By Surbhi JainReviewed by Susha Cheriyedath, M.Sc.Jun 16 2022
In an article recently published in the open-access journal Materials, researchers discussed the development of epoxy particle foam (EPFs) and novel expandable epoxy beads (EEBs).
Study: Novel Expandable Epoxy Beads and Epoxy Particle Foam. Image Credit: Meaw_stocker/Shutterstock.com
Background
Development in the field of bead foams has accelerated in recent years. Bead foams, in general, allow for the production of extremely complicated product shapes in a single step without the use of a costly injection mold. High-temperature bead foams and bead foams with specific mechanical qualities are two current trends.
To date, however, research on bead foams has primarily concentrated on thermoplastic bead foams, which are bent, melted, and dripped outside of their temperature range. Epoxy resin and hardener, unlike thermoplastics, undergo step polymerization to generate a final three-dimensional crosslinked network (3D crosslink). The addition of the gas phase to a fully crosslinked network results in a non-foamable system that cracks.
Solid-state epoxy has recently been used to make epoxy molding compounds (EMCs) for the fabrication of electronics devices utilizing injection molding techniques in a single process step. Porous beads are added directly to resin and have served as a void template for the production of syntactic foams, in addition to chemical and physical blowing agents. Because of its exceptional thermal qualities, research on porous beads has recently received a lot of attention. The most popular methods for making porous microbeads are based on resin immiscibility and a medium phase, such as epoxy in water or epoxy in oil.
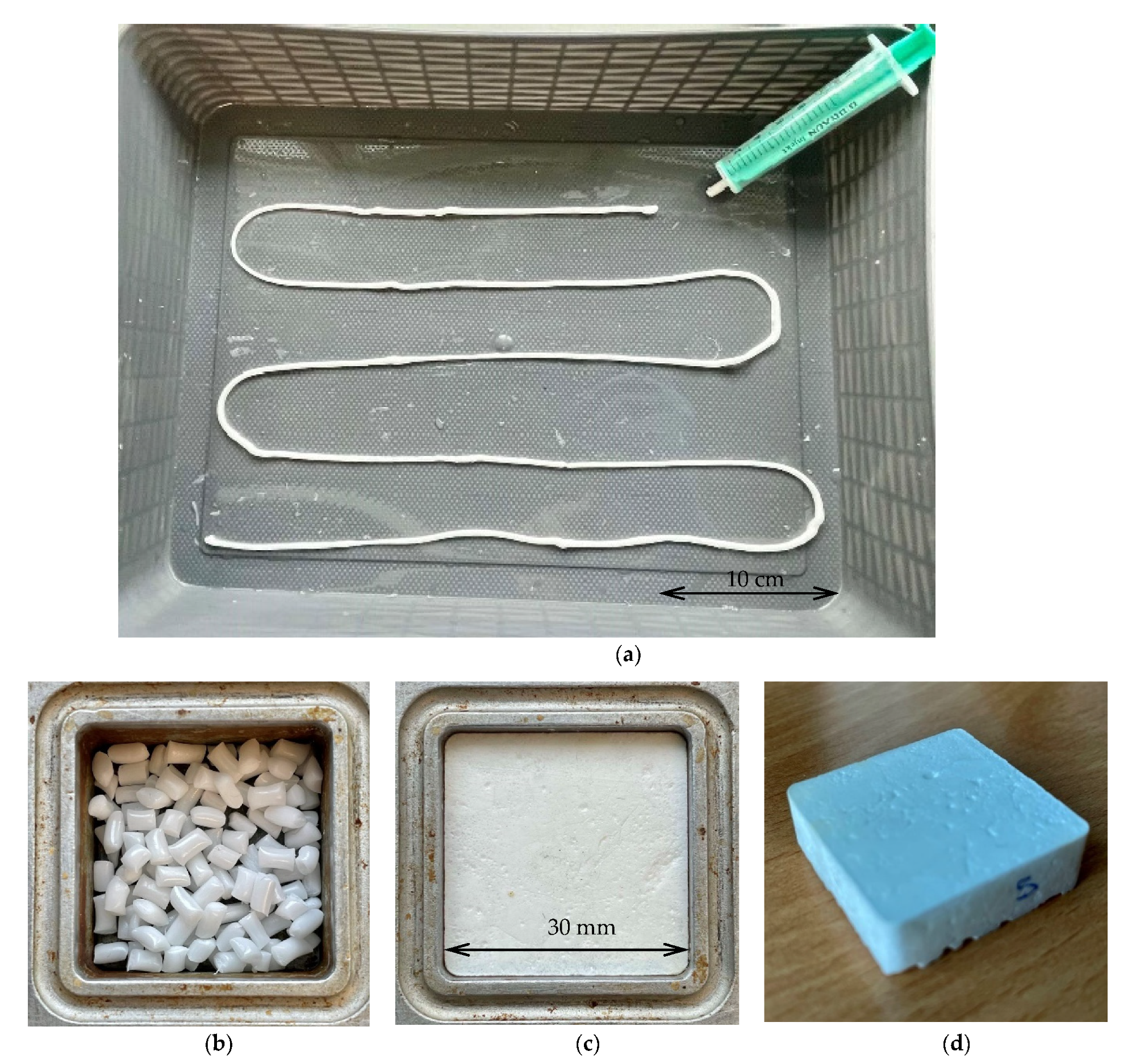
(a) Expandable epoxy extrudate with a diameter of 2.7–3.5 mm and a length of 1.5 m, (b) EEBs in mold, (c) EPF after foaming at 160 °C and cooling and (d) EPF after demolding. Image Credit: Uy Lan, D. N et al., Materials
About the Study
In this study, the authors presented a new process for the fabrication of EEBs, and their subsequent expansion followed by fusing them to generate EPFs by using solid-state carbamate foaming technology. A mixture of epoxy, carbamate, and hardener was produced and placed into a 10 mL syringe for the creation of EEBs.
To make a cylindric shape, the mixture was manually extruded into 60 °C water. At 60 °C, the extrudate was further cured to produce an epoxy oligomer with rheological tan delta 3 and 2. To obtain EEBs, the extrudate was chopped into pellets. The EEBs were then poured into an aluminum mold and baked at 160 °C to expand and fuse, which yielded EPFs of 212 kg/m3 and 258 kg/m3, respectively.
The team proposed a unique technique for the production of EEBs via an extrusion process. The oligomer network was made up of Ancamine 2914UF, an ultra-fast curing hardener, and DEN 431 epoxy Novolac. Evonik made an ionic liquid based on polyamine and p-toluenesulfonic acid, called Ancamine hardener. Isophorone diamine (IDPA) carbamate was utilized as both a blowing agent and a latent curing agent. The rheological features of the epoxy oligomer, such as storage modulus, loss modulus, and tan delta, were used to develop EEBs. Tan delta represented the damping and viscoelastic behavior as the ratio of loss modulus to storage modulus.
The researchers pre-cured the EEBs at 60 °C to various tan delta values. Further, their ability to expand and fuse to produce EPFs was studied. The gas phase was introduced into the oligomer state in order to foam the epoxy oligomer network. To obtain a complete 3D crosslinking network, more curing was conducted.
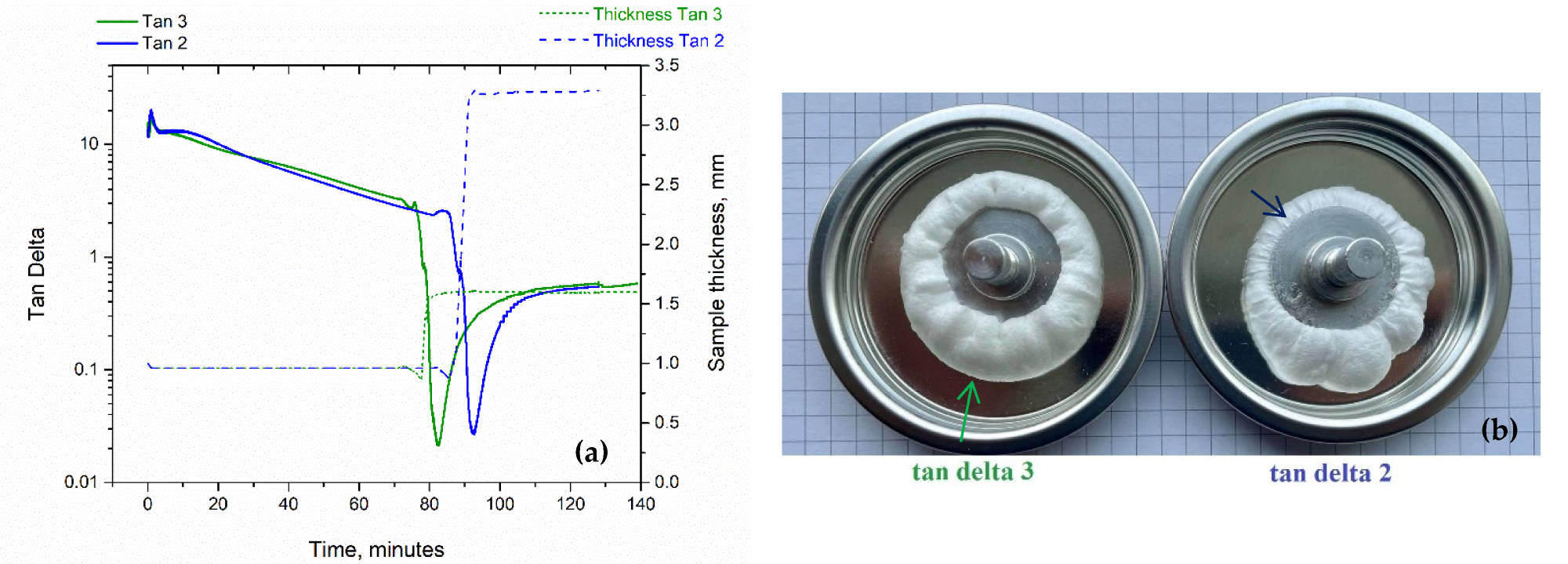
(a) Tan delta and sample thickness changing from solid state to foam versus time. (b) Rheological foam sample of tan 3 showing a soft texture, whereas tan 2 shows a rougher texture. Image Credit: Uy Lan, D. N et al., Materials
Observations
Sicomin was a two-component resin for the foaming epoxy with a Tg of 60–142 °C. The Tg of Resoltech resin epoxy foams ranged from 48 to 110 °C. Thermoset polyurethane foam generated from lignin had a Tg of 38–117 °C. EPFs had a densification strain of 0.53 to 0.55. At a foaming temperature of 160 °C, the lowest density of epoxy beads was at 130–132 kg/m3. The carbamate-filled epoxy oligomers (CfEO) tan 3 and tan 2 had G'30 °C of 30 kPa and 48 kPa, respectively, when chilled to 30 °C. The obtained EPFs had a Tg of 150–154 °C. In EPFs, the fusion boundaries were highly defined. As a result, the prepared EPFs had a compressive modulus of 50–70 MPa and a torsion storage modulus of 34–56 MPa at 30 °C.
Manual extrusion with a viscosity of 180 Pa.s was adequate for the formation of the extrudate into a circular shape after further securing. At 60 °C, DEN 431 interacted with Ancamine 2914UF to form an oligomer with tan delta 2 and tan delta 3 during the pre-curing process. Both EEBs with tan delta 2 and tan delta 3 were capable of foaming, fusion, and expansion, which resulted in high-strength EPF with Tgs of 150–154 °C and densities of 212 kg/m3 and 258 kg/m3, respectively. In both cases, an open-cell structure was obtained. The compressive modulus ranged from 50 to 70 MPa. At 50% compressive strain, the specific strength was 20–25 kNm/kg.
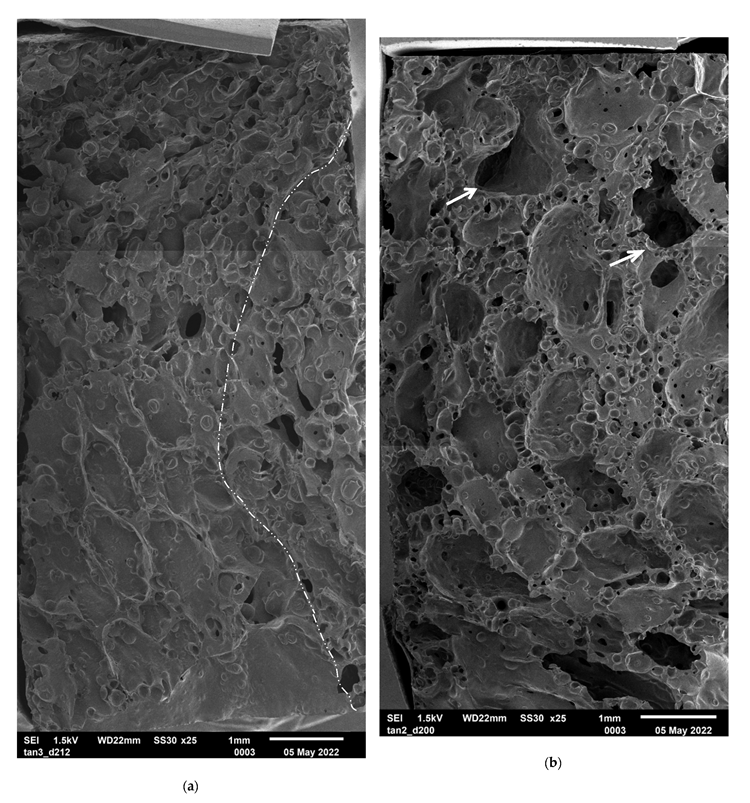
Assembled SEM of (a) EPF 212 kg/m3 made of EEB−tan 3, the dash-dot-dot line shows a fusion boundary and (b) EPF 210 kg/m3 made of EEB−tan 2. Image Credit: Uy Lan, D. N et al., Materials
Conclusions
In conclusion, this study elucidated the preparation of oligomers that could transition from a liquid to a solid form at ambient temperature. These carbamate-filled epoxy oligomers were, in fact, solid-state epoxies.
The authors mentioned that EEBs with different tan deltas and varying foaming temperatures could be produced to enhance the processing window for foaming. They also stated that because the epoxy face sheets and the epoxy foam core so securely adhere to each other, a sandwich with great strength and heat resistance should be produced between them.
Disclaimer: The views expressed here are those of the author expressed in their private capacity and do not necessarily represent the views of AZoM.com Limited T/A AZoNetwork the owner and operator of this website. This disclaimer forms part of the Terms and conditions of use of this website.
Source:
Uy Lan, D. N., Brütting, C., Bethke, C., et al. Novel Expandable Epoxy Beads and Epoxy Particle Foam. Materials 15(12) 4205 (2022). https://www.mdpi.com/1996-1944/15/12/4205