By Surbhi JainReviewed by Susha Cheriyedath, M.Sc.Jun 9 2022
In an article recently published in the journal Additive Manufacturing, researchers discussed the parametric optimization of the two-photon direct laser writing technique for the production of polymeric microneedles.
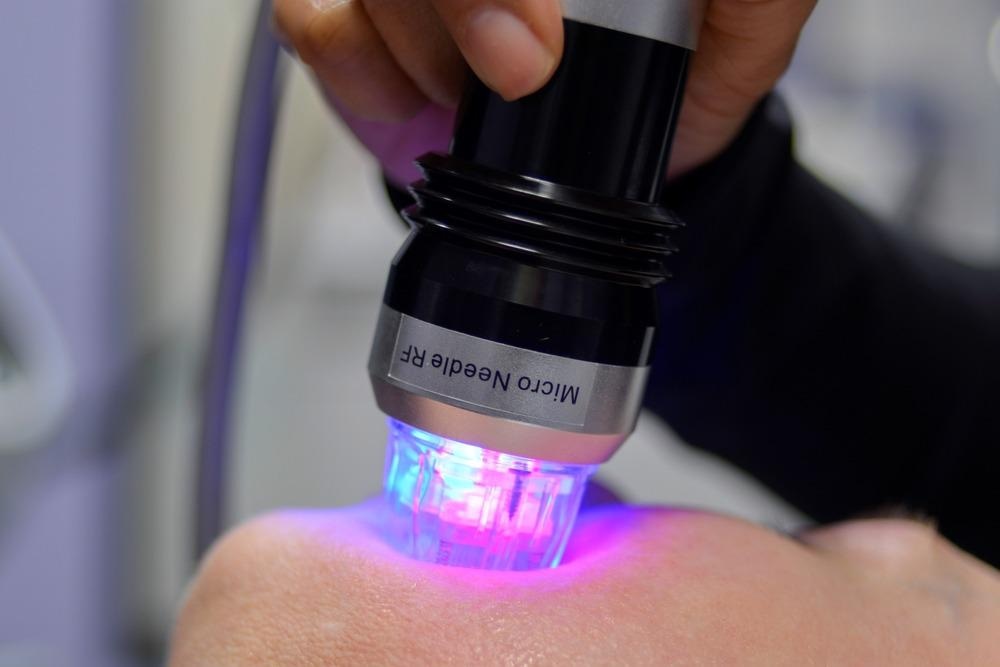
Study: Parametric optimization of two-photon direct laser writing process for manufacturing polymeric microneedles. Image Credit: AlteredR/Shutterstock.com
Background
Despite the widespread use of the hypodermic needle for blood samples and analysis, there are still limitations to its utilization. Miniaturized and more complex biomedical devices capable of delivering therapeutic medications and providing primary data on patient health are very much required. Small compounds, macromolecules, micro, and nanoparticles have all been delivered using microneedle arrays.
Combining microneedle medicine administration and bio sampling with complimentary patches or a single patch that performs both activities would be ideal. Developing vaccinations that are stable at room temperature might save a lot of money by eliminating the need for the cold chain entirely.
Microneedles are made from a number of materials, including metals, glass, silicon, ceramics, and natural and synthetic polymers, in a variety of shapes. Polymeric microneedles have attracted a lot of attention because of their biocompatibility, ease of manufacture, and mechanical stability. Rapid printing of nano- and micro-sized structures with feature sizes as tiny as 100 nm is possible with two-photon direct laser writing. Interest in polymer microneedle microprinting has grown in recent years, as has the number of academic articles published on the subject. However, rather than optimizing the printing process, most researchers have focused on the uses of microneedles created using this technique.
About the Study
In this study, the authors described how to make highly detailed microneedles with side channels and other complex designs using the two-photon direct laser writing process, as well as how to optimize and choose parameters for the microprinting of tall microneedles with side channels and other complex designs. The soft embossing method was used to demonstrate the master microneedle's reproduction capabilities. The mechanical properties and insertion force of the microneedle replicas were also studied.
The team demonstrated the printing of high-resolution microneedles and presented an in-depth investigation of the parameters affecting structure microprinting and optimization of the 3D laser lithography process for the production of microneedles by utilizing the commercial photonic professional GT system. For different prints, the laser power employed by the system varied from 80 mW to 100 mW, and the results were monitored.
After a series of optimization trials, laser power of 80 mW, a writing speed of 50,000 µm/s, and minimum and maximum slicing distances of 0.5 µm and 0.7 µm were chosen for printing microneedles with an acceptable level of polymerization.
The researchers developed rapid replication molding technologies based on polydimethylsiloxane (PDMS) molding and embossing procedures. The relationship between two-photon direct laser printing process factors such as scanning modes, laser power, hatching, scan speed, stitching, and slicing distance was described.
Observations
A microneedle array with a tip height of 300 µm had the lowest tolerance to the applied stress, but a microneedle array with a tip height of 150 µm could withstand an applied load 50% higher before failing.
The kinetics of the polymerization process in the focus voxel, which determined the polymerization degree of the printed components, was affected by the process parameters. The scan speed and laser power during the process had a substantial impact on the degree of polymerization. The results revealed that the faster the scanning speed, the less complete the polymerization was. The two-photon polymerization (TPP) revolutionized 3D printing by facilitating the printing of sub-micrometer feature sizes. The small voxel size made printing of the higher volume structures consume more time than other 3D printing processes like stereolithography, and the technology was better suited for prototyping.
Demolding of embossed cycloolefin polymer (COP) polymer microstructures was achieved without deformation or breakage of the embossed microstructures because of the flexibility of PDMS molds. Soft embossing of replica polymer microneedles provided minimal tooling and process setup costs, as well as inexpensive material and capital equipment costs, which indicated large-scale manufacturing possibilities. Porcine cadaver skin tests revealed the capacity of thermoplastic microneedles to penetrate the animal skin. Thermoplastic materials had no cytotoxicity or inflammatory effects.
Conclusions
In conclusion, this study elucidated the development of microneedles with optimal geometric accuracy and exceptional tip sharpness by using the two-photon direct laser writing technology. Feature geometries and resolution were accurately derived from computer-aided design (CAD) data rather than being constrained by the physics of traditional micro-manufacturing techniques.
The microneedle's side-open channel design generated a microfluidic channel that crossed the epidermis and communicated with the subcutaneous region, allowing for medication delivery or biomarker monitoring. The cross-sectional area accessible for molecular transport across the skin was increased by microneedle arrays. The TTP process was optimized to allow for the optimization of a large number of parameters in order to produce the most detailed features in a reasonable time, which is ideal for large-scale production operations.
The authors believe that the discussed concept is critical for grasping the fundamentals of 3D laser lithography and fabricating sophisticated microneedles with the best resolution. They also mentioned that this advanced manufacturing technology could be used to microprint a range of high-resolution, complex microstructures, not simply microneedles, by describing the process' main characteristics and features.
More from AZoM: How are PAT Techniques Used for Real-Time Particle Analysis?
Disclaimer: The views expressed here are those of the author expressed in their private capacity and do not necessarily represent the views of AZoM.com Limited T/A AZoNetwork the owner and operator of this website. This disclaimer forms part of the Terms and conditions of use of this website.
Sources:
Rad, Z. F., Prewet, P. D., Davies, G. J., et al. Parametric optimization of two-photon direct laser writing process for manufacturing polymeric microneedles. Additive Manufacturing 102953 (2022). https://doi.org/10.1016/j.addma.2022.102953.
https://www.sciencedirect.com/science/article/abs/pii/S2214860422003475