In a pre-proof article recently published in the journal Additive Manufacturing, researchers reviewed the applications of 3D polymer formworks in architecture, focusing on failures due to formwork pressure and deriving solutions to these issues. Furthermore, the team aimed to provide a guideline for the selection of thermoplastics to fabricate 3D printed formworks.
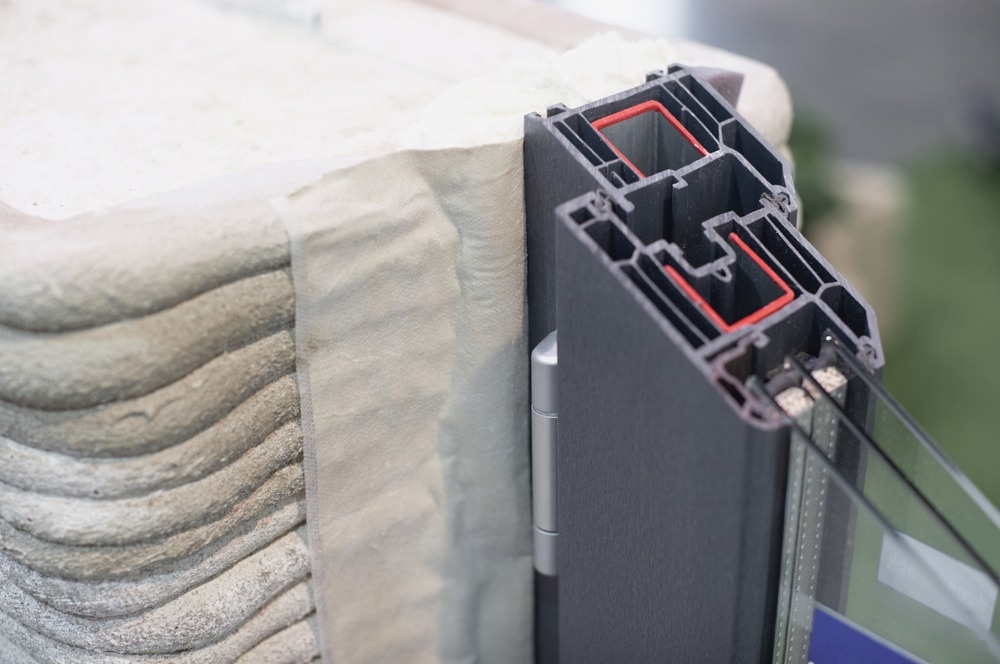
Study: Environmental Stress Cracking of 3D-Printed Polymers Exposed to Concrete. Image Credit: ya_create/Shutterstock.com
Background
Formworks are essential structures in most concrete casting and fabrication processes, supporting fresh concrete until hardening and thereby defining the texture, surface quality, and shape of the final material. Although formworks are versatile, reusable, and inexpensive, their application becomes limited with complex architectures.
Formworks have been fabricated mostly by various 3D printing processes like binder jetting and foam, clay extrusion, polymer, and concrete. One of the most acclaimed and widely studied methods is polymer extrusion 3D printing, or in other words, fused deposition modeling (FDM) and fused filament fabrication (FFF). This method is also known for being cheap, lightweight, and for its use of easily recyclable materials.
Despite this, FDM formworks are susceptible to casting failures, causing concrete leakage and resulting in unsuccessful casts. These failures are usually attributed to the pressure exerted on the thin plastic formworks by the concrete. Some 3D printing polymers like polylactic acid (PLA) are more vulnerable to premature failure, whereas others like acrylonitrile butadiene styrene (ABS) are reusable for up to 190 times.
This study focused on failures due to concrete pressures and their mitigation in FDM formworks. This was followed by identifying the widely used thermoplastics in FDM 3D printing and determining the structural performance of the formworks through a three-point bending test.
Materials and Methods
In this study, 18 different samples were procured including acrylonitrile butadiene styrene (ABS), acrylonitrile butadiene styrene + polyamide (ABS/PA), acrylonitrile styrene acrylate (ASA), acrylonitrile styrene acrylate + hindered amine light stabilizers (ASAUV), brominated polylactic acid (bPLA), high impact polystyrene (HIPS), polylactic acid + 40% lignin (Lig), polyamide (nylon) (PA), polycarbonate (PC), polyethylene terephthalate (PET), polyethylene terephthalate + wax (PETW), polyethylene terephthalate, glycol-modified (PETG), PLA sourced from extrudr (PLA1), PLA sourced from Dutch Filaments (PLA2), polylactic acid + carbon fibers (PLACF), polylactic acid and co-polymers (PLA+), polylactic acid (annealed) (PLAa), and polyvinyl alcohol (PVA).
The team subjected the samples to mechanical tests to determine the formwork’s resistance to the hydrostatic pressure while casting. The three-point bending tests were reversed by the vertical support orientation, allowing the samples to be balanced between the support pins and the loading pin.
This enabled a horizontal surface between the support pins where a drop of sodium hydroxide (NaOH) solution was applied, acting as a concrete pore solution. At a load rate of 2 mm/min, a universal testing machine conducted the tests with a 1 kN load cell. This was carried out until specimen failure or the flexural strain surpassed 10%.
Observations
The results indicated that the alkaline solution significantly affected the bending strength of certain polymers followed by rapid deterioration. The annealed PLA sample exhibited inconsequential change in stiffness and strength, while short carbon fiber reinforcement resulted in a minor but measurable increase in the bending strength and elastic modulus of the PLA.
Moreover, five modes of failure were observed; material failures, slip failures, strain limit, brittle failures, and environmental stress cracking (ESC) with material failure were the most common. This is generally caused by plastic deformation and large strain leading to fractures occurring beyond the yield point.
Similarly, slip failures occurred through plastic deformation with the difference being that the fractures came from the 3D printed layers slipping along the interfaces and separating from each other. The specimen exceeding the 10% threshold for the flexural strain reached their strain limit while brittle failures occurred in the carbon fiber reinforced PLA and the annealed PLA samples. Environmental stress cracking generally leads to brittle failure, without ductile drawing from the surfaces next to the cracks. The PLA, PC, and PET samples were highly vulnerable to ESC and exhibited loss in strength in all orientations.
The team categorized the samples based on the loss of bending strength in the presence of NaOH solution: (1) Group 1 including materials unaffected by NaOH such as ASA, ABS, HIPS, PVA, and nylon, (2) Group 2 including samples displaying moderate loss of strength such as 17.8% for PETG, 51.9% for PET, and 43.8% for PC, and (3) Group 3, including materials that were substantially affected by NaOH including samples based on PLA, which could lose approximately 60-80% of their bending strength in comparison to the dry tests.
Conclusions
To summarize, the study findings proposed an efficient experimental setup that precisely assesses the common FDM polymer behavior employed in the formwork fabrication. While polymers like PETG, PC, PET, and PLA were susceptible to ESC, additional polymers such as ASA, ABS, nylon, HIPS, ABS/PA, and PVA displayed resistance to ESC. The authors suggest that surface irregularities could be reduced or eliminated using post-processing methods like sanding, chemical washing, polishing, bead tumbling, or sand blasting.
Disclaimer: The views expressed here are those of the author expressed in their private capacity and do not necessarily represent the views of AZoM.com Limited T/A AZoNetwork the owner and operator of this website. This disclaimer forms part of the Terms and conditions of use of this website.
Source:
Andrei Jipa, Lex Reiter, Robert Flatt and Benjamin Dillenburger, Environmental Stress Cracking of 3D-Printed Polymers Exposed to Concrete, Additive Manufacturing, (2022) doi: https://www.sciencedirect.com/science/article/pii/S2214860422004183?via%3Dihub