A group of researchers recently published a paper in the journal Additive Manufacturing that demonstrated the changes in the behavior of ultra-high performance concrete (UHPC) prepared using the three-dimensional (3D) printing technology after elevated temperatures in the context of building safety.
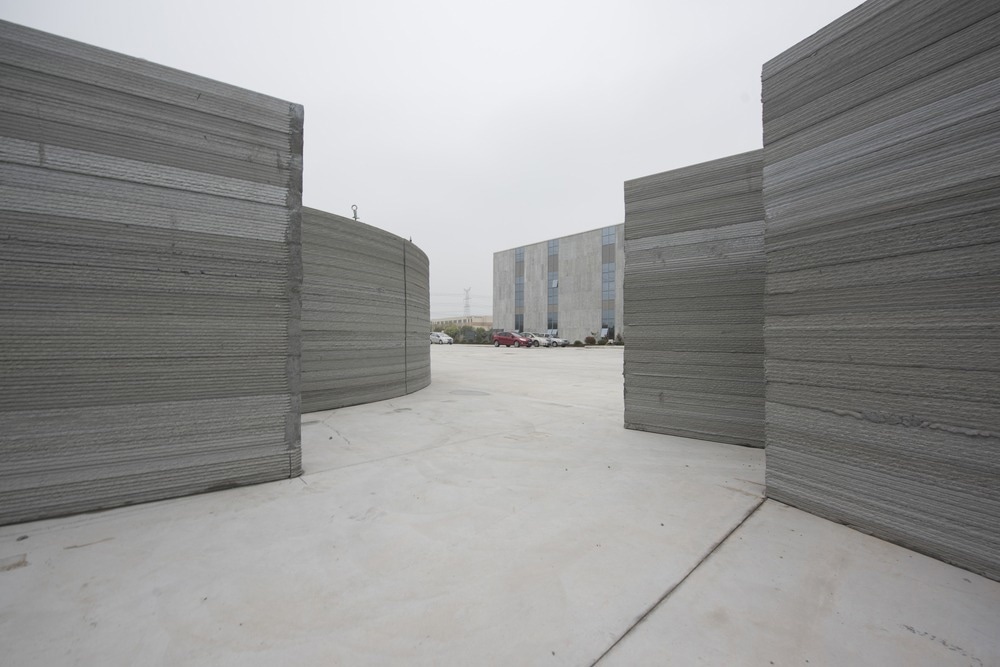
Study: Microstructure and mechanical behaviour of 3D printed ultra-high performance concrete after elevated temperatures. Image Credit: Matjazz/Shutterstock.com
Background
The fire resistance of concrete, a crucial building material, directly impacts building safety. However, concrete possesses a limited strength and its strength degrades at elevated temperatures. Thus, UHPC is being increasingly utilized for disaster reduction and prevention.
Several studies have investigated the fire resistance of UHPC. For instance, the findings of a study investigating the fire resistance of UHPC with 100-180 MPa compressive strength demonstrated that the UHPC beams with four vol.% steel fiber have a lighter degree of spalling compared to beams with two vol.% steel fiber.
The steel fiber provided bonding and tensile strength in the UHPC matrix, which decreased the spalling when the concrete was exposed to fire. Another study demonstrated that UHPC mixed with end hook type ordinary industrial steel fiber possesses the highest burst resistance at elevated temperatures.
In the last few years, 3D printing technology, a rapid prototyping technology that extrudes materials through a printer nozzle and replicates the cross-section of 3D objects in a layer-by-layer manner to create solid 3D objects, has gained prominence in the civil construction sector.
3D printing concrete technology can efficiently complete the creation of homogenous structures, deliver tailored components in time, reduce costs, and conserve construction materials. However, printing concrete and reinforcement using 3D printing technology is still very challenging.
UHPC is more suitable for 3D printing due to its good toughness and high strength. In 3D-printed UHPC (3DP-UHPC), the steel fibers are distributed directionally, and no fiber-steel connection is present between the printing layers.
This distinct microstructure of 3DP-UHPC can potentially affect its fire resistance, which necessitates the investigation of 3DP-UHPC fire resistance. Moreover, studies determining the behavior of 3DP-UHPC after high temperatures have also not been performed until now.
The Study
In this study, researchers investigated the behavior of 3D-UHPC at room temperature and after elevated temperatures in the range of 200-500 oC. Specifically, researchers analyzed the effects of target temperatures of 500 oC, 400 oC, 300 oC, 200 oC, and 20 oC, “X”, “Y”, and “Z” loading directions, steel fibers with 6 mm and 10 mm diameters, and bonding strip on the 3DP-UHPC fire resistance.
The variations in mineral composition and microstructure of 3DP-UHPC after various elevated temperatures were assessed using an energy dispersive spectrometer (EDS) and scanning electron microscopy (SEM). Additionally, the compressive strength and the ignition loss rate of the 3DP-UHPC were measured after the elevated temperatures.
The disadvantages and advantages of the 3DP-UHPC were analyzed and compared with reference specimens, including 3DP ultra-high strength concrete (UHSC), mold-casting UHSC (MC-UHSC), and mold-casting UHPC (MC-UHPC). Eventually, the compressive constitutive model of the 3DP-UHPC after elevated temperatures was proposed for the first time to promote the use of 3DP-UHPC in the field of fire safety.
Initially, the weighed cellulose, nano calcium carbonate, quartz sand, fly ash, silica fume, and cement were mixed for five min using the UJZ-15 mortar mixer to ensure uniform distribution of all materials. Subsequently, polycarboxylate superplasticizer and water were successively poured into the mixer and stirred for 10 min.
The steel fiber was dispersed evenly in the as-prepared mortar and fully mixed with the mortar. Subsequently, the fresh mortar was poured into the 3D printer hopper and extruded from the printer nozzle. The extruded mortar formed a printing wire that was laid along the X-direction.
HC1008 desktop concrete 3D printer was used for the 3D printing of UHPC. A large cubic 3DP-UHPC sample was prepared using the 3D printer before preparing the test specimens. The reference specimens were also prepared, with the mixing proportions of MC-UHPC and 3DP-UHPC and that of MC-UHSC and 3DP-UHSC kept identical. UHSC samples did not contain steel fibers.
1400℃ rapid heating box electric furnace was used for heating in the study, and the International Standard ISO834 was utilized to simulate the real fire situation. Researchers performed the static compressive test after naturally cooling down the heated specimens to room temperature using an RMT-150C rock mechanic testing machine.
Observations
3DP-UHPC samples were prepared successfully using the 3D printing method. The 3D printing method used for UHPC preparation and the inclusion of steel fibers in the concrete positively impacted the fire resistance of the 3D-UHPC samples. The 3DP-UHPC specimens displayed a compressive strength of 32.7-48.1 MPa even after 500 oC, indicating the notable fire resistance of the concrete.
Additionally, the prepared 3D-UHPC also displayed a higher elevated-temperature burst resistance compared to MC-UHPC due to the weak interface of the bonding strip that helped the water vapor to escape along the bond interface during heating, which delayed the burst occurrence.
The 3DP-UHPC displayed the best compressive behavior after 300 oC. Although this temperature affected the strength of the 3DP-UHPC sample, the effect of temperature was insignificant on the strength difference between each loading direction of 3DP-UHPC.
The 3DP-UHPC compressive strength after 400 oC was lower compared to the strength observed after 300 oC due to the expansion of the crack at the junction of the matrix and steel fiber and decarburization and oxidation of the steel fiber.
No significant impact of the steel fiber on the ignition loss rate was observed when the specimen was not cracked. The ignition loss rate of the specimens increased substantially at 500 oC due to the loss caused by the local spalling of 3DP-UHPC and the dehydration and decomposition of calcium hydroxide (Ca(OH)2) and calcium-silicate hydrate (C-S-H) gel.
The compressive constitutive model proposed in the study for 3DP-UHPC after the elevated temperatures can be used to effectively predict the compressive behavior of 3D-UHPC at various temperatures.
Taken together, the findings of this study effectively demonstrated the effectiveness of 3DP-UHPC in increasing the fire safety of buildings.
More from AZoM: Reflection Electron Microscopy for Crystal Analysis
Disclaimer: The views expressed here are those of the author expressed in their private capacity and do not necessarily represent the views of AZoM.com Limited T/A AZoNetwork the owner and operator of this website. This disclaimer forms part of the Terms and conditions of use of this website.
Source:
Li, J., Liu, Z., Wu, C. et al. Microstructure and mechanical behaviour of 3D printed ultra-high performance concrete after elevated temperatures. Additive Manufacturing 2022. https://www.sciencedirect.com/science/article/pii/S2214860422004249?via%3Dihub