people. However, emerging innovations have helped to reduce noise levels.
What is Power Coefficient?
The wind power sector frequently uses the Power Coefficient (Cp) as a metric of wind turbine efficiency. Cp is the ratio of a wind turbine's real electric power output divided by the total wind energy streaming through the rotor blades at a given wind speed. The power coefficient, when stated in this way, indicates the cumulative efficiency of the different components of a wind turbine system, such as the rotor blades, gear train, generators, and power systems.

Distribution of the power losses in different stages of a direct-drive wind turbine. Image Credit: Sohail K et al., Energies
Although wind turbines may seem a very efficient choice, all of the energy cannot be extracted from the wind flowing through its blades. The Betz law states that the maximum amount of energy that could be extracted from the wind via a wind turbine is about 59.3% under ideal conditions; in real life, the value is between 35% to 40%.
For managing the placements and attributes of the wind turbine structural system, several maximum-power-tracking and optimization approaches such as yaw, average velocity, angular position, rotational acceleration, and torque have been presented.
Multiple kinds of research on power coefficient optimization have been carried out in the previous several decades, and they have been enlarged through several conceptual, theoretical evaluations, maximum tracking locations, and refinement based on various approaches and views.
Limitations of Previous Research
Previous research has mostly concentrated on power coefficient monitoring under threshold circumstances relating to wind direction and the wind turbine's aerodynamics train, such as blade profile and angular position or TSR. However, very few researchers have looked into the effect of the ideal power coefficient on wind turbine load management and power loss reduction.

Geographical map of the wind power classification at a 50 m height in different areas in Pakistan. Image Credit: Sohail K et al., Energies
Research Findings
The generated model was used to determine the best Cp values for a 100 W direct-drive wind turbine. The wind speed areas were grouped into five zones to better comprehend the influence of Cp on the mechanical-electrical output of the wind turbine: no power generation zone, acceleration area, active region, optimum region, and lastly, power coefficient control region.
In the instance of a small-scale 100 W wind turbine, the direct powertrain finding showed that the ideal value of Cp was 0.48 for an angular position of 0 degrees and a TSR of 8.1 at a wind speed of roughly 11.2 m/s. The power output in the ideal Cp phase was the maximum across that wind interval, resulting in decreased energy losses according to the results of the optimal control model and the experimental system.
Future Perspective
Future work might focus on constructing a model predictive controller (MPC) for the present optimal control research to compel the power coefficient to maintain the reference trajectory, allowing the maximal aerodynamic performance to be drawn against accurate changes in wind speed.
Further Reading
Sohail K, Farzaneh H. Model for Optimal Power Coefficient Tracking and Loss Reduction of the Wind Turbine Systems. Energies. 15(11). 4159. Available at: https://www.mdpi.com/1996-1073/15/11/4159
Disclaimer: The views expressed here are those of the author expressed in their private capacity and do not necessarily represent the views of AZoM.com Limited T/A AZoNetwork the owner and operator of this website. This disclaimer forms part of the Terms and conditions of use of this website.